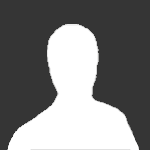
This PLC is being used to start and stop an electric motor, and also to shut it down automatically if any of three “shutdown” conditions occur:
Excessive vibration Overcurrent (overload heater contact) High winding temperature Motor Trip Logic using PLC Programming
The status of each shutdown contact is as follows:
Vibration contact: closed when okay, opens when vibration becomes excessive Overload contact: closed when okay, opens when overloaded Temperature contact: open when okay, closes when hot Draw a PLC ladder-logic program to start and stop this motor.
Be sure to make the program latching so that the operator does not have to hold the Start button to keep the motor running.
Answer:
Do you find any mistakes in the logic? Share with us through comments.
- Read more...
-
- 0 comments
- 299 views