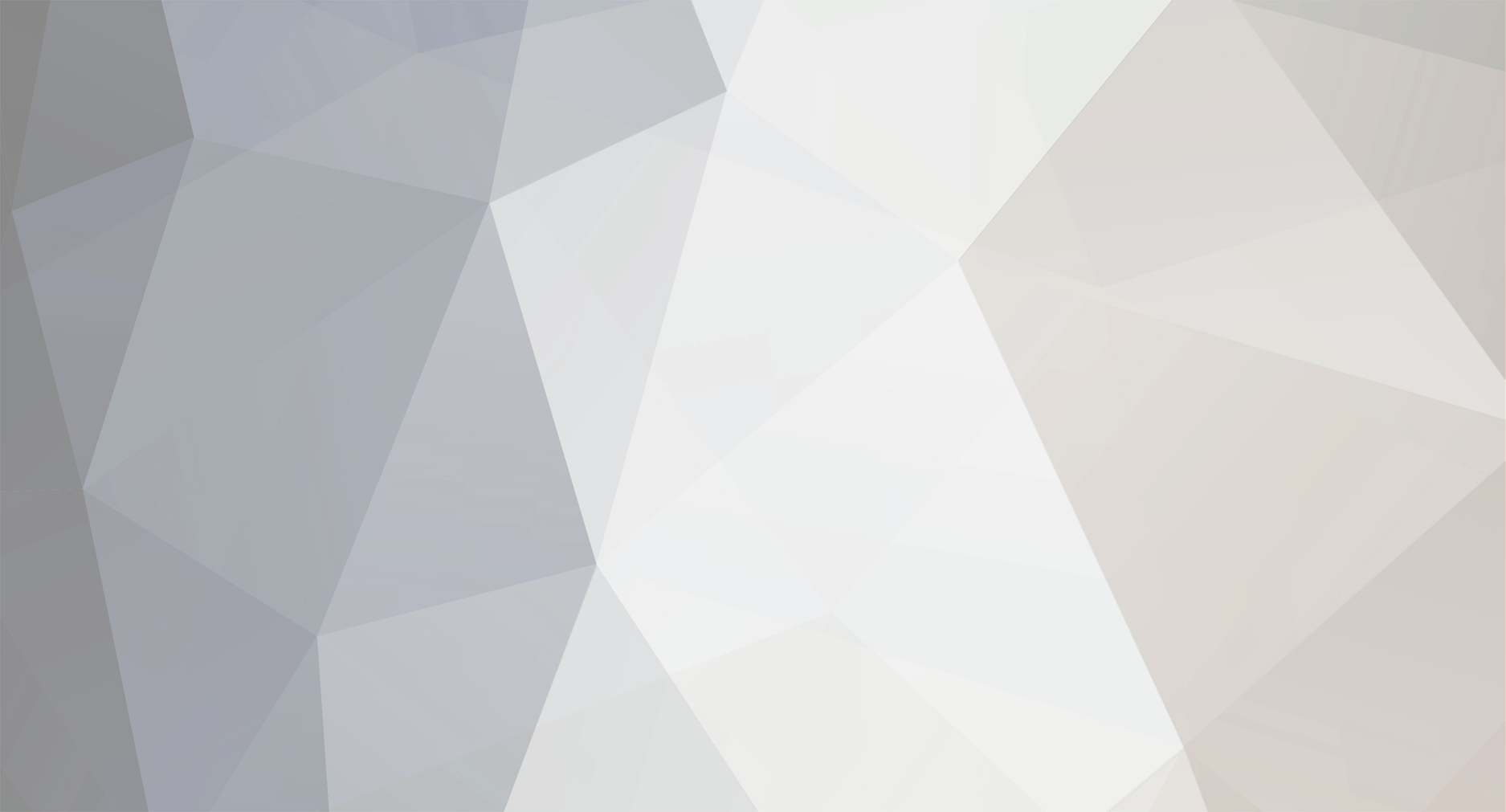
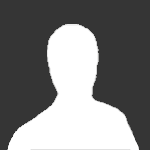
leigehong
Subscription group-
Content Count
168 -
Joined
Content Type
Profiles
Forums
PLC programming technology and HMI interface design Simplified Chinese database
- PLC AND HMI SIMPLIFIED CHINESE ARTICLES
- PLC AND HMI SIMPLIFIED CHINESE ARTICLE Comments
- PLC AND HMI SIMPLIFIED CHINESE ARTICLE Reviews
PLC and HMI Brand Database
- PLC AND HMI BRANDS INTRODUCTIONS
- PLC AND HMI BRAND INTRODUCTION Comments
- PLC AND HMI BRAND INTRODUCTION Reviews
PLC programming technology and HMI interface design English database
- PLC AND HMI ENGLISH ARTICLES
- PLC AND HMI ENGLISH ARTICLE Comments
- PLC AND HMI ENGLISH ARTICLE Reviews
PLC programming technology and HMI interface design Russian database
- PLC AND HMI RUSSIAN ARTICLES
- PLC AND HMI RUSSIAN ARTICLE Comments
- PLC AND HMI RUSSIAN ARTICLE Reviews
Spanish database on PLC programming techniques and HMI interface design
- PLC AND HMI SPANISH ARTICLES
- PLC AND HMI SPANISH ARTICLE Comments
- PLC AND HMI SPANISH ARTICLE Reviews
German database on PLC programming technology and HMI interface design
- PLC AND HMI ARTICLES IN GERMAN
- PLC AND HMI ARTICLE IN GERMAN Comments
- PLC AND HMI ARTICLE IN GERMAN Reviews
Downloads
Store
Gallery
Blogs
Calendar
Videos
Everything posted by leigehong
-
Нагрев и смешивание продуктов с использованием примера руководства ПЛК
leigehong posted A plc and hmi russian article in PLC programming learning
Это программа ПЛК для автоматического нагрева и смешивания продуктов. Изучите программирование ПЛК с помощью этого примера для студентов-инженеров. Нагрев и смешивание продуктов Описание проблемы Создайте автоматическую систему, в которой два материала собираются в одном резервуаре. Все материалы должны смешиваться до достижения ими заданной заданной температуры. Создайте лестничную программу в S7-1200 ПЛК для этого приложения. Диаграмма проблемы Решение проблемы Мы можем решить эту проблему с помощью простой логики. Для этой системы рассмотрим два отдельных реле уровня для определения уровня двух разных материалов (скажем, Материал A и Материал B). Также рассмотрим одно реле уровня для определения пустого уровня. Для управления уровнем мы можем использовать клапан одностороннего действия (полностью открытый и полностью закрытый тип). Для смешивания используется мешалка, соединенная с валом двигателя. Нагреватель и датчик температуры установлены внутри резервуара. Здесь материалы смешиваются до тех пор, пока не будет достигнута заданная температура, и после смешивания срабатывает выпускной клапан (Q0.4) для слива смешанных продуктов. Список входов и выходов Список входов НАЧАЛО цикла :- I0.0 ОСТАНОВКА цикла :- I0.1 Уровень материала B :- I0.2 Уровень материала A :- I0.3 Реле уровня пустого :- I0.4 Датчик температуры :- I0.5 Список выходов Впускной клапан 1 :- Q0.0 Впускной клапан 2 :- Q0.1 Двигатель мешалки :- Q0.2 Нагреватель :- Q0.3 Выпускной клапан :- Q0.4 Память M M0.0 :- Цикл ВКЛ Программа ПЛК для нагрева и смешивания продукта Объяснение программы В эта проблема, мы рассмотрим S7-1200 ПЛК и программное обеспечение портала TIA для программирования. Сеть 1: Эта сеть показывает простую схему фиксации для цикла ВКЛ и цикла ВЫКЛ. Нормально открытый (НО) контакт кнопки ПУСК цикла (I0.0) и нормально замкнутый контакт кнопки СТОП цикла (I0.1) для активации цикла. Сеть 2: Эта сеть должна управлять впускным клапаном 1 (Q0.0). Он срабатывает, когда обнаруживается низкий уровень в баке (I0.4). И он закрывается, когда уровень материала A определяется переключателем с адресом (I0.3). ПУСК PB (I0.0) также подключен параллельно, поэтому если низкий уровень не обнаружен, впускной клапан можно запустить, нажав ПУСК PB (I0.0). Сеть 3: Эта сеть должна управлять впускным клапаном 2 (Q0.2). Он срабатывает, когда материал A заполнен до нужного уровня. Когда цикл запущен и уровень материала A обнаружен, впускной клапан 2 (Q0.1) будет включен. Сеть 4: Эта сеть должна управлять двигателем мешалки и нагревателем. Когда бак заполнен материалом A и материалом B, нагреватель (Q0.3) и двигатель мешалки (Q0.2) будут включены. Сеть 5: Когда весь процесс смешивания и нагрева завершен, выпускной клапан (Q0.4) будет включен. NC контакт реле пустого уровня (I0.4) используется для остановки выпускного клапана, когда бак пуст. Примечание: - Вышеприведенная логика предназначена только для объяснения определенного применения. Диаграмма приведена в ознакомительных целях, фактическая система может отличаться от этой системы. Результат -
Программа ПЛК для системы охранной сигнализации
leigehong posted A plc and hmi russian article in PLC programming learning
Это программа ПЛК для систем охранной сигнализации. Изучите программирование ПЛК на примере этой задачи. Система охранной сигнализации Описание задачи Создайте программу охранной сигнализации в ПЛК S7-1200 для дома. Рассмотрим один дом, в нем мы хотим организовать автоматическую систему охранной сигнализации. Сигнализация должна включаться, когда датчик движения обнаружит любого человека. Схема задачи Решение задачи Мы можем решить эту задачу, используя простую логику. Здесь мы можем использовать два датчика, один датчик движения и второй датчик окна. Датчик окна — это петля проводов. Датчик движения спроектирован таким образом, что когда в доме или комнате обнаруживается человек, датчик активируется (меняет свое состояние на 1 или истина) Важным моментом в датчике окна является то, что ток всегда проходит, пока не разобьется стекло. Следовательно, выход всегда истинный, и когда кто-то попытается разбить стекло окна, ток не будет течь по цепи. Список входов и выходов Список входов Система ПУСК :- I0.0 Система ОСТАНОВ :- I0.1 Детектор движения :- I0.2 Датчик окна :- I0.3 Кнопка остановки сигнализации :- I0.4 Список выходов Сигнал :- Q0.0 Память M M0.0 :- Главная катушка. M0.1 :- Состояние тревоги. Релейная схема ПЛК для системы охранной сигнализации Описание программы В этой задаче мы рассмотрим ПЛК S7-1200 и программное обеспечение портала TIA для программирования. Сеть 1: Эта сеть показывает простую схему фиксации для включения и выключения системы. мы использовали нормально открытый (НО) контакт кнопки ПУСК системы (I0.0) и нормально замкнутый контакт кнопки СТОП системы (I0.1) для активации системы. Сеть 2: Когда система активирована и датчик движения (I0.2) обнаруживает вход человека, состояние тревоги (M0.1) будет включено, и это активирует сигнал тревоги (Q0.0). Обычно нормально замкнутый контакт датчика окна (I0.3) используется параллельно, поэтому в нормальном состоянии он истинный. Если обнаружено разбитие стекла или состояние окна, вход датчика окна (I0.3) становится ложным, и это активирует состояние тревоги (M0.1). Сеть 3: В этой сети защелкивающаяся схема используется для тревоги (Q0.0). Если обнаружено состояние тревоги (M0.1), сигнал тревоги будет включен, и его можно остановить, нажав сигнал СТОП PB (I0.4). Примечание: - Вышеприведенная логика приведена только для пояснения. Мы можем реализовать этот пример, также используя логику жесткого реле. Система ПЛК S7-1200 очень дорогая для этой простой системы. Результат -
Программа ПЛК для сумматора расхода
leigehong posted A plc and hmi russian article in PLC programming learning
Создайте программу ПЛК для реализации сумматора для расходомера. Расходомер имеет выход 4-20 мА, который представляет расход топлива в трубе от 0 до 100 литров/час. Программа PLC для сумматора расхода Используя эту логику, мы можем рассчитать общее количество топлива, прошедшего через трубу. Когда значение сумматора достигает 5000 литров, оно автоматически должно быть сброшено, или мы можем сбросить значение с помощью кнопки RESET. Решение проблемы Мы можем решить эту проблему с помощью простой логики. Здесь мы рассмотрим расходомер для измерения топлива с максимальным расходом 100 литров/час. Здесь мы преобразуем этот расход из л/ч в л/сек, используя инструкцию DIV для расчета. После этого, используя тактовый импульс длительностью 1 секунда, мы сохраним это значение в другой ячейке памяти, и каждое второе новое значение будет добавляться и обновляться. Здесь, например, мы считаем, что максимальное значение для сумматора составляет 5000 литров, поэтому после этого значения сумматор должен быть СБРОСЕН. Поэтому мы сравним это значение с фактическим значением и сбросим его автоматически или предоставим кнопку СБРОСА для сброса значения сумматора. Список входов/выходов Список входов Сброс:- I0.0 Память M M0.5:- 1-секундный (1с) тактовый импульс M1.2:- Положительный фронт тактового импульса MD10:- Слово памяти для конечного выхода (л/ч) расходомера MD18:- Слово памяти для конечного выхода (л/с) расходомера MD22:- Общее добавление литров MD26:- Общее количество топлива в литрах Релейная диаграмма для сумматора Объяснение программы В этой задаче мы рассмотрим программное обеспечение S7-300 ПЛК и TIA portal для программирования. Сеть 1: Здесь мы взяли конечное выходное значение расходомера в л/ч (MD10). Используя инструкцию DIV, мы преобразовали поток L/H в L/sec, а конечное значение сохранилось в MD18. Сеть 2: Здесь тактовый импульс 1 с (M0.5) будет добавлять значение каждую секунду и сохранять результат в слове памяти MD22. Сеть 3: Здесь мы переместили значение MD22 в MD26 (общее количество топлива в литрах) для отображения. Сеть 4: В этой сети нам нужно сбросить сумматор. Если общее количество топлива больше 5000 (значение 5000 приведено для примера, оно зависит от конфигурации расходомера и его диапазона), то счетчик сумматора должен автоматически обнулиться или мы можем сбросить его, нажав кнопку RESET (I0.0). Примечание: приведенная выше логика приведена только для пояснения. Здесь мы рассмотрели только конечный вывод масштабирования, поэтому мы не упомянули масштабирование 4-20 мА в логике. Результат -
Примеры программирования таймера ПЛК – TON, TOF, TP и TONR
leigehong posted A plc and hmi russian article in PLC programming learning
Обсудите примеры программирования таймера ПЛК: различные таймеры ПЛК – TON, TOF, TP и TONR. Инструкции таймера ПЛК и примеры логики таймера ПЛК. Программирование таймера ПЛК Реализация таймеров IEC (TON, TOF, TP и TONR) в ПЛК S7-1200 с использованием TIA Portal. Во многих приложениях требуется контролировать время или поток сигналов. Например, клапан или двигатель может нуждаться в управлении для работы в течение определенного интервала времени, включении через определенный интервал времени или после некоторой задержки. Диаграмма проблемы Решение проблемы Для этой проблемы мы будем использовать таймеры IEC (TON, TOF, TP и TONR) в ПЛК S7-1200 с примерами. Существует ряд различных форм таймеров, которые можно найти в ПЛК. Как показано на схеме выше, Таймер задержки включения, который включается после определенной задержки. Таймеры задержки выключения включаются на фиксированный период времени после выключения входа. Импульсный таймер включается или выключается на фиксированный период времени. Аккумуляторный таймер записывает интервалы времени. Здесь рассмотрим пример с четырьмя двигателями и четырьмя ПЕРЕКЛЮЧАТЕЛЯМИ для объяснения таймеров. Нам нужно запустить три двигателя разными способами. Первый двигатель запустится после 10-секундной задержки, второй двигатель запустится немедленно и выключится после 10-секундной задержки, а третий двигатель запустится с импульсом и выключится с 10-секундной задержкой. Четвертый двигатель будет работать в общей сложности 10 секунд. Список входов/выходов Список входов SWITCH 1: I0.0 SWITCH 2: I0.1 SWITCH 3: I0.2 SWITCH 4: I0.3 Сброс: I0.4 Список выходов MOTOR 1: Q0.0 MOTOR 2: Q0.1 MOTOR 3: Q0.2 MOTOR 4: Q0.3 Релейная схема ПЛК для таймеров Мы можем использовать инструкцию Generate-ON-delay или ON delay timer для задержки установки выхода Q на запрограммированную длительность PT. Инструкция запускается, когда результат входа IN изменяется с 0 на 1 (положительный фронт). Вы можете контролировать текущее значение времени на выходе ET блока таймера. Значение таймера начинается с T#0s и заканчивается, когда достигается значение длительности PT. Выход ET сбрасывается, как только состояние сигнала на входе IN меняется на 0. Мы можем использовать инструкцию Generate off-delay или off-delay timer для задержки сброса выхода Q на запрограммированную длительность PT. Выход Q устанавливается, когда результат логической операции (RLO) на входе IN меняется с 0 на 1 (положительный фронт сигнала). Мы можем контролировать текущее значение времени на выходе ET. Мы можем использовать инструкцию Generate impulse для установки выхода Q на запрограммированную длительность. Инструкция запускается, когда результат входа IN меняется с 0 на 1 (положительный фронт). Запрограммированное время (PT) начинается, когда запускается инструкция. В этом таймере даже если обнаружен новый положительный фронт, состояние сигнала на выходе Q не изменяется, пока идет длительность времени PT. Инструкция аккумулятора времени или таймер аккумулятора используется для накопления значений времени в течение периода, установленного параметром запрограммированного времени (PT). Когда состояние сигнала на входе IN изменяется с 0 на 1 (положительный фронт), инструкция выполняется, и начинается отсчет времени PT. В этом случае параметр Q остается установленным на 1, даже когда состояние сигнала на параметре IN изменяется с 1 на 0″ (отрицательный фронт). Вход R сбрасывает выход Q. Описание программы В этой задаче мы рассмотрим программное обеспечение S7-1200 PLC и TIA portal для программирования. Сеть 1: В этой сети мы использовали таймер задержки включения (генерировать задержку включения) для MOTOR 1 (Q0.0). Когда статус SWITCH 1(I0.0) изменится с 0 на 1, инструкция таймера будет выполнена, и она активирует MOTOR 1(Q0.0) после 10-секундной задержки. Сеть 2: В этой сети мы использовали таймер задержки выключения (генерируем задержку выключения) для MOTOR 2(Q0.1). Когда статус SWITCH 2(I0.1) изменится с 0 на 1, инструкция таймера будет выполнена, и она немедленно активирует MOTOR 2(Q0.1). Также, когда статус SWITCH 2(I0.1) изменится обратно на 0, запустится запрограммированное время (PT), и по истечении времени MOTOR 2(Q0.1) будет ВЫКЛЮЧЕН. Сеть 3: В этой сети мы использовали импульсный таймер (генерируем импульс) для MOTOR 3(Q0.2). Когда статус SWITCH 3(I0.2) меняется с 0 на 1, инструкция таймера будет выполнена, и он немедленно активирует MOTOR 3(Q0.2). В этом случае даже обнаружен новый положительный фронт, статус MOTOR 3(Q0.2) не изменяется, пока идет запрограммированное время (PT). Сеть 4: В этой сети мы использовали аккумуляторный таймер (аккумуляторное время) для MOTOR 4(Q0.3). Когда статус SWITCH 4(I0.3) меняется с 0 на 1, инструкция таймера будет выполнена, и MOTOR 4(Q0.3) запустится через 10 с. MOTOR 4(Q0.2) останется включенным, даже если статус входа изменится обратно на 0. Сброс (I0.4) необходим для сброса таймера или накопленного времени. Тестовые случаи во время выполнения -
Программа ПЛК для мигания лампы с интервалом в 5 секунд
leigehong posted A plc and hmi russian article in PLC programming learning
Это программа ПЛК для мигания (ВКЛ/ВЫКЛ) лампы с интервалом в 5 секунд. Мигающая лампа Описание проблемы Включите индикатор или лампу через пять секунд и выключите через пять секунд. Создайте программу, которая включает лампу на 5 секунд, затем выключает на 5 секунд, затем включает на 5 секунд и снова выключает на 5 секунд и так далее. Схема проблемы Решение проблемы Эту проблему можно решить с помощью таймеров. В этом случае мы будем использовать TON (таймер задержки включения). Для пояснения рассмотрим один ПЕРЕКЛЮЧАТЕЛЬ для включения цикла ВКЛ/ВЫКЛ и одну лампу для выхода. Когда пользователь нажимает ПЕРЕКЛЮЧАТЕЛЬ, лампа включается и остается включенной в течение 5 секунд, после чего выключается на 5 секунд. Этот цикл будет повторяться. Список входов и выходов Список входов SWITCH : I0.0 Список выходов Lamp : Q0.0 M Memory M0.0 : битовая память для состояния выключения лампы. Лестничная диаграмма ПЛК для мигающей лампы Объяснение программы В этой задаче мы рассмотрим программное обеспечение S7-1200 PLC и портала TIA для программирования. Сеть 1: В этой сети при нажатии SWITCH (I0.0) при отсутствии состояния выключения лампы лампа (Q0.0) будет включена. Поэтому здесь мы использовали НО контакт SWITCH (I0.0) и НЗ контакт состояния выключения лампы (M0.0). Сеть 2: В этой сети, когда лампа (Q0.0) включена, то будет выполнена инструкция TON (таймер задержки включения), которая установит состояние выключения лампы. Итак, мы взяли здесь НО контакт лампы (Q0.0), таймер TON и запрограммированное время 5 секунд. Сеть 3: Согласно нашему условию, состояние выключения лампы (M0.0) должно быть ВЫКЛ после 5-секундной задержки, поэтому мы снова использовали TON. Итак, мы использовали НО контакт состояния выключения лампы (M0.0) и TON с запрограммированным временем 5 секунд. Результат -
Программа ПЛК для альтернативной выходной цепи с защелкивающейся функцией
leigehong posted A plc and hmi russian article in PLC programming learning
Создайте программу ПЛК для альтернативной выходной цепи с защелкивающейся функцией и объясните логику релейной схемы с решением. Альтернативная выходная цепь Описание проблемы Включение света нажатием ПЕРЕКЛЮЧАТЕЛЯ в первый, третий, пятый раз и т. д. и выключение того же света нажатием ПЕРЕКЛЮЧАТЕЛЯ во второй, четвертый, шестой раз и т. д. Восстановление состояния выхода на «0» при включении питания системы или цикла. Выход может быть ПУСК нажатием КНОПКИ НЕЧЕТНОЕ количество раз и может быть ОСТАНОВЛЕН нажатием той же КНОПКИ ЧЕТНОЕ количество раз. Диаграмма проблемы Решение проблемы Мы можем решить эту проблему с помощью простой релейной логики. В этом мы рассмотрим один простой пример альтернативной работы светодиода. Здесь мы рассмотрим один светодиод и одну КНОПКУ. Нажмите КНОПКУ попеременно, и выход должен быть ВКЛ/ВЫКЛ попеременно, здесь, когда кнопка нажата нечетное количество раз, выход должен быть ВКЛ, а когда кнопка нажата четное количество раз, выход должен быть ВЫКЛ. Список входов и выходов ПЛК Список входов ПЕРЕКЛЮЧАТЕЛЬ: I0.0 Список выходов Светодиод: Q0.0 Память M M0.0 для состояния сброса светодиода M0.1 для сброса счетчика M11.0 и M11.1 – Положительный фронт Релейная диаграмма для альтернативной выходной цепи (с функцией фиксации) Описание программы ПЛК В этом приложении мы использовали ПЛК Siemens S7-300 и программное обеспечение TIA Portal для программирования. Сеть 1: В сети 1 мы использовали инструкцию SET для установки светодиода (Q0.0). Здесь мы взяли НО контакт КНОПКИ (I0.0) поэтому светодиод (Q0.0) можно активировать нажатием КНОПКИ (I0.0). Сеть 2: Здесь мы использовали счетчик, поэтому он будет подсчитывать количество переключений КНОПКИ (I0.0). Этот счетчик сообщит нам о количестве нажатий кнопки, ее значении или значении ЧЕТНОМ или НЕЧЕТНОМ числе. Сеть 3: Когда счетчик достигнет своего предустановленного значения (2) или, скажем, ЧЕТНОГО числа раз, НО контакт счетчика установит M0.0 (условие сброса светодиода). Сеть 4: В этой сети НО контакт M0.0 СБРОСИТ светодиод и счетчик. Здесь M0.1 (память сброса счетчика) СБРОСИТ счетчик. Сеть 5: Если M0.0 включен и сработает отрицательный переход (с 1 на 0) кнопки (I0.0), то состояние RESET светодиода будет выключено. Примечание: этот пример приведен для понимания базовой концепции альтернативной выходной цепи, это не полное приложение, но мы можем использовать эту концепцию в любом приложении автоматизации или любой системе. Тестовые случаи -
SIEMENS-ES Tia Portal – Bloque de organización de interrupción por errores de programación OB121
leigehong posted A plc and hmi article in Spanish in PLC programming learning
En este artículo, continuamos nuestra discusión sobre los diferentes tipos de bloques de organización en los PLC de Siemens. Esta vez, hablaremos sobre el OB121 o la interrupción por errores de programación en el portal Tia. Contenido: ¿Qué son las interrupciones por errores de programación OB121? Ejemplos de errores de programación. ¿Qué sucederá si se detecta un error de programación? Simulación de un error de programación en el portal TIA. ¿Cómo puede ser útil el OB121 contra los errores de programación? Conclusiones. ¿Qué son las interrupciones por errores de programación (OB121)? El OB121 es un bloque de organización que será llamado por el sistema operativo del PLC si ocurre un error de programación mientras se ejecuta su lógica. Tenga en cuenta que no estamos hablando de un error de programación que será detectado por el compilador al intentar descargar su lógica en su PLC. Consulte la imagen 1. Imagen 1: el compilador detectará algunos errores de programación Como puede ver en la última imagen, hay un error de programación en la lógica de mi PLC; faltan algunos operandos en la entrada y salida de la Red 1. Pero el compilador detectó este error incluso antes de descargar la lógica en el PLC. El error de la imagen 1 no es del tipo de error de programación que puede provocar la necesidad de llamar al OB121. Los errores en su programa de PLC que el compilador no puede encontrar, pero que pueden causar problemas en su lógica mientras el PLC está en funcionamiento, son los errores de programación a los que nos referimos. Estos errores activarán una llamada al OB121 por parte del sistema operativo. Ejemplos de errores de programación A continuación, se muestran algunos ejemplos de errores en la lógica de su PLC que pueden causar errores de programación: Se excedió la profundidad máxima de anidamiento de las llamadas de bloque. Ha utilizado un puntero NULL para direccionar un operando. Instrucción desconocida. La cadena direccionada tiene información de longitud incorrecta. Error de longitud de área al leer. Error de longitud de área al escribir. Error en el n.º de temporizador. Acceso a una BD que no está cargada; el número de BD se encuentra en el área permitida. La BD no existe. Estos errores y muchos más pueden provocar errores de programación en su PLC. Puede consultar la sección de Ayuda del TIA Portal para saber qué otras razones pueden provocar errores de programación del PLC. ¿Qué sucederá si se detecta un error de programación? Cuando su PLC detecta un error de programación, puede ocurrir uno de tres eventos. Su PLC mostrará un error y pasará al modo STOP. Su PLC mostrará un error pero seguirá ejecutando su lógica. Su PLC mostrará un error y luego intentará resolver este error. Estos tres eventos dependerán básicamente de la programación de su PLC. Es decir, su código decidirá cómo se comportará el sistema operativo al detectar un error de programación. Simulación de un error de programación en TIA Portal Para comprender mejor cómo se comportará el PLC, crearemos un programa simple donde provocaremos un error de programación y luego veremos qué sucederá. Vea la imagen 2. Imagen 2: lógica de programa simple La lógica que creamos es muy simple: cuando se ha habilitado InitiateProgError, el valor 126 se moverá al área DB52.DBW16. Tenga en cuenta que no hemos creado DB52, por lo que ese será nuestro error de programación. Tenga en cuenta que este error no se detectará durante la compilación o la descarga en el PLC. Vea las imágenes 3 y 4. Imagen 3: error no detectado por el compilador Vea cómo se compiló correctamente el bloque, aunque incluía un error de programación. Imagen 4: bloque descargado en el PLC Nuevamente, el bloque se descargó en el PLC con un error de programación. Ahora, simulemos nuestro programa de PLC y veamos qué sucederá. Vea la animación 1 para la simulación del código del PLC. Animación 1 Como puede ver en la animación anterior, el LED de ERROR del PLC parpadeará en rojo durante unos segundos y luego el PLC pasará al modo STOP. Vaya al diagnóstico en línea del PLC para ver qué sucedió. Vea la imagen 5. Imagen 5: diagnóstico en línea del PLC Lo que vio en la animación es exactamente lo que ve en la imagen anterior. Se pueden mencionar en 3 pasos: El PLC detecta el error de programación que es OB52 no cargado. El sistema operativo activará la llamada al OB121, pero no hay ningún OB121 creado en nuestra lógica. Cuando el PLC descubre que no hay ningún OB121 creado en nuestra lógica, el sistema operativo iniciará una solicitud STOP. Y el PLC pasará al modo STOP. ¿Cómo puede ser útil el OB121 contra los errores de programación? Agreguemos un OB121 a nuestro código de PLC y veamos cómo cambian las cosas. Vea la imagen 6. Imagen 6: Cómo agregar un OB121 Después de crear y agregar el OB121 a nuestra lógica de PLC, veamos qué sucederá en la simulación. Tenga en cuenta que no hemos escrito ninguna lógica de PLC dentro del OB121. Vea la animación 2. Animación 2 Como puede ver en la animación 2, cuando se activa InitiateProgError, el LED de ERROR del PLC parpadeará en rojo, pero el PLC seguirá funcionando. Esto significa que el PLC no entrará en modo STOP. Revisemos los diagnósticos en línea para ver qué sucedió realmente. Vea la imagen 7. Imagen 7: el error no provocó la detención del PLC En la imagen se puede ver que el PLC detecta el error pero no entra en modo STOP. Omitirá este error, continuará el ciclo y comenzará de nuevo desde el principio. Cuando llegue al error nuevamente, lo detectará nuevamente y emitirá una alarma en los diagnósticos. Omitirá el error y continuará. Eso significa que el PLC emitirá la misma alarma en cada ciclo de escaneo. Y es por eso que en la imagen se ve que el evento sigue activándose y la alarma se repite en cada ciclo de escaneo. Por lo tanto, tener un OB121 vacío le brindará el beneficio de mantener el PLC en funcionamiento y, por extensión, mantener su proceso en funcionamiento. Pero hay más que podemos hacer, podemos intentar detectar este error y eliminarlo. Además, podemos intentar mostrar el tipo de error de programación detectado. Determinar el tipo de error El OB121 tiene un identificador de ID de falla interno que podemos usar para mostrar el tipo de falla, tal vez como una alarma en una HMI. Dentro del OB121 crearemos una instrucción MOVE simple, donde enviaremos la entrada Fault_ID del OB121 a un área de memoria definida dentro de nuestra base de datos global. Ver imagen 8. Imagen 8: Identificación del tipo de error Como puede ver en la imagen anterior, cuando ocurre el error de programación, el Fault_ID se enviará a Data.ProgErrorID. Ver imagen 9. Imagen 9: Error de programación Fault_ID Puede ver que el ID de falla es 3A. Si consulta la ayuda del TIA Portal, puede encontrar el significado de esta falla. 3A: Acceso a una base de datos que no está cargada; el número de base de datos se encuentra en el área permitida. Captura del error Esto simplemente significa intentar resolver el error de programación del PLC después de haber identificado la razón. Esto dependerá principalmente de cuál es el error y cómo desea manejarlo. Simplemente simularemos una solución al error para ver cómo se comportará el PLC. La solución real para el error que creamos será simplemente crear el DB52 o usar un bloque de datos que ya esté creado. Pero para el bien de la simulación, simplemente agregaremos un contacto simple que se abrirá cuando ocurra el error de programación para capturar este error. Vea las imágenes 10 y 11. Imagen 10: Captura del error Siempre que se llame a OB121, se establecerá CatchError. Imagen 11: eliminar el error Siempre que se llame a OB121, se activará CatchError y se utilizará para detectar el error de programación en la red 1. Consulte la animación 3 para ver la simulación del PLC. Animación 3 En la animación anterior, puede ver que cuando se activa InitiateProgError, el PLC entrará en error por un momento, luego el error se borrará y el PLC estará en modo RUN todo el tiempo. Conclusión El solo hecho de tener un OB121 vacío en su lógica garantizará que su PLC no entre en modo STOP si hubo un error de programación en su código. Luego puede usar el OB121 para identificar también el error y resolverlo. -
Programación de PLC para sistema de control de tráfico en cruces en T
leigehong posted A plc and hmi article in Spanish in PLC programming learning
Este artículo trata sobre un sistema de control de tráfico en cruces en T con la ayuda de una lógica de escalera de PLC que utiliza un comparador para el funcionamiento de las luces. Sistema de control de tráfico en cruces en T La función del sistema de control de tráfico en cruces en T consta de tres grupos de segmentos. Mediante la lógica de funcionamiento del comparador, controlamos el sistema de semáforos. Primer segmento: En el primer segmento, se permite el tráfico en el carril 1 y se detienen los carriles 2 y 3. Aquí, en este segmento, se enciende la luz verde (Verde 1) del carril 1 y se encienden las luces rojas (Rojo 2) del carril 2 y (Rojo 3) del carril 3. Este período continúa durante quince segundos. Segundo segmento: En el segundo segmento, se permite el tráfico en el carril 2 y se detienen los carriles 1 y 3. Aquí, en este segmento, se enciende la luz verde (Verde 2) del carril 2 y se encienden las luces rojas (Rojo 1) del carril 1 y (Rojo 3) del carril 3. Este período continúa durante quince segundos. Tercer segmento: En el tercer segmento, se permite el tráfico del carril 3 y se detienen los carriles 1 y 2. Aquí, en este segmento, se enciende la luz verde (Verde 3) del carril 3 y se encienden las luces rojas (Rojo 1) del carril 1 y (Rojo 2) del carril 2. Este período continúa durante quince segundos. Después de la ejecución de los tres segmentos, la secuencia de operaciones comienza nuevamente y se repite de forma continua. Descripción de entradas y salidas En este proyecto de PLC, utilizamos 2 entradas, 6 salidas, 2 memorias y 1 temporizador de retardo de encendido. S.No Símbolo Descripción 1 Yo 0.0 COMENZAR 2 Yo 0.1 DETENER 3 M 0,0 MEMORIA 4 M 0,1 MEMORIA 1 5 Q 0.0 VERDE 1 6 Q 0,1 ROJO 1 7 Q 0,2 VERDE 2 8 Q 0,3 ROJO 2 9 Q 0,4 VERDE 3 10 Q 0,5 ROJO 3 11 DB1 TEMPORIZADOR DE RETARDO DE ENCENDIDO Programación del PLC y su explicación 1. Cuando se presiona el botón INICIO (I 0.0), se activa la MEMORIA (M 0.0). Esta M 0.0 es la memoria principal que se utiliza para ejecutar todos los procesos del programa. Dado que está bloqueada, solo estará activada. Si se presiona DETENER (I 0.1), todo el proceso se detendrá en cualquier momento. 2. Una vez que se activa la MEMORIA, se activa el TEMPORIZADOR DB1 que controla la sincronización de la intersección de tráfico. En este temporizador, establecemos el tiempo preestablecido de 45 segundos. Una vez que el temporizador alcanza el tiempo preestablecido que activa la MEMORIA 1 (M 0.1) y este M 0.1 también reinicia el temporizador según la lógica y ejecuta el ciclo de forma continua. 3. A continuación, el comparador desempeña un papel importante en el control de la intersección de tráfico. En primer lugar, se activa la salida VERDE 1 (Q 0.0) según la lógica. Aquí usamos Menor o igual que el comparador. En esta lógica, Q0.0 estará en el estado ENCENDIDO desde 0 segundos hasta 15 segundos. Después de eso, pasará al estado APAGADO 4. A continuación, para la salida ROJA 1 (Q0.1), usamos Mayor o igual que para que funcione. Q0.1 estará en estado ON desde 15 segundos hasta 45 segundos. Estará en estado OFF cuando Q0.0 esté en estado ON. 5. Luego, para la salida VERDE 2 (Q0.2), usamos Menor o igual a y Mayor o igual a para esta salida. Ambas funciones de comparación se conectaron en conexión lógica en serie con la salida. En este caso, Q0.2 estará en estado ON desde 16 segundos hasta 30 segundos según la condición. 6. Luego, para la salida ROJA 2 (Q0.3), también usamos Menor o igual a y Mayor o igual a para realizar la operación. Los comparadores se conectaron en conexión paralela con la salida. Esta salida estará en estado ON desde 0 segundos hasta 15 segundos y desde 30 segundos hasta 45 segundos. Entre 15 segundos, estará en estado OFF solo porque en ese momento Q0.2 está en estado ON. 7. Luego, para la última salida VERDE 3 (Q0.4), usamos Mayor o igual para que funcione. Según la lógica condicional, estará en estado ENCENDIDO desde 30 segundos hasta 45 segundos. Antes de este tiempo, estará en estado APAGADO. 8. Finalmente, la salida ROJA 3 (Q0.5). Aquí usamos Menor o igual para que funcione para ejecutar la lógica del PLC. Estará en estado ENCENDIDO desde 0 segundos hasta 30 segundos, luego estará en estado APAGADO. Conclusión Entonces, de esta manera, el control de tráfico de la intersección en T dado se ejecuta mediante la función de comparación con la lógica del PLC. Podemos controlar la lógica del tráfico con la ayuda de la lógica del PLC de muchas maneras y esta es también una de ellas. -
Fuente de alimentación y voltajes de funcionamiento del PLC
leigehong posted A plc and hmi article in Spanish in PLC programming learning
Cuando trabaja con un PLC, necesita saber qué tipos de voltajes están generalmente disponibles en él; para que pueda realizar el cableado en consecuencia. No solo la fuente de alimentación, sino que también debemos estar relacionados con el voltaje de entrada y salida requerido. Cada fabricante de PLC tiene su propio conjunto de rangos de voltaje y corriente según el módulo y la CPU que proporciona. En este artículo, aprenderemos los voltajes de funcionamiento del PLC generalmente disponibles en todas partes. Fuente de alimentación del PLC En la norma, el PLC opera en cuatro tipos de voltajes: 24 V CC, 24 V CA, 110 V CA y 240 V CA. En algunos PLC, solo la CPU requiere una fuente de alimentación y los módulos de E/S se alimentan de la placa base de la CPU, mientras que en algunos PLC, todos los módulos, incluida la CPU, las entradas y las salidas, requieren una fuente de alimentación. En cualquier caso, necesitará una fuente de alimentación conmutada o un transformador en el panel del PLC para convertir el voltaje de potencia bruta. En cuanto al voltaje de alimentación de CA, algunos PLC ofrecen un rango de voltaje de 110 a 240 V CA. Cada punto de alimentación del PLC tiene un punto de conexión a tierra para brindar seguridad al PLC en caso de sobretensión o cortocircuito. Cuando se utiliza una fuente de alimentación de CA, generalmente está equipada con un fusible de protección en su interior. La fuente de alimentación de CC también tiene un fusible en su interior, pero para la fuente de alimentación de CA, es obligatorio usarlo debido a la gran cantidad de voltaje involucrado. Cuando se proporciona el voltaje nominal en la CPU, significa que el voltaje que está proporcionando se ha estabilizado correctamente y se ha controlado en gran medida. Sin embargo, no es práctico que el voltaje permanezca constante a 24 V o 240 V. Por lo tanto, un rango de voltaje nominal viene para un PLC como 20-28 V CC o 220 V-245 V CA. Este rango está predefinido en cada PLC para que obtenga un área de suministro de energía para trabajar con ellos de manera eficiente, sin ningún problema. Fuente de alimentación para módulos de E/S Ahora, pasemos al siguiente tema sobre la fuente de alimentación necesaria para los módulos de E/S. Como se mencionó anteriormente, hay dos tipos de fuentes de alimentación disponibles: una en la que el módulo se alimenta mediante la placa base de la CPU y otra en la que el módulo requiere una fuente de alimentación externa. Al utilizar la placa base, cada CPU tiene una clasificación de mA que proporcionará como carga a los módulos conectados. Por ejemplo, si una CPU tiene una clasificación de 24 V CC – 450 mA, también especificará que la placa base de la CPU puede proporcionar esta cantidad de corriente a los módulos de E/S y solo puede conectar esa cantidad de módulos al bastidor de la CPU. Además, cada módulo especificará cuánta corriente consumirá cuando se conecte a un bus de placa base. Esto puede ayudarlo a seleccionar los módulos y la CPU adecuados para una aplicación específica. En cuanto al segundo tipo de fuente de alimentación, hay algunos módulos que requieren una fuente de alimentación externa. Por lo tanto, en ese caso, debe elegir una fuente de alimentación conmutada o un transformador con una corriente y una clasificación de carga más altas en consecuencia. Esto, a su vez, puede alimentar tanto la CPU como los módulos correctamente y también alimentar otros componentes del panel que requieren la misma fuente de alimentación. Fuente de alimentación para instrumentos de campo El cableado de campo para un PLC también requiere principalmente voltaje de CC para instrumentos y voltaje de CA para dispositivos de alta potencia. Por lo tanto, los cuatro voltajes mencionados anteriormente funcionan de la misma manera para el cableado de suministro común del módulo de E/S. Además, recuerde que, en su mayoría, hay una batería de respaldo dentro del PLC, además de la fuente de alimentación estándar. Esto garantiza que el programa dentro de la memoria del PLC permanezca intacto en caso de un corte de energía. Selección de fuente de alimentación para PLC Al seleccionar la fuente de alimentación, es necesario considerar los siguientes parámetros en general: voltaje nominal, corriente nominal, potencia nominal, ondulación y ruido, rango ajustable de voltaje, tolerancia de voltaje, regulación de línea y regulación de carga. Una vez que haya seleccionado la fuente de alimentación correcta, puede cablear la CPU y los módulos para encenderlos correctamente. De esta manera, entendemos el concepto de voltajes operativos del PLC. -
PLC vs PAC - comprensión de las principales diferencias y similitudes
leigehong posted A plc and hmi article in Spanish in PLC programming learning
Los controladores lógicos programables (PLC) y los controladores de automatización programables (PAC) son dos tipos de controladores industriales que se utilizan para automatizar procesos y máquinas en la fabricación, el procesamiento y otras aplicaciones industriales. Ambos tipos de controladores tienen funciones similares, pero también existen diferencias significativas entre ellos. En este artículo, analizaremos las diferencias, similitudes y ejemplos de PLC y PAC. Contenido: ¿Qué son los PLC? ¿Qué son los PAC? Similitudes entre PLC y PAC. Diferencias entre PLC y PAC. Ejemplos de modelos de PLC de varios proveedores. Ejemplos de modelos de PAC de varios proveedores. ¿Cuándo es más adecuado un PLC? ¿Y cuándo lo es un PAC? Conclusión ¿Qué es un PLC? PLC significa controlador lógico programable, que es una computadora industrial especializada que se utiliza para sistemas de control de automatización. El PLC está diseñado para funcionar en entornos hostiles y se utiliza para controlar maquinaria en plantas de fabricación, líneas de montaje y otros entornos industriales. Los PLC se pueden programar utilizando 5 lenguajes diferentes, como lógica de escalera, diagramas de bloques de funciones, texto de estructura, lista de instrucciones y diagramas secuenciales. Estos 5 lenguajes están aprobados y se aplican según las normas IEC 61131-3. ¿Qué es un PAC? PAC significa Controlador de automatización programable, que es similar a un PLC pero tiene una funcionalidad más avanzada. PAC combina las capacidades de un PLC tradicional con la capacidad de realizar tareas mucho más complicadas y comunicarse con otros dispositivos y sistemas, lo que los hace más flexibles y potentes que los PLC. PAC se utiliza normalmente para aplicaciones de control y automatización más complejas en industrias como la automotriz, la aeroespacial y la generación de energía. PAC se puede programar utilizando los mismos 5 lenguajes que los PLC, pero también se pueden programar utilizando C y C++, lo que les da la capacidad de manejar la codificación de algoritmos más complejos. Similitudes entre PLC y PAC Las similitudes entre PLC y PAC son tantas que a veces es difícil decir si son diferentes. Aunque todavía hay alguna diferencia entre ellos. Las similitudes que comparten pueden ser incluso mayores. Estos son algunos de los puntos en común entre los PLC y los PAC: Funcionalidad básica Tanto los PLC como los PAC están diseñados para proporcionar un control fiable y preciso de los sistemas de automatización industrial. Se utilizan para supervisar las entradas de los sensores y otros dispositivos, procesar la información y luego enviar señales de control a los actuadores y otros equipos. Programación Tanto los PLC como los PAC utilizan lenguajes de programación para crear una lógica de control que determina el comportamiento del sistema de automatización. Comparten los 5 lenguajes de programación definidos en las normas IEC 61131-3, pero los PAC ofrecen más opciones de lenguajes de programación, incluidos C y C++. Durabilidad Tanto los PLC como los PAC están diseñados para soportar entornos industriales hostiles, como temperaturas extremas, humedad y vibración. Están diseñados para ser resistentes y fiables, con una larga vida útil y menores requisitos de mantenimiento. Diseño modular Tanto los PLC como los PAC tienen un diseño modular, que permite una fácil expansión y personalización. Se pueden añadir o quitar módulos para cumplir con requisitos específicos. Estándares de la industria Tanto los PLC como los PAC están diseñados para cumplir con los estándares de la industria para sistemas de automatización y control, como IEC 61131. Estos estándares garantizan la interoperabilidad entre dispositivos y sistemas de diferentes fabricantes. Diferencias entre PLC y PAC La distinción entre PAC y PLC puede ser un tanto confusa. Si bien no existe una definición de lo que constituye un PAC, existen algunas características comunes que diferencian a PAC de PLC: Funcionalidad Si bien tanto los PLC como los PAC se utilizan para aplicaciones de automatización y control, los PAC tienen una funcionalidad más avanzada, como control de movimiento, control de procesos y adquisición de datos. Los PAC también suelen tener más potencia de procesamiento y memoria que los PLC. Conectividad Los PAC tienen opciones de conectividad más avanzadas que los PLC, incluidas Ethernet, USB e inalámbricas. Esto hace que sea más fácil integrarlos en sistemas de automatización más grandes y comunicarse con otros dispositivos y sistemas. Costo Debido a su funcionalidad y flexibilidad más avanzadas, los PAC generalmente son más costosos que los PLC. Características más avanzadas Los PAC suelen tener funciones de software más avanzadas que los PLC, como control de movimiento integrado, registro de datos y herramientas de diagnóstico avanzadas. Estas funciones facilitan a los ingenieros y técnicos la supervisión y resolución de problemas del sistema de control. Ejemplos de modelos de PLC de varios proveedores PLC Siemens S7-1500: Se trata de un PLC de alto rendimiento de Siemens, uno de los principales proveedores de automatización. Está diseñado para aplicaciones exigentes y ofrece funciones avanzadas como control de movimiento, seguridad y protección. Consulte la imagen 1. Imagen 1: PLC SIEMENS S7-1500 PLC Allen-Bradley CompactLogix 5370: Este es un PLC versátil de Rockwell Automation que ofrece una amplia gama de opciones de E/S y protocolos de comunicación. Es adecuado para una variedad de aplicaciones, incluido el control de máquinas y la automatización de procesos. Consulte la imagen 2. Imagen 2: PLC CompactLogix 5370 de Allen-Bradley PLC de la serie Q de Mitsubishi Electric: Este es un PLC confiable de Mitsubishi Electric que ofrece procesamiento de alta velocidad, opciones de E/S flexibles y capacidades de programación avanzadas. Es adecuado para una variedad de aplicaciones, incluidas las de automoción, alimentos y bebidas y productos farmacéuticos. Consulte la imagen 3. Imagen 3: PLC de la serie Q de Mitsubishi Electric PLC de la serie NJ de Omron: Este es un PLC de alta velocidad y alto rendimiento de Omron que ofrece control de movimiento avanzado y capacidades de red. Es adecuado para una variedad de aplicaciones, incluidas las de envasado, impresión y fabricación de semiconductores. Consulte la imagen 4. Imagen 4: PLC de la serie NJ de Omron PLC TwinCAT de Beckhoff: Se trata de un PLC basado en software de Beckhoff que se ejecuta en una plataforma basada en PC. Ofrece funciones avanzadas, como control de movimiento, CNC y robótica, y es adecuado para una variedad de aplicaciones, incluido el control de máquinas y la automatización de procesos. Consulte la imagen 5. Imagen 5: PLC basado en PC TwinCAT CX9240 de Beckhoff Ejemplos de modelos de PAC de varios proveedores PAC DCS DeltaV de Emerson: Se trata de un PAC de sistema de control distribuido (DCS) de Emerson. Está diseñado para aplicaciones de control continuo complejas y ofrece funciones avanzadas, como modelado de procesos, gestión de lotes y control avanzado. Consulte la imagen 6. Imagen 6: PAC Emerson DeltaV DCS PAC Schneider Electric Modicon M340: Se trata de un PAC de alto rendimiento de Schneider Electric que ofrece funciones avanzadas como control de movimiento, seguridad y ciberseguridad. Es adecuado para una variedad de aplicaciones, incluidas la energía, el tratamiento del agua y la minería. Consulte la imagen 7. Imagen 7: PAC Modicon M340 A continuación, se muestran otros ejemplos de PAC: PAC ABB AC 800M PAC Yokogawa ProSafe-RS PAC Phoenix Contact PLCnext Technology PAC Bosch Rexroth IndraMotion MLC ¿Cuándo es más adecuado un PLC? ¿Y cuándo un PAC? El PLC y el PAC se utilizan en diferentes tipos de aplicaciones de automatización según los requisitos específicos de esa aplicación. A continuación, se ofrecen algunas pautas generales sobre dónde se adapta mejor un PLC y dónde se adapta mejor un PAC: Los PLC son la mejor opción en: Aplicaciones de control discreto: Los PLC son más adecuados para aplicaciones que implican un control discreto, como controlar el funcionamiento de una cinta transportadora, un equipo de clasificación o una maquinaria de envasado. Sistemas de control simples: Los PLC son ideales para aplicaciones que tienen un sistema de control relativamente simple que se puede programar mediante lógica de escalera u otros lenguajes de programación similares. Aplicaciones sensibles al costo: Los PLC son generalmente menos costosos que los PAC, lo que los convierte en una buena opción para aplicaciones donde el costo es un factor significativo. Sistemas de tamaño pequeño a mediano: Los PLC son adecuados para sistemas de control de tamaño pequeño a mediano, donde la cantidad de entradas y salidas es relativamente baja. Un sistema de cinta transportadora en una planta de fabricación es un buen ejemplo de un sistema de automatización donde un PLC es la mejor opción. En esta aplicación, el PLC es responsable de controlar la velocidad y la dirección de la cinta transportadora, así como de monitorear el estado de los sensores y otros equipos a lo largo de la línea de la cinta transportadora. El PLC también se puede programar para manejar tareas de producción específicas, como clasificar, contar o empaquetar. Un sistema transportador normalmente tiene una estructura fija y un conjunto bien definido de operaciones que deben ejecutarse de manera secuencial. Los PLC son adecuados para este tipo de aplicación porque están diseñados para manejar tareas de control discretas y son muy confiables en su funcionamiento. Los PLC se pueden programar y configurar fácilmente para manejar diferentes tipos de sensores, actuadores y protocolos de comunicación. Los PAC son ideales para: Aplicaciones de control de procesos: Los PAC son ideales para aplicaciones que involucran control de procesos, como controlar el funcionamiento de una planta química, una planta de tratamiento de agua o una planta de energía. Sistemas de control complejos: Los PAC son ideales para aplicaciones que tienen un sistema de control complejo que requiere algoritmos avanzados y funciones de optimización. Sistemas a gran escala: Los PAC son adecuados para sistemas de control a gran escala, donde la cantidad de entradas y salidas es alta y el sistema está distribuido en un área grande. Aplicaciones de alto rendimiento: PAC capaz de manejar aplicaciones de alto rendimiento que requieren procesamiento rápido de datos, control en tiempo real y alta confiabilidad. Un sistema de control de una planta de energía es un buen ejemplo de un sistema de automatización en el que un PAC es la opción más adecuada. En esta aplicación, el PAC es responsable de controlar y supervisar una gran cantidad de procesos y equipos complejos, como turbinas, generadores, calderas y bombas. El PAC también es responsable de recopilar y analizar datos de varios sensores y otras fuentes y tomar decisiones basadas en esos datos para optimizar el rendimiento de la planta. Un sistema de control de una planta de energía es un entorno muy complejo y dinámico, con muchos procesos y equipos diferentes que funcionan simultáneamente. Los PAC son adecuados para este tipo de aplicación porque ofrecen funciones avanzadas como control distribuido, redundancia y tolerancia a fallas, que son esenciales para garantizar la confiabilidad y la seguridad de la planta. Los PAC pueden manejar grandes cantidades de datos y pueden programarse para realizar algoritmos complejos y tareas de optimización. Conclusión Tanto el PLC como el PAC se utilizan en aplicaciones de automatización industrial. Tienen diferentes capacidades y son los más adecuados para diferentes tipos de aplicaciones. Al seleccionar entre PLC y PAC, es esencial considerar los requisitos específicos de la aplicación. Los PLC se utilizan normalmente en aplicaciones de control discreto que tienen un sistema de control relativamente simple. Los PAC se utilizan en aplicaciones de control de procesos que tienen un sistema de control complejo y requieren algoritmos avanzados y funciones de optimización. -
Diferencia entre microcontrolador y PLC
leigehong posted A plc and hmi article in Spanish in PLC programming learning
Controlar un proceso en cualquier máquina o sistema siempre ha sido una fantasía para los ingenieros. Gracias al advenimiento de la tecnología, se han desarrollado muchos controladores para controlar un proceso de forma flexible y confiable. Entre los controladores, hay dos tipos generales que se utilizan ampliamente en muchos procesos, desde pequeña escala hasta gran escala. Son microcontroladores y PLC. Pueden realizar todas las operaciones, desde pequeños cálculos hasta algoritmos complejos, rendimiento lógico y procesamiento de datos. Esto hace que la tarea sea más fácil al automatizar el proceso. En esta publicación, veremos la diferencia entre microcontrolador y PLC. ¿Qué es un microcontrolador? Primero, comprendamos los conceptos básicos. Tiene un botón pulsador y una lámpara. Se le pide que encienda la lámpara después de 5 segundos de presionar el botón pulsador. De estos, ¿qué necesitamos para ejecutar esta tarea? Necesitará una entrada (botón pulsador), una salida (lámpara), un controlador para ejecutar esta tarea (tipo procesador), una fuente de alimentación para alimentar los circuitos y una memoria para almacenar esta lógica y el estado de las entradas y salidas. Esto, cuando se combina en un solo paquete, forma un microcontrolador. En resumen, un microcontrolador es un tipo de computadora pequeña que toma entradas físicas, procesa la lógica de acuerdo con ellas y enciende o apaga las salidas físicas. Es un pequeño dispositivo tipo chip que incorpora todos estos circuitos en él, como un pequeño paquete, y realiza todo el trabajo de procesamiento y control. Un microcontrolador manejará una pequeña cantidad de entradas y salidas. Por ejemplo, considere un pequeño circuito de pantalla como LED o LCD montado en un dispositivo portátil. Si presiona un botón pulsador en él, mostrará el número correspondiente en la pantalla. Y cuando presione otro botón pulsador, mostrará algún otro número escrito de acuerdo con la lógica dentro del procesador. Esto significa que primero fue programado para mostrar un número y luego, al presionar el segundo botón, se mostraría un número calculado. Todos estos cálculos, el manejo del almacenamiento de variables y el procesamiento de E/S se realizan dentro de este chip de microcontrolador. ¿Qué es un PLC? Pasemos a un nivel superior de procesamiento. Tienes 50 sensores, ya sea de 4-20 mA o de termopar. Tienes 20 tipos diferentes de salidas, ya sean actuadores de 0-10 V CC o salidas de relé. Se te ha asignado la misma tarea de aceptar entradas y controlar salidas de acuerdo con la lógica escrita en él. Se requerirán los mismos componentes de E/S, fuente de alimentación, procesador y memoria. Pero, puedes ver que todas estas placas/pines de E/S con memoria y procesador no se pueden integrar en un solo chip pequeño. Aquí es cuando entra en escena el PLC. El PLC es básicamente una extensión del microcontrolador. Es un dispositivo tipo caja de gabinete que tiene placas de E/S, memoria y un procesador; todos interconectados entre sí en diferentes chips. Todos estos chips forman un solo gabinete de PLC. Los IO pueden ser de diferentes tipos, desde señales digitales simples hasta señales analógicas complejas. Tienen placas de comunicación especiales, que pueden comunicarse con protocolos de la vida real como Ethernet, Modbus, CAN Open, Profibus, Profinet, etc. Los microcontroladores también tienen placas de comunicación, pero tienen interfaces pequeñas y conectividad limitada. Los módulos IO están integrados en el PLC principal o conectados a módulos remotos a través de la comunicación. Esto permite fácilmente la expansión de IO. Varios sensores y actuadores industriales de alta calidad se pueden interconectar fácilmente con PLC. Diferencia entre microcontrolador y PLC Ahora que hemos entendido su significado, echemos un vistazo a sus diferencias: Solo en la definición, supimos que un PLC puede manejar una gran cantidad de procesos y ciclos. Por eso, es mejor usarlo para aplicaciones industriales. Los microcontroladores no pueden atender una gran cantidad de IO con requisitos complejos de cableado y comunicación. Es más adecuado para aplicaciones a pequeña escala. El procesamiento de señales es mucho más flexible en PLC en comparación con un microcontrolador. Esto significa que la conversión de analógico a digital, las entradas y salidas de contadores de alta velocidad se configuran más fácilmente en un PLC que en un microcontrolador. Los microcontroladores son más económicos que los PLC, debido a la cantidad limitada de funciones que ofrecen. La principal ventaja del PLC es su robustez y estabilidad. Con una temperatura muy alta y resistencia ambiental, es el producto más adecuado para entornos críticos, riesgosos y hostiles. El PLC puede ser mucho más propenso al ruido electromagnético y otros tipos de ruido que un microcontrolador. La programación es mucho más fácil en un PLC que en un microcontrolador. Los microcontroladores utilizan software complejo como C y C++ para la programación, lo que es mucho más fácil en un PLC ya que tiene lenguajes que se correlacionan fácilmente con la comprensión de un esquema eléctrico. Los microcontroladores requieren conocimientos de sistemas integrados, VLSI y software para diseñarlos, mientras que los programadores de PLC requieren conocimientos de automatización industrial, instrumentación y redes para diseñarlos. -
¿Qué son las secuencias FIFO y LIFO en PLC?
leigehong posted A plc and hmi article in Spanish in PLC programming learning
La lógica secuencial es de gran utilidad en la programación de PLC. Ayuda a ordenar las cosas fácilmente. Una amplia gama de aplicaciones que utilizan PLC tienen alguna lógica secuencial escrita en ellas. Dos de las secuencias más utilizadas son LIFO y FIFO. Seguramente habrás oído los nombres en electrónica cuando se utilizan para apilar y secuenciar. Estos tipos de lógica secuencial también están disponibles en PLC. En este artículo, aprenderemos los conceptos de secuencia LIFO y FIFO en la programación de PLC. Secuencia FIFO en PLC FIFO significa primero en entrar, primero en salir. El significado de esta secuencia se puede entender fácilmente a partir de su nombre. Lo que llega primero saldrá primero. Introduces un elemento y, cuando solicitas un elemento, se te proporcionará el primero que se introduzca. Esta misma lógica funciona en la programación de PLC para la secuencia FIFO. En programación, se asigna un bloque lógico llamado FIFO. Puede almacenar hasta 16 palabras o más, según el PLC. Contiene tres tipos de entradas: reinicio, almacenamiento y recuperación. En un flanco ascendente de la entrada de reinicio, la secuencia se reinicia y se vacía. En un flanco ascendente de la entrada de almacenamiento, la palabra presente en la entrada se almacena en el bloque. El bloque memorizará la secuencia de palabras recibidas. En un flanco ascendente de la entrada de recuperación, la palabra ingresada primero se dará en la palabra de destino configurada por el programador del PLC. Tiene dos salidas: vacía y llena. Si el bit vacío es verdadero, entonces indica que el almacenamiento está vacío, y si la entrada llena es verdadera, entonces indica que el almacenamiento está lleno. Secuencia LIFO en PLC LIFO significa último en entrar, primero en salir. El significado de esta secuencia se puede entender fácilmente a partir de su nombre. Lo que llega último saldrá primero. Usted ingresa un elemento; y cuando solicita un elemento, se le proporcionará el último que se ingrese. Esta misma lógica funciona en la programación de PLC para la secuencia LIFO. En programación, se asigna un bloque lógico llamado LIFO. Puede almacenar hasta 16 palabras o más, según el PLC. Contiene tres tipos de entradas: reinicio, almacenamiento y recuperación. En un flanco ascendente de la entrada de reinicio, la secuencia se reinicia y se vacía. En un flanco ascendente de la entrada de almacenamiento, la palabra presente en la entrada se almacena en el bloque. El bloque memorizará la secuencia de palabras recibidas. En un flanco ascendente de la entrada de recuperación, la palabra que se ingresó en último lugar se dará en la palabra de destino configurada por el programador. Tiene dos salidas: vacía y llena. Si el bit vacío es verdadero, entonces indica que el almacenamiento está vacío, y si la entrada llena es verdadera, entonces indica que el almacenamiento está lleno. Estas secuencias son bastante fáciles de operar. El programador debe tener cuidado de que no se entreguen entradas simultáneamente a los bloques de almacenamiento. El bloque no realizará ninguna acción en este caso. Solo se debe dar una entrada a la vez. También se debe tener en cuenta que los distintos PLC funcionan de manera diferente en el reinicio en caliente o en el reinicio en frío. En general, en un reinicio en frío del PLC, por ejemplo, el registro se restablecerá y, en caso de un reinicio en caliente, el registro permanecerá intacto tal como está. Depende del fabricante. -
Herramientas necesarias para que un programador de PLC las lleve consigo en el lugar de trabajo
leigehong posted A plc and hmi article in Spanish in PLC programming learning
Siempre que un programador de PLC visita un lugar de trabajo para la puesta en servicio o para alguna llamada de servicio, debe saber qué herramientas debe tener consigo antes de comenzar a trabajar. Esto se debe a que la mayoría de los lugares de trabajo son muy remotos y no todos los materiales serán fácilmente accesibles si se olvidan de llevarlos. Por lo tanto, si tiene el cuidado adecuado y lleva consigo los materiales necesarios, podrá realizar su trabajo fácilmente. En general, hay mucha confusión cuando los programadores leen la lista de tareas pendientes; por lo tanto, pensé en mencionarla de manera sencilla para que puedan comprenderla rápidamente. Herramientas del programador de PLC A continuación se mencionan las principales herramientas necesarias para un programador de PLC. Computadora portátil con software de PLC instalado Cables de interfaz USB a PLC Cables Ethernet Juego de destornilladores Medidores de prueba eléctricos (multímetro) Pelacables Cortadores de cables Destornillador para bloque de terminales Cinta aisladora Disco duro portátil o unidad flash USB Herramienta de crimpado RJ45 Convertidores seriales (RS232 a USB, etc.) Herramientas de configuración de IP (opcional) Etiquetadora para etiquetar cables Conmutador Ethernet industrial Calibrador de bucle para señales analógicas Alicates aislados Cuaderno y bolígrafo para documentación Impresora portátil para etiquetas en el sitio Correa de muñeca antiestática Nota: Las herramientas necesarias pueden variar según la marca y el modelo específicos del PLC y la naturaleza del trabajo en el sitio. Asegúrese siempre de llevar también el equipo de protección personal (EPP) necesario. En esta publicación, veremos las herramientas que un programador de PLC debe llevar en el sitio. Portátil adecuado Este es el primer y más importante requisito básico. Un portátil deficiente con una pantalla o hardware rotos o un rendimiento de RAM lento o poca memoria puede obstaculizar gravemente el trabajo del programador. Todo el software necesario debe estar presente en el portátil que el programador haya utilizado. Cualquier software instalado incorrectamente puede estropear su trabajo de forma muy grave. Todos sus puertos de comunicación deben funcionar correctamente. El cargador del portátil debe ser adecuado. Aparte de esto, los adaptadores de red como el Wi-Fi deben funcionar correctamente. Cables de programación Cuando un programador de PLC va al sitio, básicamente va a conectarse a algún dispositivo de automatización. Para eso, todos los cables de programación necesarios deben estar presentes junto con él. Debe verificar estos cables en la oficina antes de ir al sitio. Por ejemplo, si un PLC tiene un puerto USB, un puerto LAN y un puerto RS485, entonces debe llevar al menos cables USB y LAN, que son fáciles de conseguir. Llevar solo un cable es arriesgado. Memoria USB / Disco duro portátil El almacenamiento externo es un requisito indispensable porque puede requerirlo en cualquier momento para transferir archivos o almacenar copias de seguridad. El almacenamiento debe tener suficiente espacio libre para almacenar datos cuando sea necesario. Hoy en día, muchos dispositivos de automatización vienen con un puerto USB (memoria USB); por lo que llevarlo es una ventaja adicional para la seguridad, si los cables no funcionan. Ratón En el sitio, los programadores de PLC la mayor parte del tiempo enfrentan la presión de completar las tareas a tiempo. Trabajar con paneles táctiles de portátiles consume mucho tiempo. Además, el diseño gráfico se vuelve frenético con un panel táctil de portátil. Por lo tanto, llevar un ratón USB les ayuda a completar la tarea con mucha facilidad. Juego de destornilladores Un destornillador es una herramienta muy importante para un programador de PLC. Si enfrenta algún problema de cableado en el sitio o si el electricista necesita ayuda adicional, entonces los destornilladores de varios tamaños serán muy útiles. Además, el programador de PLC puede trabajar de forma independiente en algún cableado eléctrico sin la ayuda de alguien, para resolver rápidamente cualquier problema. Pelacables Al igual que los destornilladores, los pelacables también desempeñan un papel importante. Si surge la necesidad repentina de realizar una gran cantidad de cableado, un programador de PLC puede hacerlo de forma independiente simplemente pelando los extremos de los cables y realizando el cableado según sea necesario. Conectividad de red Como un programador de PLC puede requerir acceso a soporte en línea muchas veces, es necesario que la tarjeta SIM tenga suficientes datos y la velocidad debe ser lo suficientemente buena para admitirlo. Por lo general, también es posible que la tarjeta SIM que tenga tenga acceso limitado al sitio. En este caso, solicite la ayuda de ingenieros locales para obtener sus datos o, mejor aún, puede llevar un dispositivo de red para un uso óptimo. Artículos de escritorio Sería bueno que los programadores de PLC llevaran artículos de escritorio como cuadernos, bolígrafos, marcadores, etc. para escribir. Muchas veces, escribir algo durante el trabajo ayuda a los programadores a recordar cosas en situaciones estresantes. Además, como existe una presión constante de los clientes para realizar el trabajo, escribir cosas facilita el trabajo de los programadores. De esta manera vimos las herramientas necesarias que debe llevar un programador de PLC en obra. -
Módulo CRA en el PLC de Schneider: módulo adaptador de E/S remotas
leigehong posted A plc and hmi article in Spanish in PLC programming learning
En la automatización industrial, hay situaciones en las que los instrumentos de E/S se encuentran muy lejos del panel y no se pueden interconectar con el PLC local debido a la distancia involucrada. Por este motivo, hay módulos de E/S remotas disponibles que solo comunican los datos de estos E/S con el PLC principal. Esto facilita la comunicación y brinda flexibilidad a los ingenieros de instrumentos para colocar el instrumento en cualquier lugar que se requiera. Módulo adaptador de E/S remotas La comunicación entre el adaptador remoto y el PLC principal se realiza principalmente a través de Ethernet, que es el modo de comunicación más rápido y eficiente. Dichos módulos de E/S remotas están disponibles en muchas marcas de PLC. De ellas, Schneider Electric es una de ellas y, en ella, está disponible un módulo BMXCRA o BMECRA. En esta publicación, veremos el concepto de módulos CRA en el PLC de Schneider. Módulo CRA en el PLC de Schneider Imagen: BMXCRA31210, módulo Modicon X80 RIO CRA es un módulo adaptador de E/S remoto de la gama de automatización de PLC de Schneider. No tiene ninguna CPU para escribir lógica; es solo un comunicador de datos. Toma valores de E/S y los actualiza a la CPU principal de forma continua. El módulo funciona con el protocolo Ethernet IP. Tiene tres puertos LAN para trabajar. Aparte de los valores de E/S estándar, el módulo también proporciona varios tipos de diagnósticos para la resolución de problemas. Esto ayuda a los programadores a escribir la lógica de forma más flexible. Por ejemplo, tiene tres módulos de E/S a una distancia muy rápida de la CPU. Luego, solo configure estos tres módulos en el módulo CRA en el software; y el CRA los usará para la comunicación de datos con la CPU. Configuración del módulo El módulo tiene dos interruptores giratorios que definen el ID del módulo. Por ejemplo, hay 4 módulos CRA utilizados en el sistema. Los cuatro están ubicados a grandes distancias entre sí. Luego, cada módulo debe tener una identidad separada para que la lógica de la CPU pueda distinguirlo fácilmente. Además, la IP del módulo se establece en el programa de la CPU. No hay configuración en el módulo CRA. Simplemente configure correctamente las direcciones IP en la lógica del PLC para los módulos CRA, establezca la ID con interruptores giratorios y sus módulos CRA comenzarán a funcionar en consecuencia. El módulo tiene cuatro LED para la resolución de problemas: Ejecución, E/S, Estado del módulo y Estado de la red. Lea el catálogo del módulo en detalle para obtener una descripción adecuada. Módulo de comunicación PLC de Schneider El módulo solo es compatible con la gama M580 y Quantum de PLC de Schneider. Una cosa interesante sobre este módulo es que tiene una gran cantidad de servicios de comunicación como agente SNMP, cliente SNTP, cliente FDR, cliente FTP, cliente TFTP, cliente DHCP, mensajes explícitos CIP y calidad de servicio. Todos estos son parte de las características de ciberseguridad y ayudan a proteger el módulo de ciberataques. Los módulos CRA son completamente redundantes. Depende de cómo conecte en red el sistema. El nivel de redundancia depende de cómo se conectan los cables y de cómo se decide la topología. En función de eso, se puede operar la lógica de forma segura sin temor a la pérdida de datos de E/S. Por ejemplo, se tienen dos módulos CRA y se desea redundancia de E/S. En función de la topología que admita, se puede diseñar la red de tal forma que si falla un puerto LAN del primer módulo CRA, se pueden llevar los datos a través del segundo puerto LAN al segundo módulo CRA y luego al PLC principal. Hay varias opciones de enrutamiento disponibles. De esta forma, vimos el concepto del módulo CRA en Schneider PLC. -
ALLEN BRADLEY-ES Módulo AENT en el PLC Rockwell: adaptador de E/S remotas
leigehong posted A plc and hmi article in Spanish in PLC programming learning
En la automatización industrial, hay tres tipos de E/S: local, remota y distribuida. Define si las E/S están en un panel eléctrico local o en un panel de red remoto. Se decide en función de la ubicación de los instrumentos de campo desde el panel. Los diferentes tipos de fabricantes de automatización tienen módulos correspondientes en su marca para trabajar con E/S remotas. Una de esas marcas famosas es Rockwell. En el PLC Rockwell, el adaptador de red más utilizado para la comunicación de E/S es el módulo AENT. Este módulo se puede conectar en una ubicación distinta al PLC local y se conecta a él a través de la comunicación Ethernet. Las E/S correspondientes se interconectan con el módulo AENT. En esta publicación, veremos el concepto del módulo AENT en el PLC Rockwell. Módulo AENT en el PLC Rockwell Como se mencionó anteriormente, un módulo AENT es un tipo de adaptador de E/S remotas. El módulo no tiene ninguna CPU; Es simplemente una interfaz de red que se utiliza para comunicar las E/S de campo con el PLC principal a través del protocolo Ethernet IP. Esto significa que no se puede escribir ninguna lógica en el módulo, ya que solo leerá y escribirá datos de los módulos de E/S configurados con él en la CPU del PLC principal. Puede conectar un máximo de 64 módulos de E/S con un módulo AENT para la interconexión. Generalmente se lo identifica con la serie 1734-AENT. No solo se obtienen datos de E/S, sino que también se obtienen todos y cada uno de los diagnósticos de las E/S a través de este módulo. Esto hace que la resolución de problemas sea mucho más sencilla. La comunicación del módulo se realiza a través del protocolo Ethernet IP y tiene puertos RJ45 para ello. Puede comunicarse en modo semidúplex o dúplex completo. La fuente de alimentación estándar para este módulo es de 24 V CC. Configuración de la dirección IP Existen tres métodos generales a través de los cuales se configura la dirección IP en el módulo: Configurando los interruptores (tiene tres números que indican los últimos tres dígitos de la dirección IP) Usando el software BootP/DHCP disponible en Rockwell Usando el software de configuración IP disponible en Rockwell. Una vez que configure la dirección IP, podrá utilizar el módulo para comunicarse con el PLC principal. En el software del PLC (Studio 5000), los módulos de E/S deben configurarse en este módulo AENT. Estos módulos luego comunican su estado de E/S a la CPU principal a través del módulo AENT. Este módulo se puede utilizar en topología en estrella o en árbol. Diagnóstico de LED El módulo tiene los siguientes LED para diagnóstico: estado del módulo, estado de la red, actividad de la red, estado del bus POINT, energía del sistema y energía del campo. Puede obtener una descripción detallada de cada uno de los LED leyendo su catálogo. Esto ayuda en la resolución detallada de problemas del módulo. Una cosa a tener en cuenta es que la fuente de alimentación conectada al módulo puede controlar solo un máximo de 10 módulos de E/S; por lo tanto, se requiere un módulo de fuente de alimentación después de cada 10 módulos conectados en el AENT. Tamaño del chasis Uno de los términos más importantes relacionados con este módulo es el tamaño del chasis. El tamaño del chasis significa la cantidad de módulos conectados con AENT. Por ejemplo, si se utilizan 19 módulos de E/S, debe configurar el tamaño del chasis en la configuración de AENT en 20. El adaptador almacena esta configuración de tamaño del chasis en un almacenamiento no volátil. Cuando el tamaño del chasis no volátil del adaptador no coincide con la cantidad real de módulos presentes en su placa base, el adaptador no realizará ninguna conexión de E/S. Además, una vez que esté en línea, deberá configurar este tamaño en línea, además de la configuración fuera de línea. Después de este paso, solo podrá usar el módulo para comunicar valores de E/S con la CPU principal. El módulo AENT es un adaptador de gama más alta y, por lo tanto, se usa solo con tres tipos de PLC: Control Logix, Compact Logix y Flex Logix. De esta manera vimos el concepto del módulo AENT utilizado en Rockwell PLC. -
ALLEN BRADLEY-ES Instrucciones One-Shot de flanco ascendente y descendente en PLC Rockwell
leigehong posted A plc and hmi article in Spanish in PLC programming learning
En cualquier PLC, es importante entender cómo se han escrito sus instrucciones. La comprensión básica es la misma en todos los lenguajes; la diferencia es cómo se ilustra. Si tenemos claras las instrucciones, entonces podemos trabajar con cualquier tipo de software de PLC. Una de las marcas más utilizadas en automatización es Rockwell. Hay muchos tipos diferentes de instrucciones en ella para la programación. En eso, hay dos instrucciones que son las más necesarias en cualquier lógica de PLC. Son: flanco ascendente de un disparo y flanco descendente de un disparo. En esta publicación, veremos el funcionamiento de estas dos instrucciones. Flanco ascendente de un disparo (OSR) En la programación de PLC, debe haber escuchado dos tipos comunes de objetos: pico positivo y pico negativo. Un pico positivo significa que se activa solo cuando la variable cambia de 0 a 1. La salida de este objeto viene en un tipo de pulso de activación. Ahora, en lugar del estado de la variable, hay una instrucción adicional en los PLC donde se obtiene la salida de activación de todo el escalón. Esto significa que cuando todo el peldaño o condición cambia su estado de 0 a 1, entonces la salida vendrá en una condición de activación de tipo pulso. Esta es la instrucción de activación ascendente en PLC. En Rockwell PLC, se llama instrucción de flanco ascendente de un solo disparo. Consulte la imagen a continuación para comprender. Como puede ver, la instrucción toma dos entradas en su condición. Ambas están escritas como lógica NO; lo que significa que cuando ambas están activadas, solo la condición es verdadera. Ahora, cuando esto sucede, la instrucción tiene dos variables: bit de almacenamiento y bit de salida. La función del bit de almacenamiento es almacenar el estado de la condición. Cuando ambos bits se activan y la condición cambia de 0 a 1, entonces el bit de almacenamiento se actualiza como 1 y pasa este valor al bit de salida. El bit de salida se activa durante un período de tiempo muy corto, en milisegundos. Luego, el programador del PLC puede usar esta salida de pulso en su lógica. Mientras la condición sea verdadera, el bit de almacenamiento no cambia. Tan pronto como la condición se vuelve falsa, el bit de almacenamiento se actualiza con 0. Cuando la condición se vuelve verdadera nuevamente, entonces el bit de salida se activa como un pulso. Esto demuestra que esta instrucción es muy útil cuando se desea activar una salida con solo un pulso, y este pulso debe generarse solo cuando toda la condición es verdadera, y no cuando una sola variable se vuelve verdadera. Flanco descendente de un disparo (OSF) Ahora, tomemos un ejemplo en el que se requiere tomar una acción cuando el sistema se detiene. Esto significa que cuando la condición se vuelve falsa de verdadera, entonces se debe tomar alguna acción. Y la acción debe realizarse en un tipo de disparador; no debe estar continuamente activa. Esto se llama pico negativo. Para ejecutar esta función, se debe tomar un pico negativo de la variable o el pico negativo se debe tomar de toda la condición como se explicó anteriormente. Para el segundo tipo, se utiliza la instrucción de flanco descendente de un disparo en Rockwell PLC. Consulte la imagen anterior. Hay 2 condiciones NO en el renglón, y la salida de este renglón está conectada al bloque OSF. El bloque tiene dos bits: almacenamiento y salida. El bit de almacenamiento se utiliza para almacenar la condición del renglón. Cuando la condición se vuelve verdadera, el bit de almacenamiento se actualiza a 1. Cuando la condición pasa de ser verdadera a falsa, el bit de almacenamiento se actualiza a 0 y el bit de salida se convierte en 1 en forma de pulso. El ciclo se repite nuevamente cuando la condición se vuelve verdadera una vez más. El bit de salida está en forma de pulso y está activado por un tiempo muy corto, en milisegundos. Esto demuestra que esta instrucción es muy útil cuando se desea activar una salida solo con un pulso, y este pulso debe generarse solo cuando toda la condición es falsa, y no cuando una sola variable se vuelve falsa. De esta manera, vimos las instrucciones de flanco ascendente de un solo impulso y de flanco descendente de un solo impulso en Rockwell PLC. -
¿Qué es la E/S distribuida? – Periféricos descentralizados en PLC
leigehong posted A plc and hmi article in Spanish in PLC programming learning
En este artículo hablaremos sobre los periféricos descentralizados o E/S distribuidas, no vamos a analizar el TIA Portal, solo vamos a discutir qué son las E/S distribuidas y por qué las necesitamos. Contenido: ¿Qué son los periféricos externos o E/S distribuidas? Un ejemplo simple para explicar la necesidad de las E/S distribuidas. o 1 máquina con un PLC en la máquina. o 1 máquina con el PLC está lejos en un lugar seguro. o 2 o más máquinas con el mismo PLC o tener una máquina ya instalada con diferentes módulos de E/S (archivos GSD) conclusión Periféricos externos Los dispositivos de E/S distribuidas son dispositivos utilizados en sistemas de automatización y control. Actúan como intermediarios entre el controlador central (PLC) y los diferentes sensores y actuadores instalados en su proceso de automatización. Imagínelos como mensajeros que recopilan información de los sensores y entregan comandos a los actuadores. E/S distribuida Este enfoque distribuido simplifica el cableado, en lugar de tener todos los cables que van directamente al PLC, se instalan estos dispositivos IO distribuidos en el lado de la máquina. Recopilan información de sensores (como temperatura o movimiento) y envían comandos a actuadores (como motores o válvulas). Esto hace que todo el sistema funcione sin problemas, con menos cableado, y también es más fácil de administrar y expandir, lo que da como resultado una mejora en la flexibilidad del sistema. En la siguiente sección, usaremos algunos ejemplos para explicar la idea y la necesidad de IO distribuida de una manera más sencilla. Un ejemplo simple para explicar la necesidad de IO distribuida Supongamos que tenemos una máquina de producción, esta máquina está controlada a través de un PLC, cualquier tipo de PLC, consulte la imagen 1. Imagen 1. Máquina de producción controlada a través de un PLC. Como puede ver, el PLC que controla la máquina está instalado en el campo en el lado de la máquina. Como sabemos, los PLC están diseñados para funcionar en entornos hostiles, por lo que no es una mala idea instalar el PLC en el lado de la máquina, ya que sabemos que podrá soportar las diferentes condiciones de funcionamiento relacionadas con la máquina, ya sea una temperatura ambiente alta, humedad, vibración, etc. Ahora bien, ¿qué sucede si necesitamos modificar nuestro proceso y aumentar el control que tenemos sobre la máquina, es decir, si necesitamos aumentar la cantidad de entradas y salidas de la máquina? Esto significará que necesitaremos obtener un PLC más grande con una mayor cantidad de E/S, o al menos necesitaremos agregar módulos de E/S al PLC actual. Debe saber que agregar módulos de E/S adicionales al PLC actual dependerá del PLC que haya elegido para su proyecto, porque cada PLC tiene la cantidad máxima de E/S que puede agregar al PLC. Entonces, si la cantidad adicional de E/S que necesitamos excede la cantidad máxima de E/S que puedo agregar al PLC, entonces tendré que conseguir un PLC más grande, y eso significará reescribir su software para el nuevo PLC o al menos migrar su proyecto. Vea la imagen 2. imagen 2. PLC más grande para la nueva extensión de la máquina. Entonces, con la nueva extensión, tuvimos que conseguir un PLC más grande. AHORA, dijimos que el PLC se puede instalar en el campo y está diseñado para soportar entornos hostiles, pero por lo general, eso no es lo que se hace y, por lo general, el PLC se instala lejos en un lugar bien acondicionado y protegido como una sala MCC. Esto significa que cada señal de entrada o salida de nuestro proceso tendrá que estar conectada desde el lado de la máquina al PLC en la sala MCC, por lo que si tengo 100 señales de E/S, tendré que tender 100 cables de señal entre la máquina y el PLC. Y si necesito hacer alguna ampliación en el futuro, tendré que tirar de los cables nuevos adicionales. Ver imagen 3. Imagen 3. Instalación del PLC dentro de la sala MCC. Como puede ver, ahora tenemos que tirar un cable entre el PLC y la máquina para cada señal de E/S que tengamos en nuestro proceso. Esto puede ser aceptable en una máquina pequeña con una pequeña cantidad de E/S, pero no tanto con un proceso grande que tenga muchas E/S. Como esto incluirá tirar de una gran cantidad de cables, esto aumentará el costo de este proceso y también presentará nuevos problemas que deben solucionarse, como canalizaciones de cables, compatibilidad EMC, bandejas de cables y más consideraciones adicionales. Y aquí es donde los periféricos externos o los módulos de E/S distribuidas se vuelven muy útiles. Ver imagen 4. Imagen 4. Uso de un dispositivo de E/S distribuidas. Un módulo de E/S distribuido es simplemente un módulo de E/S que se puede instalar en el lado de la máquina para recopilar todas las entradas del proceso y enviarlas al PLC, y también recibe la señal de salida del PLC y la envía a los dispositivos de accionamiento relacionados. Como puede ver en la imagen, la conexión entre el PLC y la máquina ahora se realiza tirando de un cable de comunicación entre el dispositivo de E/S distribuido y el PLC. Los dispositivos de E/S distribuidos tienen muchas capacidades de comunicación; en nuestro ejemplo, asumimos una comunicación Profinet, de ahí el color verde. El uso de un dispositivo de E/S distribuidas le dará la ventaja de ampliar sus E/S de proceso sin necesidad de instalar un PLC más grande. Simplemente agregará las E/S nuevas a su dispositivo y la comunicación entre el PLC seguirá siendo la misma utilizando Profinet o cualquier otro método de comunicación. Incluso puede tener una máquina completamente nueva controlada con el mismo PLC, solo tendrá que tirar de un nuevo cable de comunicación desde el PLC a la nueva máquina. Vea la imagen 5. imagen 5. Control de 2 máquinas con el mismo PLC. Como puede ver, para controlar una máquina completamente nueva con mi PLC, solo necesitaría un cable de comunicación adicional desde el PLC y la máquina. Por supuesto, debe asegurarse de que las capacidades de su PLC puedan manejar el procesamiento y el control de las dos máquinas. Una cosa más, las E/S distribuidas se pueden usar con diferentes marcas de PLC, lo que significa que puedo usar diferentes marcas de E/S distribuidas con el PLC Siemens. Consulte la imagen 6. 98-1.gif imagen 6. Uso de diferentes marcas de E/S distribuidas. Como puede ver en la imagen, una máquina utiliza un dispositivo de E/S distribuidas SIEMENS y la otra máquina utiliza un dispositivo de E/S distribuidas Schneider y ambos se controlarán a través del mismo PLC. Conclusión Los dispositivos de E/S distribuidas se utilizan para ampliar el alcance de un sistema de control, lo que permite la conexión de una gran cantidad de sensores y actuadores a largas distancias. Las E/S distribuidas reducen la cantidad de cableado necesario en comparación con una conexión de señal de máquina-PLC tradicional. Es fácil agregar o quitar dispositivos en un sistema de E/S distribuidas, lo que lo hace altamente escalable y confiable. -
Ejemplos de programación de temporizadores de PLC: TON, TOF, TP y TONR
leigehong posted A plc and hmi article in Spanish in PLC programming learning
Analice acerca de los ejemplos de programación de temporizadores de PLC: los diferentes temporizadores de PLC son TON, TOF, TP y TONR. Instrucciones de temporizador de PLC y ejemplos de lógica de temporizador de PLC. Programación de temporizadores de PLC Implementación de temporizadores IEC (TON, TOF, TP y TONR) en el PLC S7-1200 mediante TIA Portal. En muchas aplicaciones, existe un requisito para controlar el tiempo o el flujo de señales. Por ejemplo, es posible que sea necesario controlar una válvula o un motor para que funcionen durante un intervalo de tiempo determinado, se enciendan después de un intervalo de tiempo o después de un retraso. Diagrama del problema Solución del problema Para este problema, utilizaremos temporizadores IEC (TON, TOF, TP y TONR) en el PLC S7-1200 con ejemplos. Existen diferentes formas de temporizadores que se pueden encontrar en los PLC. Como se muestra en el diagrama anterior, Temporizador de retardo de encendido que se activa después de un retraso de tiempo determinado. Los temporizadores de retardo de apagado se activan durante un período de tiempo fijo después de apagar la entrada. El temporizador de pulsos se activa o desactiva durante un período de tiempo fijo. El temporizador acumulador es el que registra intervalos de tiempo. Aquí, considere el ejemplo de cuatro motores y cuatro INTERRUPTORES para obtener una explicación de los temporizadores. Necesitamos poner en marcha tres motores de diferentes maneras. El primer motor arrancará después de un retraso de 10 segundos, el segundo motor arrancará inmediatamente y se apagará después de un retraso de 10 segundos y el tercer motor arrancará con un pulso y se apagará con un retraso de 10 segundos. El cuarto motor funcionará durante un total de 10 segundos. Lista de entradas/salidas Lista de entradas SWITCH 1: I0.0 SWITCH 2: I0.1 SWITCH 3: I0.2 SWITCH 4: I0.3 Reset: I0.4 Lista de salidas MOTOR 1: Q0.0 MOTOR 2: Q0.1 MOTOR 3: Q0.2 MOTOR 4: Q0.3 Diagrama de escalera de PLC para temporizadores Podemos utilizar la instrucción de temporizador Generate-ON-delay o ON delay para retrasar la configuración de la salida Q por la duración programada PT. La instrucción se inicia cuando el resultado de la entrada IN cambia de 0 a 1 (flanco positivo). Puede monitorear el valor de tiempo actual en la salida ET del bloque Timer. El valor del temporizador comienza en T#0s y termina cuando se alcanza el valor de duración PT. La salida ET se restablece tan pronto como el estado de la señal en la entrada IN cambia a 0. Podemos utilizar la instrucción Generate off-delay o Off-delay Timer para retrasar el restablecimiento de la salida Q por la duración programada PT. La salida Q se establece cuando el resultado de la operación lógica (RLO) en la entrada IN cambia de 0 a 1 (flanco positivo de la señal). Podemos monitorear el valor de tiempo actual en la salida ET. Podemos utilizar la instrucción Generate pulse para establecer la salida Q por una duración programada. La instrucción se inicia cuando el resultado de la entrada IN cambia de 0 a 1 (flanco positivo). El tiempo programado (PT) comienza cuando se inicia la instrucción. En este temporizador, incluso si se detecta un nuevo flanco positivo, el estado de la señal en la salida Q no se ve afectado mientras se esté ejecutando la duración del tiempo PT. La instrucción del acumulador de tiempo o temporizador del acumulador se utiliza para acumular valores de tiempo dentro de un período establecido por el parámetro de tiempo programado (PT). Cuando el estado de la señal en la entrada IN cambia de 0 a 1 (flanco positivo), se ejecuta la instrucción y comienza la duración PT. En este caso, el parámetro Q permanece establecido en 1, incluso cuando el estado de la señal en el parámetro IN cambia de 1 a 0″ (flanco negativo). La entrada R restablece la salida Q. Descripción del programa En este problema, consideraremos el PLC S7-1200 y el software del portal TIA para la programación. Red 1: En esta red, hemos utilizado un temporizador de retardo de encendido (generar retardo de encendido) para el MOTOR 1 (Q0.0). Cuando el estado del INTERRUPTOR 1(I0.0) cambia de 0 a 1, se ejecutará la instrucción del temporizador y activará el MOTOR 1(Q0.0) después de un retraso de 10 s. Red 2: En esta red, hemos utilizado un temporizador de retardo de apagado (generar retraso de apagado) para el MOTOR 2(Q0.1). Cuando el estado del INTERRUPTOR 2(I0.1) cambia de 0 a 1, se ejecutará la instrucción del temporizador y activará el MOTOR 2(Q0.1) inmediatamente. Además, cuando el estado del INTERRUPTOR 2(I0.1) cambia de nuevo a 0, comenzará el tiempo programado (PT) y, después de ese tiempo, el MOTOR 2(Q0.1) se apagará. Red 3: En esta red, hemos utilizado un temporizador de pulsos (generar pulsos) para el MOTOR 3(Q0.2). Cuando el estado del INTERRUPTOR 3(I0.2) cambia de 0 a 1, se ejecutará la instrucción del temporizador y activará el MOTOR 3(Q0.2) inmediatamente. En este caso, incluso si se detecta un nuevo flanco positivo, el estado del MOTOR 3(Q0.2) no se ve afectado mientras se esté ejecutando el tiempo programado (PT). Red 4: En esta red, hemos utilizado un temporizador acumulador (tiempo acumulador) para el MOTOR 4(Q0.3). Cuando el estado del INTERRUPTOR 4(I0.3) cambia de 0 a 1, se ejecutará la instrucción del temporizador y el MOTOR 4(Q0.3) se pondrá en marcha después de 10 s. El MOTOR 4(Q0.2) permanecerá encendido, incluso cuando el estado de entrada vuelva a cambiar a 0. El reinicio (I0.4) es necesario para reiniciar el temporizador o el tiempo acumulado. Casos de prueba en tiempo de ejecución -
Programa PLC para hacer parpadear una lámpara en intervalos de 5 segundos
leigehong posted A plc and hmi article in Spanish in PLC programming learning
Este es un programa PLC para hacer parpadear (encender/apagar) una lámpara en intervalos de 5 segundos. Lámpara parpadeante Descripción del problema Haga que el indicador o la lámpara se enciendan después de cinco segundos y se apaguen después de cinco segundos. Cree un programa que encienda la lámpara durante 5 segundos, luego apáguela durante 5 segundos, luego enciéndala durante 5 segundos y vuelva a apagarla durante 5 segundos, y así sucesivamente. Diagrama del problema Solución del problema Este problema se puede resolver utilizando temporizadores. En este caso, utilizaremos TON (temporizador de retardo de encendido). Para la explicación, consideramos un INTERRUPTOR para habilitar el ciclo de ENCENDIDO/APAGADO y una lámpara para la salida. Cuando el usuario presiona el INTERRUPTOR, la lámpara se activará y permanecerá ENCENDIDA durante 5 segundos; luego se APAGARÁ durante 5 segundos. Este ciclo se repetirá. Lista de entradas y salidas Lista de entradas INTERRUPTOR: I0.0 Lista de salidas Lámpara: Q0.0 Memoria M M0.0: memoria de bits para la condición de lámpara apagada. Diagrama de escalera del PLC para lámpara parpadeante Explicación del programa En este problema, consideraremos el PLC S7-1200 y el software del portal TIA para la programación. Red 1: En esta red, cuando se presiona el INTERRUPTOR (I0.0), cuando la condición de lámpara apagada no está presente, entonces la lámpara (Q0.0) estará encendida. Entonces, aquí usamos el contacto NO del INTERRUPTOR (I0.0) y el contacto NC de la condición de lámpara apagada (M0.0). Red 2: En esta red, cuando la lámpara (Q0.0) está encendida, se ejecutará la instrucción TON (temporizador de retardo de encendido) y se establecerá la condición de lámpara apagada. Por lo tanto, aquí hemos tomado el contacto NO de la lámpara (Q0.0), el temporizador TON y el tiempo programado es de 5 segundos. Red 3: Según nuestra condición, la condición de lámpara apagada (M0.0) debe apagarse después de un retraso de 5 segundos, por lo que hemos utilizado TON nuevamente. Por lo tanto, utilizamos el contacto NO de la condición de lámpara apagada (M0.0) y TON con un tiempo programado de 5 segundos. Resultado -
Programa de PLC para circuito de salida alternativa con función de enclavamiento
leigehong posted A plc and hmi article in Spanish in PLC programming learning
Diseñe un programa de PLC para un circuito de salida alternativa con una función de enclavamiento y explique la lógica de escalera con una solución. Circuito de salida alternativa Descripción del problema Encienda la luz presionando un INTERRUPTOR la primera, tercera, quinta vez, etc. y apague la misma luz presionando el INTERRUPTOR la segunda, cuarta, sexta vez, etc. Restaure el estado de salida a "0" cuando se enciende el sistema o se enciende el ciclo. La salida se puede INICIAR presionando un BOTÓN una cantidad IMPAR de veces y se puede DETENER presionando el mismo BOTÓN una cantidad PAR de veces. Diagrama del problema Solución del problema Podemos resolver este problema usando lógica de escalera simple. En este caso, consideramos un ejemplo simple de funcionamiento de LED alternativo. Aquí, consideramos un LED y un BOTÓN. Presione el BOTÓN alternativamente y la salida debe estar ENCENDIDA/APAGADA alternativamente; aquí, si presiona el botón un número impar de veces, la salida debe estar ENCENDIDA y si presiona el botón un número par de veces, la salida debe estar APAGADA. Lista de entradas y salidas del PLC Lista de entradas INTERRUPTOR: I0.0 Lista de salidas LED: Q0.0 Memoria M M0.0 para condición de reinicio del LED M0.1 para reinicio del contador M11.0 y M11.1: flanco positivo Diagrama de escalera para circuito de salida alternativo (con función de enclavamiento) Descripción del programa del PLC En esta aplicación, hemos utilizado el PLC Siemens S7-300 y el software TIA Portal para la programación. Red 1: En la red 1 hemos utilizado la instrucción SET para configurar el LED (Q0.0). Aquí hemos tomado el contacto NO del BOTÓN (I0.0) de modo que el LED (Q0.0) se pueda activar al presionar el BOTÓN (I0.0). Red 2: Aquí hemos utilizado un contador para que cuente los tiempos de conmutación del BOTÓN (I0.0). Este contador nos indicará la cantidad de veces que se presiona el botón, su valor o si el valor es un número PAR o IMPAR. Red 3: Cuando el contador alcance su valor preestablecido (2) o, digamos, un número PAR de veces, el contacto NO del contador configurará M0.0 (condición de reinicio del LED). Red 4: En esta red, el contacto NO del M0.0 REINICIARÁ el LED y el contador. Aquí, M0.1 (memoria de reinicio del contador) REINICIARÁ el contador. Red 5: Si M0.0 está ENCENDIDO y se activa la transición negativa (de 1 a 0) del botón (I0.0), la condición de REINICIO del LED estará APAGADA. Nota: Este ejemplo se proporciona para comprender el concepto básico del circuito de salida alternativo; no es una aplicación completa, pero podemos usar este concepto en cualquier aplicación de automatización o cualquier sistema. Casos de prueba -
Programa PLC para Tanque Mezclador
leigehong posted A plc and hmi article in Spanish in PLC programming learning
Cree un diagrama de escalera para controlar un proceso de mezclado por lotes. Implemente un programa PLC para el tanque mezclador o el proceso de mezclado utilizando lógica de escalera PLC. Programa PLC para Tanque Mezclador Fig : Tanque mezclador Un tanque se utiliza para mezclar dos líquidos. El circuito de control requerido funciona de la siguiente manera: A. Cuando se presiona el botón START, los solenoides A y B se energizan. Esto permite que los dos líquidos comiencen a llenar el tanque. B. Cuando el tanque está lleno, el interruptor de flotador se dispara. Esto desenergiza los solenoides A y B y arranca el motor utilizado para mezclar los líquidos. C. Se permite que el motor funcione durante 1 minuto. Después de que transcurra 1 minuto, el motor se apaga y el solenoide C se energiza para drenar el tanque. D. Cuando el tanque está vacío, el interruptor de flotador desactiva el solenoide C. E. Se puede utilizar un botón de PARADA para detener el proceso en cualquier momento. F. Si el motor se sobrecarga, se detendrá la acción de todo el circuito. G. Una vez que se ha activado el circuito, continuará funcionando hasta que se detenga manualmente. Solución lógica de PLC En la siguiente figura se muestra un esquema de relé que realizará la lógica de este circuito. La lógica de este circuito es la siguiente: Fig.: Esquema de relé A. Cuando se presiona el botón de INICIO, se activa la bobina de relé CR. Esto hace que todos los contactos CR se cierren. El contacto CR-1 es un contacto de retención que se utiliza para mantener el circuito a la bobina CR cuando se suelta el botón de INICIO. B. Cuando se cierra el contacto CR-2, se completa un circuito a las bobinas de solenoide A y B. Esto permite que los dos líquidos que se van a mezclar comiencen a llenar el tanque. C. A medida que el tanque se llena, el flotador se eleva hasta que se activa el interruptor de flotador. Esto hace que el contacto del interruptor de flotador normalmente cerrado se abra y el contacto normalmente abierto se cierre. D. Cuando el interruptor de flotador normalmente cerrado se abre, las bobinas de solenoide A y B se desenergizan y detienen el flujo de los dos líquidos hacia el tanque. E. Cuando el contacto normalmente abierto se cierra, se completa un circuito hacia la bobina de un arrancador de motor y la bobina de un temporizador de retardo de encendido. El motor se utiliza para mezclar los dos líquidos. F. Al final del período de tiempo de un minuto, todos los contactos TR cambian de posición. El contacto TR-2 normalmente cerrado conectado en serie con la bobina del arrancador del motor se abre y detiene el funcionamiento del motor. El contacto TR-3 normalmente abierto se cierra y energiza la bobina de solenoide C, lo que permite que el líquido comience a drenar del tanque. El contacto TR-1 normalmente cerrado se utiliza para asegurar que las válvulas A y B no puedan volver a activarse hasta que el solenoide C se desactive. G. A medida que el líquido se drena del tanque, el flotador baja. Cuando el flotador baja lo suficiente, el interruptor de flotador se dispara y sus contactos vuelven a sus posiciones normales. Cuando el contacto del interruptor de flotador normalmente abierto se vuelve a abrir y desactiva la bobina TR, todos los contactos TR vuelven a sus posiciones normales. H. Cuando el contacto TR-3 normalmente abierto se vuelve a abrir, el solenoide C se desactiva y cierra la válvula de drenaje. El contacto TR-2 se vuelve a cerrar, pero el motor no puede reiniciarse debido al contacto del interruptor de flotador normalmente abierto. Cuando el contacto TR-1 se vuelve a cerrar, se completa un circuito con los solenoides A y B. Esto permite que el tanque comience a llenarse y el proceso comienza nuevamente. I. Si el botón de PARADA o el contacto de sobrecarga se abren, la bobina CR se desactiva y todos los contactos CR se abren. Esto desenergiza todo el circuito. Nota: El programa del PLC también será muy similar al esquema del relé anterior. Tarea para ti Analiza la siguiente animación y comparte el funcionamiento del circuito a través de comentarios. -
Control de circuito neumático PLC
leigehong posted A plc and hmi article in Spanish in PLC programming learning
Aquí analizamos el control de circuito neumático PLC con diferentes ejemplos. Diagrama de escalera PLC para cilindros neumáticos de simple y doble efecto. Ejemplos de circuitos neumáticos PLC Ejemplo 1: Se utiliza un cilindro de doble efecto para realizar una operación de mecanizado. El cilindro neumático avanza presionando dos botones pulsadores simultáneamente. Si se suelta cualquiera de los botones pulsadores, el cilindro vuelve a la posición inicial. Dibuje el circuito neumático, el diagrama de cableado del PLC y el diagrama de escalera para implementar esta tarea. Solución: Como se muestra en el diagrama de cableado del PLC, los botones pulsadores PB1 y PB2 están conectados en la dirección de memoria I1 e I2. I1 e I2 están conectados en serie en el diagrama de escalera para realizar esta función lógica AND. Cuando se presionan simultáneamente los pulsadores PB1 y PB2, las direcciones I1 e I2 pasan del estado 0 al estado 1, como resultado, la energía fluye a través de la bobina y habrá una salida en la bobina 01. La salida en la bobina 01 hace funcionar la bobina del solenoide y el cilindro avanza para realizar la operación requerida. Si se presiona cualquiera de PB1 y PB2, las direcciones de bit correspondientes pasan a 0, ya que I1 e I2 están en serie, si cualquiera de ellos pasa al estado 0, no habrá ninguna salida en 01 y, por lo tanto, el solenoide se desenergiza y regresa. Ejemplo 2: Se utiliza un cilindro de doble efecto para realizar el movimiento de avance y retroceso. El cilindro neumático avanza presionando los pulsadores PB1. El cilindro regresa presionando el pulsador PB2. Dibuje el circuito neumático, el diagrama de cableado del PLC y el diagrama de escalera para implementar esta tarea. Solución El diagrama de cableado del PLC y los diagramas de escalera se muestran en la Figura anterior. Cuando se presiona el pulsador PB1, el estado de la dirección I1 cambia a 1 y, por lo tanto, habrá salida 01. La salida de 01 opera el solenoide Y1 y el cilindro avanza. Cuando el cilindro alcanza la posición extrema hacia adelante y se presiona el pulsador PB2, el estado de la dirección I2 cambia a 1 y, por lo tanto, habrá salida 02. La salida de 02 opera el solenoide Y2 y el cilindro regresa a la posición inicial. Ejemplo 3: El cilindro de doble efecto se utiliza para avanzar y regresar automáticamente después de alcanzar la posición extrema hacia adelante. El cilindro neumático avanza presionando los pulsadores PB1. Dibuje el circuito neumático, el diagrama de cableado del PLC y el diagrama de escalera para implementar esta tarea. Solución El diagrama de cableado del PLC y los diagramas de escalera se muestran en la Figura anterior. Cuando se presiona el pulsador PB1, el estado de la dirección I1 cambia a 1 y, por lo tanto, habrá salida 01. La salida de 01 opera el solenoide Y1 y el cilindro avanza. Cuando el cilindro alcanza la posición extrema hacia adelante y se opera el interruptor de límite S2, el estado de la dirección I3 cambia a 1 y, por lo tanto, habrá una salida 02. La salida de 02 opera el solenoide Y2 y el cilindro regresa a la posición inicial. Ejemplo 4: Se utiliza un cilindro de doble efecto para realizar la operación de prensado. El cilindro debe moverse hacia adelante cuando se presiona el botón PB1 y regresar durante un tiempo establecido de 20 segundos antes de que regrese automáticamente a la posición inicial. El interruptor de límite S2 se utiliza para detectar el final del movimiento hacia adelante del cilindro. Dibuje el circuito neumático, el diagrama de cableado del PLC y el diagrama de escalera para implementar esta tarea. Solución Cuando se presiona PB1, el estado de entrada de la dirección I1 cambia a 1 y hay una salida en O1. Debido a la salida en O1, se opera la bobina del solenoide Y1 y el cilindro se mueve hacia adelante. Cuando el cilindro alcanza la posición final, se opera el interruptor de límite S2 y, como resultado, la dirección I3 cambia a 1 y, en consecuencia, inicia el temporizador T1. El estado de la señal del temporizador T1 cambia a 1 después de que se alcanzan los 20 segundos. Al final de los 20 segundos, habrá una salida de la salida O2 establecida del temporizador T1. La bobina Y2 se activa, lo que provoca el movimiento de retorno del cilindro. Ejemplo 5: El cilindro de doble efecto se utiliza para realizar un movimiento continuo de vaivén. El cilindro tiene que moverse hacia adelante cuando se presiona el botón PB1 y una vez que comienza el movimiento alternativo de vaivén, debe continuar hasta que se presione el botón de parada PB2. Los interruptores de límite se utilizan para detectar la posición final. Dibuje el circuito neumático, el diagrama de cableado del PLC y el diagrama de escalera para implementar esta tarea. Solución: Las operaciones de inicio y parada se pueden implementar utilizando un indicador de memoria con dirección M1 que se establece mediante PB1 y se restablece mediante PB2. El estado del elemento de memoria M1 se escanea a través de un contacto NA y se combina en serie con el estado del sensor S1 para obtener controles de inicio y parada. Ejemplo 6: Se utiliza un cilindro de doble efecto para realizar operaciones de vaivén. El cilindro debe avanzar cuando se presiona el botón PB1 y continuar con el movimiento de vaivén hasta que se realicen 10 ciclos de operaciones. Dibuje el circuito neumático, el diagrama de cableado del PLC y el diagrama de escalera para implementar esta tarea. Solución El funcionamiento completamente automático del cilindro se puede obtener como antes utilizando los interruptores de límite S1 y S2. La operación de inicio y parada se puede implementar utilizando el indicador de memoria con dirección M1 que se establece mediante PB1 en I1 y se reinicia mediante el contacto NC de un contador descendente. El estado del indicador de memoria M1 escaneado a través de un contacto NA (rung 2) se combina en serie con el sensor de estado S1 para obtener controles de inicio y parada. Ejemplo 7: Dibuje el circuito neumático, el diagrama de cableado del PLC y el diagrama de escalera para implementar la secuencia A+B+B-A-. Solución En este circuito de secuencia, se utiliza PB2 para iniciar el programa. Al presionar PB2, se establece el último estado de memoria M4 y se reinician todos los demás indicadores de memoria M1, M2 y M3. Inicialmente, se activan S1 y S3 y generan salidas. Condición 1: Al presionar PB1, se establece el indicador de memoria M1 y se reinicia el indicador de memoria M4. Se activa el solenoide Y1. El cilindro A se extiende (A+). El sensor S1 se desactiva cuando A se desplaza y S2 se activa cuando se alcanza la posición final. Condición 2: Cuando se activa S2, se establece la memoria M2 y se reinicia el indicador de memoria M1. Se activa el solenoide Y3. El cilindro B se extiende (B+). El sensor S3 se desactiva cuando B se desplaza y S4 se activa cuando se alcanza la posición final. Condición 3: Cuando se activa S4, se establece la memoria M3 y se reinicia el indicador de memoria M2. Se activa el solenoide Y4. El cilindro B se retrae (B-). El sensor S4 se desactiva cuando B se desplaza y S3 se activa cuando se alcanza la posición inicial. Condición 4: Cuando se activa S3, se establece la memoria M4 y se reinicia el indicador de memoria M3. Se activa el solenoide Y2. El cilindro A se retrae (A-). El sensor S2 se desactiva cuando B se desplaza y S1 se activa cuando se alcanza la posición inicial. -
Ejemplo de lógica de escalera de PLC
leigehong posted A plc and hmi article in Spanish in PLC programming learning
Aquí, emularemos exactamente el mismo circuito de alarma de alta presión utilizando un PLC MicroLogix 1000 de Allen-Bradley en lugar de una bobina de relé: Ejemplo de lógica de PLC Programa de lógica de escalera Supongamos que se aplica una presión de fluido de 36 PSI al interruptor de presión. Esto es menor que el ajuste de disparo del interruptor de 50 PSI, lo que deja al interruptor en su estado "normal" (cerrado). Esto envía energía a la entrada I:0/2 del PLC. El contacto etiquetado I:0/2 dibujado en el programa de lógica de escalera del PLC actúa como un contacto de relé impulsado por una bobina energizada por el terminal de entrada I:0/2. De esta manera, el contacto cerrado del interruptor de presión activa el terminal de entrada I:0/2, que a su vez “cierra” el símbolo de contacto normalmente abierto I:0/2 dibujado en el programa de lógica de escalera. Este contacto “virtual” envía energía virtual a una bobina virtual etiquetada B3:0/0, que no es más que un solo bit de datos en la memoria del microprocesador del PLC. “Activar” esta bobina virtual tiene el efecto de “activar” cualquier contacto dibujado en el programa que tenga la misma etiqueta. Esto significa que el contacto normalmente cerrado B3:0/0 ahora estará “activado” y, por lo tanto, en estado abierto, sin enviar energía virtual a la bobina de salida O:0/1. Con la bobina virtual O:0/1 “sin alimentación”, la salida real O:0/1 en el PLC estará eléctricamente abierta y la lámpara de alarma no tendrá alimentación (no estará encendida). Si suponemos que se aplica una presión de fluido de 61 PSI al presostato, el contacto del presostato normalmente cerrado se activará (forzará) a abrirse. Esto tendrá el efecto de desenergizar la entrada I:0/2 del PLC, “abriendo” así el contacto virtual normalmente abierto en el programa del PLC que lleva la misma etiqueta. Este contacto virtual “abierto” interrumpe la alimentación virtual a la bobina virtual B3:0/0, lo que hace que el contacto virtual normalmente cerrado B3:0/0 se “cierre” y envíe alimentación virtual a la bobina virtual O:0/1. Cuando esta bobina de salida virtual se “energiza”, el canal de salida real del PLC se activa y envía alimentación real a la luz de alarma para encenderla, lo que indica una condición de alarma de alta presión. Podemos simplificar aún más este programa de PLC eliminando el relé de control virtual B3:0/0 y simplemente haciendo que la entrada I:0/2 active la salida O:0/1 a través de un contacto virtual “normalmente cerrado”: El efecto es el mismo: la salida O:0/1 del PLC se activará siempre que la entrada I:0/2 se desactive (siempre que el presostato se abra por una presión alta), encendiendo la lámpara de alarma en una condición de alta presión. En una condición de baja presión, la entrada energizada I:0/2 fuerza al contacto virtual normalmente cerrado I:0/2 a abrirse, desenergizando así la salida O:0/1 del PLC y apagando la lámpara de alarma. Los controladores lógicos programables no solo han simplificado enormemente el cableado de los controles lógicos industriales al reemplazar multitud de relés electromecánicos con un microprocesador, sino que también han agregado capacidades avanzadas como contadores, temporizadores, secuenciadores, funciones matemáticas, comunicaciones y, por supuesto, la capacidad de modificar fácilmente la lógica de control a través de la programación en lugar de recablear los relés. La belleza de la programación lógica en escalera es que traduce la comprensión del técnico de los circuitos de control de relés tradicionales a una forma virtual donde los contactos y las bobinas interactúan para realizar funciones de control prácticas. Sin embargo, un concepto clave que se debe dominar es la asociación de condiciones de la vida real con el estado del interruptor en función de la representación "normal" de esos contactos de interruptor, ya sean reales (relé) o virtuales (PLC). Una vez que se domina este concepto vital, es posible comprender tanto los circuitos de control de relés cableados como los programas de PLC. Sin dominar este concepto vital, no se pueden entender ni los circuitos de control de relés ni los programas de PLC. -
Convenciones de nombres de etiquetas de PLC
leigehong posted A plc and hmi article in Spanish in PLC programming learning
Cuando diseña una lógica de PLC, debe tener cuidado con los nombres que proporciona a las etiquetas. Debe ser fácil de entender e interpretar para cualquier programador. No debe ser ni demasiado largo ni demasiado corto. La convención de nombres es importante porque el etiquetado incorrecto puede causar problemas de resolución de problemas para los programadores. Además, dar nombres largos consumirá la memoria del PLC. Por lo tanto, cada programador debe seguir las convenciones de nombres adecuadas antes de escribir un programa de PLC. En esta publicación, veremos el concepto de convenciones de nombres de etiquetas de PLC. Convenciones de nombres de etiquetas de PLC En primer lugar, comprendamos cómo la convención de nombres de etiquetas juega un papel importante en la programación de PLC. Tiene un motor con su comando de ejecución y retroalimentación de ejecución como E/S de PLC. El motor está ubicado en la sala de sopladores y se usa como compresor de aire. El nombre de la etiqueta del motor en el P&ID es M-101. Ahora bien, para un programador de PLC, identificar la ubicación de una etiqueta es importante. Por lo tanto, existen dos tipos de mentalidades que normalmente definen a un programador de PLC. El primero intentará dar la mayor cantidad de información posible en un nombre de etiqueta; por lo tanto, puede nombrar el comando de funcionamiento del motor como M101_Compressor_Run_Command. El segundo intentará darle el nombre como Q_M101_Comp. La segunda mentalidad parece muy clara, ya que está dando nombres cortos y manteniendo la longitud lo más mínima posible. Esta es la razón por la que nombrar una etiqueta de PLC es importante, ya que libera al programador de leer etiquetas tan largas en situaciones en las que se ha presentado una solución de problemas urgente. (Cabe señalar que la denominación de etiquetas de PLC no acepta ningún carácter especial aparte del guión bajo (_)). Un nombre de etiqueta de PLC debe contener información que pueda ayudar al programador a relacionarse con su significado. Esto generalmente implica la siguiente información: tipo de datos (p. ej., booleano, entero), flujo de datos (p. ej., entrada, salida), alcance (p. ej., local, global), tipo de instrumento o dispositivo (p. ej., motor, válvula, sensor), parámetro de proceso (p. ej., presión, flujo, temperatura) y ubicación del dispositivo. Estilos de nombres de etiquetas Existen varios estilos según los estándares IEC que se deben seguir para una denominación adecuada. Veamos algunos de los más utilizados: Estilo Camel, Estilo Pascal, Estilo Snake, Estilo de prefijo con tipo de datos Estilo Camel En este estilo, no hay guiones bajos entre ellos. Se le da un nombre completo a la palabra entera, pero cada palabra comienza con una letra mayúscula. Por ejemplo, tomemos el ejemplo mencionado anteriormente. M101_Compressor_Run_Command se escribirá como m101CompressorRunCommand. Puede identificar cada palabra con una letra mayúscula. La primera letra será una letra minúscula obligatoria. Este estilo se ve bien si la palabra es pequeña. Evita el uso de guiones bajos y esto hace que el consumo de memoria sea menor. Estilo Pascal Es similar al estilo camel; la única diferencia es que la primera letra será una letra mayúscula obligatoria. Por ejemplo, nuestra etiqueta se escribirá como M101CompressorRunCommand. Estilo Snake El ejemplo que discutimos antes es el estilo Snake. Aquí, cada palabra estará separada por un guión bajo. Estilo de prefijo con tipo de datos Aquí, la etiqueta tendrá como prefijo el tipo de datos del nombre de la etiqueta. En nuestro caso, el tipo de etiqueta era booleano. Según los estándares IEC, una etiqueta booleana generalmente tiene un prefijo de 'x'. Entonces, nuestro estilo se escribirá como xM101CompressorRunCommand. Esto ayuda al programador a identificar qué tipo de datos se utilizan para esa etiqueta en particular. Consejos para nombrar etiquetas en la programación de PLC La primera y más importante regla es que la longitud de una etiqueta debe ser corta, pero no tan corta que nadie pueda entenderla. Como se mencionó, la longitud debe contener la información adecuada en una longitud adecuada. Se deben evitar estrictamente los nombres largos. Siga los estilos generales de nombres de etiquetas que se analizaron. Estos se ajustan a las normas IEC y hacen que la lógica se vea ordenada y clara. Para reducir los errores durante la creación de etiquetas, utilice archivos de Excel. Excel reduce la carga de trabajo de una manera muy amplia, ya que la duplicación y la copia se vuelven muy fáciles. Casi no se producen errores en los archivos de Excel. No siempre es necesario utilizar un nombre completo para una palabra. Por ejemplo, la válvula se puede escribir como vlv y la temperatura se puede escribir como temp. Evite escribir la etiqueta en mayúsculas. Parece complicado e inadecuado de leer. -
¿Cómo convertir un diagrama eléctrico en un programa de PLC?
leigehong posted A plc and hmi article in Spanish in PLC programming learning
La programación de PLC tomó como referencia los dibujos eléctricos. A medida que pasó el tiempo y se hizo difícil solucionar problemas en los sistemas eléctricos que involucraban automatización, se requirió que algún controlador ejecutara una lógica y hiciera lo necesario. Esto dio origen a los sistemas PLC. Como sabes, la programación de PLC tiene muchos tipos de lenguajes y el original es el lenguaje de escalera. Debes saber que los diagramas eléctricos también ayudan a convertirlo en lógica de escalera. En esta publicación, veremos cómo convertir un diagrama eléctrico en un programa de PLC. Entender el diagrama eléctrico En primer lugar, debes entender el diagrama eléctrico. Consulta la siguiente imagen. Cada circuito tiene dos extremos: positivo y negativo. La corriente comienza desde el extremo positivo y fluye a través del extremo negativo. En el medio, vienen los componentes y dispositivos eléctricos. Si consulta la siguiente imagen, hay cuatro componentes: el botón de inicio, el botón de parada, el contacto auxiliar de la lámpara y la lámpara. La fuente de alimentación comienza desde el extremo positivo y va a la entrada del pulsador de arranque (contacto NA). La salida del pulsador de arranque va a la entrada del pulsador de parada (contacto NC). La salida del pulsador de parada va a la entrada de la lámpara. La salida de la lámpara está conectada a la fuente de alimentación del extremo negativo. En paralelo al pulsador de arranque, otro cable baja desde la entrada del botón hasta un contacto auxiliar de la lámpara. La salida de este contacto se conecta de nuevo a la salida del pulsador. Cuando se suministra la fuente de alimentación y se presiona el botón de arranque, la lámpara se encenderá ya que obtiene el camino para la corriente. Ahora, si se suelta el botón, la lámpara se apagará ya que no obtiene el camino. Entonces, para bloquearlo, colocamos el contacto de la lámpara en paralelo que mantendrá la ruta de la fuente de alimentación. Cuando se presiona el botón de parada, la ruta de suministro eléctrico se corta y la lámpara se apaga. Convertir el diagrama de cableado al programa de PLC Ahora, una vez que haya entendido el diagrama de cableado, comience a interpretarlo de la misma manera para la programación de PLC. Consulte la imagen a continuación. La lógica de escalera tendrá dos extremos de alimentación: izquierdo y derecho. El izquierdo es el equivalente a un extremo de alimentación positivo y el derecho es el equivalente a un extremo de alimentación negativo. Necesitará cuatro componentes de programación de PLC: botón pulsador de inicio -> contacto NA, botón pulsador de parada -> contacto NC, lámpara -> bobina de salida y contacto NA de lámpara. Primero, coloque el contacto NA del botón pulsador de inicio. En paralelo a él, coloque la lámpara en contacto NA. Después de esto, coloque el contacto NC del botón pulsador de parada. Por último, coloque la lámpara en contacto NA. El funcionamiento será el mismo que se explicó para el diagrama de cableado. Viste que el mismo dibujo eléctrico se interpretó y se convirtió en lógica de escalera. Los consejos generales a seguir son: 1. Comprenda el diagrama de cableado desde la alimentación de entrada hasta la alimentación de salida. Mientras tanto, vea qué componentes están colocados, dónde y cómo están cableados. 2. En el cableado, identifica las partes de entrada y las partes de salida y márcalas con colores diferentes. 3. Comienza a programar siguiendo el diagrama y colocando los componentes de la misma manera que se hace el cableado. 4. Ejecuta el programa y observa cómo funciona.