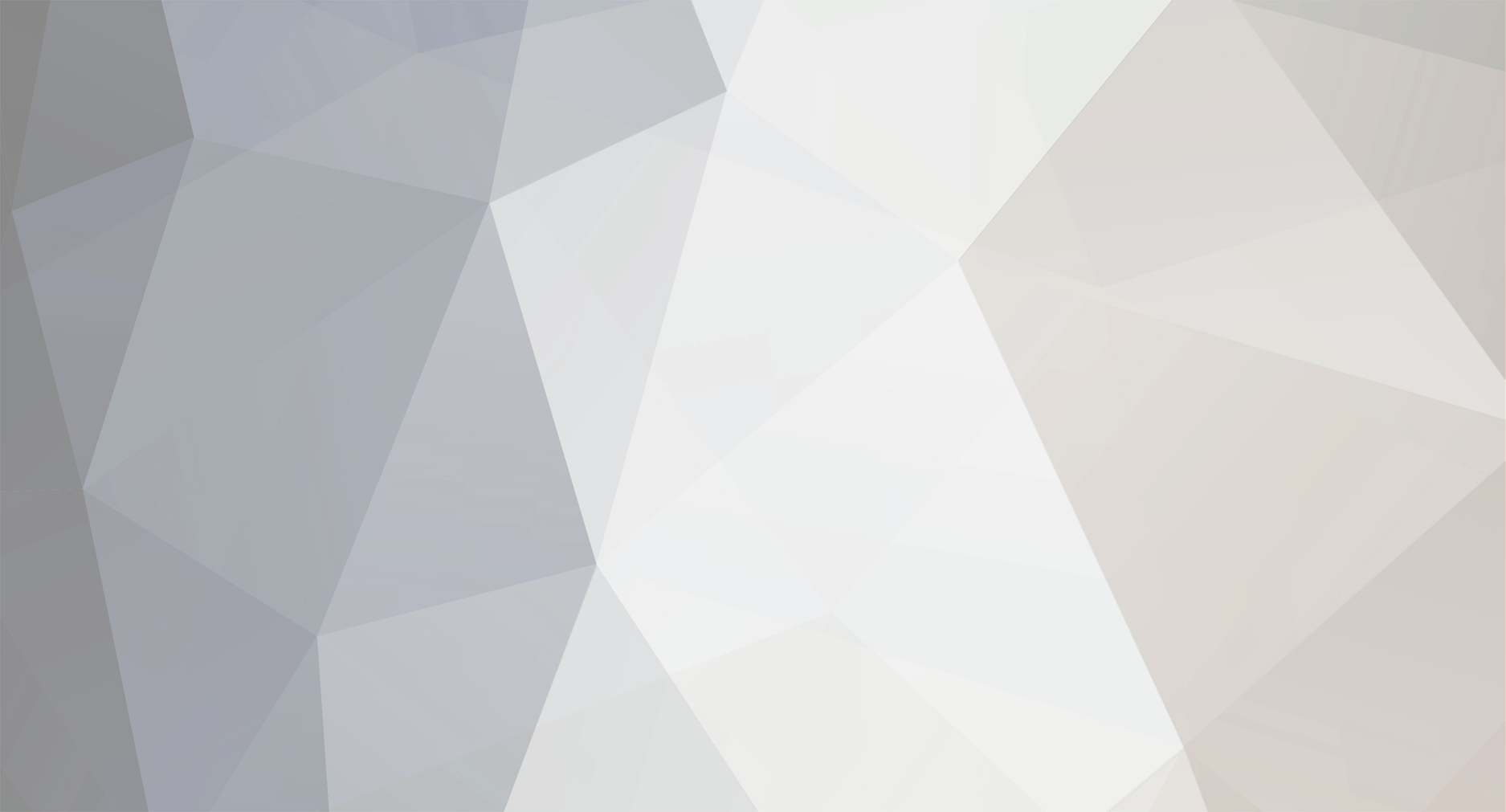
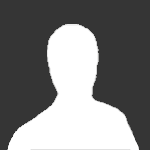
leikang
Staff group-
Content Count
189 -
Joined
-
Last visited
Content Type
Profiles
Forums
PLC programming technology and HMI interface design Simplified Chinese database
- PLC AND HMI SIMPLIFIED CHINESE ARTICLES
- PLC AND HMI SIMPLIFIED CHINESE ARTICLE Comments
- PLC AND HMI SIMPLIFIED CHINESE ARTICLE Reviews
PLC and HMI Brand Database
- PLC AND HMI BRANDS INTRODUCTIONS
- PLC AND HMI BRAND INTRODUCTION Comments
- PLC AND HMI BRAND INTRODUCTION Reviews
PLC programming technology and HMI interface design English database
- PLC AND HMI ENGLISH ARTICLES
- PLC AND HMI ENGLISH ARTICLE Comments
- PLC AND HMI ENGLISH ARTICLE Reviews
PLC programming technology and HMI interface design Russian database
- PLC AND HMI RUSSIAN ARTICLES
- PLC AND HMI RUSSIAN ARTICLE Comments
- PLC AND HMI RUSSIAN ARTICLE Reviews
Spanish database on PLC programming techniques and HMI interface design
- PLC AND HMI SPANISH ARTICLES
- PLC AND HMI SPANISH ARTICLE Comments
- PLC AND HMI SPANISH ARTICLE Reviews
German database on PLC programming technology and HMI interface design
- PLC AND HMI ARTICLES IN GERMAN
- PLC AND HMI ARTICLE IN GERMAN Comments
- PLC AND HMI ARTICLE IN GERMAN Reviews
Downloads
Store
Gallery
Blogs
Calendar
Videos
Everything posted by leikang
-
MITSUBISHI-ES Programación y simulación de PLC para el funcionamiento automático de puertas
leikang posted A plc and hmi article in Spanish in PLC programming learning
En este programa de PLC, el funcionamiento automático de puertas está diseñado mediante programación de PLC para abrir o cerrar la puerta al detectar un objeto. Aquí, el objeto no es más que un automóvil. Funcionamiento automático de puertas La siguiente simulación muestra el funcionamiento del sistema de puertas automáticas. Entradas y salidas Tipo Número de dispositivo Nombre del dispositivo Operación Entrada X0 Límite inferior activado cuando la puerta alcanza el límite inferior. Entrada X1 Límite superior activado cuando la puerta alcanza el límite superior. Entrada X2 Sensor de entrada activado cuando el objeto se acerca a la puerta. Entrada X3 Sensor de salida activado cuando el objeto sale de la puerta. Entrada YO Puerta arriba Se mueve hacia arriba cuando YO está activado. Salida Y1 Puerta abajo Se mueve hacia abajo cuando Y1 está activado. Salida Y6 Luz encendida cuando Y6 está activado. Salida Y7 Zumbador Suena cuando Y7 está activado (la lámpara en la pantalla está encendida). Descripción del programa A medida que el automóvil se acerca a la entrada, la puerta se mueve hacia arriba. Un sensor de entrada X2 se utiliza para detectar la presencia del vehículo en la entrada. En el momento en que el vehículo pasa, la puerta se mueve hacia abajo. Un sensor de salida X3 se utiliza para detectar la presencia del vehículo después de cruzar la puerta. El movimiento ascendente de la puerta se detiene cuando se activa el interruptor de límite superior (X1). De manera similar, el movimiento descendente de la puerta se detiene cuando se activa el interruptor de límite inferior (X0). La puerta permanece levantada mientras se detecte el vehículo dentro del rango de entrada (sensor de entrada X2) y salida (sensor de salida X3). Un zumbador (Y7) suena como señal del movimiento de la puerta. Mientras el vehículo se encuentra dentro del rango de detección, entre el sensor de entrada (X2) y el sensor de salida (X3), una luz (Y6) permanece encendida. El estado del movimiento de la puerta se indica mediante la iluminación o el apagado de cuatro luces indicadoras en el panel de control. Es posible el control manual de la puerta. Los botones del panel de control se pueden presionar para abrir (⬆Puerta arriba) o cerrar (⬇Puerta abajo) la puerta. Programación de PLC -
MITSUBISHI-ES Programación de PLC para línea de distribución y clasificación: lógica avanzada
leikang posted A plc and hmi article in Spanish in PLC programming learning
En esta lógica avanzada de PLC, detecte diferentes tamaños de piezas y clasifíquelas según el tamaño de las cajas y colóquelas en las bandejas. Las piezas no son más que cajas de diferentes tamaños, como pequeñas, medianas y grandes. El robot coloca cajas de diferentes tamaños al azar en la cinta transportadora. Luego, el sistema detecta el tamaño de la caja y se mueve hacia la cinta transportadora correspondiente y las coloca en las bandejas correspondientes. Programación de PLC para línea de distribución y clasificación La siguiente simulación muestra el funcionamiento del sistema de línea de distribución y clasificación. Entradas y salidas Tipo Número de dispositivo Nombre del dispositivo Operación Entrada X0 Punto de inicio (suministro) ENCENDIDO cuando se detecta la pieza. Entrada X1 Superior ENCENDIDO cuando se detecta la pieza. Entrada X2 Medio ENCENDIDO cuando se detecta la pieza. Entrada X3 Inferior ENCENDIDO cuando se detecta la pieza en el extremo derecho. Entrada X4 Sensor ENCENDIDO cuando se detecta la pieza en el extremo derecho. Entrada X5 Sensor El transportador avanza cuando Y1 está ENCENDIDO. Entrada X6 Detectar pieza ON cuando la pieza se detecta delante del empujador. Entrada X10 Punto de inicio (Descargar) ON cuando el robot de descarga está en el punto de inicio. Entrada X11 Pieza en mesa ON cuando la pieza está en la mesa. Entrada X12 Operación del robot finalizada ON cuando la operación del robot ha finalizado. Salida Y1 Transportador hacia delante El transportador se mueve hacia delante cuando Y2 está ON. Salida Y2 Transportador hacia delante Se mueve hacia el frente cuando Y3 está ON. Salida Y3 Ala de clasificación El transportador se mueve hacia delante cuando Y4 está ON. Salida Y4 Transportador hacia delante El transportador se mueve hacia delante cuando Y5 está ON. Salida Y5 Transportador hacia delante Se extiende cuando Y6 está ON y se retrae cuando Y6 está OFF. El empujador no se puede detener en la mitad de la carrera. Salida Y6 Empujador El robot mueve la pieza a la bandeja cuando Y7 está ON. Comienza un ciclo de proceso. Salida Y7 Comando de descarga El robot mueve la pieza a la bandeja cuando Y7 está ON. Comienza un ciclo de proceso. Salida Y10 Rojo Se enciende cuando Y10 está encendido. Salida Y11 Verde Se enciende cuando Y11 está encendido. Salida Y12 Amarillo Se enciende cuando Y12 está encendido. Descripción del programa Al pulsar el botón PB1 (X20) en el panel de control se activa el comando de suministro (Y0), lo que pone al robot en movimiento para mover el objeto. Una vez que el robot ha completado su tarea de mover la pieza y vuelve a su posición original, se desactiva el comando de suministro (Y0). Al activar el comando de suministro (Y0), el robot se impulsa para proporcionar una pieza. Al activar el interruptor SW1 (X24) en el panel de control, los transportadores avanzan. Por el contrario, al desactivar el interruptor, los transportadores se detienen. Las piezas transportadas por el transportador de distintos tamaños, a saber, grandes, medianas y pequeñas, se clasifican según la entrada de los sensores superior (X1), medio (X2) e inferior (X3) y se entregan en bandejas designadas. Las piezas grandes se dirigen al transportador trasero cuando se activa el ala de clasificación (Y3) en el transportador dividido, seguido por el transporte de la pieza en el transportador y finalmente desciende desde el borde derecho. Las piezas medianas se dirigen al transportador delantero cuando se desactiva el ala de clasificación (Y3) en el transportador dividido y, posteriormente, el robot las transfiere a la bandeja. Las piezas pequeñas se dirigen al transportador trasero tras la activación del ala de clasificación (Y3) en el transportador dividido. Una vez que se activa el sensor de detección de piezas (X6) en el transportador dividido, el transportador se detiene y la pieza se empuja hacia la bandeja. Cuando el robot detecta una pieza en la mesa (X11), se activa el comando de descarga (Y7). Una vez que el robot termina sus operaciones, lo que se indica mediante la activación del estado Operación del robot finalizada (X12) (lo que sucede cuando se deposita una pieza en la bandeja), se desactiva el comando de descarga (Y7). Si el interruptor SW2 (X25) del panel de control permanece activado, se produce un suministro automático de una nueva pieza en las siguientes condiciones: Cuando el robot inicia el transporte de una pieza mediana. Cuando se añade una pieza pequeña a la bandeja o una pieza grande desciende por el borde derecho del transportador. Las luces de la pantalla parpadean de la siguiente manera: La luz roja indica que el robot está en proceso de suministro de una pieza. La luz verde significa que el transportador está en movimiento. La luz amarilla se ilumina cuando el transportador está detenido. Programa del PLC -
MITSUBISHI-ES Programación de PLC: clasificación y distribución de cajas por altura
leikang posted A plc and hmi article in Spanish in PLC programming learning
En esta programación de PLC, clasificamos y distribuimos cajas por altura en los contenedores de almacenamiento designados mediante sensores y transportadores. Este programa de PLC distribuye la cantidad especificada de piezas según su tamaño. Clasificación de cajas por altura mediante PLC La siguiente simulación muestra el principio de funcionamiento de la lógica de PLC para clasificar cajas según su altura. Aquí tenemos 3 cajas de diferentes tamaños: pequeña, mediana y grande. Hay tres contenedores de almacenamiento para cada tamaño de caja. Hay tres empujadores y tres transportadores. Cada tamaño de caja tiene un empujador y un transportador. El robot coloca las cajas al azar en el transportador. Los sensores se utilizan para detectar el tamaño de la caja. Los transportadores se ponen en marcha y se detienen cuando el tamaño de caja respectivo llega allí mediante los sensores. El empujador respectivo se activa y mueve el tamaño de caja respectivo a los contenedores de almacenamiento dedicados. Lista de E/S del PLC La siguiente tabla enumera las entradas y salidas de este sistema. Tipo Número de dispositivo Nombre del dispositivo Operación Entrada X0 Punto de inicio ENCENDIDO cuando el robot está en el punto de inicio. Entrada X1 Superior ENCENDIDO cuando se detecta la pieza. Entrada X2 Central ENCENDIDO cuando se detecta la pieza. Entrada X3 Inferior ENCENDIDO cuando se detecta la pieza. Entrada X4 Sensor ENCENDIDO cuando se detecta la pieza en la pendiente. Entrada X5 Sensor ENCENDIDO cuando se detecta la pieza en la pendiente. Entrada X6 Sensor ENCENDIDO cuando se detecta la pieza en la pendiente. Entrada X7 Sensor ENCENDIDO cuando se detecta la pieza en el extremo derecho. Entrada X10 Detectar pieza ENCENDIDO cuando se detecta la pieza delante del empujador. Entrada X11 Detectar pieza ENCENDIDO cuando se detecta la pieza delante del empujador. Entrada X12 Detectar pieza ENCENDIDO cuando se detecta la pieza delante del empujador. Salida Y0 Comando de suministro Se suministra una pieza Cuando Y0 está ENCENDIDO. Comienza un ciclo de proceso: la pieza de madera se repite en orden M, S, L, M, M, L, S, S, L, L. Salida Y1 Transportador hacia adelante El transportador avanza cuando Y1 está ENCENDIDO. Salida Y2 Transportador hacia adelante El transportador avanza cuando Y2 está ENCENDIDO. Salida Y3 Transportador hacia adelante El transportador avanza cuando Y3 está ENCENDIDO. Salida Y4 Transportador hacia adelante El transportador avanza cuando Y4 está ENCENDIDO. Salida Y5 Empujador Se extiende cuando Y5 está ENCENDIDO y se retrae cuando Y5 está APAGADO. El empujador no se puede detener en la mitad de la carrera. Salida Y6 Empujador Se extiende cuando Y6 está ENCENDIDO y se retrae cuando Y6 está APAGADO. El empujador no se puede detener en la mitad de la carrera. Salida Y7 Empujador Se extiende cuando Y7 está ENCENDIDO y se retrae cuando Y7 está APAGADO. El empujador no se puede detener en la mitad de la carrera. Descripción del programa Programación de un controlador lógico programable (PLC) para la clasificación de cajas en función de la altura y la distribución de los componentes. Para iniciar la operación del robot, se debe presionar el botón PB1 (X20) ubicado en el panel de control, que activa el comando de suministro del robot (Y0). El comando de suministro del robot (Y0) se desactiva cuando el robot completa el movimiento de la pieza y regresa a su posición inicial. El comando de movimiento del transportador se controla mediante el interruptor SW1 (X24) en el panel de control. Al activar el interruptor (encenderlo) se impulsa el movimiento del transportador hacia adelante, mientras que al desactivarlo (apagarlo) se detiene el transportador. La clasificación de las piezas, segregadas en tamaños grande, mediano y pequeño, se ejecuta a través de la entrada de los sensores superior (X1), medio (X2) e inferior (X3). Después de la clasificación, las piezas se transportan a sus bandejas designadas. La presencia de una pieza en el empujador se identifica mediante la activación (encendido) de los sensores de detección de piezas (X10, X11 o X12). Tras la detección de una pieza, el transportador se detiene y la pieza detectada se desplaza hacia la bandeja. Nota: El funcionamiento del empujador se rige por el comando de accionamiento del empujador. Al recibir una señal de encendido, el empujador se extiende por completo, mientras que una señal de apagado hace que se retraiga. Cada bandeja debe contener una cantidad específica de piezas, según su tamaño. Las piezas que superen estas cantidades especificadas pasan por alto el empujador y se expulsan del transportador por el extremo derecho. La cantidad designada de piezas por tamaño es la siguiente: Grande: 3 piezas Mediano: 2 piezas Pequeño: 2 piezas Lógica de escalera de PLC -
MITSUBISHI-ES Sistema de máquina clasificadora de productos basado en PLC: control de elevador
leikang posted A plc and hmi article in Spanish in PLC programming learning
En este programa avanzado de PLC, se utiliza un sistema de máquina clasificadora de productos basado en PLC para transportar diferentes productos mediante el elevador para separar las piezas según el tamaño. Aquí hay tres posiciones disponibles según el tamaño, como pequeño, mediano y grande. Los transportadores se utilizan para transferir los productos y colocarlos en las bandejas. Sistema de máquina clasificadora de productos basado en PLC La siguiente simulación muestra el sistema de clasificación de PLC mediante la operación de elevador. Entradas y salidas Tipo Número de dispositivo Nombre del dispositivo Operación Entrada X0 Superior ENCENDIDO cuando se detecta la pieza. Entrada X1 Medio ENCENDIDO cuando el elevador está en una posición inferior. Entrada X2 Inferior ENCENDIDO cuando se detecta la pieza. Entrada X3 Pieza en elevador ENCENDIDA cuando se detecta la pieza. Entrada X4 Posición de elevador inferior ENCENDIDA cuando el elevador está en la posición media. Entrada X5 Posición de elevador medio ENCENDIDA cuando el elevador está en la posición media. Entrada X6 Posición de elevador superior ENCENDIDA cuando la pieza está en el elevador. Entrada X10 Sensor ON cuando la pieza se detecta en el extremo izquierdo. Entrada X11 Sensor ON cuando la pieza se detecta en el extremo izquierdo. Entrada X12 Sensor ON cuando la pieza se detecta en el extremo derecho. Entrada X13 Sensor ON cuando la pieza se detecta en el extremo izquierdo. Entrada X14 Sensor ON cuando la pieza se detecta en el extremo derecho. Entrada X15 Sensor ON cuando el elevador está en la posición superior. Salida YO Comando de suministro Se suministra una pieza cuando YO está ON: El cilindro de metal se repite en orden S, L, M, L, M, S. Salida Y1 Transportador hacia adelante ON cuando la pieza se detecta en el extremo derecho. Salida Y2 Comando de elevación hacia arriba El elevador se mueve hacia arriba cuando Y2 está ON. El elevador se detiene cuando Y2 está OFF. Salida Y3 Comando de elevación hacia abajo El elevador se mueve hacia abajo cuando Y3 está ON. El elevador se detiene cuando Y3 está OFF. Salida Y4 Comando de rotación del elevador El transportador se mueve hacia adelante cuando Y1 está ON. Salida Y5 Bajar transportador hacia adelante El elevador gira para transferir la pieza al transportador cuando Y4 está ON. El elevador gira de nuevo a la posición original cuando Y4 está APAGADO. Salida Y6 Transportador intermedio hacia adelante El transportador avanza cuando Y5 está ENCENDIDO. Salida Y7 Transportador superior hacia adelante El transportador avanza cuando Y6 está ENCENDIDO. Descripción del programa El sistema completo consta de dos componentes: Control general y Gestión del elevador. Control general: Al activar el botón PB1 (X20) en el panel operativo se inicia el comando de suministro (Y0) para la tolva. Al desactivar el botón PB1 (X20) se desactiva el comando de suministro (Y0). Al activar el comando de suministro (Y0), la tolva entrega una pieza. Los transportadores inician el movimiento cuando se activa el SW1 (X24) en el panel de control. Por el contrario, los transportadores detienen el movimiento cuando se desactiva el SW1 (X24). Al detectar una pieza mediante el sensor X10, X12 o X14 ubicado a la izquierda del transportador, se inicia el transportador correspondiente, transportando la pieza a la bandeja del extremo derecho. Tres segundos después de que una pieza pase por el sensor X11, X13 o X15 a la derecha del transportador, este se detiene. Las piezas de distintos tamaños (grande, mediana, pequeña) en el transportador se clasifican según las entradas de los sensores Superior (X0), Medio (X1) e Inferior (X2). Gestión del elevador: Una vez que se activa la pieza en el sensor del elevador (X3) en el elevador, la pieza se transporta a uno de los siguientes transportadores según su tamaño: Pieza grande: dirigida al transportador superior Pieza mediana: dirigida al transportador mediano Pieza pequeña: dirigida al transportador inferior Los comandos de elevación hacia arriba (Y2) y elevación hacia abajo (Y3) se gestionan según la posición del elevador, detectada por los siguientes sensores: Superior: X6 Medio: X5 Inferior: X4 Al transferir la pieza del elevador al transportador, se inicia el comando de rotación del elevador (Y4). Después de la transferencia de una pieza, el elevador vuelve a su posición inicial y permanece en espera. Lógica del PLC -
MITSUBISHI-ES Programa PLC para control de escenario: cortinas y elevación del escenario
leikang posted A plc and hmi article in Spanish in PLC programming learning
El programa PLC para control de escenario permite abrir y cerrar las cortinas, así como subir y bajar el escenario. Ofrece dos modos de funcionamiento: automático y manual. Programa PLC para control de escenario La siguiente simulación muestra el uso de PLC para aplicaciones de control de escenario. Este es un proyecto de utilidad en el que tenemos que abrir y cerrar las cortinas del escenario de forma automática y también manual mediante pulsadores. Los sensores se utilizan para detectar las posiciones de las cortinas derecha e izquierda en diferentes puntos. Después de abrir las cortinas, el escenario se moverá hacia arriba y se elevará a la posición superior. De manera similar, cuando las cortinas estén cerradas, el escenario central se moverá hacia abajo. La posición del escenario también se rastreará mediante sensores de límite inferior y superior. Lista de dispositivos PLC La siguiente tabla enumera todas las entradas y salidas de este programa PLC. Tipo Número de dispositivo Nombre del dispositivo Operación Entrada X0 Interior (cortina izquierda) ON cuando la cortina está a la mitad. Entrada X1 ON cuando la cortina se cierra completamente. ON cuando la cortina se abre completamente. Entrada X2 Exterior (cortina izquierda) ON cuando la cortina se cierra completamente. Entrada X3 Interior (cortina derecha) ON cuando la cortina está a la mitad. Entrada X4 Medio (cortina derecha) ON cuando la cortina se abre completamente. Entrada X5 Exterior (cortina derecha) ON cuando el escenario alcanza un límite inferior. Entrada X6 Límite superior de escenario El escenario se mueve hacia arriba cuando Y2 está ON. El escenario se detiene cuando Y2 está OFF. Entrada X7 Límite inferior de escenario ON cuando el escenario alcanza el límite superior. Salida Y0 Comando de apertura de cortina Las cortinas se abren cuando Y0 está ON. Las cortinas se detienen cuando Y0 está OFF. Salida Y1 Comando de cierre de cortina Las cortinas se cierran cuando Y1 está ON. Las cortinas se detienen cuando Y1 está OFF. Salida Y2 Escenario arriba El escenario se mueve hacia arriba cuando Y2 está ON. El escenario se detiene cuando Y2 está OFF. Salida Y3 Escenario hacia abajo El escenario se mueve hacia abajo cuando Y3 está encendido. El escenario se detiene cuando Y3 está apagado. Salida Y5 Zumbador Suena cuando Y5 está encendido (la lámpara en la pantalla está encendida). Descripción del programa Programa de PLC para controlar los ajustes del escenario, incluyendo la apertura/cierre de cortinas y la subida/bajada del escenario. El propósito de este programa de PLC es facilitar el control sobre una variedad de ajustes del escenario, que abarcan tareas como la apertura y el cierre de cortinas, así como la subida y bajada del escenario en sí. Para adaptarse a diferentes preferencias y requisitos, el programa ofrece dos modos de operación distintos: automático y manual. Operación automática Cuando se presiona el botón “Begin” (X16) en el panel de operación, un timbre (Y5) emite un sonido durante 5 segundos. Nota: El botón “Begin” (X16) solo se puede activar cuando las cortinas están cerradas y el escenario está ubicado en su límite inferior. Después de que el timbre se detiene, se activa el comando para abrir las cortinas (Y0). Las cortinas continuarán abriéndose hasta alcanzar sus límites exteriores, definidos por las señales de entrada X2 y X5. Una vez que las cortinas están completamente abiertas, el escenario comienza a elevarse cuando se activa el comando “Escenario arriba” (Y2). El escenario continuará moviéndose hacia arriba hasta alcanzar su límite superior, como lo indica la señal de entrada X6. Al presionar el botón “Fin” (X17) en el panel de operación, se inicia el cierre de las cortinas. Se activa el comando para cerrar las cortinas (Y1) y las cortinas se cerrarán hasta que alcancen sus límites interiores, definidos por las señales de entrada X0 y X3. Operación manual Las siguientes operaciones solo están disponibles cuando la operación automática descrita anteriormente no está activa. Las cortinas se pueden abrir presionando el botón “Cortina abierta” (X10) en el panel de operación. Las cortinas se detendrán una vez que alcancen sus límites exteriores (X2 y X5). Las cortinas se pueden cerrar presionando el botón “Cerrar cortina” (X11) en el panel de operación. Las cortinas continuarán cerrándose hasta que alcancen sus límites internos (X0 y X3). El escenario se puede elevar presionando el botón “⬆Escenario arriba” (X12) en el panel de operación. El escenario se detendrá una vez que alcance su límite superior (X6). El escenario se puede bajar presionando el botón “⬇Escenario abajo” (X13) en el panel de operación. El escenario se detendrá una vez que alcance su límite inferior (X7). Las luces indicadoras en el panel de operación se iluminarán o apagarán según corresponda, brindando información visual sobre el estado de las cortinas y las operaciones del escenario. Programación de PLC -
Diferencias entre E/S cableadas y E/S seriales de PLC
leikang posted A plc and hmi article in Spanish in PLC programming learning
En los controladores lógicos programables (PLC) y los sistemas de control distribuido (DCS), la elección entre E/S cableadas y E/S seriales se vuelve especialmente crítica debido a la naturaleza en tiempo real de estos sistemas y las complejidades asociadas de los procesos industriales. A continuación, desglosaré las características de cada uno en estos sistemas específicos. E/S cableadas A continuación, se enumeran los puntos principales que debemos analizar sobre las E/S cableadas. Conexión directa Respuesta en tiempo real Complejidad del cableado Flexibilidad limitada Fiabilidad Integridad de la señal Idoneidad Aplicaciones críticas para la seguridad 1. Conexión directa Las E/S cableadas se conectan directamente al PLC o DCS. Cada dispositivo de entrada o salida tiene una línea dedicada que regresa al controlador. 2. Respuesta en tiempo real Estas E/S generalmente están diseñadas para tareas de control en tiempo real. Se utilizan especialmente en aplicaciones sensibles al tiempo, como control de procesos, interbloqueos y paradas de emergencia, donde se requiere una acción inmediata. 3. Complejidad del cableado Para sistemas grandes con numerosos puntos de E/S, las soluciones cableadas pueden volverse engorrosas, requiriendo un cableado extenso y gabinetes de control más grandes. 4. Flexibilidad limitada Modificar o expandir un sistema cableado puede requerir mucho trabajo debido a la necesidad de recableado físico. 5. Fiabilidad Las E/S cableadas suelen considerarse más confiables para tareas críticas debido a su naturaleza sencilla, punto a punto, lo que reduce el riesgo de fallas de comunicación. 6. Integridad de la señal La integridad de la señal suele ser mejor con conexiones cableadas, especialmente en entornos con mucha interferencia electromagnética (EMI) en comparación con la comunicación en serie. 7. Idoneidad Más adecuadas para sistemas más pequeños o en escenarios donde la confiabilidad y la velocidad son de suma importancia. 8. Seguridad Las E/S cableadas se utilizan principalmente en aplicaciones críticas para la seguridad, como las aplicaciones de control de procesos industriales donde los bucles de control son críticos. E/S serial A continuación, se enumeran los puntos principales que debemos analizar sobre las E/S seriales. Serialización de datos Comunicación basada en protocolos Escalabilidad Capacidad de red Manejo de datos Distancia Vulnerabilidad Costo Seguridad 1. Serialización de datos Las E/S seriales transmiten datos de a un bit por vez, generalmente a través de una sola línea de datos. Esto contrasta con los sistemas paralelos que envían múltiples bits simultáneamente. Tenemos cables individuales para cada señal en las E/S cableadas, pero las E/S seriales generalmente tienen un solo cable para transmitir/recibir todos los datos. 2. Comunicación basada en protocolos Por lo general, se basan en protocolos industriales establecidos como Modbus, PROFIBUS o Ethernet/IP para la comunicación, que estandarizan el intercambio de datos entre dispositivos. 3. Escalabilidad Las E/S seriales son generalmente más escalables. Agregar más puntos de E/S a menudo solo requiere configurar la red existente, sin necesidad de cableado adicional de regreso al controlador. 4. Capacidad de red Las E/S seriales se pueden conectar en red fácilmente y, a menudo, cuentan con diagnósticos integrados, lo que las hace más versátiles pero también agrega complejidad. 5. Manejo de datos Las E/S seriales son más versátiles en lo que respecta al manejo de datos. Pueden transmitir tipos de datos más complejos, incluidos números reales y cadenas, a través de la red. 6. Distancia Son más adecuadas para aplicaciones donde los puntos de E/S están ubicados lejos del controlador PLC o DCS. Es posible que necesitemos algunos dispositivos especiales como repetidores, puertas de enlace, etc. para algunos casos. 7. Vulnerabilidad Debido a que se basan en protocolos, las E/S seriales pueden ser más vulnerables a problemas como colisiones de datos, latencia y otros problemas relacionados con la red. 8. Costo Si bien los costos iniciales de configuración pueden ser más altos debido al hardware de red, el costo a largo plazo puede ser menor, en particular para sistemas que requieren modificaciones o escalamiento frecuentes. 9. Seguridad Las E/S seriales nunca se utilizan en aplicaciones críticas para la seguridad, ya que el daño del cable principal puede provocar una falla total de los datos. Elección entre E/S cableadas y seriales La elección entre las dos suele depender de varios factores, como el tamaño del sistema, la velocidad de operación requerida, la seguridad, la complejidad de los datos y las consideraciones de costo. Los ingenieros suelen realizar un análisis detallado, a veces incluso utilizando ambos tipos en diferentes secciones de un solo sistema PLC o DCS para aprovechar las ventajas de cada uno. Por ejemplo, las E/S cableadas se pueden utilizar para aplicaciones críticas para la seguridad, mientras que las E/S seriales se pueden utilizar para tareas de recopilación y monitoreo de datos. Comparación entre E/S cableadas y E/S seriales La siguiente tabla muestra las diferencias entre E/S cableadas y E/S seriales. Parámetros E/S cableadas E/S seriales Tipo de conexión Conexión directa, punto a punto Basada en protocolo, generalmente en red Velocidad de transferencia de datos Generalmente más rápida, procesamiento en tiempo real Puede ser más lenta debido a la serialización (según el protocolo) Complejidad Puede ser más lenta debido a la serialización (según el protocolo) Complejidad más manejable Escalabilidad Difícil y costosa de escalar Más fácil y menos costosa de escalar Fiabilidad Mayor debido a menos puntos de falla Puede tener más puntos de falla Cableado Se requiere cableado extenso Menos cableado, a menudo solo una sola línea de datos Integridad de la señal Mejor en entornos con alta EMI Puede ser susceptible a EMI Tipos de datos admitidos Generalmente señales analógicas de 4-20 mA, 24 V CC para señales digitales. Este valor puede ser mayor debido al hardware de red Distancia Adecuado para distancias más cortas Puede manejar distancias más largas Costo (inicial) Menor para sistemas pequeños y Mayor para sistemas más grandes Alto (depende del protocolo) Costo (mantenimiento) Mayor debido a la complejidad de la resolución de problemas Generalmente menor Flexibilidad Limitado; difícil de modificar Altamente flexible; fácil de modificar Redundancia Difícil y costoso de implementar Más fácil y menos costoso de implementar Aplicaciones de seguridad A menudo se usa para tareas críticas para la seguridad Se usa con menos frecuencia para tareas críticas para la seguridad Diagnóstico de red Limitado o ninguno A menudo integrado Cuando se trata de seguridad en los sistemas PLC y DCS, las E/S cableadas y las E/S seriales tienen diferentes características que pueden mejorar o potencialmente comprometer la seguridad de un proceso industrial. A continuación se muestra una tabla de comparación enfocada únicamente en el aspecto de seguridad de estos dos tipos de sistemas de E/S. Aspecto de seguridad E/S cableadas E/S seriales Confiabilidad Generalmente mayor confiabilidad debido a conexiones directas y menos puntos de falla. Basado en protocolos y redes, lo que introduce más puntos de falla potenciales. Capacidad de respuesta en tiempo real Excelente para la respuesta en tiempo real, a menudo se usa en apagados de emergencia y enclavamientos de seguridad. Puede experimentar latencia debido a la congestión de la red o limitaciones del protocolo, lo que los hace menos ideales para una acción inmediata. Complejidad del sistema Una menor complejidad generalmente hace que sea más fácil identificar y abordar problemas de seguridad. La complejidad de las redes y los protocolos puede dificultar la identificación de la causa raíz de los problemas de seguridad. Integridad de la señal Menos susceptible a la interferencia electromagnética (EMI), lo que mejora la calidad y confiabilidad de la señal. Potencialmente más susceptible a la EMI y la degradación de la señal, lo que podría comprometer la seguridad. Integridad de los datos Debido a que generalmente es punto a punto, la corrupción de datos es menos probable. Más propenso a problemas de integridad de datos debido a la red, lo que aumenta el riesgo de fallas relacionadas con la seguridad. Error humano Menos propenso a errores de configuración que afecten la seguridad, debido a su simplicidad. Mayor probabilidad de errores humanos durante la configuración o el mantenimiento, lo que afecta la seguridad del sistema. Situaciones de emergencia A menudo, la opción preferida para sistemas críticos para la seguridad, como apagados de emergencia, debido al tiempo de respuesta rápido. Por lo general, no se utiliza para tareas de acción inmediata debido a la posible latencia y otros problemas relacionados con la red. Seguridad Menor susceptibilidad a ataques cibernéticos, ya que generalmente no están conectados en red. Más vulnerable a amenazas cibernéticas que pueden comprometer la seguridad, debido a la red. Funciones de seguridad integradas Las funciones de seguridad suelen estar cableadas y son sencillas, lo que las hace robustas. Pueden tener protocolos de seguridad integrados, pero estos pueden verse comprometidos por problemas de red. Certificaciones Más fácil de certificar para aplicaciones críticas para la seguridad debido a la menor complejidad y mayor confiabilidad. Puede requerir pruebas y certificaciones más exhaustivas debido a las complejidades de la red y el protocolo. Desde una perspectiva de seguridad, la elección entre E/S cableadas y seriales suele inclinarse hacia las E/S cableadas para aplicaciones de seguridad críticas, debido a su confiabilidad inherente y sus capacidades de respuesta inmediata. Sin embargo, la seguridad general de un sistema no está determinada únicamente por el tipo de E/S utilizado; también está influenciada por factores como el diseño, las prácticas de mantenimiento y la competencia del personal operativo. -
¿Qué es un proyecto de modernización de PLC? – Importancia, procedimiento
leikang posted A plc and hmi article in Spanish in PLC programming learning
Un proyecto de modernización de PLC implica actualizar o reemplazar el antiguo sistema PLC (controlador lógico programable) con una versión más nueva y avanzada. Esto se hace para mejorar el rendimiento, agregar nuevas funciones o mantener la compatibilidad con tecnologías modernas, todo mientras se minimiza la necesidad de reemplazar por completo el equipo existente. Proyecto de modernización de PLC Cuando se trabaja en cualquier sistema, ya sea automatización industrial o cualquier otra cosa, no siempre es necesario poner en funcionamiento una planta completamente nueva. Hay ocasiones en las que una planta antigua no funciona correctamente según los resultados deseados. Esto significa que no todo el sistema, solo algunas partes. Puede ser un sistema PLC, un sistema eléctrico o un sistema mecánico. En lugar de cambiar todo el sistema, es mejor reemplazar solo esa parte por una nueva. Los sistemas restantes se mantendrán como están. Esto se llama modernización. Es un aspecto muy importante que los ingenieros deben aprender. En esta publicación, veremos los pasos relacionados con la modernización de un sistema PLC. ¿Por qué es necesaria la modernización de PLC? Cuando se tiene un sistema PLC, es inevitable que falle en ocasiones. Es algo natural para cualquier sistema (no solo para los PLC) y no significa que el sistema PLC falle siempre. Es el peor escenario posible. Ahora bien, aparte del PLC, el resto de los sistemas eléctricos y mecánicos funcionan bien. Las causas más comunes de la necesidad de reemplazar un sistema PLC son: errores repetidos en la lógica, un PLC obsoleto que ha fallado y ya no está disponible en el mercado, fallas repetidas de firmware o hardware en el PLC y falta de servicio. En estos casos, en lugar de reemplazar todo el sistema, la mejor opción es reemplazar solo el sistema PLC. Esto se denomina trabajo de modernización del PLC. Básicamente, se actualiza el PLC por uno nuevo o se lo reemplaza por completo por uno de una marca nueva. Esto reduce los costos, no afecta la planta de trabajo original, ahorra tiempo y aumenta la confiabilidad. Básicamente, la lógica de trabajo de la planta seguirá siendo la misma; solo se la reemplaza por un nuevo hardware y se pone en funcionamiento la planta. Procedimiento para el proyecto de modernización de PLC El primer paso es estudiar el plano del panel de control del PLC. Cada PLC tiene su propia versión diferente de cableado y también el concepto de sumidero-fuente. Por lo tanto, es necesario que primero comprenda el cableado original realizado. Esto lo ayudará a preparar una nueva lista de E/S según su PLC actual. Porque si sigue la misma lista de IP a ciegas, enfrentará principalmente problemas de cableado en el sitio cuando instale el nuevo PLC Obtenga el programa antiguo si es posible. Si no es posible, desarrolle una nueva lógica fresca en la oficina antes de ir al sitio. Además, pruebe la lógica con el cliente o, en el mejor de los casos, el cliente final. El cliente final será de gran ayuda porque ha operado el antiguo sistema PLC y puede ayudar a resolver consultas rápidamente. El cliente puede ayudar a verificar en profundidad el proceso. Si se prueba el programa antes de ir al sitio, se reducirá drásticamente su tiempo en el sitio. Intente hacer coincidir las pantallas y desarrollar los gráficos como están con los antiguos en funcionamiento. Esto ayudará a los operadores a operar la planta con más facilidad, como están acostumbrados. Una vez que la lógica y los gráficos estén listos, planifique la visita al sitio con el electricista. El electricista primero reemplazará el nuevo PLC en lugar del antiguo y luego verificará todos los puntos con un multímetro. Esto es para asegurarse de que todos los puntos se hayan conectado o no según el nuevo cableado. Una cosa importante a tener en cuenta es que la modernización requiere un apagado adecuado, así que asegúrese antes de planificar la visita al sitio. Una vez que se haya verificado el cableado sin alimentación, encienda el sistema y descargue los programas más recientes en el PLC y los gráficos. Ahora, en primer lugar, debe verificar las E/S. Este es un paso muy crucial, porque está reemplazando el cableado antiguo por uno nuevo. Todas las E/S en el campo deben responder de la misma manera que funcionaban antes. Sin esto, no puede hacer funcionar la planta en modo automático o manual. Ahora, verifique la lógica escrita y vea si se está ejecutando según el sistema anterior o no. Todos los enclavamientos de seguridad, condiciones permisivas, secuencias y otra lógica deben funcionar de la misma manera que el sistema anterior. Tanto el cliente como el cliente final deben aprobar esto para su verificación y mencionarlo en el informe si está funcionando correctamente. Realice todos los informes finales, guarde la copia de seguridad final y tome fotografías y videos del sistema en funcionamiento. Esto garantiza un informe de finalización del proyecto de modernización del PLC que ha realizado. Resumen del proyecto de PLC Evalúe el sistema de PLC existente, identifique las necesidades de modernización y determine los objetivos, el alcance y las limitaciones del proyecto. Diseñe un nuevo plan detallado del sistema, garantizando la integración con la maquinaria y la red existentes, y desarrolle una estrategia de migración. Realice una copia de seguridad de todos los programas, datos y documentación del sistema actual y prepare un plan de recuperación. Adquiera el nuevo PLC y cualquier hardware adicional, garantizando la compatibilidad y disponibilidad. Prepare el sitio de instalación con las medidas de seguridad necesarias y programe el tiempo de inactividad si es necesario. Desmantele el sistema PLC antiguo e instale el nuevo PLC y el hardware relacionado. Transfiera o reescriba la lógica del programa al nuevo PLC, probando todas las funciones y la comunicación. Realice pruebas integrales del nuevo sistema, valide el rendimiento y realice los ajustes necesarios. Capacite al personal sobre las operaciones y el mantenimiento del nuevo sistema, y actualice o cree la documentación del sistema. Cambie oficialmente al nuevo sistema PLC, controle de cerca los problemas y brinde el soporte necesario. Realice una revisión posterior a la implementación para evaluar el éxito, documentar las lecciones aprendidas y planificar el mantenimiento o las actualizaciones futuras. -
SIEMENS-ES Transferencia de datos entre sistemas PLC: TSEND_C y TRCV_C
leikang posted A plc and hmi article in Spanish in PLC programming learning
En los últimos artículos, analizamos cómo establecer una conexión entre dos PLC mediante los bloques TCON y TDISCON y cómo mover datos entre ellos mediante los bloques TSEND y TRCV. Transferencia de datos entre sistemas PLC En este artículo, aprenderemos una nueva instrucción que se puede utilizar para comunicarse y transferir datos entre sistemas PLC mediante los bloques TSEND_C y TRCV_C. TSEND_C La instrucción TSEND_C es una instrucción de TIA Portal que se utiliza para configurar y establecer una conexión entre dos PLC. Una vez que se ha configurado y establecido la conexión, el PLC la mantendrá y supervisará automáticamente. La instrucción TSEND_C se ejecuta de forma asincrónica y tiene las siguientes funciones: Configurar y establecer una conexión de comunicación similar al bloque TCON. Enviar datos a través de una conexión de comunicación existente similar al bloque TSEND. Terminar o restablecer la conexión de comunicación similar al bloque TDISCON. Por lo tanto, el nombre compact se le da a la instrucción TSEND_C, ya que actúa como más de 3 bloques al mismo tiempo. TRCV_C La instrucción TRCV_C también es una instrucción TIA Portal que se utiliza para configurar y establecer una conexión entre dos PLC. Una vez que se ha configurado y establecido la conexión, el PLC la mantendrá y supervisará automáticamente. La instrucción “TRCV_C” se ejecuta de forma asincrónica e implementa las siguientes funciones en secuencia: Configurar y establecer una conexión de comunicación similar a TCON. Recibir datos a través de una conexión de comunicación existente similar a TRCV. Terminar o restablecer la conexión de comunicación similar a TDISCON. Por lo tanto, el nombre compact se le da a la instrucción TRCV_C, ya que actúa como más de 3 bloques al mismo tiempo. Uso de TSEND_C y TRCV_C en nuestro proyecto de PLC En el último artículo, cuando necesitábamos establecer y pasar a enviar datos desde PLC_1 a PLC_2, tuvimos que usar tres bloques diferentes en cada PLC. Vea la imagen 1. imagen 1. Lógica dentro de PLC_1 Como puede ver, usamos los bloques TCON y TDISCON para establecer y restablecer la conexión y usamos TSEND para enviar los datos desde PLC_1. Y lo mismo se hizo para PLC_2. Vea la imagen 2. imagen 2. Lógica de PLC_2 Nuevamente, usamos los bloques TCON y TDISCON para establecer y restablecer la conexión y usamos TRCV para recibir los datos desde PLC_1. Ahora, queremos reemplazar todos estos bloques e intentar usar TSEND_C y TRCV_C en su lugar para lograr la misma funcionalidad. Primero, en PLC_1 donde necesitamos enviar datos, usaremos el bloque TSEND_C, solo arrastre y suelte el bloque dentro del OB1 principal. Consulte la imagen 3. imagen 3. Agregue el bloque TSEND_C. Como TSEND_C es esencialmente un bloque de función, se le solicitará que cree una instancia de datos. Consulte la imagen 4. imagen 4. Cree una instancia para TSEND_C TSEND_C se parece al bloque TSEND en el sentido de que necesita realizar algunas configuraciones y agregar algunas señales. Consulte la imagen 5. imagen 5. Bloque TSEND_C Ahora, necesitamos una señal para que REQ y Data envíen y también para configurar la conexión. Para la señal REQ, creamos una etiqueta SendData. Además, podemos simplemente arrastrar y soltar el bloque de datos que creamos en el último artículo que necesitamos enviar a PLC_2, podemos simplemente arrastrarlo y soltarlo en la entrada DATA del bloque. Consulte la imagen 6. imagen 6. Configuración del bloque TSEND_C. Para configurar el parámetro de conexión para el bloque, podemos presionar el pequeño ícono de configuración en la parte superior del bloque para abrir la vista de configuración. La vista de configuración se verá muy similar a la del bloque TCON. Consulte la imagen 7. imagen 7. Parámetros de conexión de TSEND_C Ya mostramos cómo configurar el parámetro de conexión en artículos anteriores, por lo que podemos hacer lo mismo que hicimos con el bloque TCON, consulte la imagen 8. imagen 8. Configuración del parámetro de conexión Con esta configuración de conexión, terminamos todas las configuraciones de TSEND_C. Observe cuánto más rápido fue en comparación con la configuración de los bloques TCON, TDISCON y TSEND. Ahora, necesitamos agregar el TRCV_C al PLC_2 para que pueda recibir los datos enviados desde el PLC_1. En el OB1 principal del PLC_1, simplemente arrastre y suelte el TRCV_C en su lógica. Vea la imagen 9. Recuerde crear una instancia de datos para el bloque TRCV_C. imagen 9. Agregue el TRCV_C Una vez que se agrega el TRCV_C a su lógica, debemos configurarlo. Como hicimos con el TSEND_C, necesitamos agregar una señal para habilitar la recepción de datos y también necesitamos agregar el bloque de datos en el que guardaremos los datos. Vea la imagen 10. imagen 10. TRCV_C Definimos una etiqueta RecieveData como la señal EN_R. Ver imagen 11. imagen 11. Definir etiqueta EN_R Recuerde desmarcar la opción “acceso optimizado al bloque” del bloque de datos o el bloque no funcionará como mostramos en los artículos anteriores. A continuación, debemos configurar los parámetros de conexión del bloque TRCV_C, como hicimos con TSEND_C, solo tenga en cuenta que el PLC asociado no especificado ahora es el PLC_1, consulte la imagen 12. imagen 12. Parámetros de conexión de TRCV_C Simulación del proyecto de PLC Ahora que hemos configurado el bloque TSEND_C y TRCV_C, queremos simular nuestro proyecto y ver cómo funcionarán, pero primero, crearemos una lógica simple para actualizar automáticamente los datos de PLC_1 que se enviarán a PLC_2. Consulte la imagen 13. imagen 13. Lógica simple para actualizar datos automáticamente. Ahora, compilemos e iniciemos una simulación para nuestro proyecto. Lo primero que notará es que PLC_1 y PLC_2 intentarán establecer una conexión de inmediato porque configuramos TSEND_C y TRCV_C, ellos intentan establecer una conexión automáticamente. Por eso habrá una conexión entre los dos PLC. Ver imagen 14. Imagen 14. La conexión se establece directamente. Como puede ver, la conexión entre los PLC se establece directamente, porque el parámetro CONT en TSEND_C y TRCV_C está configurado en TRUE, lo que significa que el bloque intentará establecer automáticamente una conexión con el PLC asociado. Podemos colocar cualquier señal de control aquí para controlar el establecimiento de la conexión. La otra cosa que puede ver es que el REQ de TSEND_C y el EN_R de TRCV_C están configurados en FALSE, y es por eso que no habrá transferencia de datos entre los PLC. Ver imagen 15. imagen 15. No hay transferencia de datos entre los PLC. Si la señal REQ de TSEND_C se establece en verdadero, el PLC_1 intentará enviar los datos, pero esperará a que el otro PLC habilite la recepción de los datos, consulte la imagen 16. imagen 16. REQ es verdadero. Como puede ver, SendData es VERDADERO, pero no se enviaron datos porque RecieveData sigue siendo falso. El PLC_2 solo recibirá datos del PLC_1 cuando ReceiveData esté establecido en verdadero. Consulte la imagen 17. imagen 17. Los datos se envían al PLC_2 Como puede ver, cuando RecieveData es verdadero, los datos se enviarán del PLC_1 al PLC_2. Sin embargo, puede ver que los datos dentro de los dos PLC son diferentes porque los datos del PLC_1 cambian automáticamente según la lógica simple que hicimos antes. Esto significa que la señal EN_R permite la transferencia de datos una vez, cuando necesito transferir datos nuevamente, esta señal debe volverse falsa y luego verdadera nuevamente. Consulte el proyecto TIA Portal adjunto y observe la transferencia de datos entre PLC. -
Cómo implementar el flip flop SR usando lógica de escalera de PLC
leikang posted A plc and hmi article in Spanish in PLC programming learning
Este es el programa de PLC para implementar el flip flop SR en PLC. Aprenda la programación de PLC con esta lógica de ejemplo. Flip flop SR usando lógica de escalera de PLC Descripción del problema Implemente un programa para la lógica del flip flop SR en PLC usando lenguaje de escalera. Diagrama del problema Solución de PLC Como sabemos, los sistemas más complejos no se pueden controlar solo con lógica combinacional. La razón principal es que no podemos, o elegimos no agregar sensores para detectar todas las condiciones. En estos casos, podemos usar eventos para estimar la condición del sistema. El flip flop SR se usa para bloquear o desbloquear algo, para bloquear algo en ON o apagarlo. La mayoría de los PLC tienen instrucciones especiales para la función de flip flop SR, por lo que no se requiere lógica personalizada para este tipo de PLC. El flip flop SR primero ejecuta la función SET y luego la función RESET. Nota: aquí estamos considerando la función simple de la instrucción de flip flop SR sin usar una instrucción especial ni usar la función de enclavamiento. Aquí estamos usando un circuito de enclavamiento simple para la función de flip flop SR. Aquí, como se muestra en la figura, se toman dos botones pulsadores o dos entradas para la implementación del programa. Cuando el usuario presione el botón SET o se reciba 1 en la entrada S, la salida Q estará ENCENDIDA y si se presiona el botón RESET o se recibe 1 en la entrada R, Q^ estará ENCENDIDA. Lista de entradas/salidas Entradas digitales Entrada de ajuste: I0.0 Entrada de reinicio: I0.1 Salidas digitales Salida Q: Q0.0 Salida Q^: Q0.1 Memoria M Bobina de relé 1: M0.0 Bobina de relé 2: M0.1 Diagrama de escalera del PLC para implementar el flip-flop SR Explicación del programa Para este programa de PLC, utilizamos el software de programación S7-300 PLC y TIA Portal. También podemos implementar esta lógica utilizando otros PLC. Red 1: Aquí utilizamos el contacto NC de la bobina de relé 1 (M0.0) de modo que cuando se presiona el botón de reinicio, la salida Q (Q0.0) está APAGADA. Red 2: Aquí usamos el contacto NC de la bobina de relé 2 (M0.1) de modo que cuando se presiona el botón de configuración, la salida Q^ (Q0.1) está APAGADA. Red 3: Aquí cuando presionamos el botón RESET (I0.0), la bobina de relé 1 (M0.0) se bloqueará. Red 4: Aquí cuando presionamos el botón SET (I0.1), la bobina de relé 2 (M0.1) se bloqueará. Si ambas entradas están bajas durante el encendido, la salida Q^ (Q0.1) se activará debido a su orden. Si ambas entradas están Nota: la aplicación anterior puede ser diferente de la aplicación real. Este ejemplo es solo para fines explicativos. También podemos implementar esta lógica en otros PLC. Este es el concepto simple de implementar la función de inversión de SR sin instrucciones. También podemos usar este concepto en otros ejemplos. Todos los parámetros considerados en el ejemplo son solo para fines explicativos, los parámetros pueden ser diferentes en aplicaciones reales. Resultado -
Programa de PLC para leer la temperatura en el PLC
leikang posted A plc and hmi article in Spanish in PLC programming learning
Este es un programa de PLC para leer la temperatura en el PLC. Aprenda a programar un PLC usando problemas de ejemplo y soluciones. Leer la temperatura en el PLC Descripción del problema Escriba un programa de PLC en el que podamos monitorear la temperatura actual. Aquí estamos usando un controlador de temperatura externo y su salida también está conectada al PLC para monitorear la temperatura del material en el tanque. Diagrama del problema Solución del problema RTD: dispositivos con resistencia que cambia con los cambios de temperatura de manera lineal. Este valor de resistencia cambiará a medida que cambie la temperatura y, al suministrar una corriente constante, la caída de voltaje medida a través de la resistencia se puede usar para determinar la nueva resistencia y, por lo tanto, la temperatura. Los RTD vienen en una variedad de tipos, siendo el tipo más común un PT100. Está hecho de platino que ha sido calibrado para ser de 100 ohmios a 0 grados C. En la aplicación anterior, queremos medir la temperatura del material del tanque, para eso usamos un sensor RTD que medirá la temperatura del tanque y enviará una señal al controlador de temperatura. El controlador de temperatura enviará una señal en forma de voltaje (0-10 V CC). Si el RTD detecta una temperatura de 0 grados, enviará 0 V CC y si detecta la temperatura máxima, enviará 10 V CC al PLC. El controlador de temperatura está conectado directamente al PLC, por lo que el PLC leerá el voltaje. Nota: – Aquí consideramos una aplicación simple para la explicación. Necesitamos medir la temperatura del material del tanque usando un sensor RTD. Y también consideramos otros componentes para fines de control. Supongamos que el rango de escala del controlador de temperatura es de 0 a 100 °C = 0 a 10 V CC y, de acuerdo con esta señal, el PLC considera de 0 a 27648. Lista de E/S Memoria M Valor analógico del controlador de temperatura: MW100 Valor real del controlador de temperatura: MD104 Multiplicación: MD108 Temperatura real en °C: MD112 Diagrama de escalera del PLC para leer la temperatura Explicación de la lógica del PLC Para esta aplicación, utilizamos el software de portal TIA y el PLC S7-300 para la programación. También podemos implementar esta lógica utilizando otros PLC. Red 1: En esta red, implementamos la lógica para la conversión de valores. Es necesario convertir el valor de INT a DINT para fines de multiplicación o cálculo. Entonces, al usar la instrucción de conversión, el valor analógico del RTD (MW100) se convierte en un valor analógico real (MD104). Nota: el controlador de temperatura proporciona una señal de 0 a 10 V CC al PLC. El convertidor ADC o el módulo de entrada analógica convertirán esta señal analógica en formato digital, y el rango de esta señal digital es de 0 a 27648. Este rango digital puede cambiar de un PLC a otro. Red 2: Tenemos el rango de temperatura del RTD que es de 0 a 100 grados C y el rango de voltaje de salida es de 0 a 10 V CC. Por lo tanto, necesitamos escalar esta salida de voltaje en términos de lectura de temperatura. Aquí, multiplique el valor según la ecuación y el valor final se almacenará en MD108. Nota: aquí, el controlador de temperatura y el rango de medición de temperatura son de 0 a 100 °C. Red 3: Ahora, para el resultado final, el valor multiplicado se divide por 27648, el resultado se almacenará en MD112 (temperatura real en °C). Nota: la aplicación anterior puede ser diferente de la aplicación real. Este ejemplo es solo para fines explicativos. También podemos implementar esta lógica en otros PLC. Este es el concepto simple de lectura de temperatura en un PLC S7-300; también podemos usar este concepto en otros ejemplos. Todos los parámetros considerados en el ejemplo son solo para fines explicativos; los parámetros pueden ser diferentes en aplicaciones reales. -
Programa de PLC para escalado de válvulas de control
leikang posted A plc and hmi article in Spanish in PLC programming learning
Este es un programa de PLC para implementar el escalado analógico en el PLC S7-300. Escalado de válvulas de control Descripción del problema Implementar el programa de PLC en S7-300 para el escalado analógico. Diagrama del problema Solución del problema Las entradas analógicas provienen de diferentes sensores o transmisores. Los transmisores convierten la cantidad física en señal eléctrica. Podemos medir muchas cantidades físicas utilizando sensores analógicos, como temperatura, presión, nivel, distancia, flujo, etc. Por supuesto, podemos medir todas las cantidades físicas utilizando sensores analógicos, pero a modo de ejemplo y explicación, aquí tomamos un ejemplo de válvula de control. Como se muestra en la figura, aquí consideramos una válvula de control y tiene una salida de 4-20 mA (retroalimentación de válvula) y una entrada de 4-20 mA (comando de válvula) para su funcionamiento. Por lo tanto, cuando el PLC le da 20 mA a la válvula de control de flujo, la válvula estará abierta al 100 % y para 4 mA estará al 0 % (cerrada). De otra manera, la válvula de control de flujo también proporciona una señal de salida que se puede utilizar para el sistema de bucle cerrado/para la indicación del porcentaje de la válvula. Si la válvula está abierta al 100 %, el PLC recibirá una señal de 20 mA y para el 0 % recibirá 4 mA. Nota: aquí consideramos el sistema de bucle cerrado para una explicación sencilla, por lo que el operador establecerá el parámetro de comando de apertura de la válvula de control en un rango entre 0 % y 100 %. Ahora, según el sistema de bucle cerrado, la válvula de control proporcionará una señal de salida (retroalimentación de la válvula) y, mediante el uso de la instrucción SCALE, el operador puede ver el parámetro de apertura real de la válvula en los gráficos. Lista de entradas/salidas Memoria M Habilitar comando-Escalado:- M0.0 Selección bipolar-Escalado:- M0.1 Valor actual del sensor o transmisor:- MW10 Palabra de error-Escalado:- MW12 Salida escalada:- MD20 Habilitar comando-Desescalado:- M1.0 Selección bipolar-Desescalado:- M0.2 Valor dado de la pantalla:- MD24 Palabra de error-Desescalado:- MW16 Salida sin escalar:- MW26 Diagrama de escalera de PLC para escalado de válvulas Explicación de la lógica de escalera Para esta aplicación, utilizamos el software de PLC S7-300 y TIA Portal para la programación. También podemos implementar esta lógica utilizando otros PLC. Red 1: En esta red, la lógica de escalado se ejecuta cuando el comando Habilitar (M0.0) está ACTIVADO. La instrucción “Escalar” sirve para convertir el entero (aquí, la señal de 4-20 mA de la válvula de control o MW10) en el parámetro IN que se puede escalar en unidades físicas entre un límite bajo (salida del 0 %) y un límite alto (salida del 100 %). El resultado o la salida escalada (MD20) de la instrucción se emite en el parámetro OUT. Si la selección bipolar (M0.1) está ACTIVADA, se supone que el valor en el parámetro IN es bipolar (rango entre -27648 y +27648). Si la selección bipolar (M0.1) está DESACTIVADA, se supone que el valor en el parámetro IN es unipolar (rango entre 0 y 27648). Red 2: La instrucción “Unscale” se utiliza para desescalar el número de punto flotante (valor dado en la pantalla o MD24) en el parámetro IN en unidades físicas entre un límite bajo y un límite alto. El resultado de la instrucción se emite (salida desescalada MW26) en el parámetro OUT. Si la selección bipolar (M0.2) está activada, se supone que el valor en el parámetro IN es bipolar (rango entre -27648 y +27648). Si la selección bipolar (M0.2) está desactivada, se supone que el valor en el parámetro IN es unipolar (rango entre 0 y 27648). Tabla de códigos de error: Nota: La aplicación anterior puede ser diferente de la aplicación real. Este ejemplo es solo para fines explicativos. También podemos implementar esta lógica en otros PLC. Este es el concepto simple de las instrucciones SCALE y UNSCALE, también podemos usar este concepto en otros ejemplos. Todos los parámetros considerados en el ejemplo se incluyen únicamente con fines explicativos; los parámetros pueden ser diferentes en las aplicaciones reales. Resultado -
Tutorial de diagrama de escalera de PLC para el control de nivel de tanques paralelos
leikang posted A plc and hmi article in Spanish in PLC programming learning
Este es un programa de PLC para controlar el nivel de tanques paralelos. Aprenda la programación de PLC usando este ejemplo. Control de nivel de tanques paralelos Descripción del problema Dos tanques están conectados en paralelo. Necesitamos calentar y enfriar el material entrante en los tanques y controlar simultáneamente el nivel de los tanques. Implemente el programa de PLC para esta aplicación. Diagrama del problema Solución del problema El proceso de calentamiento se utiliza para calentar el material en el tanque y el proceso de enfriamiento se utiliza para enfriar el material. Aquí, considere que ambos materiales son iguales como se muestra en la figura, la válvula de entrada alimenta material en ambos tanques. Aquí podemos usar interruptores de nivel para detectar los niveles bajos y altos para ambos tanques. Use dos sensores de temperatura para medir la temperatura de ambos tanques. Se utilizan válvulas de salida en la parte inferior de los tanques para drenar los materiales para su posterior procesamiento. Escribiremos un programa de PLC para esta aplicación. Lista de entradas y salidas Entradas digitales INICIO de ciclo: I0.0 PARADA de ciclo: I0.1 Nivel bajo del tanque 1 (LL1): I0.3 Nivel bajo del tanque 2 (LL2): I0.4 Nivel alto del tanque 1 (LH1): I0.5 Nivel alto del tanque 2 (LH2): I0.6 Salidas digitales Válvula de entrada V2 para tanque de calentamiento: Q0.0 Válvula de entrada V3 para tanque de enfriamiento: Q0.1 Válvula de salida V4 para tanque de calentamiento: Q0.2 Válvula de salida V5 para tanque de enfriamiento: Q0.3 Memoria M Bit de ENCENDIDO del ciclo: M0.0 Registro de temperatura del tanque de calentamiento: MD10 Registro de temperatura del tanque de enfriamiento: MD14 Válvula de salida V5 para tanque de enfriamiento: Q0.3 Programa de PLC para control de nivel de tanques paralelos Explicación del programa Para esta aplicación, utilizamos el PLC S7-300 y el software TIA Portal para la programación. También podemos implementar esta lógica utilizando otro PLC. Red 1: Esta red es para el circuito de enclavamiento. Siempre que se presione el botón de INICIO (I0.0), el bit de ENCENDIDO del ciclo (M0.0) estará ENCENDIDO. El ciclo se puede DETENER presionando el PB de DETENER (I0.1). Red 2: Cuando se detecta un nivel bajo del tanque de calentamiento (I0.3), la válvula de entrada V2 (Q0.0) estará ENCENDIDA. Si no se detecta un nivel alto en el tanque 1 (I0.5) y se presiona el botón de INICIO (I0.0), la válvula de entrada V2 (Q0.0) estará ENCENDIDA. Red 3: Si se detecta un nivel bajo en el tanque 2 (I0.4), la válvula de entrada V3 (Q0.1) estará ENCENDIDA. Si se presiona el botón de INICIO y no se detecta un nivel alto en el tanque 2 (I0.6), la válvula de entrada V3 (Q0.1) estará ENCENDIDA. Red 4: Si el ciclo está ENCENDIDO y la temperatura real del tanque de calentamiento (MD10) es mayor o igual que la temperatura establecida (70 °C), la válvula de salida V4 (Q0.2) estará ENCENDIDA Red 5: Si el ciclo está ENCENDIDO y la temperatura real del tanque de enfriamiento (MD14) es menor o igual que la temperatura establecida (20 °C), la válvula de salida V5 (Q0.3) estará ENCENDIDA. Nota: Este ejemplo es solo para fines explicativos. Podemos implementar esta lógica en cualquier PLC o mediante lógica de relé. La aplicación anterior puede ser diferente de la aplicación real o puede ser parte de la lógica de la planta. Resultado -
Programa PLC para la aplicación de mezcla automática de líquidos
leikang posted A plc and hmi article in Spanish in PLC programming learning
Cree un programa PLC para la aplicación de mezcla automática de líquidos utilizando programación de lógica de escalera. Estudie el proceso de mezcla utilizando un diagrama de escalera de PLC. Aplicación de mezcla de líquidos Descripción del problema En muchas industrias, se utilizan muchos sistemas de mezcla para mezclar soluciones. Algunas plantas utilizan automatización completa o semiautomatización. En un sistema manual, existen muchas desventajas, como falta de precisión, problemas de retardo de tiempo, pérdida de líquidos, consumo de tiempo, etc. Aquí estamos discutiendo la aplicación semiautomática de un sistema de mezcla. Diagrama Solución del problema Para este ejemplo, utilizamos programación PLC y para eso usamos el PLC Siemens S7-1200. Para una explicación sencilla, podemos considerar un ejemplo simple de sistema de mezcla como el que se muestra arriba. En esta aplicación, el operador puede preparar una solución pura sin mezclar utilizando los interruptores S1 y S2. Y el operador puede preparar una solución o material mezclado utilizando el interruptor S3. El operador observa el nivel del tanque y puede descargar el líquido dentro del tanque operando la válvula V5. Además, el motor del agitador M estará en funcionamiento mientras se llena el tanque. Proporcionaremos un sistema de interbloqueo para que el operador no pueda operar ambos interruptores al mismo tiempo. V1, V3 y V5 son válvulas manuales que no están conectadas al PLC. V2 y V4 son válvulas operadas electrónicamente que pueden ser controladas por el PLC. Lista de entradas y salidas del PLC Entradas digitales Hay tres interruptores S1, S2 y S3 S1: I0.0 S2: I0.1 S3: I0.3 Salidas digitales Tenemos dos válvulas V2 y V4. un motor agitador M1 V2: Q0.0 V4: Q0.1 M1: Q0.2 Diagrama de escalera de PLC para aplicación de mezcla automática de líquidos Explicación del programa de PLC Para esta aplicación, utilizamos el software de portal TIA y PLC S7-1200 para la programación. En la red 1, hemos tomado el contacto NO de S1 (I0.0) y el contacto NC de S2 (I0.1) y S3 (I0.2) en serie. Al activar el interruptor S1, el operador puede INICIAR la válvula V2 para la solución 1 (líquido 1). En la red 2, hemos tomado el contacto NO de S2 (I0.1) y el contacto NC de S1 (I0.0) y S3 (I0.2) en serie. Al activar el interruptor S2 (I0.1), el operador puede INICIAR la válvula V4 (Q0.1) para la solución 2 (líquido 2). Para las redes 1 y 2, hemos tomado una conexión en paralelo, contacto NO de S3 (I0.2) y en serie con contacto NC de S1 (I0.0) y S2 (I0.1). Debido a la conexión en paralelo anterior, el operador puede operar ambas válvulas activando el interruptor S3 (I0.2) para la solución mezclada (Líquido 1 y Líquido 2) Según nuestra condición, el agitador M1 (Q0.2) debe activarse automáticamente mientras se llena el tanque. Por lo tanto, hemos tomado el contacto NO de V2 (Q0.1) y en paralelo el contacto NO de V4 (Q0.1) para que el agitador se active automáticamente al operar cualquier interruptor. Casos de prueba en tiempo de ejecución Nota: La lógica de PLC anterior proporciona una idea básica sobre la aplicación de PLC en la aplicación de mezcla de líquidos. La lógica es limitada y no es una aplicación completa. -
Programa PLC para control secuencial de motores
leikang posted A plc and hmi article in Spanish in PLC programming learning
Este es el programa PLC para el sistema operativo de motores secuenciales. Control secuencial de motores Descripción del problema En muchas industrias, se utilizan muchos motores. A veces, necesitamos poner en marcha más de un motor en una aplicación. Cuando tenemos una potencia nominal de entrada baja, existe la posibilidad de que el MCB entrante se dispare cuando uno o más motores ARRANQUEN en paralelo porque consumirán más energía. Aquí consideraremos un ejemplo similar en el que ARRANCAMOS cada motor uno por uno. Diagrama del problema Solución del problema El problema se puede resolver mediante programación PLC o lógica de relé. En este caso, tenemos que operar motores secuencialmente. Hay un total de 3 motores que se deben controlar en una secuencia, de modo que cada motor arranque secuencialmente, por ejemplo, el motor 1 ARRANCA y, luego de una demora, el motor 2 arrancará y, luego de una demora, el motor 3 arrancará. De esta manera, toda la operación tardará 10 segundos en poner en marcha todos los motores en una secuencia. Al proporcionar este retraso, podemos evitar el problema de que los motores consuman mucha corriente durante el arranque inicial. Todos los motores funcionarán en la secuencia y se debe proporcionar un retraso de 5 segundos entre las operaciones de cada motor. Aquí se escribirá la lógica para la operación secuencial de los motores que utilizan PLC. Lista de entradas y salidas Lista de entradas PB de inicio: I0.0 PB de parada: I0.1 Lista de salidas Ciclo encendido: Q0.0 Motor 1: Q0.1 Motor 2: Q0.2 Motor 3: Q0.3 Diagrama de escalera de PLC para control de motor secuencial Explicación de la lógica de escalera En esta aplicación, utilizamos el PLC Siemens S7-1200 y el software TIA Portal para la programación. También podemos diseñar esta lógica con un circuito de relé. Red 1: En la Red 1, escribimos la lógica para la condición de ciclo ENCENDIDO. Aquí, la lámpara de ciclo ENCENDIDO (Q0.0) indicará el estado del ciclo. El ciclo se puede iniciar presionando el botón de INICIO PB (I0.0) y se puede detener presionando el botón de DETENER PB (I0.1). Cuando el ciclo esté ENCENDIDO, al mismo tiempo se iniciará el Motor 1 (Q0.1). Y al mismo tiempo, se ejecutará la instrucción del temporizador. Red 2: En la Red 2, el contacto NA del Motor 1 inicia el Temporizador T1 y cuando el Temporizador del Motor 2 (Q0.1) alcance el valor establecido de 5 segundos, el contacto NA del T1 ARRANCARÁ el Motor 2 (Q0.1). Red 3: En la Red 3, hemos tomado la lógica para el motor 3. Aquí hemos dado el contacto NO del motor 2 para iniciar el temporizador del motor 3. Cuando T2 alcance el valor establecido de 5 s, el contacto NO del T2 ARRANCARÁ el motor 3 (Q0.0). Cuando se presione STOP PB (I0.1), se activará el contacto NC, lo que hará que el ciclo (Q0.0) se APAGUE. Además, los motores 2 y 3 dejarán de funcionar. Casos de prueba en tiempo de ejecución Nota: La lógica de PLC anterior proporciona una idea básica sobre la aplicación de PLC en el control secuencial de motores. La lógica es limitada y no es una aplicación completa. -
Programa PLC para lógica de interruptor de dos vías
leikang posted A plc and hmi article in Spanish in PLC programming learning
Este es un programa PLC para lógica de interruptor de dos vías para luz de escalera en casa Lógica de interruptor de dos vías de PLC En una casa tipo dúplex hay planta baja y primer piso y, a veces, también segundo piso. A veces, las personas necesitan ir de la planta baja al primer piso o del primer piso a la planta baja mediante la escalera provista en la casa. Pero en la escalera no hay luz solar, por lo que las personas necesitan una lámpara/luz para ver los escalones de la escalera fácilmente. Aquí estamos usando un PLC simple para controlar esta lámpara usando dos interruptores, un interruptor en la planta baja y un segundo interruptor en el primer piso para controlar una lámpara como se muestra en la siguiente figura. Nota: también podemos construir el circuito usando relés/interruptores simples. Este artículo solo sirve para comprender el concepto básico del interruptor de dos vías usando una lógica de escalera de PLC. Imagen Solución Resolveremos este problema mediante una automatización simple. Como se muestra en la figura, considere una casa simple con un piso y una escalera en la casa. Aquí configuraremos el sistema de iluminación para que los usuarios enciendan o apaguen la luz, ya sea que estén en la parte inferior o superior de la escalera. Proporcionaremos un interruptor independiente para cada piso, como se muestra en la figura anterior. Requisitos de E/S del PLC Entradas digitales SW1: I0.1 SW2: I0.2 Salidas digitales Lámpara: Q0.0 Programa de PLC para interruptor de dos vías Explicación del programa Para esta aplicación, utilizamos el software de programación TIA Portal y el PLC S7-1200. En el programa anterior, hemos agregado dos contactos NO de SW 1 (I0.1) y SW 2 (I0.2) en serie y contactos NC de SW1 (I0.1) y SW2 (I0.2) en paralelo de esta serie de contactos NO SW1 y SW2. Si el estado del interruptor inferior (SW1) y el estado del interruptor superior (SW2) son iguales, la lámpara estará ENCENDIDA. Y si el estado del interruptor superior o inferior es diferente del otro, la lámpara (Q0.0) estará APAGADA. Cuando la lámpara (Q0.0) está APAGADA, el usuario puede ENCENDERLA cambiando el estado de cualquier interruptor. También puede APAGAR la lámpara cambiando el estado de uno de los dos interruptores. Resultado Nota: La lógica del PLC anterior proporciona una idea básica sobre la aplicación del PLC para la lógica del interruptor de dos vías. La lógica es limitada y no es una aplicación completa. -
El PLC activa o desactiva las salidas en función de los eventos
leikang posted A plc and hmi article in Spanish in PLC programming learning
Escriba el siguiente programa de PLC para activar o desactivar las salidas en función de los eventos. Un interruptor determinado (I:1/0) debe iniciar un proceso. El proceso debe ejecutarse durante 30 segundos, detenerse durante 10 segundos y luego repetirse mientras el interruptor I:1/0 permanezca cerrado. Abrir I:1/0 en cualquier momento es para restablecer todos los temporizadores y desactivar todas las salidas. La salida O:2/0 debe activarse durante el período de ejecución de 30 segundos y la salida O:2/1 debe activarse durante el período de detención de 10 segundos. Durante el período de ejecución, una sola salida O:2/2 es controlada por la entrada I:1/1. Si I:1/1 está abierto (al comienzo del período de ejecución), O:2/2 debe estar apagado durante los primeros 5 segundos y luego encendido durante 10 segundos. Si I:1/1 está cerrado (al comienzo del período de ejecución), O:2/2 debe estar apagado durante los primeros 10 segundos y luego encendido durante 15 segundos. Cambiar I:1/1 después de que haya comenzado el período de ejecución no debería cambiar la secuencia anterior. La salida O:2/2 siempre debe estar apagada durante el período de detención. Activación o desactivación de salidas del PLC -
Programa PLC para la lógica de control del nivel de agua
leikang posted A plc and hmi article in Spanish in PLC programming learning
Diseñe un programa PLC para controlar el nivel de un tanque de almacenamiento de agua encendiendo y apagando una bomba de descarga según los niveles bajo y alto. Programa PLC para el control del nivel de agua Descripción de la lógica Automático: si se selecciona el modo automático en el panel de control local, la bomba se controlará de forma lógica según el interruptor de nivel bajo y el interruptor de nivel alto. Manual: si se selecciona el modo manual en el panel de control local, independientemente del estado del interruptor de nivel bajo y el interruptor de nivel alto, la bomba se controlará manualmente mediante el botón de encendido/apagado en el panel de control local. Cuando el nivel del agua alcanza el nivel bajo, la bomba se detiene. Si el nivel del agua alcanza el punto alto, la bomba se pone en marcha para que se pueda drenar el agua y, por lo tanto, bajar el nivel. Panel de indicación: este panel contiene LED para mostrar el estado del control del nivel de agua. Tiene señales de bomba en funcionamiento, nivel bajo y nivel alto. Si la bomba está en funcionamiento, la luz de estado de bomba en funcionamiento estará encendida. Entonces, si se activa el interruptor de nivel bajo, la luz de estado de nivel bajo se encenderá. Si se activa el interruptor de nivel alto, la luz de estado de nivel alto se encenderá. Lógica de escalera del PLC Modo manual seleccionado, posición OFF y agua en nivel bajo Modo manual seleccionado y agua entre niveles bajo y alto Modo automático seleccionado e interruptor de nivel alto activado -
Programa PLC para la operación de llenado continuo
leikang posted A plc and hmi article in Spanish in PLC programming learning
Programa PLC: Una operación de llenado continuo requiere que las cajas que se mueven sobre un transportador se posicionen y llenen automáticamente. Programa PLC para la operación de llenado continuo Propósito Solenoide: Para controlar el llenado de producto desde la tolva. El solenoide se activará después de posicionar la caja (activación del interruptor de proximidad) y se desactivará nuevamente después de que se active el interruptor de nivel (nivel lleno). Interruptor de nivel: Para detectar el nivel de producto en la caja de llenado. Interruptor de proximidad: Para posicionar la caja exactamente debajo de la tolva. Motor: Para hacer funcionar el transportador de manera que la caja se mueva en consecuencia. Panel de control local: Tiene botones de INICIO y DETENCIÓN que se utilizan para controlar la secuencia. Panel de indicación: Muestra el estado de la planta/lote. Las señales de estado son Ejecutar/En espera/Lleno. Lógica PLC Las siguientes son las posiciones predeterminadas: Interruptor de PARADA: normalmente cerrado (NC) Interruptor de INICIO: normalmente abierto (NO) Interruptor de proximidad: normalmente abierto (NO) Interruptor de nivel: normalmente abierto (NO) Nota: En la lógica de escalera podemos usar contactos NO o NC como predeterminados de interruptor de proximidad y nivel según sea necesario. Si usamos NO, se convierte en NC después de activar el interruptor. Si usamos NC, se convierte en NO después de activar el interruptor. Explicación Aquí tenemos 5 peldaños/líneas completas en la lógica de escalera anterior. Primer peldaño: Tiene indicación de PARADA, INICIO y FUNCIONAMIENTO. La PARADA predeterminada es NC, INICIO es NO, cuando presionamos el comando INICIO, tanto PARADA como INICIO son NC, por lo que se activará la salida FUNCIONAMIENTO. La indicación FUNCIONAMIENTO se mostrará en el panel de indicación. Como INICIO es un botón pulsador que genera solo un comando momentáneo. Entonces, usamos un contacto NO lógico de la salida RUN. Cuando se activa RUN, el NO se convierte en NC y retiene/enclava el comando START y RUN se activará continuamente aunque se pierda la señal START, ya que es de tipo momentáneo. Segundo peldaño: Se usa para indicar el estado de la señal STAND BY en el panel indicador. El contacto NC de indicación RUN está conectado a STANDBY. Entonces, cuando se activa la señal RUN o se inicia el proceso, NC se convierte en NO y la indicación STAND BY se deshabilitará. Si no está en funcionamiento, se activará el modo stand by. Tercer peldaño: Se usa para indicar el estado de la señal FULL en el panel indicador. Cuando se activan el interruptor de nivel y el interruptor de proximidad, los contactos NO se convertirán en NC y se habilitará el estado de la señal FULL. Cuarto peldaño: Se usa para controlar el motor, ya sea START/STOP. El contacto NC del interruptor de proximidad se usa aquí y el contacto NO de la señal RUN se usa para controlar el motor. Entonces, cuando presionamos el botón START (INICIO), se activará RUN (como se explicó en el primer escalón), por lo que el contacto NO de la señal RUN se convertirá en NC. Las señales de proximidad y RUN están habilitadas/en buen estado, luego el motor se pondrá en marcha, el transportador comenzará a funcionar y la caja/paquete comenzará a moverse. Una vez que la caja llega antes que Hooper, se activará el interruptor de proximidad. Por lo tanto, el contacto NC del interruptor de proximidad se convierte en NO, por lo que el motor se detendrá inmediatamente. Después del llenado, la caja debe moverse nuevamente y llegar al otro lado. Por lo tanto, aquí usamos el contacto NO del interruptor de nivel a través del interruptor de proximidad. Cuando se completa el llenado, el contacto del interruptor de nivel cambia de NO a NC, por lo que nuevamente el motor se pone en marcha y mueve la caja al otro extremo. Quinto escalón: Se usa para controlar el funcionamiento de la válvula solenoide. Si el solenoide se activa, comienza a llenar la caja y si la válvula solenoide se desactiva, se detendrá el llenado. Aquí usamos principalmente el contacto NO de la señal RUN, el contacto NC del interruptor de nivel y el contacto NO de proximidad para controlar la válvula solenoide. La válvula solenoide se activará cuando se dé el comando de INICIO (el contacto NO de la señal de MARCHA se convierte en NC), cuando el nivel sea cero (aquí se utiliza el contacto NC del interruptor de nivel como predeterminado), cuando la caja se coloque debajo de la tolva (se utiliza el contacto NO del interruptor de proximidad. De modo que cuando la caja llegue debajo de la tolva, el contacto NO se convierte en NC). Una vez que todos los parámetros lógicos estén en orden, se activará la válvula solenoide y comenzará el llenado. Si el nivel alcanza el 100 %, el interruptor de nivel se convertirá en NO y, por lo tanto, se detendrá el llenado desactivando la válvula solenoide. Aquí utilizamos el interruptor de proximidad porque el llenado debe iniciarse cuando la caja se coloca en la posición correcta. Después de llenar, la caja se retira y el llenado comenzará nuevamente cuando la siguiente caja llegue debajo de la tolva. -
Lógica de escalera del motor de la cinta transportadora PLC
leikang posted A plc and hmi article in Spanish in PLC programming learning
Tutoriales de programación de PLC para lógica de escalera del motor de la cinta transportadora PLC o control de la cinta transportadora mediante un controlador lógico programable (PLC). Lógica de escalera del motor de la cinta transportadora PLC Objetivo: Las tareas secuenciales son las siguientes Cuando se presiona el botón START Se iniciará el motor Se activará la luz indicadora RUN (luz verde) El motor está en funcionamiento, por lo que la caja comenzará a moverse El sensor de proximidad detectará cuando la caja llegue al otro extremo Se detendrá el motor Se desactivará la luz indicadora RUN (luz verde) Se activará la luz indicadora STOP (luz roja) Se utilizará un botón pulsador de parada de emergencia para detener el motor en cualquier momento. Esquema de relé R : Lámpara indicadora de PARADA, G : Lámpara indicadora de MARCHA, M : Motor, OL : Relé de sobrecarga (Relé de protección del motor), LS1 : Interruptor de proximidad, PB1 : Botón pulsador de arranque, PB2 : Botón pulsador de parada de emergencia, CR : Relé de contactor Secuencia operativa Se activa el botón de arranque. CR1-1 se cierra para sellar CR1 o para bloquear el comando de inicio CR1-2 se abre, apagando la luz piloto roja de parada CR1-3 se cierra, enciende la luz piloto verde de marcha CR1-4 se cierra para energizar el arrancador del motor y el motor La caja/paquete se mueve y el interruptor de proximidad (LS1) detecta la caja cuando llegó y desenergiza la bobina CR1 CR1-1 se abre para abrir el contacto de sellado (comando de inicio desbloqueado) CR1-2 se cierra, enciende la luz piloto roja CR1-3 se abre, apaga la luz piloto verde CR1-4 se abre para desenergizar la bobina de arranque, detener el motor y finalizar la secuencia Lógica de escalera de PLC -
Cómo lee el PLC los datos de los transmisores de campo
leikang posted A plc and hmi article in Spanish in PLC programming learning
La instrumentación y el control se basan en la conversión de variables físicas o de proceso a un formato más útil para la pantalla del operador. La presión en una tubería se convierte en deflexión mecánica de un diafragma, que se convierte en energía eléctrica mediante un extensómetro (el diafragma y el extensómetro constituyen un transductor), luego en un valor entero numérico mediante un módulo de E/S y luego en un valor de unidad de ingeniería de punto flotante mediante el PLC o la HMI para su visualización. Esta información también se utiliza para ayudar a generar comandos de salida, que se convierten en señales eléctricas y luego en acción mecánica. El truco es comprender las relaciones de E/S de los distintos convertidores. Cómo lee el PLC los datos de los transmisores de campo Por ejemplo, un orificio de flujo provocará una caída de presión predecible a medida que los fluidos fluyen a través de él. Un transmisor de presión puede medir esta caída de presión comparando la presión aguas arriba con la presión aguas abajo. Aunque esta diferencia de presión no es lineal con el caudal, tiene una relación repetible con él. Esta relación se aproxima mejor como una función de raíz cuadrada. Tomar la raíz cuadrada de la señal de presión diferencial la linealiza efectivamente con el caudal. Una vez que se ha establecido una relación lineal, se puede deducir toda la secuencia de conversión del transmisor a la pantalla de la computadora a partir de una medición. La siguiente figura muestra dos circuitos típicos de medición de temperatura de la siguiente manera: La configuración superior utiliza la fuente de alimentación externa del transmisor para alimentar el bucle de señal. Esta configuración se conoce como bucle de cuatro cables. La configuración inferior utiliza una fuente de alimentación interna (alimentación de tarjeta AI) para alimentar el bucle. Esta configuración se conoce como bucle de dos cables. La siguiente discusión sobre las conversiones de unidades se aplica a ambos tipos de circuitos. Concéntrese en el circuito superior. Un termopar es el elemento sensor. Los termopares son dispositivos que utilizan el principio de contacto bimetálico para generar una pequeña señal de milivoltios. Tenga en cuenta que la curva de temperatura-voltaje que se presenta en el gráfico es relativamente lineal en todo el intervalo de temperatura. Fuera de ese intervalo de temperatura, la señal puede volverse menos lineal (una característica de un termopar), pero eso no tiene importancia aquí. El escalado del instrumento siempre debe comenzar en la medición del proceso. El diseñador consulta la hoja de balance de calor y materia (HMB) para nuestro sistema imaginario y descubre que la temperatura esperada en el punto de medición es de aproximadamente 105 °C. El calentador aguas arriba es capaz de calentar el sistema a aproximadamente 130 °C antes de que se apague debido a su enclavamiento por sobretemperatura. El ingeniero de diseño sabe que un intervalo calibrado correctamente colocaría el punto de funcionamiento normal aproximadamente en la mitad de la curva. El extremo superior tendría que estar por encima de los 130 °C. Después de pensarlo un poco, el ingeniero decide utilizar un intervalo de calibración de 15 a 150 °C y elige un termopar tipo K, que proporciona una salida de 0,597 a 6,138 mV en ese intervalo de temperatura. El transmisor de temperatura, entonces, debe calibrarse en banco para proporcionar una señal de salida de 4 a 20 mA que sea proporcional a la señal de entrada de 0,597 a 6,138 mV esperada del termopar. El transmisor, al ser una fuente de corriente (a diferencia de una fuente de voltaje), varía su salida de potencia según sea necesario para mantener una salida de miliamperios constante que sea proporcional a los milivoltios en su entrada, es decir, la lectura de temperatura medida. (Nota: una fuente de voltaje, como una batería, intenta mantener un voltaje constante independientemente de la carga, mientras que una fuente de corriente intenta mantener una corriente constante independientemente de la carga). El transmisor de temperatura convierte entonces esta señal en una señal de 4-20 mA que ha sido escalada, en este caso para un rango de 15 a –150 °C. El PLC tiene un módulo de entrada analógica que detecta la salida del transmisor de temperatura. Prácticamente todos los módulos de entrada analógica son voltímetros, aunque se los incluya como entradas de miliamperios. A veces, la resistencia es externa en la regleta de terminales y, a veces, es interna en el módulo de E/S del PLC (que se muestra en la Figura). En cualquier caso, la señal de 4-20 mA se convertirá en un voltaje. Normalmente, este voltaje es de 1-5 VCC porque la resistencia utilizada es de 250 ohmios. Este valor analógico debe convertirse entonces en un valor binario. En nuestro ejemplo, la especificación del PLC indica que este módulo de E/S del PLC en particular tiene una resolución de 12 bits. Para encontrar la resolución del módulo en términos de la variable de proceso, realice una conversión binaria: 212 = 4095. Por lo tanto, para un intervalo de entrada de 1 a 5 VCC, el módulo de E/S del PLC proporciona un valor entero al programa del PLC que va de 0 a 4095. El programa del PLC puede obtener estos datos para utilizarlos según sea necesario. Una de las posibles acciones del programa del PLC es mover este valor de datos a un búfer de interfaz de red (una serie de ubicaciones contiguas en la memoria del PLC) para su transmisión a la HMI. El valor entero de conteo sin procesar se pone a disposición para la transmisión de datos a través de la red. La HMI recibe este flujo de datos transmitidos, que luego se almacena en un búfer de datos de entrada. La computadora HMI tiene una base de datos de archivo de etiquetas, que contiene instrucciones sobre cómo manipular cada elemento de datos para su presentación al operador. Muchas de las etiquetas en el archivo de etiquetas están vinculadas a elementos de datos en el búfer de datos de entrada. Una de esas etiquetas está vinculada a esta ubicación en particular. El valor sin procesar de 0 a 4095 se extrae y se convierte a unidades de ingeniería mediante el uso de la fórmula incorporada en la base de datos del archivo de etiquetas o en el software de pantalla gráfica que utiliza la información. La fórmula en nuestro caso de muestra se muestra en la siguiente figura. El valor producido (85,88) sería el valor que se muestra al operador en oC como se muestra a continuación en las siguientes figuras: -
Control de semáforos mediante lógica de escalera de PLC
leikang posted A plc and hmi article in Spanish in PLC programming learning
En nuestra ciudad, nos encontramos con un atasco de tráfico de tres vías con mucha frecuencia. Este programa de PLC ofrece la solución para controlar los atascos de tráfico pesados mediante el control de lógica programable. Control de semáforos mediante PLC Solución del problema Hay muchas formas de escribir un programa para el control de semáforos, por ejemplo, el método de salida del secuenciador, pero en este caso normal se utilizan entradas, salidas y temporizadores. Los temporizadores se utilizan para dar un retraso de tiempo para que la salida se active y desactive. La bobina de reinicio se utiliza al final para ejecutar el programa de forma continua. Los bloques comparadores se utilizan para reducir la cantidad de temporizadores utilizados. Programa realizado en el software AB RSLogix 500. Lista de entradas y salidas para el sistema de control de tráfico Programa de PLC para sistema de control de tráfico de 3 vías La siguiente columna tabular proporciona los pasos o la secuencia de salidas para activar. Descripción de la lógica de PLC para sistema de control de tráfico de 3 vías RUNG000: Este es un peldaño de enclavamiento para operar el sistema a través del PB de inicio y parada maestro. RUNG001 y RUNG0002: Iniciar el temporizador para activar la primera salida verde oeste, de modo que este y oeste deben estar en rojo. Los comparadores en el peldaño paralelo se utilizan para desactivar la roja este después de 15 segundos. El bit de temporización del temporizador T4:2 en contacto paralelo se utiliza para activar nuevamente la roja este en el quinto y sexto paso. (Consulte la columna de la tabla anterior para obtener más información) RUNG 0003: Activación de la luz roja del norte hasta el tercer paso mediante el bit de temporización del temporizador y los bloques comparadores de T4:0 y T4:1. Rung 0004: Activación de la luz amarilla del este durante 5 segundos mediante bloques comparadores. (Paso 2.º) Rung 0005-0006-0007-0008-0009-0010: Se siguen los mismos procedimientos para activar otras salidas. (Consulte la columna de la tabla para obtener una secuencia de operaciones) RUNG 0011: Se activa la bobina de reinicio mediante el bit de finalización de T4:2 para reiniciar el ciclo desde el principio El programa se ejecuta de forma continua hasta que se presiona el botón STOP PB Conclusión: El control de semáforo de 3 formas explicado anteriormente mediante PLC es solo un ejemplo. Puede variar con respecto al tiempo real. Podemos utilizar este programa de ejemplo para comprender el funcionamiento de los temporizadores y la función del bloque comparador en el PLC AB. -
Técnicas de cableado de señales digitales de PLC
leikang posted A plc and hmi article in Spanish in PLC programming learning
En una planta de proceso, el control de encendido/apagado se realiza a través del PLC o DCS. La siguiente figura es una descripción general de un circuito discreto/digital (encendido/apagado), que muestra todo el proceso desde la fuente de alimentación a través del sensor y hasta el PLC. Técnicas de cableado de señales digitales de PLC En la figura anterior, se monta un interruptor de nivel en un recipiente. El interruptor es monitoreado por un módulo de entrada digital de PLC. El circuito se alimenta a través de un disyuntor (CB2) en un panel de alimentación de instrumentos. La alimentación principal se lleva a un panel de clasificación, donde la energía se divide, alimentando múltiples circuitos con fusibles. El fusible 03FU es el fusible de desconexión principal, mientras que los fusibles restantes son fusibles de distribución. El fusible 06FU alimenta nuestro circuito. El cable activo (eléctricamente vivo) 06A se pasa a la caja de conexiones de campo (FJB) como un cable en un cable multiconductor. Este cable, a veces llamado cable principal o cable de conexión, se conecta en la caja de conexiones de campo (FJB), donde, en este ejemplo, se alimentan dos cables de par trenzado sin blindaje al dispositivo final, LSH-47. Esto deja un conductor de repuesto. El cable activo 06A llega al terminal + del contacto de forma A y se conecta al terminal H para activar la electrónica del interruptor de nivel. El número de cable cambia a través del contacto de relé a 06B. Este cable envía la señal de regreso a la FJB, donde la señal se pasa de regreso al gabinete de terminación a través del cable de conexión de múltiples conductores. Allí, la señal y el neutro se emparejan y pasan al módulo PLC. Tenga en cuenta que el cable neutro de retorno, etiquetado 02N (ya que es el cable de retorno para CB2), se divide hacia el PLC y el interruptor de nivel. NOTA: Siempre es recomendable utilizar un cable de par trenzado cuando se conecta a un sistema PLC. Los cables de par trenzado presentan una excelente inmunidad al ruido, lo que resulta particularmente útil cuando se conectan a cargas de alta impedancia, como las que se encuentran en los módulos de E/S de PLC/DCS. Una carga de alta impedancia puede ser particularmente sensible al ruido, ya que la corriente que la acompaña es muy baja y la cantidad de trabajo real que se realiza es mínima. Eso es todo, en pocas palabras. A continuación, se incluye un comentario sobre los problemas de conectividad relacionados con el cableado de señales de PLC/DCS. a. Sumidero y fuente Los términos sumidero y fuente se utilizan para describir la forma en que un componente particular del circuito se relaciona con el flujo de energía. Estos términos en realidad provienen de la época de la lógica de transistores. Se puede pensar en un transistor como un simple interruptor para esta discusión (Figura siguiente). DC (+) es el terminal positivo de CC, DCC es CC común Este tipo de transistor requiere una pequeña resistencia en su colector (el lado superior) para limitar la corriente. En el ejemplo del caso 1, la resistencia está en su lugar, con la carga mostrada en serie con el emisor del transistor. Cuando el transistor conduce, la corriente fluye a través de la resistencia, el transistor y luego a través de la carga. Este circuito no se usó mucho porque la corriente se divide a través del circuito interno, dejando menos energía disponible para impulsar la carga y elevando las temperaturas en el módulo de E/S. Caso 2 Esto proporciona un circuito de fuente más típico, donde la salida del PLC, al apagarse, cambia la corriente de carga completa para impulsar la carga. Cuando la salida se enciende, el transistor conduce, lo que hace que la mayor parte de la corriente se desvíe a través de él, privando a la carga y, por lo tanto, desenergizándola. La desventaja de esta configuración es que seguirá habiendo una pequeña corriente de fuga a través de la carga, ya que una cierta cantidad de corriente seguirá dirigiéndose a través de la carga, aunque no lo suficiente, por lo general, para hacer que la carga permanezca energizada. Sin embargo, al solucionar problemas, se detectará un pequeño voltaje a través de una carga desenergizada. En el ejemplo del Caso 3, la carga es la resistencia del colector. Cuando el transistor conduce, la carga se energiza. Desde el punto de vista de la electrónica de la placa, esta es una mejor configuración porque la mayor parte del calor se disipa por la carga. La desventaja de esta configuración es que “cambiar el neutro” es contra-intuitivo y puede ser inseguro, ya que el voltaje completo está presente tanto en los terminales positivo como negativo de la carga cuando se desenergiza. Por estas razones, el Caso 2 ha evolucionado hasta convertirse en la configuración de salida más común. Este concepto de sumidero/fuente se puede extender a cualquier circuito. b. Protección del circuito (fusible) La mayoría de los módulos de E/S tienen fusibles internos. Sin embargo, eso no significa mucho para el usuario. Si bien el fusible interno limita el daño al módulo en sí, en la mayoría de los casos el módulo aún debe enviarse a la fábrica para su reparación. Por lo tanto, el resultado final es el mismo para el usuario: un módulo roto. Como resultado, es una buena práctica agregar fusibles externos a cada punto de E/S, con una capacidad nominal apenas inferior a la capacidad nominal del fusible en la placa de circuito del módulo. Si bien esto limita el tamaño de la carga que puede ser accionada directamente por el módulo, el fusible interno y el módulo están protegidos. Precaución: Si las salidas discretas con fusibles internos están integradas en cadenas de interbloqueo, o si están en circuitos que dependen de contactos normalmente cerrados para iniciar acciones de seguridad, se debe utilizar otro tipo de módulo que no esté fusionado. O se pueden implementar relés de interposición. Es posible que el punto de E/S funcione normalmente (por ejemplo, cerrar sus contactos e informar al programa que los ha cerrado) pero que aún así no pase energía debido a un fusible interno fundido. c. Circuitos de entrada digital (DI) Los módulos de entrada digital (DI) escanean continuamente sus puntos de entrada para detectar la presencia o ausencia de voltaje. Si hay voltaje, se escribe un 1 en una ubicación de memoria. Si no hay voltaje, se escribe un 0 allí. El tipo y la magnitud del voltaje requeridos son dos de los factores que distinguen un módulo DI de otro. La mayoría de los puntos DI tienen una alta impedancia, lo que minimiza la cantidad de corriente absorbida y, por lo tanto, tienen un efecto relativamente menor en el sistema de distribución de energía. Cada punto de entrada digital puede considerarse como una lámpara, que está encendida o apagada. Los módulos DI pueden estar aislados eléctricamente punto a punto, o pueden agruparse conectando internamente el común de E/S. La mayoría de los módulos actuales están agrupados, ya que la agrupación permite una mayor densidad. Como hemos visto, las densidades de puntos de hasta 32 puntos por módulo son comunes en la configuración agrupada. La siguiente figura muestra dos módulos DI diferentes. El primer módulo conecta internamente el lado CC(+) del circuito. El punto de E/S luego pasa energía al dispositivo de campo. Este tipo de módulo se denomina módulo de suministro. Esta configuración es inusual. La conmutación del lado común en el campo normalmente no se realiza. Si el módulo conecta internamente el lado común de CC del circuito, entonces el módulo se considera un módulo de sumidero. El punto de E/S completa la ruta al común de CC. Esta configuración se utiliza en la gran mayoría de los casos porque permite que cada punto de E/S se fusione individualmente cerca de la fuente de alimentación antes de que la energía se distribuya al dispositivo de campo. En cualquier caso, la corriente fluye en la misma dirección a través del interruptor montado en el campo. d. Circuitos de salida digital (DO) Los contactos de relé se consideran dispositivos de salida porque obligan a otros dispositivos a reaccionar cuando cambian de estado. Las salidas digitales de PLC pueden considerarse como contactos de relé. En muchos casos, eso es simplemente lo que son. En otros, el elemento de conmutación puede ser un dispositivo de estado sólido de algún tipo. Incluso en ese caso, la analogía del relé funciona siempre que el diseñador recuerde considerar la corriente de fuga. Los módulos DO encienden y apagan el voltaje para hacer que un dispositivo externo cambie de estado. Estos módulos son "aislados" o "no aislados". Si un módulo no está aislado, entonces es de sumidero o de fuente. 1. Circuitos DO aislados Un circuito DO aislado es uno en el que la fuente de energía se puede aislar entre puntos de E/S. La fuente no está conectada a un bus interno. El costo es de dos terminales por punto, por lo que es caro. Hay tres fuentes de energía mojada, con los puntos 1, 2, 4, 5 y 6 aislados del punto 3 y los puntos 7 y 8. En este ejemplo, se alimenta CA al punto 3, mientras que las señales CC están en los puntos restantes. Hacer esto demuestra las posibilidades. En la práctica, es una buena idea separar las señales CA y CC si es posible. 2. Circuitos DO no aislados Al igual que con el módulo PLC DI, la densidad de puntos es una característica importante de los módulos DO. Como se puede ver en el módulo aislado en la Figura, el aislamiento tiene un precio. Un módulo de 16 terminales tiene una densidad de puntos de solo ocho, ya que se necesitan dos terminales por punto. Al conectar internamente un común, la densidad de puntos se puede mejorar drásticamente. Sin embargo, el resultado es un módulo no aislado que impone límites al diseñador. Las fuentes de energía deben administrarse. En la mayoría de los casos, esto no es un problema, ya que es posible extender la alimentación de E/S del PLC al dispositivo de campo. Sin embargo, si un dispositivo de campo debe generar su propia señal, se debe agregar un relé de interposición al circuito para proporcionar aislamiento. La figura anterior muestra dos módulos de salida digital diferentes. El primero conecta internamente el lado CC(+) del circuito. El punto de E/S proporciona una ruta a la alimentación, lo que lo convierte en un módulo de suministro. Si el módulo conecta el lado común de CC del circuito, como se muestra en la figura anterior, ejemplo 1, entonces el módulo se considera un módulo de sumidero. El punto de E/S completa la ruta al común. Este tipo de módulo rara vez se usa hoy en día debido a la conmutación del lado común. El ejemplo 2 es mucho más común, ya que coloca la acción de conmutación por delante de la carga en términos de flujo de corriente. -
Técnicas de cableado de señales analógicas de PLC
leikang posted A plc and hmi article in Spanish in PLC programming learning
A diferencia del circuito discreto/digital (encendido/apagado), las señales analógicas varían en un rango de voltaje o corriente. Tomando el mismo recipiente descrito anteriormente en el ejemplo de cableado digital, ¿cómo cambiaría el cableado si reemplazamos el interruptor con un transmisor de nivel? Técnicas de cableado de señales analógicas de PLC La siguiente figura tiene el mismo panel de disyuntores, pero ahora está alimentando una fuente de alimentación de CC. La fuente de alimentación podría estar en su propio gabinete o podría estar en el panel de maniobras. En cualquier caso, la alimentación de CC se distribuye en el panel de maniobras. Un solo fusible podría alimentar varios circuitos, o cada circuito podría estar fusionado. El transmisor se alimenta con +24 VCC en su terminal positivo. La señal de corriente de 4–20 mA se obtiene del terminal (-) del transmisor al PLC. El cableado es de par trenzado y blindado. El cable de señal está numerado con el número del transmisor y los cables en el interior están numerados para proporcionar información sobre la fuente de alimentación. El blindaje se termina en el panel de maniobras, donde se reúnen todos los blindajes y se terminan en una terminal de tierra que está aislada del gabinete. Nota: Se debe tener cuidado para garantizar que el blindaje solo esté conectado a tierra en un punto. Los blindajes que están conectados a tierra en más de un punto pueden inyectar grandes picos de ruido en la señal. Esta condición se denomina bucle de tierra y puede ser un problema muy difícil de aislar, ya que el problema es intermitente. Se debe utilizar una conexión a tierra "silenciosa" para conectar a tierra todos los blindajes en un punto. Una conexión a tierra silenciosa es aquella que está conectada a una tríada de tierra dedicada o a la toma central de un transformador de aislamiento. Una conexión a tierra ruidosa sería aquella que está ubicada físicamente lejos del transformador y que da servicio a motores, luces u otros elementos ruidosos. Ese es el circuito de entrada analógica básica de dos cables. A continuación, se incluye información específica sobre las distintas posibilidades analógicas: a. Protección del circuito (fusibles) Los circuitos analógicos siempre son de bajo voltaje, generalmente 24 VCC. Como resultado, no es necesario fusionar circuitos analógicos individuales para la seguridad del personal. Además, la mayoría de los módulos de E/S analógicos tienen circuitos limitadores de corriente integrados. Por lo tanto, generalmente no es necesario fusionar para proteger los módulos. Si se cumplen estas dos condiciones (y el diseñador debe confirmarlo con el fabricante), se puede evitar la fusión por punto si se desea. Si un diseñador desea ahorrar dinero al no fusionar cada punto, se debe considerar la posibilidad de agrupar los circuitos en zonas de control de daños. Por ejemplo, si hay un par de bombas, una principal y una de respaldo, los instrumentos para las dos deben estar en grupos de fusibles separados para evitar que un solo fusible fundido las destruya a ambas. Para obtener más información, consulte Particiones de E/S en el índice. b. Inmunidad al ruido Los circuitos analógicos son susceptibles al ruido electrónico. Si, por ejemplo, un cable analógico se encuentra junto al cable de alto voltaje de un motor, entonces el cable de señal analógica actuará como una antena, captando el ruido acoplado magnéticamente generado por el motor. Existen otras fuentes de ruido, como la radiación de radiofrecuencia (RF) de un walkie-talkie. El ruido en un cable de señal analógica puede provocar errores en la lectura del valor de la señal, lo que a su vez puede causar una multitud de problemas en el sistema de control. Algunas formas de mitigar el ruido incluyen: • Cables de par trenzado: El ruido electrónico se puede reducir en gran medida mediante el uso de cableado de par trenzado. La mayoría de los instrumentos utilizan dos cables para transmitir sus señales. La corriente fluye hacia el dispositivo en un cable y regresa desde el dispositivo en el otro. Si estos cables están trenzados, entonces el ruido inducido será casi el mismo en cada cable. La magnitud del flujo de corriente inducida es idéntica en cada conductor, pero viaja en direcciones opuestas, cancelando así la mayor parte del ruido. • Blindaje: Otro refinamiento en el rechazo del ruido es el blindaje, es decir, el uso de una malla o blindaje de lámina con conexión a tierra alrededor de los conductores. Como se mencionó anteriormente, el blindaje nunca debe estar conectado a tierra en más de un lugar para evitar bucles de tierra. La mayoría de los fabricantes de instrumentos recomiendan conectar a tierra el blindaje en el instrumento de campo. Sin embargo, un mejor lugar para hacerlo es en el panel de maniobras. Es más fácil verificar y gestionar las conexiones a tierra si están en un solo lugar. Además, es posible garantizar una buena conexión a tierra en ese punto. • Conducto: Un último refinamiento en el rechazo de ruido es el conducto metálico conectado a tierra. Esto rara vez se requiere, excepto para cables de comunicaciones de datos y para circuitos particularmente críticos. c. Detector de temperatura de resistencia (RTD) Un RTD está hecho de un trozo especial de cable cuya resistencia eléctrica cambia de manera predecible cuando el cable se expone a temperaturas variables. El material de elección hoy en día es platino de 100 ohmios, aunque a veces se utilizan otros tipos, como cobre de 10 ohmios. Para el RTD de platino, la clasificación es de 100 ohmios a 0 ºC. Los cambios de resistencia con la temperatura son muy pequeños, lo que provoca variaciones de voltaje en el rango de milivoltios. Los RTD están conectados a un circuito de puente de Wheatstone que está sintonizado con el RTD. Pero esta sintonización se produce en el banco de pruebas. ¿Qué sucede en el entorno de campo? Ya hemos analizado las dificultades de atenuación de línea inherentes a las señales de milivoltios (Capítulo 4). Este problema se supera en el circuito RTD mediante el uso de una o dos entradas de detección. Estas entradas ayudan a anular los efectos de las pérdidas de cobre debido a líneas largas y variaciones de temperatura a lo largo de ellas y son cables adicionales que deben incluirse en el cable RTD, de ahí los términos RTD de tres y cuatro cables. d. Termopar Como hemos analizado, un termopar explota la fuerza electromotriz (EMF) que surge de los cambios de temperatura que afectan a dos metales diferentes que se han laminado juntos. Esta EMF se manifiesta como una señal de milivoltios (CC). Cuando se unen ciertas combinaciones de estos metales diferentes, se produce una curva predecible de temperatura a voltaje a medida que cambia la temperatura en la unión. La señal se mide en el extremo abierto de los dos cables y se utiliza una escala de milivoltios por grado para convertir el voltaje a unidades de ingeniería. Por lo tanto, el termopar es un dispositivo de dos cables. Es susceptible al ruido radiado e inducido y, por lo tanto, suele alojarse en un cable blindado si se extiende por una distancia muy larga. La señal del termopar también es susceptible a la degradación debido a la pérdida de línea, por lo que es conveniente minimizar la longitud del cable. Además, es importante utilizar el cable de extensión adecuado. Un termopar suele venir con una conexión de coleta corta a la que se debe conectar el cable de extensión. Si se utiliza un material de cable diferente, como cobre, para extender la señal al PLC, se crea una "unión fría" espuria que provoca un EMF inverso que cancela parcialmente la señal. Por lo tanto, se debe utilizar el cable de extensión adecuado o se debe instalar un dispositivo llamado compensador de unión fría o referencia de punto de hielo entre el cableado de cobre y el cableado del termopar. Los módulos de E/S de termopar ya tienen la compensación de unión fría incorporada, por lo que se requiere el uso del cable de extensión de termopar adecuado. Los tipos específicos de termopares presentan diferentes características de temperatura. Un termopar tipo J se forma uniendo un cable de hierro con un cable de constantán. Esta configuración proporciona una curva relativamente lineal entre 0 y 750 ºC.8 Un termopar tipo K tiene un cable de níquel-cromo acoplado a un cable de níquel-aluminio, a veces llamado cromel/alumel. El termopar tipo K abarca un rango de temperatura útil de -200 a 1250 ºC. Otras combinaciones producen diferentes curvas de respuesta. e. 0–10 milivoltios (mV) Analógico Las señales analógicas se generaron primero mediante modulación de voltaje. En la antigüedad, un transmisor generaba una señal débil que debía capturarse y luego filtrarse y amplificarse para poder usarse para mover un bolígrafo en una grabadora o una aguja en un medidor. El talón de Aquiles de la señal de milivoltios es su susceptibilidad al ruido eléctrico. Este problema de relación señal-ruido aumenta en función de la longitud del cable, por lo que el transmisor debía estar muy cerca del indicador o registrador. En la actualidad, las señales de milivoltios se envían, en general, a transductores que convierten la pequeña señal en una corriente o en otros medios (como valores de datos digitales) menos susceptibles al ruido y a la pérdida de decibelios (dB) antes de abandonar la proximidad del elemento sensor. Sin embargo, algunos registradores y sistemas de adquisición de datos aún funcionan con la señal de milivoltios. f. Analógica de 4 a 20 miliamperios (mA) El impulso para superar las deficiencias de atenuación de línea de la señal de milivoltios dio como resultado el desarrollo del bucle de corriente de 4 a 20 mA. Como resultado de su rendimiento enormemente mejorado, este método de transmisión de señales analógicas se convirtió rápidamente en el estándar de la industria. La mayoría de los instrumentos de campo del mercado tienen un elemento sensor (sensor) y un elemento transmisor. El transmisor está sintonizado con el sensor, que puede proporcionar cualquier tipo de señal, desde analógica modulada en frecuencia hasta milivoltios de CC. Cualquiera que sea la forma de la señal, el transmisor la interpreta y la convierte en una corriente de salida entre 4 y 20 mA y, dentro de ese intervalo, es proporcional en magnitud a la entrada. El proceso de ajustar la salida a la entrada se denomina escalado. De este modo, el transmisor se convierte en lo que se conoce como una fuente de corriente variable. Así como una batería, como fuente de voltaje, intenta mantener un voltaje constante, independientemente de la cantidad de carga que se le aplique, la fuente de corriente intenta mantener una corriente constante (para una señal de entrada dada), independientemente de la carga. Dado que la corriente es común en todos los puntos de un circuito en serie, el problema de la longitud del cable (como se señaló como un problema con la señal de milivoltios) se anula. Por supuesto, la capacidad del dispositivo para forzar una corriente constante a través de un circuito se puede superar si se aplica suficiente carga. Por lo tanto, el diseñador debe saber cuánta energía es capaz de producir la fuente de corriente. En general, los instrumentos actuales pueden mantener 20 mA con una resistencia de circuito de 1000 ohmios. Dado que un instrumento típico no tiene más de 250 ohmios de resistencia de entrada, es posible alimentar varios instrumentos desde una sola fuente de corriente sin necesidad de un aislador. Por ejemplo, un solo transmisor debería poder enviar su señal a un PLC, un registrador gráfico y un totalizador a un costo de 750 ohmios, más la resistencia de línea. Esto debería estar dentro de la zona de confort de un transmisor típico. Nota: todavía hay instrumentos con clasificaciones de 600 ohmios en el mercado, por lo que el diseñador siempre debe verificar cuando se contemple un circuito complejo. Para determinar la energía disponible para el circuito, el diseñador debe poder identificar al proveedor de esa energía. Esa tarea a veces no es tan sencilla como podría parecer, y la respuesta a la pregunta afectará en gran medida el cableado del circuito. Hay dos tipos principales de circuitos analógicos, como se describe desde el punto de vista del transmisor. Los transmisores con dos cables se consideran dispositivos pasivos que absorben corriente, mientras que los transmisores con cuatro cables son dispositivos activos que generan corriente. La siguiente figura muestra tres transmisores de temperatura, cada uno conectado a diferentes puntos de E/S en el mismo módulo PLC. Un transmisor se alimenta directamente (es decir, con cuatro cables), mientras que los otros se alimentan indirectamente (es decir, con dos cables). Cada transmisor está conectado a un dispositivo de control, en este caso, una entrada de PLC. Desde la perspectiva del PLC, todas las entradas de corriente de 4–20 mA son en realidad entradas de voltaje. Se utilizan resistencias, ya sean externas proporcionadas por el usuario, como se muestra aquí, o internas, para convertir la corriente en voltaje. Los puntos de la computadora en sí son en realidad voltímetros de alta resistencia, lo que les da un excelente aislamiento de los dispositivos de campo y minimiza la carga adicional en el circuito de entrada. Los puntos de E/S en el PLC se muestran con energía interna disponible para cada punto, por lo que el módulo puede ser la fuente de voltaje para el bucle. A continuación se incluye un comentario detallado sobre las diferencias entre los dispositivos de dos y cuatro cables: 1. Circuito de cuatro cables Como se ve a continuación, un transmisor de cuatro cables es aquel que proporciona la energía para alimentar el bucle y generar la señal modulada por corriente. La mayoría de los transmisores de nivel, por ejemplo, son dispositivos de cuatro cables. Los dispositivos de cuatro cables siempre tienen conexiones de alimentación además de las conexiones de señal. Sin embargo, no todos los transmisores alimentados son de cuatro cables. Si la salida de un transmisor alimentado se indica como pasiva, entonces el dispositivo puede tratarse como una unidad de dos cables desde el punto de vista del circuito de señal. La mayoría de los dispositivos de grabación reciben alimentación externa, pero son pasivos en el circuito. En estos casos, la alimentación externa es solo para la electrónica interna de la unidad. El circuito de señal está aislado de esta fuente de alimentación. Tenga en cuenta que el grabador que se muestra en el circuito inferior es un dispositivo pasivo alimentado. 2. Circuito de dos cables Se dice que un dispositivo de dos cables está alimentado por bucle. Esto significa que el dispositivo funciona absorbiendo la energía que necesita para generar la señal del bucle de corriente. Esto también se conoce como "disipación de corriente". Esta nomenclatura puede ser un poco confusa porque un transmisor que está absorbiendo corriente sigue siendo la fuente de señal para el circuito. La energía para el bucle de corriente se suministra en otra parte. Un transmisor clasificado como de dos cables normalmente debe ser el primer dispositivo en el circuito con respecto al flujo de corriente. En otras palabras, el terminal positivo del transmisor debe estar conectado directamente al terminal positivo de la fuente de voltaje. La fuente de voltaje suele ser una fuente de alimentación de 24 VCC. (a) Circuitos de dos cables con fuente de alimentación independiente En referencia a la Figura anterior, el punto de E/S 2 del PLC representa un circuito de dos cables con una fuente de alimentación de CC externa. Observe que los cables deben estar enrollados (en sentido de polaridad) en el PLC para que la polaridad adecuada esté presente en el punto de E/S. Esto se debe a que el flujo de corriente ahora se invierte con respecto al ejemplo anterior, ya que el transmisor debe convertirse en la primera carga del bucle en lugar de ser la fuente de energía del bucle. (b) Circuitos de dos cables con fuente de alimentación interna del PLC La mayoría de los sistemas PLC actuales pueden generar la corriente del bucle por sí mismos simplemente conectando el terminal positivo del transmisor a un terminal diferente en el PLC. El terminal negativo del transmisor se conecta entonces al lado positivo del punto de E/S, y el lado negativo del punto de E/S se conecta al común de CC del sistema PLC. Esto se muestra en el ejemplo del punto de E/S 3. En ese ejemplo, se ha añadido un registrador al bucle. -
Ejemplos de programación de PLC en automatización industrial
leikang posted A plc and hmi article in Spanish in PLC programming learning
Desarrolle ejemplos de programación de PLC en automatización industrial de acuerdo con la lógica que se detalla a continuación: Una sierra, un ventilador y una bomba de aceite se encienden cuando se presiona un botón de inicio. Si la sierra ha funcionado menos de 20 s, la bomba de aceite debe apagarse cuando se apaga la sierra y el ventilador debe funcionar durante 5 s adicionales después de apagar la sierra. Si la sierra ha funcionado durante más de 20 s, el ventilador debe permanecer encendido hasta que se restablezca con un botón de reinicio del ventilador independiente y la bomba de aceite debe permanecer encendida durante 10 s adicionales después de que se apague la sierra. Escriba un programa de PLC que implemente este proceso. Ejemplos de programación de PLC Descripción del programa: Rung 0000: PB de inicio/parada de emergencia bloqueado con memoria B3:0/0. Rung 0001: B3:0/0 habilitado para encender la sierra (O: 0/0), el ventilador (O: 0/1) y la bomba de aceite (O: 0/2). El contacto normalmente cerrado del interruptor de parada está en serie con la salida de la sierra para apagarla. El interruptor de reinicio del ventilador y el temporizador T4:0 están conectados para apagar el ventilador cuando se cumple la condición. El temporizador T4:2 se detiene un poco y el bit de memoria es para apagar la bomba de aceite. Rung 0002: Cuando se presiona el botón de parada, de acuerdo con la lógica mencionada en el punto 2, la salida del ventilador (O: 0/2) debe apagarse después de 5 s. El bloque comparador restringe el temporizador T4:0 para que funcione después de los 20 s de funcionamiento de la sierra. Rung 0003: El temporizador T4:1 funciona cuando se presiona el botón de inicio. Cuando se presiona el botón de parada en cualquier momento después de los 20 s, la salida de la sierra se apagará. Después de 10 s, se apagará la bomba de aceite. Esta operación la realiza el temporizador T4:2. El bit de finalización del temporizador T4:0 se utiliza para restringir la operación del temporizador T4:1 cuando T4:0 está activado. Renglón 0004: Se utiliza menos de un bloque comparador para realizar la lógica mencionada en el punto 2, para apagar el ventilador cuando la operación de salida de la sierra fue inferior a 20 s. Salida del programa: Ahora vemos la simulación de la lógica de escalera anterior para diferentes condiciones, como se menciona a continuación. Cuando se presiona el PB de inicio Cuando se presiona el interruptor de parada antes de los 20 s Cuando se presiona el interruptor de parada después de los 20 s Cuando se presiona el interruptor de reinicio del ventilador Conclusión: Podemos usar este ejemplo para comprender la lógica de programación en el PLC Allen Bradley. -
Programa PLC para el control de entrada y salida de aparcamientos
leikang posted A plc and hmi article in Spanish in PLC programming learning
Este es un programa PLC para el control de entrada y salida de aparcamientos subterráneos o en sótanos. Aparcamiento de coches con PLC Descripción del problema Debido a las zonas concurridas, nos enfrentamos a muchos problemas de aparcamiento de vehículos en sótanos o subterráneos en centros comerciales, hoteles, complejos, etc. Esto sucede debido a la contradicción entre el número de vehículos en rápido crecimiento y los espacios de aparcamiento limitados en centros comerciales, tiendas y complejos en las ciudades, lo que da como resultado el fenómeno de "aparcamiento difícil y aparcamiento desordenado". El problema actual del aparcamiento tiene graves repercusiones en la calidad de vida de las personas y en el funcionamiento de las carreteras. Diagrama del problema Solución del problema Con una automatización sencilla podemos reducir el problema del aparcamiento en sótanos o subterráneos en centros comerciales, hoteles, complejos, etc. La entrada y salida en el sótano es un paso de un solo carril y necesita semáforos para controlar los coches. Aquí consideramos la indicación de dos luces para el control de los coches. Las luces rojas prohíben la entrada y salida de vehículos, mientras que las luces verdes permiten la entrada y salida de vehículos. Cuando un vehículo entra por el pasillo desde la entrada de la planta baja, ambas luces rojas (planta baja y sótano) estarán encendidas. Se prohíbe la entrada y salida de otros vehículos durante el proceso hasta que el vehículo pase por el pasillo único. Cuando el pasillo esté despejado, ambas luces verdes (planta baja y sótano) estarán encendidas y permitirán la entrada de otros vehículos desde la planta baja o el sótano. Inicialmente mantendremos las luces verdes ENCENDIDAS y la luz roja APAGADA Lista de entradas y salidas Lista de entradas INTERRUPTOR principal: I0.0 Sensor S1 para entrada/salida de planta baja: I0.1 Sensor S2 para entrada/salida de sótano: I0.2 Lista de salidas Luz verde (Entrada/salida de planta baja): Q0.0 Luz verde (Entrada/salida de sótano): Q0.1 Luz roja (Entrada/salida de planta baja): Q0.2 Luz roja (Entrada/salida de sótano): Q0.3 Lista de bobinas de memoria M M10.0: Estará ENCENDIDO cuando el automóvil pase el sensor S1 M10.3: Estará ENCENDIDO cuando el automóvil pase el sensor S2 M0.0: Borde positivo del sistema ENCENDIDO M0.1 y M11.0: Borde positivo del sensor S1 M0.3 y M11.1: Borde positivo del sensor S2 M11.2: borde negativo del sensor S2 M11.3: borde negativo del sensor S1 Diagrama de escalera de PLC para control de entrada/salida de estacionamiento de automóviles Descripción del programa En esta aplicación hemos utilizado el PLC Siemens S7-300 y el software TIA Portal para la programación. Red 1: Según la explicación anterior, en la primera red, cuando el sistema está ENCENDIDO (I0.0), inicialmente ambas luces verdes (planta baja (Q0.0) y sótano (Q0.1)) estarán ENCENDIDAS. Se ejecuta la instrucción SET y se activarán las salidas Q0.0 y Q0.1. Red 2: Según la explicación anterior en la segunda red, cuando el sistema está encendido (I0.0), inicialmente ambas luces rojas (planta baja (Q0.2) y sótano (Q0.3)) estarán apagadas. Se ejecuta la instrucción RESET y se restablecerán las salidas Q0.2 y Q0.3. Red 3: Cuando el automóvil ingresa al pasaje vacío desde la planta baja, se activará el sensor S1 (I0.1) y con este disparador, se activará la bobina de memoria M10.0. Red 4: Cuando el automóvil ingresa al pasaje vacío desde el sótano, se activará el sensor S2 (I0.2) y con este disparador, se activará la bobina de memoria M10.3. Red 5: Ambas luces rojas se activarán mediante el disparador positivo del sensor S1 o del sensor S2, ya que cuando el automóvil ingresa en un pasaje vacío, ambas luces rojas (Q0.2 y Q0.3) prohibirán la entrada o salida del automóvil desde ambos lados. Red 6: Aquí hemos tomado el disparador negativo de ambos sensores S1 (I0.1) y S2 (I0.2), por lo que cuando se activan, las luces rojas (Q0.2 y Q0.3) se APAGARÁN. Cuando el automóvil pase completamente el pasaje vacío, las luces rojas (Q0.2 y Q0.3) deben APAGARSE. Red 7: En esta red, las luces verdes (Q0.0 y Q0.1) se encenderán cuando las luces rojas estén APAGADAS. Las luces verdes (Q0.0 y Q0.1) permiten que otros automóviles ingresen o salgan. Red 8: Si las luces rojas (Q0.2 y Q0.3) están ENCENDIDAS en ese momento, las luces verdes (Q0.0 y Q0.1) deben estar APAGADAS. Por lo tanto, en esta red, cuando las luces rojas (Q0.2 y Q0.3) estén ENCENDIDAS en ese momento, se ejecutará la instrucción de reinicio y las luces verdes (Q0.0 y Q0.1) estarán APAGADAS. Red 9: Si el sistema está ENCENDIDO (I0.0) y el INTERRUPTOR está APAGADO, todas las memorias deben estar a 0. Aquí hemos tomado la instrucción MOVE para mover el cero en todas las memorias (MB0, QB0 y MB10). Este ejemplo es solo para explicar el concepto; no se consideran todos los parámetros en este ejemplo (como el sistema de apertura/cierre de puertas, alarmas, etc.). Resultado Nota: La lógica de PLC anterior proporciona una idea básica sobre la aplicación del PLC en el control de estacionamiento de automóviles de las puertas de entrada/salida. La lógica es limitada y no es una aplicación completa.