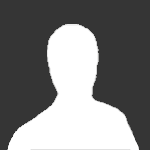
并且,在深入研究 PLC 的高级指令之前,程序员必须首先了解这些基本块,以便正确实施它们并获得帮助以更轻松地学习高级块。
在本文中,我们将了解 PLC 编程中定时器和计数器之间的区别。
什么是定时器?
定时器是一种用于在一定延迟后打开或关闭输出的指令。例如,如果您想在 5 秒后打开一盏灯,则使用定时器执行此任务。
定时器将接受输入,当输入打开时,其计时将开始。5 秒后,定时器输出将打开,从而间接打开灯。我们正在谈论的是该类型的普通定时器。
定时器有两种类型——定时器关闭和脉冲定时器。简而言之,基本功能是相同的——在一定延迟后执行任务。
请参考上图以更正确理解。定时器有四个输入和输出——输入、设定值、当前值和输出。输入接受启动定时器的条件,设定值用于获取设定的定时器值,当前值显示当前运行的定时器值,输出用于打开或关闭与其连接的变量。
当 PLC 定时器获得输入时,如果设定值为 5 秒,则定时器从 1、2 和 3 开始,依此类推,直到 5。当 5 秒完成后,输出打开。当输入关闭时,定时器的当前值立即变为零。
无论定时器是否正在运行;如果输入关闭,则定时器不会启动,其输出和当前值将为零。这是 TON(定时器开启延迟)定时器的功能。
什么是计数器?
计数器是一种指令,用于在达到设定的计数后打开输出。计数可以递增或递减。
例如,如果您想在按下按钮五次后打开灯,则使用计数器执行此任务。计数器将接受输入,当输入打开时,其计数将递增为 1。
当输入关闭时,不会发生任何事情。当它再次收到输入时,计数将递增为 2。计数 5 过去后,计数器输出将打开,从而间接打开灯。我们谈论的是计数器向上类型。
计数器还有一种类型 - 计数器向下。简而言之,基本功能是相同的 - 在一定计数后执行任务。
请参阅上图以更正确理解。计数器有五个输入和输出 - 计数输入、复位输入、设置值、当前值和输出。计数输入接受计数条件,复位输入接受计数器复位条件,设定值用于获取设定的计数器值,当前值显示当前运行的计数器值,输出用于打开或关闭与其连接的变量。
当计数器获得计数输入时,如果设定值为 5,则计数器递增为 1,依此类推,直到 5;在计数输入中收到每个脉冲时(意味着计数输入必须打开和关闭 5 次)。完成 5 次计数后,输出打开。
现在,即使给出计数输入脉冲,计数器也会在 5 之后继续增加,输出也将保持打开状态。要再次将计数器状态恢复为零,您必须提供复位输入。给出此输入后,计数器当前值变为零,输出也会关闭。因此,它类似于锁存型功能。要解锁计数器,您必须重置它。这是 CTU(计数向上)计数器的功能。
定时器和计数器之间的区别
PLC 中的定时器和计数器之间的主要区别如下。
定时器需要连续输入才能打开变量,但计数器不需要连续输入。因此,定时器在连续条件下工作,而计数器在脉冲条件下工作。 如果移除定时器输入,则其输出将返回到零状态;但如果移除计数器输入,则计数器将保持其最后一个值。 定时器没有复位输入,而计数器需要复位输入才能将计数器恢复到其原始状态。 定时器的类型包括定时器开启、定时器关闭和定时器脉冲。计数器的类型包括计数器加法和计数器减法。 定时器设定值可以是秒、分钟或毫秒;但计数器设定值是固定整数。
- Read more...
-
- 0 comments
- 252 views