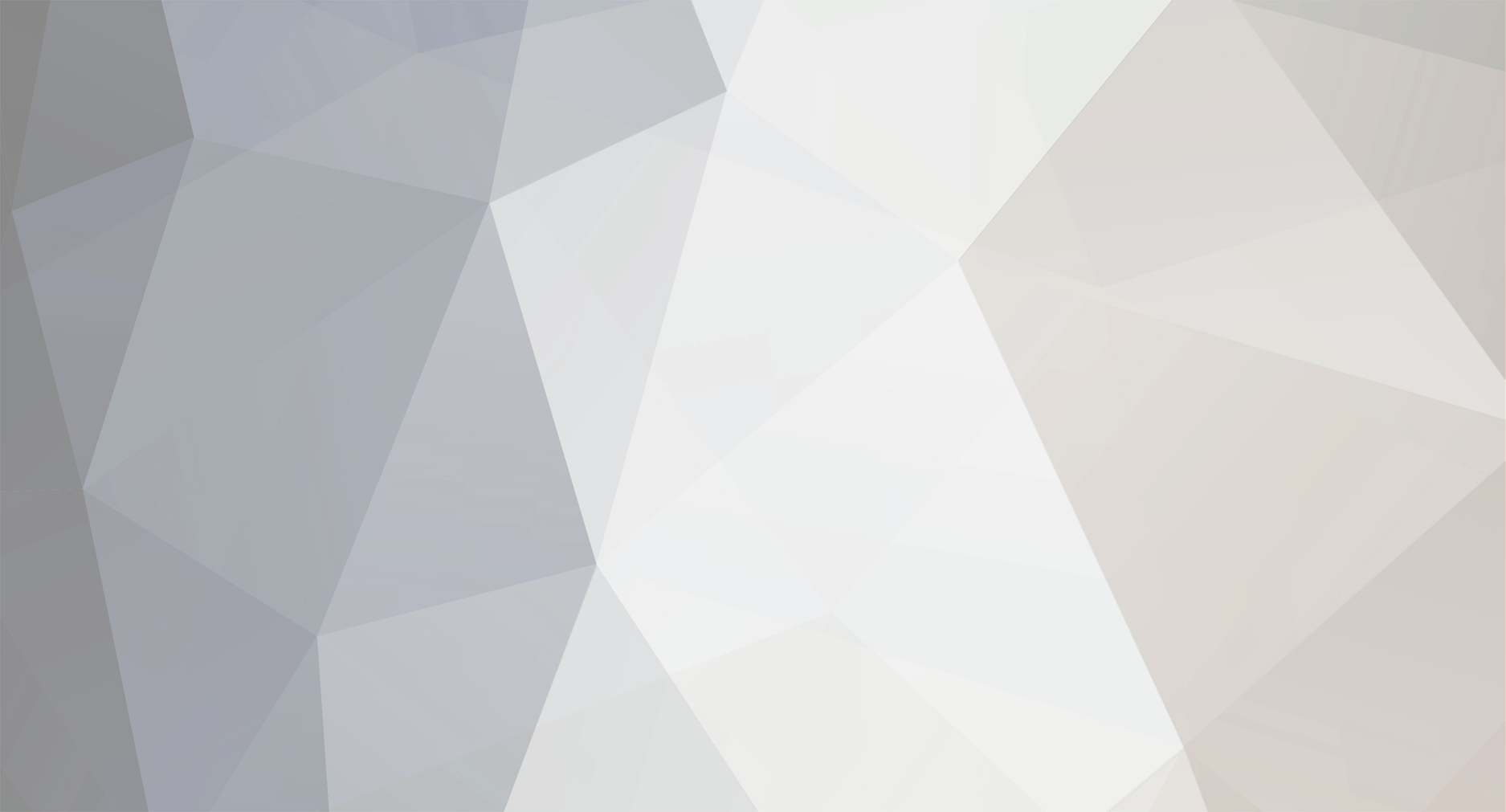
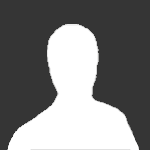
leizuofa
Staff group-
Content Count
198 -
Joined
-
Last visited
Content Type
Profiles
Forums
PLC programming technology and HMI interface design Simplified Chinese database
- PLC AND HMI SIMPLIFIED CHINESE ARTICLES
- PLC AND HMI SIMPLIFIED CHINESE ARTICLE Comments
- PLC AND HMI SIMPLIFIED CHINESE ARTICLE Reviews
PLC and HMI Brand Database
- PLC AND HMI BRANDS INTRODUCTIONS
- PLC AND HMI BRAND INTRODUCTION Comments
- PLC AND HMI BRAND INTRODUCTION Reviews
PLC programming technology and HMI interface design English database
- PLC AND HMI ENGLISH ARTICLES
- PLC AND HMI ENGLISH ARTICLE Comments
- PLC AND HMI ENGLISH ARTICLE Reviews
PLC programming technology and HMI interface design Russian database
- PLC AND HMI RUSSIAN ARTICLES
- PLC AND HMI RUSSIAN ARTICLE Comments
- PLC AND HMI RUSSIAN ARTICLE Reviews
Spanish database on PLC programming techniques and HMI interface design
- PLC AND HMI SPANISH ARTICLES
- PLC AND HMI SPANISH ARTICLE Comments
- PLC AND HMI SPANISH ARTICLE Reviews
German database on PLC programming technology and HMI interface design
- PLC AND HMI ARTICLES IN GERMAN
- PLC AND HMI ARTICLE IN GERMAN Comments
- PLC AND HMI ARTICLE IN GERMAN Reviews
Downloads
Store
Gallery
Blogs
Calendar
Videos
Everything posted by leizuofa
-
ПЛК включает или выключает выходы на основе событий
leizuofa posted A plc and hmi russian article in PLC programming learning
Напишите следующую программу ПЛК для включения или выключения выходов на основе событий. Определенный переключатель (I:1/0) должен запустить процесс. Процесс должен выполняться в течение 30 секунд, останавливаться на 10 секунд, а затем повторяться, пока переключатель I:1/0 остается замкнутым. Открытие I:1/0 в любое время приводит к сбросу всех таймеров и отключению всех выходов. Выход O:2/0 должен быть включен в течение 30-секундного периода работы, а выход O:2/1 должен быть включен в течение 10-секундного периода остановки. Во время периода работы один выход O:2/2 управляется входом I:1/1. Если I:1/1 открыт (в начале периода работы), O:2/2 должен быть выключен в течение первых 5 секунд, а затем включен в течение 10 секунд. Если I:1/1 закрыт (в начале периода работы), O:2/2 должен быть выключен в течение первых 10 секунд, а затем включен в течение 15 секунд. Изменение I:1/1 после начала периода работы не должно изменить указанную выше последовательность. Выход O:2/2 всегда должен быть выключен в течение периода остановки. Включение или отключение выходов ПЛК -
Напишите программу счетчиков ПЛК для приведенного ниже примера. Счетчики ПЛК Определенный процесс заключается в подсчете количества переходов «истина-ложь» на входе I:0.0/0 в течение 10-секундного периода. Подсчет должен выполняться, если входное слово I:0.1 имеет значение меньше 10000 или больше 20000. 10-секундный период подсчета должен начинаться через 15 секунд после начала процесса. I:0.0/1 — это вход запуска процесса, а вход I:0.0/2 — это вход остановки процесса. Дисплей подсчета должен выводиться в слово O:0.0 только в конце периода подсчета. Все выходы должны быть обесточены через 5 секунд после периода подсчета. Процесс должен повторяться только после еще одного отдельного нажатия входа запуска процесса. Напишите эффективную программу релейной логики для этого процесса. Логика ПЛК
-
Программа логического вентиля ПЛК
leizuofa posted A plc and hmi russian article in PLC programming learning
Напишите программу логического вентиля ПЛК для примера ПЛК ниже. Программа логического вентиля Напишите программу, которая выполняет операцию И B3:0 с B3:1 при подаче питания на I:0.0/0, операцию ИЛИ B3:0 с B3:1 при подаче питания на I:0.0/1, операцию ИСКЛЮЧАЮЩЕЕ ИЛИ B3:0 с B3:1 при подаче питания на I:0.0/2 и операцию ДОПОЛНЕНИЯ B3:0 при подаче питания на I:0.0/3. B3:1 должна содержать результат в каждом случае. Если подаётся питание на более чем один вход I:0.0/0-I:0.0/3, будет выполнена только одна из операций. Порядок приоритета операций должен быть от И (высший приоритет) до ДОПОЛНЕНИЯ (низший приоритет). Логика лестничной схемы ПЛК -
ALLEN BRADLEY-RU Подпрограммы ПЛК Allen Bradley
leizuofa posted A plc and hmi russian article in PLC programming learning
Инструкции JSR, SBR и RET используются для указания контроллеру выполнить отдельный файл подпрограммы в программе релейной логики и вернуться к инструкции, следующей за инструкцией JSR. Подпрограммы ПЛК Allen Bradley Инструкция SBR должна быть первой инструкцией на первой ступени в файле программы, содержащем подпрограмму. Используйте подпрограмму для хранения повторяющихся разделов логики программы, которые должны быть выполнены из нескольких точек в вашей прикладной программе Подпрограмма экономит память, поскольку вы программируете ее только один раз. Обновляйте критический ввод-вывод в подпрограммах с помощью инструкций немедленного ввода и/или вывода (IIM, IOM), особенно если ваше приложение вызывает вложенные или относительно длинные подпрограммы В противном случае контроллер не обновляет ввод-вывод, пока не достигнет конца основной программы (после выполнения всех подпрограмм) Выходы, контролируемые в подпрограмме, остаются в своем последнем состоянии, пока подпрограмма не будет выполнена снова. При выполнении инструкции JSR контроллер переходит к инструкции подпрограммы (SBR) в начале целевого файла подпрограммы и возобновляет выполнение с этой точки. Вы не можете перейти ни в одну часть подпрограммы, кроме первой инструкции в этом файле. Целевая подпрограмма идентифицируется номером файла, который вы ввели в инструкции JSR. Инструкция SBR служит меткой или идентификатором для программного файла как обычного файла подпрограммы. Инструкция должна быть запрограммирована как первая инструкция первой ступени подпрограммы. Инструкция RET отмечает конец выполнения подпрограммы или конец файла подпрограммы. Ступень, содержащая инструкцию RET, может быть условной, если эта ступень предшествует концу подпрограммы. Таким образом, контроллер пропускает остаток подпрограммы, только если условие ее ступени истинно. -
Напишите программу таймеров ПЛК для следующего примера ПЛК. Таймеры ПЛК Создайте схему синхронизации ПЛК, которая будет выводить (используя выход O:2/0) 0,5-секундный импульс каждые две секунды (т. е. включен на 0,5 с, затем выключен на 2 с). Если переключатель (используя I:1/0) замкнут, и 1-секундный импульс каждые две секунды, если переключатель разомкнут. Лестничная логика
-
Registro de bits de desplazamiento en PLC
leizuofa posted A plc and hmi article in Spanish in PLC programming learning
Hay muchas instrucciones en PLC que ayudan a ejecutar la lógica de una manera simplificada. Las instrucciones vienen en varias categorías como aritmética, comparación, lógica, controlador, etc. Por ejemplo, una instrucción de suma simple para sumar dos variables viene en la categoría aritmética. Por lo tanto, de manera similar, hay muchos tipos de instrucciones disponibles en una lógica de PLC. Una de esas instrucciones que se usa ampliamente en la programación de PLC es la instrucción de desplazamiento. Viene en la categoría de procesamiento numérico. En este artículo, aprenderemos el concepto de instrucción de registro de bits de desplazamiento en la programación de PLC. Registro de bits de desplazamiento en PLC Como su nombre lo indica, una instrucción de desplazamiento es un comando para desplazar bits de una palabra en una posición predefinida. Por ejemplo, tiene una palabra de 16 bits. Quiere mover el bit número 3 de su cuarta posición actual a la séptima posición. Entonces, siempre que se dé un pulso de comando de desplazamiento, el bit se desplazará en cada activación de la cuarta posición a la séptima posición. En esa continuidad, el bit en la quinta posición se moverá a la octava posición; y el bit en la tercera posición se moverá a la sexta posición. Entonces, aquí, estás desplazando los bits en un grupo por la cantidad de posiciones que definas. Instrucción Shift Las instrucciones Shift vienen en dos tipos: shift y rotate. Echemos un vistazo a la instrucción rotate. Considere una sintaxis: %MW10:= SHL (%MW12, 4). %MW10 es la palabra de memoria de destino y %MW12 es la palabra de memoria de origen. Consulte la siguiente imagen. En %MW10, cuando se proporciona un primer disparador para el desplazamiento a la izquierda, el bit 0 se desplaza al bit 1, y así sucesivamente. Este resultado se almacena en %MW12. Cuando se proporcionan tales disparadores cuatro veces, en última instancia, el bit 0 se desplazará finalmente al bit 4, y así sucesivamente. El resultado final se almacena en %MW12 de todos modos y obtiene una respuesta final de los bits desplazados cuatro posiciones desde la palabra de origen. Pero, una cosa para recordar es que, con cada cambio, el bit anterior se llena con el valor 0. Esto se puede ver claramente en la imagen. Después del primer cambio, el primer bit en %MW12 es 0. Por lo tanto, después de cuatro cambios, el resultado final será - 0000 1101 1100 0000. Este cambio puede ser a la derecha o a la izquierda. Hay otro tipo de cambio en el PLC; el anterior añadía ceros de la posición anterior, pero este segundo tipo mantiene el valor del primer bit (MSB para la derecha y LSB para la izquierda) tal como está. Esto se llama cambio aritmético. Por lo tanto, si el valor del primer bit (MSB para la derecha y LSB para la izquierda) inicialmente antes del cambio era 1, entonces el último bit permanecerá como 1 solamente y los ceros se añadirán desde el segundo bit anterior hasta la cantidad de veces que se dé el comando de cambio. Cabe señalar que el último bit que se desplaza siempre se almacena en un bit de acarreo. Instrucción de rotación El segundo tipo es la instrucción de rotación. Considere la sintaxis: %MW10:= ROL (%MW12, 4). %MW10 es la palabra de memoria de destino y %MW12 es la palabra de memoria de origen. Usaremos la misma imagen anterior como referencia. La instrucción de rotación, como lo define el nombre, simplemente gira los bits en la cantidad de posiciones que usted defina. En comparación con la instrucción de desplazamiento, donde se agregó cero después de cada bit anterior, aquí los bits simplemente se desplazan en la misma secuencia que en la dirección izquierda. Entonces, suponga que tiene una palabra de origen de – 1100 1010 1100 0101; luego, después de un disparador de 4 posiciones, el resultado final será – 1010 1100 0101 1100. La misma lógica funciona en la dirección correcta. El último bit desplazado también se almacena en un bit de acarreo. Existe otro tipo en la categoría de rotación. En este caso, en lugar de desplazar solo 16 bits, se transfiere el bit de acarreo. Esto significa que el último bit se desplaza al bit de acarreo y, a continuación, el bit de acarreo se desplaza al primer bit, y así sucesivamente. En el tipo anterior, el último bit solo se almacenaba en el bit de acarreo. -
SIEMENS-ES Tutorial de configuración de hardware del PLC Siemens S7-1200
leizuofa posted A plc and hmi article in Spanish in PLC programming learning
El PLC S7-1200 es una solución compacta, modular y rentable que ofrece una amplia gama de funciones y flexibilidad para aplicaciones de automatización de tamaño pequeño a mediano. Estas funciones incluyen opciones de comunicación, memoria, rendimiento de la CPU y configuración de E/S. Cuando tenga un proceso que necesite controlar, debe elegir el PLC y configurarlo para que se adapte mejor a los requisitos de su proceso. En este artículo, analizaremos la configuración de hardware del PLC S7-1200 y daremos un ejemplo de cómo configurarlo en el portal Siemens Tia. Contenido: ¿Cuál es la configuración de hardware de un PLC? Importancia de la configuración de hardware. Ejemplo de proyecto simple. ¿Cómo configurar nuestro PLC con el ejemplo dado? Configuración de hardware de CPU. Configuración de hardware de E/S. Configuración de HMI. Conclusión. ¿Cuál es la configuración de hardware de un PLC? La configuración de hardware se refiere a los componentes específicos del PLC, como la CPU, la memoria, los módulos de entrada/salida (E/S), los puertos de comunicación, la fuente de alimentación y cualquier módulo o accesorio adicional que pueda ser necesario y agregarse al sistema. La configuración de hardware de un PLC también incluye habilitar o deshabilitar algunas de las características de la CPU, según el dispositivo, sus capacidades y los requisitos de su proceso. Los pasos de configuración de hardware para un PLC generalmente implican lo siguiente: Seleccione el modelo de PLC adecuado según los requisitos de la aplicación. Identifique los requisitos de entrada/salida para el sistema, que incluyen el tipo y la cantidad de sensores, actuadores y otros dispositivos que se conectarán al PLC. Elija el protocolo de comunicación y la topología de red que se utilizará para conectar el PLC a otros dispositivos y sistemas. Determine los requisitos de la fuente de alimentación para el PLC y sus periféricos. Monte el PLC en una ubicación adecuada y conecte todos los cables y alambres necesarios. Configure el software del PLC para comunicarse con los componentes de hardware y configure las funciones lógicas y de control adecuadas. Los pasos específicos para la configuración del hardware pueden variar según el modelo de PLC y los requisitos de la aplicación, pero estos son los pasos básicos que suelen estar involucrados en el proceso. En este artículo, hablaremos sobre la configuración del hardware que se realiza en la plataforma TIA Portal. Esto significa que asumiremos que conoce su aplicación y que ya ha elegido su modelo de PLC y la fuente de alimentación para alimentarlo. Puede consultar artículos anteriores en los que analizamos cómo elegir el PLC y la fuente de alimentación que mejor se adapten a su aplicación. Importancia de la configuración del hardware en el PLC La configuración adecuada del hardware garantiza que el sistema sea confiable y robusto. Si los componentes del hardware no están configurados correctamente, es posible que no funcionen como se espera, lo que provocará fallas o errores del sistema. La configuración del hardware afecta el rendimiento del sistema. Al elegir los componentes de hardware correctos y configurarlos adecuadamente, el sistema puede funcionar con la máxima eficiencia y velocidad y puede manejar un gran volumen de entradas y salidas. La configuración del hardware afecta la escalabilidad y la flexibilidad del sistema. La elección de los componentes de hardware y su configuración debe tener en cuenta futuras ampliaciones o modificaciones del sistema, para garantizar que el sistema pueda adaptarse fácilmente a los cambios o actualizaciones. La configuración del hardware afecta el costo del sistema. Al seleccionar los componentes y la configuración de hardware adecuados, se pueden evitar costos innecesarios y se puede minimizar el costo general del sistema. Configuración del hardware del S7-1200 Supondremos un proyecto de PLC simple y veremos cómo podemos configurar el PLC en nuestro proyecto antes de comenzar a escribir nuestro código. Sistema de control de temperatura para un reactor mediante PLC El proyecto implica controlar la temperatura de un reactor mediante un PLC. El sistema debe medir la temperatura del reactor y ajustar la temperatura controlando el flujo de un fluido refrigerante. El proyecto utiliza cuatro termopares para medir la temperatura, dos válvulas solenoides para controlar el flujo del fluido refrigerante y un motor para impulsar el impulsor del reactor. Configuración de E/S Entradas: Termopares 1 a 4: son 4 entradas analógicas que miden la temperatura en diferentes ubicaciones dentro del reactor. Pulsador de Parada de Emergencia: Es una entrada digital que se utiliza para detener el sistema en caso de una emergencia. Potenciómetro de Punto de Ajuste de Temperatura: Es una entrada analógica que permite al operador establecer el punto de ajuste de temperatura deseado. Salidas: Válvula Solenoide 1 y 2: Son 2 salidas digitales que controlan el flujo del fluido refrigerante a través de las tuberías del reactor. Control de Motor: Es una salida digital que controla la velocidad y dirección del motor que impulsa el impulsor. Control de Calentador: Es una salida digital que controla el sistema de calentamiento del reactor. Operación del Sistema: El sistema espera a que el operador fije el punto de ajuste de temperatura mediante el potenciómetro. El PLC lee el punto de ajuste de temperatura y lo compara con la temperatura actual del reactor, que se mide mediante los cuatro termopares. Si la temperatura del reactor está por debajo del punto de ajuste, el PLC activa la salida de control del calentador para aumentar la temperatura. Si la temperatura del reactor está por encima del punto de ajuste, el PLC activa una de las salidas de la válvula solenoide para aumentar el flujo del fluido de enfriamiento y disminuir la temperatura. El PLC monitorea continuamente la temperatura y ajusta los sistemas de calefacción y enfriamiento para mantener el punto de ajuste deseado. El PLC también controla el motor que impulsa el impulsor para mezclar el contenido del reactor. Si se presiona el botón de parada de emergencia, el PLC desactiva todas las salidas y detiene el sistema. El proyecto del PLC se puede ampliar y modificar aún más para incluir funciones adicionales, como alarmas, registro de datos o monitoreo remoto, según los requisitos específicos del proyecto. Sin embargo, no nos ocuparemos de codificar la lógica del PLC de este sistema, sino que utilizaremos este ejemplo para explicar cómo configurar el hardware del PLC para que se ajuste a nuestro proyecto. Esto incluye: Selección de la CPU del PLC. Selección de los módulos de E/S. Asignación de las etiquetas de entrada y salida a los módulos de hardware. Asignación de una IP al PLC para la comunicación. Asignación de una contraseña de protección. Configuración de la hora local del PLC. Configuración de la HMI y establecimiento de la conexión con el PLC. ¿Cómo configurar el PLC con el ejemplo dado? A continuación, analizaremos la creación básica de un proyecto de PLC con el hardware necesario. La configuración del hardware de la CPU: Selección de la CPU: Cuando inicie un nuevo proyecto en TIA Portal, deberá configurar un nuevo dispositivo y agregarlo a su proyecto. Consulte la imagen 1. Imagen 1. Configure un dispositivo para su proyecto Como puede ver en la imagen anterior, el portal TIA ya le muestra que el primer paso debe ser configurar un nuevo dispositivo. En el artículo anterior, analizamos cómo elegir el PLC que se adapta a su proceso, por lo que no lo volveremos a mencionar aquí. Para nuestro proyecto, dado que es un proyecto simple, elegiremos la CPU 1214C AC/DC/RLY. Consulte la imagen 2. Imagen 2. Agregue un nuevo controlador al proyecto Propiedades de la CPU: Dependiendo de la CPU que haya seleccionado para su proyecto, estarán disponibles diferentes características y propiedades de la CPU. Puede habilitar o deshabilitar estas características según sus necesidades. Algunas de las características necesitarán una configuración adicional. Vea la imagen 3. Imagen 3 – Propiedades de la CPU Como puede ver en la imagen anterior, hay muchas propiedades que puede configurar para su CPU en el proyecto. Mencionaremos algunas de estas propiedades que deberá configurar en cada proyecto que realice, algunas otras propiedades se utilizan solo en casos especiales. Comunicación: Esta es una configuración muy importante para cualquier proyecto de PLC; su proyecto probablemente tendrá diferentes módulos y dispositivos que necesitan comunicarse entre sí. Configurar la comunicación entre su PLC y estos dispositivos es importante para su proyecto. Al seleccionar la CPU, ya ha definido cómo será la comunicación. Algunas CPU solo funcionan con Profinet, algunas solo funcionan con Profibus y algunas tienen la capacidad de usar ambos. El PLC seleccionado para este ejemplo solo funciona con Profinet. Desde la interfaz Profinet, establecerá la dirección IP para su PLC, esta IP debe ser única en el proyecto; no puede usar la misma IP para dos módulos diferentes. Consulte la imagen 4. Imagen 4: interfaz Profinet Tiempo de ciclo: Esta es otra propiedad importante para su PLC, como ya sabe; el tiempo de ciclo de su programa dependerá de la cantidad de código que haya escrito y de cuánto tiempo le tomará al PLC ejecutar este código. En las propiedades de tiempo de ciclo, puede configurar el tiempo de monitoreo de ciclo; si el PLC tarda más que este tiempo establecido en ejecutar el programa, entonces el PLC dará un error. Consulte la imagen 5. A partir de esta propiedad también puede determinar el tiempo de ciclo mínimo para su CPU; puede hacerlo si activó la opción “Habilitar tiempo de ciclo mínimo para OB cíclicos”. Luego puede escribir el tiempo de ciclo mínimo que desee y el PLC ajustará su rendimiento para que coincida con este tiempo. Por supuesto, este tiempo está limitado por la capacidad de rendimiento de la CPU, por lo que no puede reducirlo por debajo de un cierto límite. Imagen 5: Propiedad de tiempo de ciclo Bits de memoria del sistema y del reloj: Los bits de memoria del sistema y los bits de memoria del reloj son bits integrados dentro de la CPU que el sistema operativo utiliza para indicar ciertos eventos en el PLC. Por ejemplo, hay un bit de memoria que cambiará a VERDADERO solo en el primer escaneo o un bit de memoria que será VERDADERO si cambia el estado de diagnóstico; también hay algunos bits de memoria del reloj dedicados, como un bit que representa un reloj de 10 Hz o un bit que representa un reloj de 2 Hz. Estos bits pueden ser muy útiles en algunas aplicaciones y pueden ahorrar mucho código de programación para obtener la misma funcionalidad. Ver imagen 6. imagen 6 – Habilitar bits de memoria de sistema y reloj Puede habilitar el uso de uno o ambos bytes de memoria; también puede determinar la dirección de estos bytes como puede ver en la imagen. Hora del día: Otra propiedad muy importante de su PLC es configurar la hora dentro de su PLC. En casi cualquier proyecto que realice, necesitará saber la hora real para poder asignar ciertas acciones con diferentes fechas. En el artículo anterior, hablamos sobre las horas locales y del sistema dentro del PLC y cómo usarlas. Esta propiedad de la CPU le permite configurar la hora local en la zona horaria que desee. Ver imagen 7. Imagen 7 – Propiedad de hora local Protección y seguridad: A partir de esta propiedad, puede determinar el nivel de acceso y la protección con contraseña para su PLC. Consulte la imagen 8. Imagen 8: propiedad de protección y seguridad Las propiedades mencionadas anteriormente son las propiedades configuradas con mayor frecuencia en casi cualquier proyecto de PLC que realice. Hay otras propiedades que es menos probable que se utilicen con programas simples, como servidores web y OPC UA. El siguiente paso en la configuración del hardware de su proyecto es configurar las E/S. Configuración del hardware de las E/S: Otro paso importante de su proyecto es la configuración de las E/S, lo que significa decidir cuántos módulos de E/S necesita y qué tipo de módulos de E/S necesita. Al decidir sobre las E/S, debe considerar algunos puntos clave, como tener algunos puntos de E/S de repuesto y elegir los módulos de E/S que se ajusten a los sensores de entrada y los actuadores de salida dentro de su proyecto. Ver imagen 9. Imagen 9 – Añadiendo módulo de entrada analógica Como mencionamos en nuestro proyecto de ejemplo, tenemos 4 termopares utilizados como entradas analógicas a mi PLC, por lo que necesito añadir un módulo de entrada analógica con al menos 4 canales de entrada porque el PLC seleccionado solo tiene 2 canales de entrada analógica. Otra cosa es que el termopar es un tipo especial de entrada analógica que requiere un módulo de entrada dedicado. Por eso elegimos el módulo AI 8xTC, que tiene 8 canales de entrada dedicados a ser utilizados con termopares; elegimos el módulo de 8 canales y el de 4 para tener canales de repuesto para uso futuro en caso de que necesitemos ampliar nuestro proyecto. Si vas a las propiedades del módulo AI 8xTC verás que puedes configurar cada canal de entrada individualmente, puedes elegir el tipo de termopar, escala de medición y otras propiedades. Consulte la imagen 10. Imagen 10: configuración del módulo de entrada A continuación, deberá definir las etiquetas de E/S y asignar cada entrada o salida que tenga a un punto de E/S adecuado en su PLC o en los módulos de E/S. Consulte la imagen 11. Imagen 11: asignación de etiquetas de entrada Luego, continúe asignando el resto de las etiquetas de entradas y salidas, consulte las imágenes 12 y 13. Imagen 12: asignación de etiquetas de entrada para el PLC Imagen 13: asignación de etiquetas de salida a su proyecto Configuración de HMI Su proyecto de PLC probablemente necesitará una HMI; después de seleccionar su HMI, hay diferentes configuraciones que puede realizar. En este artículo, solo le mostraremos cómo configurar la comunicación entre la HMI y el PLC. Como puede ver en la imagen anterior, puede seleccionar una HMI agregando un nuevo dispositivo y luego seleccionar una HMI. Vea la imagen 14. Imagen 14: selección de una HMI Existen diferentes formas de configurar la comunicación entre la HMI y el PLC, pero la forma más fácil es a través de la página de vista de red. Vea la imagen 15. Imagen 15: configuración de la conexión de la HMI Dentro de la página de vista de red, puede configurar la conexión entre la HMI y el PLC simplemente haciendo clic en el pequeño cuadrado verde que representa Profinet desde la HMI y arrastrándolo hacia el PLC. A continuación, TIA Portal dibujará una línea verde entre los dos módulos y le dará automáticamente a la HMI una dirección IP para configurar la comunicación entre ellos. Conclusión La configuración del hardware es un paso muy crítico de cualquier proyecto de PLC. La configuración de hardware adecuada de su PLC garantizará que se cumplan las funciones necesarias del proyecto. Las configuraciones de hardware incluyen la selección de módulos de E/S, la habilitación o deshabilitación de determinadas propiedades de la CPU y la configuración de distintos dispositivos, como la HMI, con su PLC. -
SIEMENS-ES Descripción general de los PLC de SIEMENS: S7-1500, S7-1200, S7-400, S7-300
leizuofa posted A plc and hmi article in Spanish in PLC programming learning
Siemens es una conocida empresa multinacional que opera en una variedad de industrias, incluidas la energía, la atención médica, el transporte y la automatización industrial. Siemens se fundó en 1847 y desde entonces se ha convertido en una corporación global con operaciones en muchos países. Siemens es conocida por sus productos y servicios innovadores y ha sido reconocida como una de las empresas más sostenibles del mundo. En este artículo, brindaremos una descripción general de los PLC de Siemens, que son una parte muy pequeña de los diversos productos de Siemens en el sector de la automatización industrial. Contenido: Siemens en la automatización industrial. Diferentes familias de PLC de Siemens. Descripción general de los PLC S7 de Siemens. Simatic S7-1200. Simatic S7-1500. Simatic S7-300. Simatic S7-400. CPU Simatic S7-ET 200 ¿Por qué hay tantos modelos diferentes? ¿Cómo decidir qué tipo de PLC S7 se adapta mejor a mi aplicación? Conclusión. Siemens en la automatización industrial Siemens es líder en el campo de la automatización industrial y es conocida por sus productos y soluciones de alta calidad. La empresa ofrece una amplia gama de productos de automatización industrial, incluidos controladores lógicos programables (PLC), interfaces hombre-máquina (HMI), variadores de frecuencia (VFD) y redes de comunicación industrial. Siemens también ofrece soluciones de software para la automatización industrial, como el portal TIA de automatización totalmente integrada, que es un marco de ingeniería que integra todas las herramientas de software de automatización en una sola plataforma. Además, Siemens ha desarrollado su propia plataforma de Internet industrial de las cosas (IIoT) llamada MindSphere, que permite la recopilación y el análisis de datos de dispositivos conectados en entornos industriales. Diferentes familias de PLC de Siemens Siemens tiene dos familias principales de PLC que se desarrollaron y son: Familia de PLC Simatic S5 Familia de PLC Simatic S7 La serie Simatic S5 fue la generación anterior de PLC de Siemens y todavía se utiliza en algunos sistemas industriales más antiguos, pero ya no se fabrica. La serie Simatic S7 es el PLC actual de Siemens. Ofrece una amplia gama de CPU con diferentes niveles de rendimiento y funcionalidad para satisfacer diferentes necesidades de automatización. La serie S7 es conocida por su confiabilidad, robustez y flexibilidad, y se usa ampliamente en industrias como la automotriz, la de alimentos y bebidas y la farmacéutica. Descripción general del PLC Siemens S7 La generación S7 de PLC de Siemens ofrece una amplia gama de CPU con diferentes niveles de rendimiento y funcionalidad para satisfacer las demandas de diferentes procesos de automatización industrial; estas CPU pertenecerán a una de las siguientes subfamilias: Simatic S7-1200 El Simatic S7-1200 es un PLC compacto diseñado para aplicaciones de tamaño pequeño a mediano. Ofrece una solución de automatización flexible y rentable con su diseño compacto, comunicación integrada y opciones de programación. Simatic S7-1500 El Simatic S7-1500 es un PLC de alto rendimiento diseñado para aplicaciones de mediana a gran escala. Ofrece funciones avanzadas como control de movimiento, seguridad y protección, lo que lo hace adecuado para tareas de automatización complejas. Simatic S7-300 El Simatic S7-300 es un PLC modular que se puede adaptar fácilmente a una amplia gama de aplicaciones. Ofrece una gran potencia de procesamiento, amplias opciones de comunicación y una amplia gama de módulos de E/S, lo que lo convierte en una opción popular para muchas industrias. Simatic S7-400 El Simatic S7-400 es un PLC de alto rendimiento diseñado para aplicaciones exigentes que requieren una gran potencia de procesamiento y amplias capacidades de comunicación. Ofrece una gran cantidad de módulos de E/S, opciones de redundancia y diagnósticos avanzados, lo que lo hace adecuado para tareas de automatización complejas. Simatic S7-ET 200SP El Simatic S7-ET 200SP es un sistema de E/S remotas compacto que se puede integrar fácilmente con otros PLC Simatic S7. Ofrece un alto grado de flexibilidad, escalabilidad y modularidad, lo que lo hace adecuado para diversas aplicaciones de automatización. Cuando crea un nuevo proyecto en TIA Portal e intenta agregar un nuevo dispositivo, puede encontrar todas las CPU disponibles y compatibles de diferentes familias S7. Consulte la imagen 1. Imagen 1: hay diferentes PLC disponibles en la generación Simatic S7 PLC S7-1200 El Simatic S7-1200 es un PLC versátil y rentable que ofrece una gama de modelos para satisfacer diferentes necesidades de automatización, lo que lo convierte en una opción popular para aplicaciones de tamaño pequeño a mediano. A continuación, se ofrece una descripción general de los diferentes modelos de la serie S7-1200: CPU Simatic S7-1200: Estas son las CPU estándar de la serie S7-1200 y vienen en diferentes versiones, incluidas la CPU 1211C, la CPU 1212C, la CPU 1214C, la CPU 1215C y la CPU 1217C. Ofrecen una funcionalidad más avanzada que los controladores básicos, incluidas interfaces de comunicación integradas y opciones de E/S adicionales. También vienen en diferentes versiones, incluidas DC/DC/DC, DC/DC/RLY, AC/DC/RLY y AC/DC/TC. Tienen una funcionalidad limitada, pero son ideales para tareas de control simples. Simatic S7-1200 Safety Integrated: Esta es una versión con certificación de seguridad del S7-1200 que incluye funciones relacionadas con la seguridad, como entradas de seguridad, salidas de seguridad y comunicación de seguridad, para mejorar la seguridad del sistema de automatización. Simatic S7-1200 SIPLUS: Esta es una versión reforzada del S7-1200 que está diseñada para funcionar en entornos hostiles con temperaturas extremas, humedad y vibración. Vea la imagen 2 para conocer los diferentes modelos del S7-1200. Imagen 2: diferentes modelos de CPU S7-1200 PLC S7-1500 El Simatic S7-1500 es un PLC potente que ofrece una gama de modelos para satisfacer diferentes necesidades de automatización, lo que lo convierte en una opción popular para aplicaciones exigentes. A continuación, se ofrece una descripción general de los diferentes modelos de la serie S7-1500: CPU estándar Simatic S7-1500: Estas son las CPU estándar de la serie S7-1500 y vienen en diferentes versiones, incluidas la CPU 1511-1 PN, la CPU 1513-1 PN, la CPU 1515-2 PN y la CPU 1518-4 PN. Ofrecen procesamiento de alta velocidad y opciones de comunicación avanzadas, como Profinet, Profibus y Ethernet industrial. Simatic S7-1500 Safety Integrated: Esta es una versión con certificación de seguridad del S7-1500 que incluye funciones relacionadas con la seguridad, como entradas de seguridad, salidas de seguridad y comunicación de seguridad, para mejorar la seguridad del sistema de automatización. Controladores avanzados Simatic S7-1500: Se trata de versiones avanzadas del S7-1500 que ofrecen funciones adicionales, como control de movimiento, conteo de alta velocidad y opciones de comunicación avanzadas. CPU T Simatic S7-1500: Se trata de una versión avanzada de las CPU S7-1500 que tienen funciones de control de movimiento ampliadas, como funciones cinemáticas y funciones de engranajes y levas. NPU TM Simatic S7-1500: Se trata de una unidad de procesamiento neuronal (NPU) diseñada para aplicaciones de aprendizaje automático e inteligencia artificial (IA), como mantenimiento predictivo, control de calidad y optimización de procesos. Consulte la imagen 3 para ver los diferentes modelos de S7-1500. Imagen 3: diferentes modelos de S7-1500 PLC S7-300 CPU Simatic S7-300: Estas son las CPU estándar de la serie S7-300 y vienen en diferentes versiones, incluidas la CPU 312C, la CPU 313C, la CPU 314C, la CPU 315-2DP, la CPU 317-2DP y la CPU 319-3PN/DP. Ofrecen una gran potencia de procesamiento, opciones de comunicación avanzadas y una amplia gama de opciones de E/S. CPU Simatic S7-300 Fail-Safe: Estas son versiones con certificación de seguridad de las CPU S7-300 que incluyen funciones relacionadas con la seguridad, como entradas de seguridad, salidas de seguridad y comunicación de seguridad, para mejorar la seguridad del sistema de automatización. CPU compactas Simatic S7-300: Se trata de versiones compactas de las CPU S7-300 que ofrecen un tamaño y un consumo de energía reducidos, lo que las hace ideales para aplicaciones con espacio y suministro de energía limitados. CPU tecnológicas Simatic S7-300: Se trata de CPU especializadas diseñadas para aplicaciones de automatización específicas, como control de movimiento, control de temperatura y control de procesos. Controladores distribuidos Simatic S7-300: Se trata de controladores modulares que ofrecen opciones de comunicación y E/S distribuidas, lo que los hace ideales para aplicaciones que requieren automatización distribuida. Consulte la imagen 4 para conocer los diferentes modelos de S7-300. Imagen 4: diferentes modelos de S7-300 PLC S7-400 CPU Simatic S7-400: Estas son las CPU estándar de la serie S7-400 y vienen en diferentes versiones, incluidas la CPU 412-1, la CPU 414-1, la CPU 414-2, la CPU 416-2 y la CPU 417-4. Ofrecen una gran potencia de procesamiento, opciones de comunicación avanzadas y una amplia gama de opciones de E/S. CPU Simatic S7-400H: Estas son CPU de alta disponibilidad que ofrecen opciones de redundancia para mejorar la disponibilidad y la confiabilidad del sistema de automatización. CPU Simatic S7-400F/FH: Estas son CPU con certificación de seguridad que incluyen funciones relacionadas con la seguridad, como entradas de seguridad, salidas de seguridad y comunicación de seguridad, para mejorar la seguridad del sistema de automatización. Controladores distribuidos Simatic S7-400: Son controladores modulares que ofrecen opciones de comunicación y E/S distribuidas, lo que los hace ideales para aplicaciones que requieren automatización distribuida. Consulte la imagen 5 para conocer los diferentes modelos de S7-400. Imagen 5: diferentes modelos de S7-400 PLC Simatic S7-ET 200 CPU Simatic S7-ET 200: Estas son las CPU estándar de la serie S7-ET 200 y vienen en diferentes versiones, incluidas la CPU 1511C-1 PN, la CPU 1513-1 PN y la CPU 1515-2 PN. Ofrecen una gran potencia de procesamiento, opciones de comunicación avanzadas y una amplia gama de opciones de E/S. CPU Simatic S7-ET 200F: Se trata de CPU con certificación de seguridad que incluyen funciones relacionadas con la seguridad, como entradas de seguridad, salidas de seguridad y comunicación de seguridad, para mejorar la seguridad del sistema de automatización. CPU Simatic S7-ET 200SP: Se trata de CPU compactas que ofrecen un tamaño y un consumo de energía reducidos, lo que las hace ideales para aplicaciones con espacio y suministro de energía limitados. Consulte la imagen 6 para conocer los diferentes modelos de S7-ET200. Imagen 6 – Diferentes modelos de S7-ET200 ¿Por qué hay tantos modelos diferentes? Hay muchos modelos diferentes de PLC S7 de Siemens para ofrecer a los clientes una amplia gama de opciones y características entre las que elegir, lo que les permite seleccionar el PLC que mejor se adapte a sus necesidades de automatización específicas. Los diferentes modelos ofrecen diferentes características, potencia de procesamiento, memoria, opciones de comunicación y capacidades de E/S. Algunos modelos están diseñados para aplicaciones específicas, como control de movimiento, control de temperatura y control de procesos, mientras que otros están diseñados para sistemas de automatización de uso general. Además, a medida que avanza la tecnología y surgen nuevos requisitos de automatización, Siemens continúa desarrollando y lanzando nuevos modelos y versiones de PLC S7 con características y capacidades mejoradas, lo que proporciona a los clientes la última tecnología de automatización para ayudarlos a mejorar su productividad, reducir sus costos y mejorar el rendimiento de su sistema. ¿Cómo decidir qué tipo de PLC S7 se adapta mejor a mi aplicación? La elección del tipo correcto de PLC S7 para su aplicación requiere una consideración cuidadosa de varios factores. A continuación, se indican algunos pasos generales que le ayudarán a decidir qué tipo de PLC S7 se adapta mejor a su aplicación: Determine el tamaño y la complejidad de su sistema de automatización: Si tiene un sistema de automatización grande y complejo, es posible que necesite un PLC de alto rendimiento, como el S7-400 o el S7-1500, que pueda gestionar una gran cantidad de puntos de E/S y opciones de comunicación avanzadas. Si su sistema es más pequeño y menos complejo, un PLC más pequeño, como el S7-1200 o el S7-300, puede ser suficiente. Identifique los tipos de E/S necesarios y cuente: Cada PLC S7 tiene un rango diferente de opciones y capacidad de E/S. Debe determinar el tipo y la cantidad de puntos de E/S que necesita para su aplicación y seleccionar el PLC que pueda admitirlos. Considere la velocidad de procesamiento y el rendimiento necesarios: Los distintos PLC S7 tienen diferentes velocidades de procesamiento y capacidades de rendimiento. Debe determinar la velocidad de procesamiento necesaria y seleccionar el PLC que pueda satisfacer sus requisitos de rendimiento. Evalúe las opciones de comunicación requeridas: Los diferentes PLC S7 ofrecen diferentes opciones de comunicación, como Ethernet, Profibus, Profinet y AS-i. Debe determinar los protocolos de comunicación necesarios para su aplicación y seleccionar el PLC que pueda admitirlos. Considere las características de seguridad requeridas: Si su aplicación requiere funciones de seguridad, como entradas de seguridad, salidas de seguridad y comunicación de seguridad, es posible que necesite un PLC con certificación de seguridad, como el S7-1500F o el S7-400F. Conclusión Siemens ofrece una amplia gama de productos de automatización industrial que incluyen varios modelos de PLC con diferentes funcionalidades y capacidades de rendimiento, incluidas las CPU S7-1200, S7-1500, S7-300 y S7-400. Los diferentes modelos de PLC S7 de Siemens están ahí para brindarles a los clientes una amplia gama de opciones y características para elegir. Elegir el modelo de PLC que mejor se adapte a su Proceso requiere algunos puntos a considerar antes de seleccionar el PLC, algunos de estos puntos son el número de E/S, los requisitos de seguridad y las opciones de comunicación. -
Programación secuencial de PLC para válvulas neumáticas
leizuofa posted A plc and hmi article in Spanish in PLC programming learning
Este es un programa de PLC para el funcionamiento de válvulas neumáticas en modo secuencial. Programación secuencial de PLC para válvulas neumáticas Escriba una lógica de escalera para la programación secuencial de PLC para que las válvulas neumáticas operen cilindros en modo secuencial. Solución: Aquí en este sistema, hay dos cilindros y dos pulsadores que están conectados al PLC. Los pulsadores están conectados a las entradas del PLC y los cilindros están conectados a las salidas del PLC. Existen las siguientes condiciones para que el sistema funcione, que son las siguientes: – Cuando se presiona START PB, el cilindro A debe arrancar y el cilindro B debe arrancar después de 5 segundos del cilindro A. Cuando se presiona STOP PB, se deben detener ambos cilindros A y B. Ahora, para cumplir con las siguientes condiciones, debemos utilizar un temporizador que retrase la operación del cilindro B. Lista de entradas/salidas Entradas: X1 - START PB X2 - STOP PB Salidas: Y0 - Cilindro A Y1 - Cilindro B Diagrama de escalera para la operación secuencial de cilindros Explicación del programa: En el peldaño 1, usamos STRAT PB (X1) para iniciar el cilindro A (Y0). Aquí usamos el contacto NC de STOP PB (X2) para detener el cilindro A (Y0). En paralelo con el contacto X1, usamos el contacto NA de Y0 para bloquear la salida. En el peldaño 2, usamos el temporizador T0 para contar el retraso del cilindro B (Y1). En el peldaño 3, usamos el contacto NA de T0, por lo que una vez que se activa el retraso de tiempo en el cilindro B (Y1). -
SIEMENS-ES ¿Cómo leer la hoja de datos del PLC? – Notas importantes sobre el PLC
leizuofa posted A plc and hmi article in Spanish in PLC programming learning
En este artículo, aprenderemos a leer la hoja de datos del PLC y notas importantes sobre las especificaciones del PLC que son útiles para los ingenieros de automatización. Además, hablaremos sobre qué información diferente se proporciona en una hoja de datos del PLC y cómo puede ser útil para mí como programador o como ingeniero de instalación. Contenido: ¿Qué información proporciona una hoja de datos? Ejemplos de información en una hoja de datos del PLC Valor nominal de corriente y voltaje Memoria del PLC Diferentes bloques y direcciones de áreas de datos Especificaciones de entradas y salidas Interfaces y protocolos de comunicación Condiciones ambientales Notas importantes sobre la lectura de la hoja de datos. ¿Qué información proporciona una hoja de datos? La hoja de datos de un PLC le proporcionará mucha información; esta información cubrirá casi todas las características que puede proporcionar el PLC. Pero parte de esta información no será tan importante para usted como otra, depende de cuál sea su alcance con el PLC. Si usted es el ingeniero de instalación, entonces se centrará en las especificaciones técnicas del PLC, como el voltaje de suministro, el tipo de entradas y salidas y la potencia nominal de estos puntos de E/S. También prestará más atención a la dimensión del PLC y las condiciones ambientales durante el funcionamiento del PLC para determinar el tamaño del panel eléctrico que utilizará para el PLC y también los métodos de enfriamiento utilizados para el PLC. ¿Cómo leer la hoja de datos del PLC? Por otro lado, si usted es solo el programador del PLC, entonces la información anterior puede no ser tan crítica para usted, en cambio, se centrará en los datos relacionados con, por ejemplo, la memoria del PLC, la cantidad de E/S disponibles y la capacidad de agregar nuevos módulos. También prestará atención a otra información como los lenguajes de programación compatibles con ese PLC porque no todos los PLC admiten todos los lenguajes de programación. La comunicación y la red también son otros puntos importantes que le interesarán como programador. La hoja de datos de un PLC siempre comenzará con una descripción general del PLC. Consulte las imágenes 1 y 2 para ver ejemplos sencillos de S7-1200 y S7-1500. Imagen 1: primera página de una hoja de datos de un PLC S7-1500. Imagen 2: primera página de una hoja de datos de un PLC S7-1200. Como puede ver, al principio de la hoja de datos se incluye una descripción general del PLC. Esta descripción general le dará una idea básica sobre el PLC y si se adapta o no a su aplicación. Ejemplos de la información incluida en una hoja de datos de un PLC En este artículo, utilizaremos la hoja de datos de un PLC S7-1200 para mostrar parte de la información que contiene. Corriente nominal y voltaje En una sección determinada de la hoja de datos debe haber información sobre los valores nominales de voltaje y corriente del PLC. Algunos PLC necesitarán una fuente de CC mientras que otros requerirán una fuente de CA. Además, las entradas y salidas del PLC pueden tener valores nominales diferentes, que es exactamente el caso de nuestro PLC, donde el suministro de voltaje al PLC es de 220 CA, pero los valores nominales para las E/S son de CC. Consulte la imagen 3. Imagen 3: valores nominales de voltaje y corriente. Memoria del PLC En la hoja de datos se proporcionarán diferentes capacidades de memoria del PLC. Esto mostrará cuánta memoria de trabajo tiene y si puede expandirla o no. Consulte la imagen 4. Imagen 4: descripción de la memoria del PLC. Diferentes bloques y direcciones de áreas de datos En esta sección, conocerá los diferentes bloques que puede utilizar con su PLC, como temporizadores, contadores, FC, etc. Y el número máximo de bloques que puede utilizar. También se le proporcionará la memoria de las áreas de datos y su retentividad. Consulte la imagen 5. Imagen 5: bloques de CPU disponibles. Especificaciones de entradas y salidas Este es otro dato crítico que se debe proporcionar, a través de esta información sabrá la cantidad de E/S que se proporcionan con su PLC y cómo conectar y utilizar cada E/S. Consulte las imágenes 6 y 7. Imagen 6: entradas digitales del PLC. Como puede ver, tenemos 8 puntos DI en nuestro PLC, 6 de los cuales se pueden utilizar para entradas HSC (conteo de alta velocidad) como codificadores. También te dice que el voltaje de entrada es de 24 VCC, lo que significa que no puedes conectar directamente sensores de CA o entradas al PLC. Imagen 7: nuestro PLC tiene salidas digitales. Si el PLC tiene E/S analógicas, también se mencionará en la hoja de datos. Consulta la imagen 8 Imagen 8: descripción de las E/S analógicas. Interfaces y protocolos de comunicación Las interfaces de comunicación disponibles en tu PLC, así como los protocolos de comunicación que puede admitir, también se mencionarán en la hoja de datos. Consulta la imagen 9. Imagen 9: la interfaz de comunicación del PLC. Como puedes ver, el PLC que tenemos solo tiene una interfaz de comunicación, que es una interfaz PROFINET proporcionada como un puerto RJ-45. Sin embargo, el propio PLC puede admitir muchos protocolos de comunicación, como PROFIBUS y AS-Interface. Ver imagen 10. Imagen 10: Protocolos de comunicación admitidos. Condiciones ambientales Este es otro dato muy importante que debe conocer sobre su PLC, ya que lo ayudará a decidir el tipo de gabinete y refrigeración que mejor se adaptará a su PLC. Consulte la imagen 11. Imagen 11: condición ambiental del PLC. Notas importantes sobre la lectura de la hoja de datos de un PLC No todas las hojas de datos de PLC contienen la misma información, ya que los diferentes PLC tendrán diferentes características y capacidades y, por lo tanto, diferente información para mostrar. No toda la información dentro de la hoja de datos será importante para usted, eso dependerá de si es un programador de PLC o un ingeniero de instalación, como mencionamos anteriormente. Está bien si no comprende parte de la información en la hoja de datos, como dijimos, la hoja de datos proporcionará información sobre casi todas las características admitidas por su PLC, es posible que no conozca algunas de estas características y es posible que ni siquiera necesite usarla. Por ejemplo, las características de OPC UA o del servidor web. Por lo tanto, si encuentra algún dato que no comprende, no significa necesariamente que su PLC no se adapte a su proyecto. Conclusión Leer la hoja de datos del PLC es importante para decidir si el PLC es adecuado para su aplicación o no. También es importante decidir con qué tipos de E/S y valores nominales de suministro de voltaje puede trabajar. Intente leer la hoja de datos de diferentes modelos de PLC y vea si puede comprender la información básica proporcionada en la hoja de datos. -
SIEMENS-ES ¿Cuál es la versión de firmware de un PLC? – Siemens PLC Hardware
leizuofa posted A plc and hmi article in Spanish in PLC programming learning
En este artículo vamos a hablar de un problema importante que ocurre mucho cuando comienzas a programar tu PLC, se trata de los errores comunes de la versión de firmware y cómo manejarlos. Contenido: ¿Cuál es la versión de firmware de un PLC? ¿Por qué la versión de firmware puede causar problemas? ¿Cómo saber la versión de firmware de un PLC de hardware? ¿Cómo manejar los errores de versión de firmware? Conclusiones. ¿Cuál es la versión de firmware de un PLC? El firmware de un PLC o un módulo de PLC (IOs, módulos de comunicación, etc.) es simplemente el software interno instalado en el PLC que es responsable de lo que el hardware puede hacer realmente. Una versión de firmware determinará qué característica interna tiene tu PLC, como los protocolos de seguridad, funciones de optimización internas, mejor manejo del tiempo y otras características y capacidades diferentes. Un PLC con una versión de firmware más antigua tendrá menos características y capacidades internas que un PLC con una versión de firmware más nueva. Las imágenes 1 y 2 muestran cómo el mismo PLC de hardware tendrá diferentes características y capacidades de rendimiento con diferentes versiones de firmware instaladas. Imagen 1: versión de firmware V4.0 Imagen 2: versión de firmware V4.4 ¿Has notado cómo la misma CPU ahora tiene más funciones agregadas con solo actualizar a una versión de firmware más alta? Con la versión de firmware V4.4 más alta, la CPU ahora tiene OPC UA, entre otras funciones agregadas a sus capacidades de rendimiento. ¿Por qué la versión de firmware puede causar problemas? Mira, normalmente comienzas tu proyecto de PLC seleccionando el PLC y luego comienzas a programar. Seleccionarás tu PLC en TIA Portal de acuerdo con uno de dos puntos: Ya has comprado el PLC de hardware, por lo que seleccionarás el mismo PLC que tienes en el proyecto de TIA Portal. Todavía no has comprado un PLC, por lo que seleccionarás un PLC en TIA Portal que cumpla con tus requisitos y luego lo comprarás más tarde. En cualquiera de los dos casos, si la versión de firmware del PLC seleccionado en el proyecto de TIA Portal es diferente de la versión de firmware del hardware real, tendrá un problema. Y su programa ni siquiera se descargará al PLC de hardware. Por lo tanto, siempre debe asegurarse de que la versión de firmware del PLC real coincida con el PLC seleccionado en TIA Portal. Vale la pena mencionar que si la versión de firmware seleccionada en TIA Portal es anterior a la del PLC real, no tendrá problemas con su programa, perderá algunas de las características y capacidades del PLC, pero su programa funcionará bien. Los problemas aparecerán si ocurre lo contrario, si la versión de firmware seleccionada en TIA Portal es más reciente que la del PLC real, entonces tendrá un problema. Por eso, si no conoce la versión de firmware de su hardware, debe seleccionar la versión anterior en el proyecto de TIA Portal. ¿Cómo saber la versión de firmware del PLC de hardware? Podemos conocer la versión de firmware del PLC de hardware que tenemos mediante uno o dos métodos: Desde el propio PLC La versión de firmware de cualquier módulo PLC siempre está escrita en algún lugar del dispositivo de hardware. Vea las siguientes imágenes. Imagen 3: versión de firmware FS:04 Imagen 4: la versión de firmware es V7.0.5 Desde el software TIA Portal Usando el software TIA Portal puede conectar su PLC a su TIA Portal y buscar el dispositivo, luego puede encontrar la versión de firmware del dispositivo de hardware, vea los siguientes pasos. Ni siquiera tiene que crear un nuevo proyecto; solo la vista de proyecto de TIA Portal es suficiente, vea la imagen 5. Imagen 5: Vista de proyecto de TIA Portal sin crear un proyecto. Desde el acceso en línea, busque su PLC. Como la conexión entre el TIA Portal y el PLC se realiza a través de un cable Ethernet, utilizaremos la opción de conexión Ethernet. Haga doble clic en Actualizar dispositivos accesibles para comenzar a buscar su PLC. Consulte la imagen 6. Imagen 6: Actualizar dispositivos accesibles para buscar su PLC. Si hay una conexión entre el PLC y el TIA Portal, el software debería encontrar su PLC. Consulte la imagen 7. Imagen 7: El software encontró su PLC. Ahora, haga doble clic en En línea y diagnóstico para mostrar la información de su PLC. Consulte la imagen 8. Imagen 8: Información en línea del PLC. En el atributo General, puede encontrar la versión de firmware de su PLC como se muestra en la imagen anterior. También puede encontrar la versión de firmware en el atributo Funciones. Consulte la imagen 9. Imagen 9: versión de firmware del atributo de funciones. ¿Cómo manejar los errores de versión de firmware? Primero, creemos un escenario de error de versión de firmware y luego veremos cómo manejar y solucionar este error. Comenzaremos simplemente creando un nuevo proyecto y luego agregando un nuevo dispositivo. En este ejemplo de PLC, elegiremos intencionalmente una versión de firmware más nueva que la del hardware del PLC real. Sabemos que el firmware de nuestro PLC es V4.0, pero en TIA Portal elegiremos la versión de firmware V4.4. Vea la imagen 10. Imagen 10: agregue un nuevo PLC con una versión de firmware más alta. Presione OK para agregar su dispositivo y eso es todo, ha creado una situación que provocará un error de firmware. Para ver eso, intentemos descargar el proyecto a nuestro PLC. Tenga en cuenta que ni siquiera hemos escrito ningún código. Simplemente descargémoslo al PLC. Vea la imagen 11. Imagen 11: Error en la descarga al PLC, firmware incompatible. Como se puede ver en la imagen anterior, una vez que se intenta descargar el proyecto al PLC, aparecerá un error que indica que las versiones de firmware del PLC y del TIA Portal no coinciden. Incluso se puede ver si se intenta acceder a Internet. Ver imagen 12. Imagen 12 – El PLC se encuentra en estado de error. Para solucionar este error, simplemente debemos cambiar la versión de firmware del PLC seleccionado en el proyecto TIA Portal a una versión anterior o igual al firmware del PLC de hardware actual. Para ello, vamos a la página de propiedades del PLC y seleccionamos Cambiar versión de firmware en el atributo General. Ver imagen 13. Imagen 13 – Cambiar la opción de versión de firmware. Una vez que se pulsa el botón Cambiar versión de firmware, aparecerá una ventana de cambio de dispositivo; en esta ventana, se podrá cambiar la versión de firmware. Consulte la imagen 14. Imagen 14: ventana de cambio de dispositivo. En la ventana de cambio de dispositivo, verá el dispositivo actual que ha seleccionado antes y el nuevo dispositivo cuyo firmware necesita que coincida con el que tiene actualmente. Tenga en cuenta que, al elegir un firmware inferior, por ejemplo V4.3, la información en la parte inferior de la ventana le mostrará qué características ha perdido al pasar a un firmware inferior, como se ve en la imagen anterior. Ahora, cambie el firmware del nuevo dispositivo a la versión V4.0 del PLC de hardware. Y observe cuántas características y capacidades ha perdido el PLC simplemente por elegir un firmware inferior. Consulte la imagen 15. Imagen 15: Coincidencia del firmware entre el PLC de hardware y el software. Presione OK para confirmar los cambios y ahora intente descargar su proyecto una vez más al PLC. Notará que ahora el proyecto se cargará en el PLC sin ningún error. Consulte la imagen 16. Imagen 16: el proyecto se carga en el PLC. Una carga exitosa del proyecto en el PLC indica que el error de versión de firmware ahora está solucionado. También puede conectarse a Internet y verificarlo desde la vista en línea del proyecto del PLC. Consulte la imagen 17. Imagen 17: vista en línea del proyecto. Las marcas de verificación y los círculos verdes que ve en la imagen anterior indican que todas las configuraciones del software y el hardware coinciden y son compatibles entre sí. Conclusión Los errores de versión de firmware son un problema muy común al que se enfrenta al crear un nuevo proyecto en TIA Portal. Una práctica recomendada es conocer la versión de firmware del dispositivo de hardware que tiene y hacer coincidir el firmware con el dispositivo seleccionado en TIA Portal. Si no conoce el firmware del dispositivo de hardware, debe elegir la versión más antigua del módulo seleccionado dentro de TIA Portal para evitar problemas de firmware con su proyecto. -
SIEMENS-ES PLC Siemens que utiliza bits de memoria de reloj en TIA Portal
leizuofa posted A plc and hmi article in Spanish in PLC programming learning
En este artículo, hablaremos sobre los bits de memoria de reloj en TIA Portal y Siemens PLC. Y mostraremos cómo habilitar el uso de los bits de memoria y cómo puede ayudarlo a evitar codificar muchas líneas lógicas para obtener una función simple que su PLC ya realiza internamente. Contenido: ¿Qué son los bits de memoria de reloj? La necesidad de bits de memoria de reloj. Habilitar la memoria de reloj en mi proyecto. Ejemplo de programa simple. Simulación de programa. Conclusión. ¿Qué son los bits de memoria de reloj? Una memoria de reloj es una memoria de bits que cambia su estado binario periódicamente en una proporción de 1:1. Eso simplemente significa que cambia su estado periódicamente entre verdadero y falso con una frecuencia predefinida. Hay 8 bits de memoria de reloj predefinidos en la CPU, por lo que también se los llama byte de memoria de reloj. Usted decide qué byte de memoria de la CPU se convertirá en el byte de memoria de reloj cuando habilita el uso del byte de memoria y asigna los parámetros de memoria de reloj. La necesidad de bits de memoria de reloj No es necesario que tenga memoria de reloj, ya que puede crear su propia lógica y lograr la misma funcionalidad. Sin embargo, es bueno tenerla en el bolsillo cuando necesite dicha funcionalidad, ya que crear 8 lógicas independientes para 8 bits de memoria de reloj le llevará algo de tiempo y esfuerzo y puede hacer que su programa sea innecesariamente grande. Puede utilizar la memoria de reloj, por ejemplo, para activar luces indicadoras intermitentes o para iniciar operaciones periódicas recurrentes, como registrar valores reales. A cada bit del byte de memoria de bit de reloj se le asigna una frecuencia. Consulte la siguiente tabla. Bit del byte de memoria de reloj 7 6 5 4 3 2 1 0 Periodo (s) 2.0 1.6 1.0 0.8 0.5 0.4 0.2 0.1 Frecuencia (Hz) 0.5 0.625 1 1.25 2 2.5 5 10 Tabla 1. Frecuencias de los bits de memoria de reloj según el manual de ayuda del TIA Portal. Habilitar la memoria de reloj en el PLC de Siemens Para utilizar los bits de memoria de reloj en su lógica, debe habilitar el uso del byte de memoria de reloj desde las propiedades de la CPU. Consulte la imagen 1. Imagen 1: Habilitar el uso del byte de memoria de reloj Puede elegir la dirección del byte que desea asignar para la memoria de reloj, solo asegúrese de que no entre en conflicto con ningún otro byte de memoria en la lógica de su PLC. Como puede ver en la imagen, elegimos la dirección 0, por lo que si necesita usar el bit de reloj de 2 Hz, usará el bit %M0.3 Programa de ejemplo de cinta transportadora Tia Portal En un artículo anterior, usamos un ejemplo simple de una cinta transportadora que mueve un producto entre el inicio y el final de la cinta. Había un LED de indicación que se enciende cuando la cinta está en funcionamiento. Vea la imagen 2. Imagen 2: sistema de cinta transportadora simple Usaremos el mismo ejemplo, pero esta vez haremos que el LED sea más intuitivo usando los bits de memoria de reloj. Esta vez usaremos los bits de memoria de reloj con el LED para dar una indicación de diferentes casos del proceso. Descripción del Proceso En un sistema de cinta transportadora controlado por un PLC, existen dos sensores de presencia en los dos extremos de la cinta para detectar la presencia de un producto, cuando el producto se detecta al inicio de la cinta, el transportador puede iniciarse a través de un pulsador de inicio y cuando el producto llega al final la cinta se detendrá automáticamente y no volverá a funcionar hasta que se detecte nuevamente un nuevo producto al inicio y se presione el pulsador de INICIO. El LED de indicación debe tener más de un comportamiento dependiendo del caso actual del sistema. Estos casos son los siguientes: Si hay un producto al inicio de la cinta pero aún no se presiona INICIO, el LED debe parpadear con una frecuencia de 0,5 Hz. Si el transportador está moviendo el producto, el LED debe parpadear con una frecuencia de 2 Hz. Cuando el producto llega al final de la cinta, el LED debe estar ENCENDIDO Cuando se retira el producto del final, el LED se APAGA. IOs del proyecto Tenemos 4 entradas digitales de la siguiente manera: START: pulsador de arranque para poner en marcha el transportador. STOP: pulsador de parada para parar el transportador en cualquier momento. P1: sensor de presencia al inicio de la cinta. P2: sensor de presencia al final de la cinta. También tenemos 2 salidas digitales de la siguiente manera: MOTOR: al activarse la cinta transportadora empezará a funcionar. LED: se activará según la secuencia mencionada anteriormente. Código de programa Primero, seleccionamos nuestro PLC y asignamos las etiquetas de IO. Ver imagen 3 Imagen 3 – Asignar etiquetas de entradas y salidas No olvides habilitar el uso del byte de memoria de reloj como se muestra en la imagen 1. Tendremos dos redes de código, una para el control de la cinta transportadora y otra para la lógica de los LED. Ver imágenes 4 y 5 para la lógica. Imagen 4: La lógica de control de la cinta transportadora Imagen 5: La lógica de control del LED Como puede ver, el uso de los bits de memoria del reloj hizo que la lógica fuera simple y fácil de leer. Imagínese si creara la misma lógica sin el uso de estos bits, habría utilizado muchos temporizadores y su lógica habría sido bastante complicada. Simulación del programa Explicamos anteriormente cómo utilizar el PLCSim para simular nuestro código. En este ejemplo, utilizaremos la secuencia de simulación para crear la misma secuencia del proceso real y veremos si el comportamiento del LED coincide con la funcionalidad deseada o no. Comience compilando nuestro código e inicie una nueva simulación. Vea la imagen 6. Imagen 6: simulación del programa Como puede ver, el LED ahora está APAGADO; no hay presencia de productos al principio ni al final de la cinta transportadora. Creamos una secuencia de simulación y vemos cómo reaccionará el LED a diferentes condiciones del proceso. Vea la siguiente animación. Vea si puede notar cómo cambia el comportamiento del LED con diferentes condiciones del proceso. Conclusión Los bits de memoria del reloj se encienden y apagan con una frecuencia predefinida. Son muy útiles cuando necesita activar luces indicadoras intermitentes o iniciar operaciones que se repiten periódicamente. El uso de bits de memoria de reloj le ahorrará el tiempo y el esfuerzo consumidos para obtener la misma funcionalidad a través de su propia lógica. -
¿Qué son las entradas analógicas? – Procesamiento de señales analógicas en PLC
leizuofa posted A plc and hmi article in Spanish in PLC programming learning
En este artículo, hablaremos sobre el procesamiento de señales de entrada analógicas en PLC y cómo podemos manejar estas señales en el proceso de automatización. Contenido: ¿Qué son las señales de entrada analógicas? Procesamiento analógico de entrada en S7-1200 y 1500. Procesamiento analógico de entrada en S7-300 y 400. ¿Cuáles son las mejores para el control? – Señales analógicas o digitales Conclusión. ¿Qué son las señales de entrada analógicas? Antes de profundizar en cómo manejar las señales de entrada analógicas en TIA Portal, comencemos por comprender las entradas analógicas. Todo sistema de automatización necesita señales de entrada para comprender el estado del proceso para poder tomar decisiones que mantendrán el proceso en funcionamiento y estable. Estas señales de entrada son señales de entrada discretas o digitales que tienen la forma de valores 0 o 1. El otro tipo de entrada son las señales analógicas. Una señal analógica es simplemente una representación continua de una cantidad física en su sistema, por lo que si necesita monitorear la temperatura o la presión en su proceso, una señal analógica le brindará valores continuos e instantáneos que corresponden a los cambios reales en la cantidad física. Las señales analógicas se proporcionan en muchas formas estándar, pero las más comunes son 0-10 V o 4-20 mA. Dependerá del tipo de sensor analógico que esté utilizando y también determinará el tipo de módulo analógico de PLC que puede utilizar. Supongamos que tenemos un sensor de presión analógico que tiene un rango de medición de 0-10 bar y una salida en forma de 4-20 mA. Por lo general, una señal analógica tendrá una relación lineal entre la cantidad física medida y la salida correspondiente. Eso significa que si el sensor mide 0 bar, dará una señal de 4 mA y si mide 10 bar, dará una señal de 20 mA y lo mismo entre ambos también será lineal. Consulte la imagen 1. Imagen 1: representación de la señal analógica. El PLC aún no puede comprender los 4-20 mA de la cantidad física, y aquí entra en juego el uso del módulo analógico del PLC. El módulo analógico realizará otra transformación a esta representación para que el PLC pueda comprenderla. El módulo analógico convertirá las mediciones analógicas de mA en valores digitales que dependen del tipo de módulo, pero para el PLC Siemens, estos valores siempre están en el rango de 0 a 27648. Por lo tanto, si el sensor mide 0 bar, la salida será de 4 mA y se convertirá en un valor 0 dentro del PLC. Consulte la imagen 2. Imagen 2: conversión analógica a digital de la señal de entrada El PLC convertirá entonces los valores de 0 a 27648 en la medición física equivalente según su programación, a la que llegaremos más adelante. Consulte la imagen 3. Imagen 3: el valor medido escalado dentro del PLC. El procesamiento analógico de las temperaturas es bastante diferente porque el comportamiento del sensor de temperatura con los cambios físicos no es lineal como lo haría un sensor de nivel o de presión. Es por eso que existen tablas estandarizadas para los diferentes tipos de sensores de temperatura que indican qué temperatura corresponde a qué valor del sensor. Es por eso que, con la medición de temperatura, seleccionaría tipos especiales de módulos de entrada de su PLC donde estas tablas estándar se definen internamente y obtendrá directamente el valor de temperatura correspondiente a la medición del sensor. Es por eso que no puede encontrar un sensor de temperatura que tenga escrito un rango de medición de voltaje o corriente. Solo encontrará escrito el tipo de sensor, por ejemplo, PT100, PT1000, KTY84, PTC, etc. Procesamiento de entradas analógicas en S7-1200 y 1500 Para ver cómo manejamos las señales analógicas en los PLC de la familia S7 modernos, comencemos por crear un nuevo proyecto y agregar una CPU S7-1200. También agregaremos un módulo de entrada/salida analógica. Ver imagen 4. Imagen 4: Agregar un módulo de entrada analógica. Ahora, definamos nuestra etiqueta de señal de entrada. Supondremos un sensor de presión que puede medir la presión entre 0 y 10 bares y da una señal correspondiente entre 4 y 20 mA. Definiremos esa señal de entrada en las primeras etiquetas del módulo de entrada. Ver imagen 5. Imagen 5: Definir la etiqueta de señal de entrada. Como dijimos antes, el módulo de entrada puede trabajar con diferentes señales de entrada, ya sea 0-10 V o 4-20 mA, por lo que debemos asignar la configuración correcta para nuestro sensor. Como hemos dicho, la señal de presión se da en forma de 4-20 mA, por lo que configuraremos nuestro canal de entrada para ello. Ver imagen 6. Imagen 6 – Configurar el canal de entrada Ahora que hemos terminado la parte de configuración del hardware, comenzaremos a programar nuestro código de manejo. Para ello, crearemos una función FC para que podamos reutilizarla cada vez que tengamos una señal analógica para procesar. Dentro de esta FC crearemos la lógica que manejará la señal analógica y la convertirá en el valor medido físico. En TIA Portal hay instrucciones predefinidas que podemos usar para hacer exactamente eso, estas instrucciones son las instrucciones NORM_X y SCALE_X. Ver imagen 7. Imagen 7 – Instrucciones NORM_X y SCALE_X Como puede ver, NORM_X normalizará la entrada analógica a un valor entre 0 y 1, y luego se utilizará SCALE_X para escalar este valor normalizado al rango del valor físico medido, que en nuestro caso del sensor está entre 0 y 10 bares. Usamos una función FC en lugar de escribir nuestro código directamente en el OB1 principal para que nuestro código sea reutilizable con cualquier señal analógica. Cada vez que tengo una nueva señal de entrada analógica, simplemente arrastro y suelto el bloque FC en nuestro OB1 principal y escribo los parámetros asociados de la entrada requerida. Vea la imagen 8. Imagen 8: arrastre y suelte su FC. Cuando arrastre y suelte el FC en su OB1 principal, se le solicitará que proporcione el parámetro asociado de esta llamada de función. En nuestro caso, la señal de entrada es el sensor de presión y ScaledMIN y ScaledMAX son el rango de valores de medición de 0 a 10 bares. Consulte la imagen 9. Imagen 9: Asignación de los parámetros de función a nuestro sensor de presión. Si tengo una nueva entrada analógica, no tendré que volver a crear la lógica del PLC, simplemente arrastraré y soltaré la FC en el OB1 principal y asignaré los nuevos parámetros del sensor. Supongamos que ahora tenemos un nuevo sensor analógico para medir el nivel dentro de un tanque de agua entre el 0 y el 100 % del tanque. Realizaremos los mismos pasos que antes, comenzando por definir la nueva etiqueta de entrada. Consulte la imagen 10. Imagen 10: Definir un nuevo sensor de nivel A continuación, configuraremos el canal de entrada para el sensor de nivel como lo hicimos en la imagen 6. Supondremos la misma configuración. A continuación, simplemente arrastraremos y soltaremos la FC que creamos y simplemente asignaremos los parámetros del sensor de nivel. Vea la imagen 11. Imagen 11: reutilización de la FC con el sensor de nivel. Como puede ver en la imagen anterior, esta es una de las muchas ventajas de usar funciones FC en su lógica, ya que ayudó a reducir la cantidad de programación que realizamos. Ahora tiene un código genérico que se puede reutilizar muchas veces con cualquier señal analógica de entrada que pueda necesitar en su proyecto de PLC. Vea la siguiente simulación para el procesamiento de señales de entrada en un PLC Siemens. Entradas analógicas en S7-300 y S7-400 Para ver cómo manejamos las señales analógicas en los PLC de la familia S7 más antiguos, como el S7-300, comencemos por crear un nuevo proyecto y agregar una CPU S7-300. El PLC elegido ya tiene suficientes canales de entrada analógica, por lo que no agregaremos ningún módulo analógico. Consulte la imagen 12. Imagen 12: agregue un PLC S7-300. Luego definiremos la nueva etiqueta del sensor analógico; asumiremos un sensor de presión que tiene un rango de medición entre 0 y 100 bar y una salida de 4-20 mA. Configuraremos el canal de entrada del PLC como lo hicimos antes con el S7-1200 para que se ajuste a nuestro sensor de entrada analógico. Consulte la imagen 13. Imagen 13: configure el canal de entrada. Ahora, en cuanto a la parte de codificación del PLC, la instrucción en el s7-300 que se usa para manejar el procesamiento analógico es diferente a la del s7-1200. En los PLC S7-1200, tenemos que usar NORM_X y SCALE_X, pero con el S7-300 no tenemos la instrucción normalizada, solo se usa una instrucción SCALE. Consulte la imagen 14. Imagen 14: instrucción SCALE en S7-300 Como puede ver en la imagen anterior, la instrucción SCALE en S7-300 es similar a las instrucciones NORM_X y SCALE_X combinadas. Existe otra diferencia clara que es la entrada BIPOLAR. La entrada BIPOLAR se utiliza para indicar si el valor en el parámetro IN debe interpretarse como bipolar o unipolar. El parámetro puede asumir los siguientes valores: BIPOLAR = 1, entonces se supone que el valor entero de entrada está entre -27648 y +27648. Por ejemplo, cuando el sensor analógico nos da una salida en el rango de -10 V a +10 V BIPOLAR = 0, entonces se supone que el valor entero de entrada está entre 0 y 27648. Por ejemplo, cuando el sensor nos da una salida en el rango de 0 a 10 V Y así es simplemente cómo manejar las señales de entrada analógicas en los PLC S7-1200 y S7-300. ¿Cuáles son mejores para el control? Señales analógicas o digitales Mira, ambas señales son críticas y útiles para cualquier sistema de automatización, pero personalmente prefiero usar las señales analógicas si puedo, porque tener mediciones de señales analógicas para las cantidades físicas del proceso me dará un monitoreo continuo de los parámetros del proceso que me permitirá rastrear y controlar mejor mi proceso. Además, tener un monitoreo continuo de los parámetros me permitirá establecer una lógica de control diferente para diferentes valores de señal, lo que hará que sea más fácil tener un rango de valores para controlar el proceso y otros rangos de valores para alarmas y advertencias del proceso que se desvían del funcionamiento normal. Conclusión Una señal analógica es una representación continua de una cantidad física en su sistema. Las entradas analógicas se proporcionan más comúnmente en el rango de 0 a 10 V o de 4 a 20 mA. El procesamiento de señales analógicas significa convertir la señal analógica de 4 a 20 mA en un rango de valores que corresponde a la cantidad física real y que el PLC puede comprender. En la familia de PLC S7 moderna, como S7-1200, el manejo de señales analógicas se realiza mediante las instrucciones NORM_X y SCALE_X. En la familia de PLC S7 más antigua, como S7-300, el manejo de señales analógicas se realiza mediante la instrucción SCALE, que es básicamente una combinación entre las instrucciones NORM_X y SCALE_X. -
SIEMENS-ES ¿Cómo obtener una copia de seguridad del programa de un PLC físico Siemens?
leizuofa posted A plc and hmi article in Spanish in PLC programming learning
En este artículo, le mostraremos cómo realizar una copia de seguridad del programa desde el PLC físico a su computadora utilizando el software del portal Siemens Tia. Contenido: ¿Por qué necesitaría realizar una copia de seguridad? ¿Cómo realizar una copia de seguridad del PLC? Notas sobre la copia de seguridad del PLC Conclusión ¿Por qué necesitaría realizar una copia de seguridad? Imagínese si eliminara accidentalmente su software de la PC mientras trabajaba en él. O tal vez necesite realizar una actualización de cierto software de proceso que ha estado ejecutándose durante 10 años y ya no tiene el código del software. En lugar de reescribir todo el código desde cero, será más fácil simplemente cargar el código actual y realizar los cambios. En este artículo, le mostraremos cómo cargar fácilmente el software contenido dentro del PLC a su PC. ¿Cómo realizar una copia de seguridad del PLC? TIA Portal con los nuevos controladores Siemens S7-1200 y S7-1500 ofrece más ventajas a la hora de realizar una copia de seguridad en comparación con los controladores más antiguos, como el S7-300 o el S7-400. Con los controladores más antiguos, realizaría la copia de seguridad, pero no mostraría ningún comentario ni detalles de direccionamiento; el software funcionará bien, pero será difícil de leer o comprender. Con los controladores PLC más nuevos, ahora puede cargar tanto el código como todo el direccionamiento y los comentarios asociados, lo que hará que la lectura del código sea muy sencilla y que sea posible realizar cualquier actualización. Pasos para cargar el software desde el PLC Cree un nuevo proyecto, pero a diferencia de lo que hacemos habitualmente, no agregaremos un nuevo dispositivo, sino que presionaremos Online y elegiremos “cargar dispositivo como una nueva estación”. Vea la imagen 1. Imagen 1: cargue el dispositivo como una nueva estación. Esto lo llevará a cargar el dispositivo en la ventana PG/PC. Consulte la imagen 2. Imagen 2: ventana de carga de dispositivos. Debe elegir el tipo de interfaz PG/PC como se muestra en la última imagen y luego presionar Iniciar búsqueda. Cuando finalice la búsqueda, verá todos los dispositivos que encontró su software. Tenga en cuenta que no es necesario buscar solo PLC; también podrá encontrar HMI, módulos IO y cualquier otro módulo de comunicación que el software pueda detectar. Consulte la imagen 3. Imagen 3: escaneo completo y dispositivos encontrados. Una vez que se complete el escaneo, puede seleccionar el PLC que necesita cargar y luego presionar Cargar. Esto comenzará a cargar el software desde el PLC a su TIA Portal. Consulte la imagen 4. Imagen 4: se completó la carga desde el PLC. Como puede ver en la imagen anterior, el proyecto completo guardado en el PLC se cargará en su TIA Portal. Incluso con todos los comentarios y direcciones. Vea la imagen 5. Imagen 5: se carga el proyecto del PLC Como puede ver, se cargó todo el proyecto del PLC desde el PLC a su PC. Con todos los bloques, comentarios y configuraciones del proyecto. Notas sobre la copia de seguridad desde el PLC Si su PC y el PLC tienen direcciones IP diferentes, el TIA Portal le solicitará que asigne una nueva IP para su PC que coincida con la dirección del PLC e incluso lo hará automáticamente, si lo permite. Si el proyecto en el PLC está protegido con contraseña, se le solicitará que escriba esta contraseña antes de que comience el paso de carga. Si no puede proporcionar la contraseña correcta, la carga no comenzará. Asegúrese de saber la contraseña, si la tiene. A veces, TIA Portal encuentra su PLC, pero no puede cargar el proyecto debido a diferentes razones; por ejemplo, el proyecto en el PLC está escrito en una versión de TIA Portal diferente a la que está utilizando en este momento. De cualquier manera, se le mostrará el motivo de la carga fallida y podrá cargar el proyecto una vez que se solucionen estos motivos. Conclusión Puede cargar el proyecto en el PLC a su PC mediante TIA Portal. Si el PLC es s7-1200 o s7-1500, el proyecto se cargará con todas las direcciones y comentarios asociados. Si hay alguna razón que impida que TIA Portal cargue el proyecto, TIA Portal le mostrará este motivo y podrá cargarlo una vez que solucione el problema. -
¿Qué lenguaje es mejor para la programación de PLC?
leizuofa posted A plc and hmi article in Spanish in PLC programming learning
Cuando escuchas sobre la programación de PLC, los cinco lenguajes utilizados en ella son: lógica de escalera, texto estructurado, diagrama de bloques funcionales, diagrama de flujo secuencial y lista de instrucciones. Cualquier lenguaje, una vez entendido, se puede utilizar para escribir un código de aplicación y hacer funcionar una máquina correctamente. El mejor lenguaje de programación de PLC Figura: ejemplo de lógica de escalera Pero a menudo, los nuevos programadores de PLC se confunden en cuanto a qué usar para escribir un programa. Si entiende las ventajas y desventajas de un lenguaje, entonces puede determinar fácilmente qué usar para escribir un programa de PLC. Por lo tanto, es necesario comprender la diferencia entre ellos y definir qué lenguaje usar para codificar. En esta publicación, veremos qué lenguaje es mejor para la programación de PLC. Lógica de escalera La lógica de escalera es el tipo más básico de lenguaje de programación de PLC. Se puede correlacionar fácilmente con un diagrama de control de cableado eléctrico. Tradicionalmente, el cableado de control eléctrico se usaba para operar salidas de acuerdo con las entradas proporcionadas. El diagrama de lógica de escalera que consta de contactos y bobinas se implementó de la misma manera en la programación de lógica de escalera. Tiene una serie de peldaños, cada uno de los cuales tiene contactos y bobinas. Cuando se enciende el peldaño, la bobina, según su tipo, funciona en consecuencia. Puede escribir tantos peldaños como necesite en un programa y el código se ejecutará en consecuencia. Cuando lo ve, el parecido es similar a una escalera y, por lo tanto, se le da el nombre de lógica de escalera. Consulte el diagrama a continuación para comprenderlo. Puede ver lo simple que es hacerlo. En la ilustración anterior, las entradas asociadas con un dispositivo de conmutación en el diagrama de lógica de relé se muestran como contactos en el diagrama de escalera. La bobina de salida M1 en el diagrama de lógica de relé se representa con un símbolo de bobina de salida en el diagrama de escalera. Los números de dirección que aparecen sobre cada símbolo de contacto/bobina en el diagrama de escalera son referencias a las ubicaciones de las conexiones de entrada/salida externas al controlador lógico. Entonces, entre dos rieles de potencia de extremo, puede colocar los elementos necesarios y escribir la lógica en ellos. Los peldaños se ejecutan de manera cíclica de arriba hacia abajo. Texto estructurado Se puede decir que el texto estructurado es el lenguaje de nivel de TI local. La semejanza del lenguaje de texto estructurado es muy similar a los códigos que escribimos en un lenguaje de software. Como su nombre lo indica, el texto estructurado es una serie de textos escritos en forma de asignación. Las instrucciones deben terminar con punto y coma. Cuando se realiza una asignación, el valor actual de una variable de uno o varios elementos se reemplaza por el resultado de la evaluación de la expresión. Una asignación consiste en una especificación de variable en el lado izquierdo, seguida del operador de asignación: =, seguido de la expresión a evaluar. Ambas variables (lados izquierdo y derecho del operador de asignación) deben tener el mismo tipo de datos. Consulte el diagrama a continuación para comprender. Como puede ver, tiene diferentes tipos de operaciones y condiciones. En el ejemplo anterior, se utiliza una declaración if-else para evaluar una expresión. Si la condición es verdadera, entonces la variable asignada en el lado de salida se activa y cuando la condición se vuelve falsa, entonces la variable se desactiva. El lenguaje ST es, por lo tanto, el mejor para los cálculos matemáticos, ya que parece sobrio y fácil de entender. Diagrama de flujo secuencial Un diagrama de flujo secuencial es la herramienta más avanzada cuando desea escribir programas complejos de manera repetitiva o secuencial. Como su nombre lo indica, el lenguaje SFC le permite escribir un programa a través de un diagrama de flujo. Funciona en pasos, ramas, enlaces, saltos y transiciones. Una sección SFC es una "máquina de estado", es decir, el estado lo crea el paso activo y las transiciones transmiten el comportamiento de conmutación/cambio. Los pasos y las transiciones están vinculados entre sí a través de enlaces direccionales. Dos pasos nunca pueden vincularse directamente y siempre deben estar separados por una transición. Los procesos de estado de señal activa tienen lugar a lo largo de los enlaces direccionales y se activan al cambiar una transición. Consulte la siguiente imagen para comprender. La dirección del proceso de la cadena sigue los enlaces direccionales y se extiende desde el final del paso anterior hasta el principio del siguiente paso. Las ramificaciones se procesan de izquierda a derecha. Cada paso tiene cero o más acciones. Se necesita una condición de transición para cada transición. La última transición de la cadena siempre está conectada a otro paso de la cadena (a través de un enlace gráfico o símbolo de salto) para crear un bucle cerrado. Por lo tanto, las cadenas de pasos se procesan cíclicamente. Diagrama de bloques funcionales El lenguaje de diagrama de bloques funcionales (FBD) que se utiliza generalmente en microprocesadores, también está disponible en un formato similar en la programación de PLC. Es un diagrama de bloques conectados entre sí, donde cada bloque tiene su entrada y salida. El lenguaje FBD es muy fácil de solucionar porque literalmente puedes ver todo el código en una sola vista, en lugar de desplazarte hacia arriba y hacia abajo. Esto ayuda a un mantenimiento rápido y también aumenta la eficiencia de la programación. Consulta la siguiente imagen para comprender. Como puedes ver, puedes conectar varios tipos de funciones y bloques fácilmente por líneas, lo que muestra cómo se produce un flujo en la lógica. Solo tienes que asignar pines de entrada y salida, conectar las líneas entre estos pines y tu código funciona en consecuencia. Lista de instrucciones Un programa escrito en lenguaje de lista de instrucciones consta de una serie de instrucciones que el controlador lógico ejecuta secuencialmente. Cada instrucción está representada por una sola línea de programa y consta de los siguientes componentes: número de línea, valor actual que solo se puede ver en línea, operador de instrucción y operando. Consulta la siguiente imagen para comprender. Puedes ver que cada línea ejecuta solo una operación. En lugar de los contactos y bobinas que se utilizan en la lógica de escalera, se utilizan instrucciones de carga e instrucciones de configuración/reinicio correspondientes. Es una mezcla de lógica de escalera y texto estructurado. Por eso, también se le llama similar a un lenguaje ensamblador. Cuando te conectas al PLC, puedes ver valores animados en esta ventana. Cuando vemos estos cinco lenguajes, vemos que los que más utilizan los programadores son la lógica de escalera, el texto estructurado y el diagrama de bloques funcional. Cada lenguaje tiene sus ventajas y desventajas. Pero estos tres son fáciles de entender, interpretar y diseñar. Esto ayuda al programador a diseñar la lógica correctamente. Eso no significa que los dos lenguajes restantes no se utilicen. Depende de las habilidades del programador lo que tenga que usar para implementar la codificación. Por lo tanto, es difícil comentar cuál es el mejor lenguaje; pero sí, de estos tres también, el más utilizado es la lógica de escalera. -
Actualización y migración de sistemas PLC
leizuofa posted A plc and hmi article in Spanish in PLC programming learning
Tanto si se trata de automatización industrial como de cualquier otro sistema PLC, todos los dispositivos o equipos llegan a una etapa después de un cierto período de tiempo en la que surge la necesidad de cambiarlos o actualizarlos. Actualización y migración Un PLC, si se utiliza durante más de 10 años, por ejemplo, llegará a una etapa en la que ya no tendrá soporte técnico o no estará disponible para su reemplazo porque se habrá vuelto obsoleto. En este caso, le quedan dos opciones: migrar a un conjunto de PLC completamente nuevo o actualizar el firmware y el programa. Es muy importante comprender esta diferencia, ya que ayuda a elegir el trabajo adecuado para el mismo. En esta publicación, aprenderemos la diferencia entre actualizar y migrar sistemas PLC y comprenderemos cómo implementar la opción correcta. ¿Por qué es necesario migrar o actualizar los sistemas PLC? Antes de entrar en el tema, primero es necesario comprender por qué debemos hacer lo mismo. Supongamos que ha estado utilizando un PLC “X” durante casi 15 años. No es que el programa comience a funcionar mal de repente; es una teoría completamente diferente y depende completamente de cómo el programador haya escrito el código. El código de PLC, una vez escrito, se ejecuta de la misma manera durante toda la vida. El problema comienza con el hardware y el soporte. Un fabricante de PLC, en la mayoría de los casos, no mantendrá este PLC “X” en producción durante un período de tiempo tan largo si no es estable o tiene muchas limitaciones en la programación. Más pronto, este PLC comenzará a volverse obsoleto y su reemplazo no estará disponible. Incluso el integrador del sistema o el propio fabricante del PLC no podrán brindar su soporte técnico, ya que el personal para el mismo se trasladará a una marca más nueva o su cable de programación ya no estará disponible. En ese caso, si de repente el sistema PLC falla debido a alguna razón, entonces no le quedará otra opción que esperar a que finalice un período de inactividad más largo. Además, si aún puede obtener este PLC de algún lugar, entonces su costo será muy alto y estará fuera de su presupuesto. Con las actuales interrupciones de la cadena de suministro y la reciente escasez de nuevas soluciones y piezas de automatización industrial, no es posible estimar exactamente cuánto tiempo puede llevar obtener una nueva unidad. En ese caso, le quedan dos opciones: migrar a otra marca o actualizar la existente a una CPU o programa de firmware más nuevo. Por eso, la migración y la actualización juegan un papel importante en la automatización industrial. Además, las nuevas soluciones traen consigo menos errores y riesgos, un soporte técnico más sólido, experiencia en servicio, menos inversión de capital y un funcionamiento eficiente de la planta. ¿Qué es la migración del sistema PLC? En primer lugar, comprendamos la más simple de las dos. La migración significa reemplazar completamente un sistema antiguo por un sistema nuevo. Esto es similar a un ciudadano que migra de su ciudad anterior a una nueva ciudad. Supongamos que tiene un PLC antiguo que tiene algunos defectos de hardware después de que se le hayan detectado 10 años. Dos entradas digitales de la CPU se han vuelto defectuosas y la CPU ya no está disponible en el mercado. Además, debido a un poco de mala suerte, el integrador de sistemas que proporcionó el PLC ha cerrado su negocio o ha cambiado a marcas más nuevas. En ese caso, la migración significa que deberá comprar un PLC de otra marca. Antes de comprar, deberá considerar factores como el número de E/S, el cableado de E/S, la disponibilidad del puerto de comunicación, la capacidad de programación, la capacidad de memoria, la velocidad de ejecución, cuánto se puede expandir, etc. Una vez que haya superado todo esto, deberá comprar uno nuevo y escribir un nuevo programa en él de acuerdo con el software del fabricante. Además, debe compartir la lista de E/S anterior con el nuevo proveedor, para que realice el mapeo de E/S en el PLC en consecuencia y reduzca el tiempo para cablear las E/S en el panel eléctrico. Una vez hecho esto, puede reemplazar el PLC antiguo por el nuevo y usar el sistema en consecuencia. Aunque los estándares de programación nuevos y consistentes no se pueden aplicar por completo utilizando este enfoque, la funcionalidad general se mantiene lo más cercana posible al original y el programa se puede mejorar hasta cierto punto. ¿Qué es la actualización de los sistemas PLC? Tomemos un segundo caso de actualización del sistema PLC. Tiene el mismo PLC del fabricante que se mencionó anteriormente y se ha producido una falla. Ahora, descubre que hay disponible un PLC de nivel superior del mismo fabricante, con un estilo de codificación y funcionalidades de E/S similares. Incluso el proveedor está disponible para brindar soporte. En lugar de cambiar de proveedor a uno más nuevo o cambiar completamente la marca del PLC, solo necesitará actualizar su sistema a uno más nuevo y de mayor calidad. Esta nueva CPU tendrá que reescribirse con la nueva codificación o simplemente enchufarse y funcionar, según el software. Por lo tanto, una actualización requiere un cableado de E/S y una codificación del PLC más completos a medida que actualizamos el sistema. Además, reescribir códigos nuevos desde cero permite al programador eliminar los errores que había observado en sistemas más antiguos y también planificar una lógica eficiente y confiable de una manera más sencilla. Este es un enfoque de borrón y cuenta nueva para actualizar un sistema. Diferencia entre migrar y actualizar sistemas PLC La migración significa cambiar a un fabricante de PLC completamente nuevo, mientras que la actualización significa cambiar a una CPU más nueva del mismo fabricante de PLC. La migración es más económica que la actualización, ya que requiere menos tiempo de inactividad, menos hardware nuevo, menos tiempo de programación y diseño de infraestructura. La migración es menos riesgosa que la actualización, ya que ya tiene disponible el programa del anterior y solo necesita copiar y pegar el mismo. Aunque no es posible copiar al 100 %, las funcionalidades pueden ser similares en gran medida debido a este enfoque. La migración puede dar lugar a un nuevo hardware y esto puede llevar tiempo para que los ingenieros comprendan el sistema rápidamente para luego poder realizar el mantenimiento y solucionar problemas. En este caso, la actualización es mucho más fácil. La migración es menos confiable y eficiente que la actualización porque no se sabe cómo funcionará este nuevo PLC a pesar de haberlo estudiado tanto. La migración y la actualización son tareas complicadas que requieren la experiencia detallada de los ingenieros y programadores involucrados. Además, las acciones a tomar varían de un sistema a otro. Una vez que se realiza, la tarea puede resultar completamente más sencilla. De esta manera, vimos el concepto de actualización y migración de sistemas PLC. -
Conozca las indicaciones LED de los PLC de GE
leizuofa posted A plc and hmi article in Spanish in PLC programming learning
Todos sabemos lo importante que es el PLC en la era de la automatización actual, ya que existen muchas marcas de PLC populares, como Siemens, Yokogawa, AB, ABB, GE, etc. En estos controladores PLC, se proporcionan muchas indicaciones LED para comprender los diferentes estados del controlador, pero para conocer el estado primero debemos comprender el significado de esas indicaciones. Indicaciones LED en los PLC de GE En este artículo, vamos a comprender las indicaciones LED de uno de los PLC de GE, específicamente de la serie CPL, también comprenderemos el funcionamiento de varios puertos disponibles en el controlador. En este artículo, vamos a explicar las indicaciones LED del modelo CPL-410 del PLC de GE. Acerca del modelo CPL 410 Este sistema PAC (controlador de automatización programable) llamado RX3iCPL410 cuenta con un servidor Linux incorporado y admite lenguajes de programación como lógica de escalera, texto estructurado, diagrama de bloques funcionales y C. Contiene 64 Mb de memoria de programa y datos configurable, 32 K bits para entrada y salida discretas y 32 K palabras para entrada y salida analógicas. También admite memoria masiva para intercambio de datos Admite hasta 768 bloques de programa, cada bloque con un tamaño de 128 KB, y también admite 4 números de LAN Ethernet independientes (10\100\1000). Se permiten hasta 32 números de clientes Modbus TCP IP, 48 números de SRTP (protocolo de transporte de solicitud de servicio) pueden ejecutarse simultáneamente y 16 conexiones de servidor Modbus TCP IP simultáneas. Este PLC puede soportar temperaturas de funcionamiento de hasta -40 a 70 grados C, es un dispositivo de montaje en riel DIN, admite una fuente de alimentación de 18 a 30 VCC y no requiere una fuente de alimentación especial. Se ha facilitado con cinco puertos Ethernet en el frente y una conexión RJ45 en el lado inferior. Hay una pantalla OLED disponible para navegar y monitorear varios estados de la CPU, también hay muchos interruptores con indicaciones LED disponibles para monitorear el estado y revisar las configuraciones. Podemos programar y configurar la CPU utilizando el software Proficy Machine Edition, este sistema puede crear fácilmente un sistema redundante con un tiempo de corte de 100 ms al PLC secundario. Bien, ahora vamos a discutir las indicaciones LED para este modelo de PLC GE CPL-410 en particular. En la siguiente imagen podemos ver muchas indicaciones y puertos de comunicación, en la Figura 1 el PLC no tiene ninguna conexión y la Figura 2 tiene canales de comunicación en funcionamiento. Fig 1 (izquierda) y Fig 2 (derecha) Empecemos por la esquina superior derecha. µSD: esta ranura es para insertar una tarjeta Micro-SD; la tarjeta Micro SD se utiliza para almacenamiento externo o para cargar programas; tiene una cubierta protectora para evitar daños. DISP: puede acceder a la navegación del menú de visualización en la pantalla OLED y realizar cambios según los requisitos. Con este botón puede acceder a la configuración de LAN, el estado de control, el estado de E/S, la información del dispositivo, la configuración del sistema operativo Linux, la información de redundancia y los comandos de redundancia. Podemos verificar la IP configurada de cada conexión LAN. SEL: puede guiar la selección con este botón indicador para cualquier modificación de configuración donde puede navegar por sus opciones según sus requisitos. RUN: se utiliza para ejecutar comandos al PLC, activa el menú OLED para seleccionar el modo RUN habilitado o RUN deshabilitado desde el PLC. En la condición de ejecución, la indicación verde se encenderá justo debajo del botón de ejecución. STOP: se utiliza para enviar un comando de parada al PLC. Puede seleccionar Stop Enabled o Stop Disabled usando este botón para el PLC. PHY PRES: indicación de presencia física de TPM (módulo de plataforma segura), esto hará que la luz verde se encienda en condiciones saludables. SSD: actividad del disco de estado sólido, indicación verde en condiciones saludables. Esto es para verificar el estado del disco de estado sólido o la unidad donde se almacenan los datos. TEMP: esto indica que el controlador alcanzó una temperatura excesiva, indicará una indicación LED ámbar cuando la temperatura supere el límite. OK: esta señal indica que la CPU está bien y en condiciones saludables. OE: salida habilitada, indicación verde cuando está bien. FRC: cuando aplicamos fuerza a cualquier módulo o equipo, se iluminará una indicación amarilla que muestra que la señal de fuerza está habilitada. FLT: esta indicación se iluminará con una luz roja cuando haya una falla del sistema. Una falla del sistema ocurre en caso de un problema con cualquier módulo. IO: este LED indica el estado de la red de E/S; La indicación verde se iluminará en condiciones normales. RACT: un sistema redundante es imprescindible para evitar fallas en el proceso en caso de cualquier problema con el sistema de control principal. También se requiere una supervisión cercana del sistema redundante para garantizar la disponibilidad en todo momento. La indicación LED RACT indicará que la redundancia está activa o que la unidad redundante está activa. La indicación será verde cuando los dispositivos redundantes estén activos. Este LED se activará una vez que la CPU redundante Hot Stand esté lista. RBOK: esto indica que la unidad de respaldo redundante está bien. La indicación será verde. GPOK: después de que Linux se haya iniciado correctamente y reiniciado la CPU, esta indicación LED parpadeará en verde e indicará que el propósito general está bien, es decir, un sistema operativo en buenas condiciones o listo para los inicios de sesión de los usuarios o podemos decir que Linux se está ejecutando. PWR: la alimentación está encendida, también podemos reiniciar el controlador con este botón, tenemos que mantener presionado el botón PWR para reiniciar el PLC, en condiciones adecuadas se iluminará en verde. Puertos de comunicación en el PLC Conozcamos un poco sobre los puertos de comunicación: USB1: este puerto está asignado a Linux y se puede usar para tener acceso a teclados, memorias USB, pendrives y otros dispositivos de memoria con controladores instalados correctamente. USB2: este puerto está asignado al controlador de tiempo de ejecución PACS (controlador de automatización programable) LAN: los puertos LAN se utilizan para configurar los paquetes de comunicación de la planta y la redundancia de Hot Standby donde se utilizan dos puertos de grupo LAN3 para cumplir con este propósito. Proporcionan un enlace de sincronización de datos de alta velocidad entre las dos CPU. Conecte el puerto LAN3 superior de la CPU primaria al puerto LAN3 superior de la CPU secundaria y conecte el puerto LAN3 inferior de la CPU primaria al puerto LAN3 inferior de la CPU secundaria. LAN del panel frontal: -LAN-1: este puerto no es conmutable y se conecta al conector RJ45 superior. -LAN-2: se conecta a los dos conectores RJ45 del medio y puede conmutarse internamente. -LAN-3: se conectará a los dos conectores RJ45 inferiores, estos puertos también pueden conmutarse internamente, este puerto se utiliza para proporcionar redundancia de reserva activa al sistema. LAN inferior: -RJ45: este puerto admite el protocolo de E/S en serie, también este puerto está asignado al propio sistema Linux. La velocidad y la salud del enlace del puerto LAN son muy cruciales para una comunicación adecuada, echemos un vistazo a las indicaciones superior e inferior del puerto LAN y el significado de esa indicación. Puertos LAN-Estado (indicación superior): Indicación verde: Se ha establecido el enlace correspondiente, Verde intermitente: Tráfico detectado, Apagado, Sin conexión. Puertos LAN-Velocidad (indicación inferior): Verde encendido: La velocidad de datos es de 1 Gbps o 100 Mbps, Apagado: La velocidad de datos de la red es de 10 Mbps Consulte la siguiente figura para comprender las indicaciones de los puertos LAN. Fig 3 Otros puertos disponibles en la parte inferior del PLC RJ45: Este es un puerto COM serial, donde podemos conectar un canal de comunicación con un conector RJ45, podemos usar este puerto para una conexión Ethernet directa, o podemos comunicarnos a través de un canal de comunicación Modbus o serial usando un convertidor TCP IP (Serial a Ethernet). Tenga en cuenta que el conector RJ viene con 8 pines y se conecta con cables que se combinan en par trenzado, este par trenzado ayuda a disminuir la diafonía y cancelar la interferencia electromagnética. Los puertos que se muestran a continuación se encuentran en la parte inferior del PLC (Fig. 4) Fig 4 Display Port: es un puerto de pantalla de video que podemos usar para transmitir video y audio simultáneamente o por separado. DP puede transmitir señales en un rango de 144 Hz a 4k. EFA: este es un puerto en la nube de IICS (Informatica Intelligent Cloud Services), este es un servicio basado en la nube para la integración y la gestión de datos. Con esta plataforma, puede configurar conexiones, crear usuarios, ejecutar, programar y monitorear actividades o tareas. EPCSS: Energy Pack Control & Status Signal, es un bloque de terminales con 5 números de terminales de cableado. Aunque EPCSS es opcional cuando se usa, permite que el controlador PLC guarde su estado actual en caso de pérdida de energía. 24DC IN: bloque de terminales de tres cables para suministro de energía de 24 V CC al PLC. Echemos un vistazo al resumen de todas las indicaciones LED en la Fig. 5 Fig 5 Entonces, esta fue una comprensión básica de las indicaciones LED y varios puertos del PLC de marca GE. -
Pruebas y validación en el desarrollo de PLC
leizuofa posted A plc and hmi article in Spanish in PLC programming learning
Cuando se desarrolla un programa de PLC, es necesario asegurarse de que se pruebe y valide correctamente antes de mostrarlo al cliente. Esto se debe a que un programa de PLC tiene muchas partes, como lógica, configuración, ajustes, etc. Por lo tanto, es necesario probar y validar todas y cada una de las partes, independientemente de qué programa funcione mal. Si hay errores en la configuración o la lógica, el sistema funcionará mal en el sitio. Para evitar esto, la mayoría de los programadores pasan horas probando la lógica del PLC y es un paso muy importante que realizan. En esta publicación, aprenderemos el proceso de prueba y validación del desarrollo de PLC. Pruebas y validación en el desarrollo de PLC A continuación, se mencionan algunos de los puntos relacionados con las pruebas y la validación de PLC. Reúna a las partes interesadas para una reunión inicial para discutir el alcance, los objetivos y los requisitos del proyecto de PLC. Formule los objetivos y los criterios de aceptación tanto para las pruebas como para la validación. Asigne recursos, incluidos los miembros del equipo, el hardware y las herramientas de software, necesarios para el proceso de prueba y validación. Preparar especificaciones detalladas de diseño funcional (FDS) que servirán como base para el desarrollo y la prueba del programa PLC. Desarrollar los bloques de código y las rutinas iniciales en función de las especificaciones de diseño funcional. Redactar planes de prueba específicamente para pruebas unitarias, identificando lo que cada unidad debe lograr y cómo probarlo. Ejecutar las pruebas unitarias, siguiendo los planes de prueba y registrando los resultados de cada función o rutina. Crear planes de prueba para pruebas de integración, describiendo cómo se combinarán y probarán los diferentes bloques de código y rutinas como una sola entidad. Realizar pruebas de integración, validando la funcionalidad de todo el programa y la interoperabilidad con otros sistemas. Desarrollar el protocolo FAT, especificando los criterios que debe cumplir el sistema para ser considerado aceptable. Realizar la FAT en función del protocolo FAT en un entorno simulado para garantizar que se cumplan todos los requisitos. Redactar protocolos de validación detallados que definan cómo se llevará a cabo la validación, qué se verificará y qué constituye resultados aceptables. Revisar los protocolos de validación y obtener las aprobaciones de control de calidad y otras partes interesadas. Implementar los protocolos de validación, documentar los resultados e identificar cualquier desviación o falla. Cree un protocolo SAT, centrándose en el entorno del mundo real donde funcionará el sistema PLC. Realice SAT para verificar que el sistema PLC funciona de manera confiable en su entorno operativo previsto. Prepare documentación completa de las actividades de prueba y validación, los resultados y las acciones correctivas adoptadas. Obtenga la aprobación final de todas las partes interesadas, asegurándose de que el sistema PLC esté probado y validado. Establezca procesos para monitorear el rendimiento del sistema PLC y programe actividades periódicas de reevaluación y revalidación. Archive toda la documentación y el código del proyecto PLC y cierre formalmente el proyecto. Los pasos anteriores proporcionan una guía sencilla para preparar la prueba y la validación en un nuevo proyecto de desarrollo de PLC. Echemos un vistazo a algunos pasos importantes uno por uno que deben seguirse hasta el final para un funcionamiento adecuado. Asignación de E/S El PLC funciona según las entradas y salidas. Por lo tanto, el primer paso para probar el programa es verificar la asignación de E/S en el PLC. Debe forzar cada entrada digital en la simulación o proporcionar una entrada de hardware real al PLC. Una por una, si la asignación es correcta, entonces lo mismo se reflejará en sus gráficos y programa. Esto verifica las entradas digitales. Siga el mismo proceso para las entradas analógicas. Pero, para las entradas analógicas, debe proporcionar múltiples conteos sin procesar en lugar de solo un conteo. Un amplio rango de conteos le brinda una idea adecuada de si el canal está funcionando correctamente o no. Luego, para las salidas digitales, debe forzarlas una por una. Si las salidas del PLC se encienden y apagan de acuerdo con la secuencia, entonces su asignación de DO es adecuada. Siga el mismo proceso para las salidas analógicas y proporcione un amplio rango de conteos sin procesar en lugar de un solo conteo. Obtendrá una idea adecuada de si el canal AO está funcionando correctamente o no. Verificación de protocolos de comunicación Una vez que se han verificado las E/S en el programa del PLC, el siguiente paso es verificar las direcciones de comunicación y red. Suponga que un PLC tiene un puerto Ethernet y un puerto Modbus RTU. Ha conectado una HMI al puerto Ethernet y tres VFD al puerto Modbus. El puerto Modbus se utiliza para transferir y recibir datos con VFD, como corriente, frecuencia, voltaje, etc. Usted ha realizado estas asignaciones en la lógica del PLC. Primero debe verificar el puerto Ethernet probando si la IP está haciendo ping o no; y si se está comunicando con la HMI o no. Luego, debe establecer la comunicación Modbus y verificar si los datos se están comunicando correctamente con el PLC o no. Esto borra por completo la parte del hardware porque ahora puede comunicar datos correctamente al campo; ya sea a través de E/S duras o E/S blandas. Estos dos pasos básicos son el primer paso en su validación. Modo manual Algunos sistemas tienen modo manual sin interbloqueos críticos y algunos sistemas tienen modo manual con interbloqueos críticos. Para verificar el modo manual, debe encender cada salida paso a paso y verificar si la salida física real se enciende o no. Este primer paso verifica si el DO o AO físico se ha vinculado correctamente con los botones del modo manual o no. Luego, debe generar las alarmas correspondientes y verificar si la salida se está apagando o no. Solo las salidas vinculadas deben apagarse. Las salidas restantes no deben verse afectadas. Esto garantiza que todas las salidas se hayan vinculado correctamente en el programa con los interbloqueos adecuados. Porque, una vez que se haya borrado el modo manual, se confirmará que las salidas físicas se pueden encender manualmente y luego se puede verificar el modo automático más fácilmente. Verificar directamente la lógica del modo automático confundirá al programador en cuanto a qué salida se está activando o desactivando. Verificar el modo manual garantizará que las salidas individuales se activen o no. Modo automático El siguiente gran paso es verificar el modo automático. El modo automático viene como una secuencia de verificación con enclavamientos. Cada sistema recibe un documento de lógica de control que muestra cómo funciona la secuencia con enclavamientos y matriz de salida adecuados. El programador del PLC tiene que asegurarse de que cuando se ejecuta una secuencia, las salidas correspondientes se activen o desactiven según corresponda o no. Además, ¿la secuencia se ejecuta correctamente con enclavamientos o no? La lógica del modo automático, cuando se realiza, debe dividirse principalmente en cuatro partes Activar las salidas, Escribir el flujo de la secuencia, Enlazar enclavamientos y alarmas, y Mostrar el estado de ejecución actual. Esta técnica hace que el flujo del programa sea muy fácil de ver y solucionar problemas. Se debe tratar de evitar el uso constante de bobinas de configuración y reinicio y lógica de escalera. La lógica de escalera es fácil de usar, pero cuando se ejecuta en una simulación en línea, consume tiempo para solucionar problemas. Además, las bobinas de ajuste y reinicio son difíciles de manejar, porque una vez que se utiliza una bobina de ajuste, se debe tener cuidado de restablecerla en algún lugar. De lo contrario, el bit permanecerá ajustado si la condición no se escribe correctamente. De esta manera, vimos el proceso de prueba y validación en el desarrollo de PLC. -
Control de la velocidad del motor de inducción mediante la salida analógica del PLC
leizuofa posted A plc and hmi article in Spanish in PLC programming learning
La posibilidad de controlar la velocidad del motor de inducción solo existe con los variadores de frecuencia. Básicamente, existen tres modos diferentes a través de los cuales podemos controlar la velocidad de un motor de inducción. Usando una señal digital Usando una señal analógica de 0 a 10 V / 0 a 5 V / 4 a 20 mA / 0 a 20 mA, etc. Usando la comunicación Modbus, ya sea en modo RTU o en modo TCP/IP Velocidad del motor de inducción En esta publicación, utilizaremos una señal de entrada analógica con un rango de 0 a 20 mA para controlar la velocidad del motor. Este artículo muestra cómo controlar la velocidad del motor mediante la salida analógica del PLC. Vea el siguiente esquema para obtener una descripción general. Para cambiar la velocidad del motor, se envía una señal de salida analógica de 0 a 20 mA desde el PLC al terminal de entrada analógica del VFD. La velocidad varía de 0 a 50 Hz a medida que los miliamperios aumentan de 0 a 20. En este tema, utilizamos seis puntos de salida analógica únicos del PLC inteligente S7 200 para controlar la velocidad de seis motores (cada motor tiene un VFD individual según la clasificación del motor). El PLC utilizado aquí es la CPU Siemens ST60 de la serie S7 200 Smart que tiene dos módulos de salida analógica EM AQ04 acoplados a ella, mientras que el modelo de VFD es la serie ATV310 de Schneider Electric. La HMI de Siemens se comunica con la CPU ST60 para variar la velocidad de los motores desde su pantalla. Antes de la lógica del PLC, consulte la configuración del hardware y los detalles de conexión a continuación: Los módulos de salida analógica anteriores se agregan a la CPU ST60. Cada punto de entrada analógica de los VFD recibirá una señal de 0 a 20 mA de varios puntos de salida analógica del PLC. Ahora, observe los detalles de los parámetros del variador VFD ATV310. 401: 01 (canal de referencia 1) 204.0: 0 A (tipo AI1) 204.1: 4 mA (parámetro de escala de corriente AI1 del 0 %) 204.2: 20 mA (parámetro de escala de corriente AI1 del 100 %) Aparte de estos, los parámetros del motor deben configurarse en el grupo n.º “300” según la potencia nominal del motor. El módulo de salida analógica también se denomina módulo DA o módulo digital a analógico. Según esta afirmación, un valor digital se traduce a miliamperios o voltaje de acuerdo con la configuración. Los diferentes PLC tienen varios valores digitales que se pueden convertir en una señal analógica de voltaje o miliamperios. La serie Siemens S7 200 utiliza 0 para 0 miliamperios y 27648 para 20 miliamperios. De acuerdo con el número de parámetro “204.1”, debemos determinar el valor digital en el que el punto de salida emite alrededor de 4 mA. Al utilizar el método de aciertos y errores, identificamos el valor como “5559”, en el que recibimos aproximadamente 4 miliamperios. Según la discusión anterior, la frecuencia estaría en cualquier lugar entre 0 y 50 Hz, y los miliamperios en el PLC se representan como valores digitales. Cuando se suministra una frecuencia particular desde la HMI, se requiere algún ajuste de escala para obtener la frecuencia real. Por lo tanto, podemos llamar a estos valores digitales valores “sin escala”. Ahora, para cambiar estos valores sin escalar a valores escalados, hay una fórmula a continuación: OSH = 27648.0 (valor digital sin escalar para generar una señal analógica de 20 mA) OSL = 5559.0 (valor digital sin escalar para generar una señal analógica de 4 mA) ISL = 0 (límite inferior de la salida de frecuencia en Hz) ISH = 50 (límite superior de la salida de frecuencia en Hz) “Entrada” es la variable para configurar la velocidad del motor desde la HMI. “Salida” es el valor digital escalado Ahora, colocando estos valores en la fórmula y evaluando más: Salida = [(27648.0 – 5559.0) *(Entrada – 0)/ (50 – 0)] + 5559.0 Salida = [22089.0*Entrada /50] + 5559.0 Salida = [441.78*Entrada] + 5559.0 Antes de evaluar la ecuación en la lógica de escalera, revise los ajustes de configuración de salida analógica en el software del PLC a continuación: En el software MicroWin Smart del Paso 7, haga clic en la opción resaltada Ajustes del bloque del sistema disponible en la barra del “árbol del proyecto”. En los ajustes del bloque del sistema, configure todos los canales de la primera tarjeta AQ04 y los canales 3.º y 4.º de la segunda tarjeta AQ04 con el tipo actual como resaltado. Programación de PLC para control de velocidad de motor de inducción mediante salida analógica Red 1: VD200 almacena el valor de entrada o el valor de la variable que se establece desde la HMI en forma de frecuencia o Hz. Luego se multiplica por 441,78 y se almacena en VD204. Luego, al valor en VD204 se le suma 5559 y se almacena en VD208. El valor en VD208 es un valor de salida escalado evaluado en formato real. La parte fraccionaria del valor en VD208 se descarta y la parte del número entero se almacena en VD276 en formato de entero doble mediante la instrucción "TRUNC". Después de eso, MW4 almacena este valor de entero doble en formato de entero. La dirección del primer canal del módulo AQ04, AQW16, es donde ahora se transfiere este valor. Ejemplo: si VD200 = 41,5 Hz suministrados desde la HMI, entonces VD208 = [441,78*41,5] + 5559,0 = 23892,87. Por lo tanto, para alcanzar 41,5 Hz, se debe almacenar 23892 en MW4 en forma de número entero. Según el comentario de la red, el primer canal se utiliza para variar la velocidad del motor (cargador) en una de las aplicaciones. De manera similar, las redes 2 a 6 están diseñadas para variar la velocidad de otros motores y ventiladores desde sus respectivos canales de módulos EQ04 utilizando VD212, VD224, VD236, VD248 y VD260 como sus puntos de ajuste de velocidad variable. Según las conexiones del cableado, el segundo módulo EQ04 utiliza el tercer y cuarto canal; como resultado, las direcciones utilizadas son AQW36 y AQW38. Para obtener más información, consulte Configuración de bloques del sistema. -
Mejores prácticas de cableado de PLC: controlador lógico programable
leizuofa posted A plc and hmi article in Spanish in PLC programming learning
Las mejores prácticas de cableado de PLC (controlador lógico programable) son esenciales por varias razones en los sistemas de control y automatización industrial. En las áreas de operaciones de producción, fabricación y producción de energía, así como en una amplia gama de sectores industriales, los componentes principales de los PLC ayudan a regular y monitorear diferentes procesos. Mejores prácticas de cableado de PLC Imagen cortesía de Yeulian A continuación, se presentan algunas razones clave por las que es importante un cableado de PLC adecuado. En resumen, proporciona confiabilidad, seguridad, precisión, mantenimiento, escalabilidad, cumplimiento, rentabilidad y documentación. ¿Cuáles son las prácticas adoptadas para el cableado de PLC? El cableado de un PLC (controlador lógico programable) es una parte fundamental de la instalación y puesta en servicio de sistemas de control automatizados. Los PLC se utilizan para controlar varios procesos y máquinas industriales. El cableado conecta el PLC a sensores, actuadores y otros dispositivos en la planta de producción. Garantiza que las señales se transmitan con precisión desde el PLC, lo que le permite interactuar con el equipo. A continuación, se presentan algunas prácticas importantes que se deben adoptar al cablear un PLC: Planificación Antes de comenzar con el cableado, es esencial tener un plan claro del diseño. Debe incluir componentes, dispositivos de entrada/salida (E/S) y la ubicación del PLC en el gabinete o panel eléctrico. Diagrama de cableado Asegúrese de tener una copia actualizada (revisada) del diagrama eléctrico. Selección de cables adecuados Use cables de calidad que cumplan con las especificaciones eléctricas necesarias. Asegúrese de que sean lo suficientemente largos y tengan la capacidad de corriente adecuada para evitar problemas de transmisión de señales y sobrecalentamiento. Identificación Etiquete claramente todos los cables, conectores y terminales. Simplifica la resolución de problemas, el mantenimiento y la expansión futura. El etiquetado facilita la identificación de cada cable, conector y terminal dentro del sistema. El etiquetado ayuda a mantener la integridad del sistema de control. Conectar cables o terminales por error puede provocar daños en el equipo, mal funcionamiento del sistema o incluso riesgos de seguridad. Una identificación adecuada reduce las posibilidades de errores durante la instalación o el mantenimiento. Conexiones sólidas Asegure conexiones seguras y protegidas apretando los terminales para evitar conexiones flojas que puedan provocar fallas. En las plantas industriales, el tiempo de inactividad puede ser extremadamente costoso. Las conexiones flojas provocan apagados inesperados o fallas en los equipos, lo que genera demoras en la producción y pérdidas financieras. Separación de energía y señal Mantenga una separación adecuada entre los cables de energía y los cables de señal para evitar interferencias electromagnéticas. Utilice canaletas o divisores para separar físicamente los cables, si es necesario. Esto puede ayudar a evitar la diafonía y reducir las posibilidades de interferencia. Pruebas y verificación Antes de energizar el sistema PLC, es esencial realizar pruebas de continuidad y verificación. Esto es para garantizar que todos los componentes estén conectados correctamente y según las especificaciones de diseño. Las conexiones incorrectas pueden provocar fallas, ineficiencias o daños en el equipo. Seguridad Siga las normas de seguridad eléctrica al realizar el cableado. Asegúrese de que el PLC y todos los componentes estén desenchufados antes de trabajar en el cableado. Documentación Mantenga registros detallados de todo el cableado, incluidos diagramas actualizados, listas de cables y documentación de configuración. Esto será valioso para el mantenimiento futuro y futuras modificaciones del sistema. Capacitación Asegúrese de que el personal que opera y mantiene el sistema esté capacitado en el cableado y el funcionamiento del PLC. Cumplimiento normativo Verifique que el cableado del PLC cumpla con las normas aplicables. El cableado adecuado es esencial para garantizar el funcionamiento confiable y seguro del sistema controlado por el PLC. El cableado del PLC es crucial para la confiabilidad, seguridad, precisión y capacidad de mantenimiento de un sistema de control industrial. El cableado adecuado garantiza que el sistema de control funcione según lo previsto y cumpla con las normas y regulaciones de la industria, lo que en última instancia contribuye a la eficiencia y el éxito generales del proceso industrial. ¿Por qué es importante el cableado adecuado del PLC? El cableado adecuado de un PLC (controlador lógico programable) es esencial en los sistemas de automatización industrial y control de procesos por varias razones importantes: El cableado adecuado proporciona confiabilidad al sistema. El cableado adecuado garantiza una conexión de cable fuerte y estable entre los componentes del sistema, lo que reduce la probabilidad de fallas intermitentes o errores de comunicación. Garantiza la seguridad. Un cableado incorrecto puede provocar cortocircuitos, sobrecargas y peligros eléctricos. Un cableado adecuado minimiza la posibilidad de accidentes eléctricos y garantiza que el sistema cumpla con los estándares de seguridad. Mejora el rendimiento del sistema: un cableado incorrecto puede afectar negativamente al rendimiento del sistema, provocando retrasos en la comunicación y la ejecución de instrucciones. Un cableado adecuado garantiza una transmisión de datos rápida y precisa. Un cableado adecuado reduce el tiempo de inactividad y los costos de mantenimiento. Nos ayuda a realizar un mantenimiento más simple: la organización y el etiquetado cuidadosos de los cables facilitarán la identificación y la resolución de los problemas del sistema. Cumplimiento normativo: en muchas industrias, algunas normas y regulaciones específicas requieren un cableado adecuado para garantizar la seguridad y la calidad del sistema. Consejos para el cableado de PLC Aquí compartimos los puntos principales relacionados con el cableado de PLC. Siga los códigos eléctricos nacionales y locales. Utilice cables blindados para señales analógicas y de comunicación. Asegúrese de que todos los componentes estén correctamente conectados a tierra. Etiquete todos los cables y terminales. Implemente un esquema de codificación por colores de los cables. Separe el cableado de entrada del cableado de salida. Utilice las longitudes de cable más cortas posibles. Evite enrollar los cables alrededor de los tornillos de los terminales. Seleccione los calibres de cable adecuados para los requisitos de carga y corriente. Utilice casquillos de cable para cables trenzados. Separe físicamente los cables de alto y bajo voltaje. Verifique dos veces la polaridad de la fuente de alimentación y las conexiones de E/S. Ate los cables de forma ordenada y utilice bridas. Pruebe la continuidad del cable y las conexiones correctas antes de encender. Mantenga la documentación actualizada y detallada. Utilice bloques de terminales para facilitar el mantenimiento. Realice inspecciones periódicas del cableado. Utilice mecanismos de alivio de tensión para proteger los cables. Siga los procedimientos de bloqueo y etiquetado por razones de seguridad. Realice pruebas exhaustivas del sistema una vez finalizado el cableado. -
Pasos de puesta en servicio en el sitio para programadores de PLC
leizuofa posted A plc and hmi article in Spanish in PLC programming learning
Siempre que un nuevo programador de PLC va al sitio para poner en servicio un proyecto, la primera pregunta que surge es cómo hacerlo. Esto se debe a que el sistema PLC es vasto y complejo de entender. Por lo tanto, cada programador de PLC debe saber qué hacer cuando va al sitio con una planificación adecuada. Con una cantidad tan grande de cables y dispositivos de campo eléctrico, es necesario comprender lo que está haciendo junto con la lógica del programa PLC. En esta publicación, aprenderemos los pasos de puesta en servicio que debe seguir un programador de PLC. Pasos de puesta en servicio en el sitio para programadores de PLC El primer paso para un programador de PLC es verificar si tiene todo el software de PLC necesario instalado en su computadora portátil. Supongamos que el sitio tiene automatización de Schneider en el sistema. Luego, primero, necesita instalar todo el software de PLC correspondiente en su computadora portátil. El software debe abrirse correctamente cada vez y todos los controladores relacionados también deben responder correctamente. Después de eso, debe conectar su computadora portátil al hardware de automatización en su oficina. Esto garantizará que pueda cargar y descargar correctamente en el sistema. La instalación o conectividad incorrecta del software puede provocar errores en la puesta en servicio en el sitio. Luego, debe realizar la copia de seguridad final en su computadora portátil y verificar la lógica del PLC con la simulación. Esto garantizará que vaya al sitio entendiendo todo el proceso. Después de esto, lleve todos los cables de comunicación con usted y prepárese para ir al sitio. Si se descubre que debido a las limitaciones de tiempo, el sistema no se está verificando por completo, anote los puntos pendientes y los errores lógicos observados durante las pruebas. Asegúrese de verificar esto durante la puesta en servicio. Una vez que llegue al sitio, primero observe el estado general de la planta. Cuánto trabajo mecánico está pendiente, cuánto trabajo eléctrico está pendiente; eso es lo más importante. Además, verifique el estado de los servicios públicos como agua, aire y vapor. Anote todos los estados y haga una lista de actividades diarias en su computadora portátil. Comparta este archivo con su superior inmediato para que sepa dónde está estancada la actividad y pueda impulsar a la persona correspondiente para que realice el trabajo. Una vez que se haya entregado el panel para la prueba, comience a verificar las E/S de campo. Según la lista de E/S y el diagrama de cableado, el dispositivo de campo correspondiente debe funcionar en consecuencia. Anote los problemas que encuentre y comuníquese con el electricista para resolverlos. Si hay dispositivos de comunicación en el sistema PLC, también debe verificarlos. Todos los dispositivos de comunicación deben poder comunicarse correctamente en el bus de red con el sistema de automatización PLC. Una vez que se haya verificado el cableado de campo, se debe verificar si todos los dispositivos mecánicos funcionan de acuerdo con el cableado o no. Finalmente, la ejecución del proceso es importante y si el dispositivo no responde, entonces el proceso no se ejecutará correctamente. Una vez que se haya realizado toda la parte de verificación del dispositivo, el siguiente paso es verificar la lógica con el ingeniero de procesos. Se debe verificar si la planta está funcionando de acuerdo con la lógica escrita o no. Si se encuentran problemas, verifique si se pueden resolver mediante la lógica o si deben ser resueltos por el ingeniero de procesos. Llegue a una conclusión y resuelva el problema. Esto completa la actividad de puesta en servicio del PLC. Guarde todas las copias de seguridad finales y entréguelas a su superior para su seguridad. Además, anote todos los parámetros finales del proceso y grabe un video de la planta en funcionamiento para su comprensión. Realice el informe final y obtenga la firma del cliente como prueba de que se ha realizado la puesta en servicio. Anote todas sus observaciones y asegúrese de que se resuelvan lo antes posible. Pasos de puesta en servicio del PLC A continuación se mencionan los principales pasos de puesta en servicio del PLC con breves detalles. Revisión de la documentación: Verifique los requisitos y esquemas del sistema. Controles de seguridad: Verifique el bloqueo/etiquetado y otros protocolos de seguridad. Control de hardware: Inspeccione el PLC y los módulos de E/S para detectar daños. Encendido: Encienda el PLC y confirme las funciones básicas. Establecimiento de comunicación: Configure enlaces entre el PLC y el terminal de programación. Actualización del firmware: Instale la última versión del software del PLC si es necesario. Configuración de E/S: Configure los módulos de entrada y salida. Carga del programa: Descargue el código inicial del PLC en el sistema. Modos de prueba: validar entradas, salidas y comunicaciones individuales. Controles de bucle: garantizar la integridad de la señal entre los dispositivos de campo y el PLC. Pruebas lógicas: verificar las funciones y secuencias del PLC. Simulación: probar la lógica compleja utilizando entradas simuladas. Puesta en marcha del proceso: iniciar la ejecución de prueba inicial del proceso. Ajuste fino: ajustar la sintonía del controlador PID, los temporizadores, los contadores y los puntos de ajuste en función de las ejecuciones de prueba. Actualizar documentación: registrar los cambios realizados durante la puesta en servicio. Pruebas funcionales: validar que todo el sistema funcione como se espera. Capacitación del operador: enseñar a los operadores a utilizar la nueva configuración. Crear copia de seguridad: guardar el programa del PLC final y los parámetros de configuración. Aprobación del cliente: Obtener la aprobación del cliente o del gerente de proyecto. Entrega: Finalizar la documentación para la entrega del sistema. De esta manera, vimos los pasos de puesta en marcha que debe seguir el programador del PLC. -
¿Qué es una tabla de instrucciones de programación de PLC?
leizuofa posted A plc and hmi article in Spanish in PLC programming learning
La programación de PLC tiene cinco tipos de lenguajes: lógica de escalera, lista de instrucciones, texto estructurado, diagrama de bloques funcionales y diagrama de flujo secuencial. Cada tipo de lenguaje de PLC tiene sus propias ventajas y desventajas. Si bien algunos de los lenguajes se ven bien visualmente y son fáciles de solucionar, otros lenguajes tienen un menor consumo de memoria y una velocidad de procesamiento más rápida. Uno de los lenguajes de PLC más básicos que se utilizan es la lista de instrucciones. No es tan famoso como otros lenguajes y solo lo utilizan unos pocos programadores de PLC debido a la tecnología obsoleta, pero aún está disponible en casi todo el software de los fabricantes de PLC. En esta publicación, veremos el concepto de lenguaje de lista de instrucciones en PLC. ¿Qué es una lista de instrucciones? Un programa de PLC escrito en lenguaje de lista de instrucciones consta de una serie de instrucciones que el controlador lógico ejecuta de forma secuencial. Cada instrucción está representada por una sola línea de programa y consta de los siguientes componentes: Número de línea Valor actual (solo en modo en línea) Operador de instrucción Operando(s) Comentario opcional Básicamente, si ha visto el lenguaje ensamblador tradicional utilizado en microprocesadores, entonces se sentirá identificado fácilmente con este lenguaje. También se puede definir como una mezcla de lógica de escalera y texto estructurado. Lógica de escalera en el sentido de que las instrucciones deben escribirse de manera lineal y texto estructurado en el sentido de que se utilizan mnemónicos en las palabras. Consulte la siguiente imagen para obtener más información. La primera imagen muestra una lógica de PLC escrita en lenguaje de escalera. La lógica es: %M3 se activará si %M0 está activado y %M1 está activado o %M2 está activado. Ahora, consulte la siguiente lógica para ver la lista de instrucciones. Puede ver que cada línea tiene solo un componente: la primera línea tiene %M0 y la segunda línea tiene %M1 haciendo lógica AND con la siguiente línea. La tercera línea tiene a %M2 haciendo lógica OR con la línea anterior, la cuarta línea cierra los comandos y la quinta línea activa la salida %M3. Por lo tanto, es una representación tanto de la lógica de escalera como del texto estructurado. Componentes de la lista de instrucciones A continuación se mencionan los componentes principales de una lista de instrucciones de PLC. Número de línea: los números de línea de cuatro dígitos se generan cuando crea una nueva línea de programa y el software los administra automáticamente. Se puede ver en la figura anterior como 0000 a 0004. Valores actuales: en el modo en línea, puede ver los valores actuales de cada elemento, como se muestra en la siguiente figura. Se indica como verdadero o falso en la siguiente imagen durante la animación en línea. Operadores de instrucción: este operador es un tipo de comando para ejecutar una instrucción. También se puede denominar como el lado de entrada y el lado de salida de la lógica escrita. Es un símbolo mnemotécnico que se utiliza para indicar el tipo de comando que se ejecutará en el lado de salida y también cómo lo ejecutará el lado de salida. Por ejemplo, en la imagen anterior, LD significa carga, que inicia la ejecución cargando el valor del primer bit, AND/OR denota instrucciones lógicas y ST denota almacenar valores del resultado en el bit de destino. Comentario: esto es opcional. Permite al programador escribir cualquier comentario que lo ayude a solucionar problemas de lógica fácilmente. Lista de instrucciones en la programación de PLC A continuación se mencionan algunas de las listas de instrucciones de PLC. LD – carga el valor booleano del operando en el acumulador. LDN– carga el valor booleano negado del operando en el acumulador. LDR– carga el valor booleano del operando en el acumulador cuando el valor cambia de 0 a 1 (flanco ascendente). LDF – Carga el valor booleano del operando en el acumulador cuando el valor cambia de 1 a 0 (flanco descendente). AND – Realiza una operación AND entre el resultado anterior y el operando actual. ANDN – Realiza una operación AND entre el resultado anterior y la inversa del operando actual. ANDR – Realiza una operación AND entre el resultado anterior y el flanco ascendente del operando actual. ANDF – Realiza una operación AND entre el resultado anterior y el flanco descendente del operando actual. OR – Realiza una operación OR entre el resultado anterior y el operando actual. NOT – Realiza la operación inversa del operando. ST – Toma el valor del resultado generado. STN – Toma el valor inverso del resultado generado. S – Realiza la operación de ajuste del operando. R – Realiza la operación de reinicio del operando. Aparte de estas, también tiene otras instrucciones como jump, subrutine, end, AND with, OR with, etc. dependiendo del fabricante del PLC. De esta manera vimos el concepto de lista de instrucciones en la programación del PLC. -
Ejemplo de PLC para controlar LED mediante interruptores
leizuofa posted A plc and hmi article in Spanish in PLC programming learning
En este artículo, aprenderá el ejemplo de PLC para controlar LED mediante interruptores y comprenderá la explicación de la lógica de escalera. Este ejemplo de PLC está diseñado para que los estudiantes de ingeniería aprendan y practiquen la lógica de escalera. La implementación del mismo programa de PLC para uso industrial será diferente. Ejemplo de PLC Diseñe una lógica de escalera de PLC para la siguiente aplicación. Estamos usando tres interruptores para controlar tres LED. Si 1 interruptor está encendido, entonces el LED I estará encendido. Si 2 interruptores están encendidos, entonces el LED II estará encendido. Si los 3 interruptores están encendidos, entonces el LED III estará encendido. En el artículo anterior, analizamos el mismo ejemplo de PLC utilizando interruptores de palanca. Aprenda la lógica. Entradas Las entradas digitales requeridas se enumeran a continuación. Interruptor 1: I0.0 Interruptor 2: I0.1 Interruptor 3: I0.2 Salidas Las salidas digitales requeridas se enumeran a continuación. Motor 1: Q0.0 Motor 2: Q0.1 Motor 3: Q0.2 Diagrama de escalera para controlar los LED mediante interruptores Explicación de la lógica de escalera Para esta aplicación, hemos utilizado el software EcoStruxure Machine Expert Basic v1.2 para la programación del PLC. En el programa anterior, hemos utilizado contactos normalmente abiertos, así como contactos normalmente cerrados para el interruptor 1 (I0.0), el interruptor 2 (I0.1) y el interruptor 3 (I0.2). En el escalón 0, cuando se enciende un interruptor cualquiera (contacto normalmente abierto) y los otros 2 interruptores (contactos normalmente cerrados) están apagados, se enciende el LED 1. Para encender el LED 2 del escalón 1, los 2 interruptores que sean contactos normalmente abiertos deben estar encendidos y el otro interruptor restante como contacto normalmente cerrado debe estar apagado. Para que el LED 3 esté ENCENDIDO, los interruptores 1, 2 y 3 del escalón 2 están conectados en serie, implementando así la compuerta lógica AND. El LED 3 se ENCIENDE cuando los tres interruptores están encendidos. Cuando cualquier interruptor 1 está encendido La señal fluye a través del interruptor 1, ya que está en estado verdadero. En estado falso, el interruptor 2 y el interruptor 3 también pasan señal a las salidas. Por lo tanto, el LED 1 estará ENCENDIDO. El LED I se ENCIENDE cuando el interruptor 2 está encendido y los interruptores 1 y 3 están apagados, ya que están en estado de contacto normalmente cerrado. Cuando el interruptor 3 está encendido y los otros 2 interruptores que son contactos normalmente cerrados están apagados, entonces el LED 1 se ENCIENDE. Encender más de un interruptor interrumpirá el circuito. El contacto normalmente cerrado, cuando está en estado verdadero, no permitirá la señal. Como resultado, el LED 1 se apagará. Cuando dos interruptores cualesquiera están encendidos El LED 2 se encenderá cuando el interruptor 1 y el interruptor 2 estén encendidos y el interruptor 3 esté apagado. El interruptor 3, como contacto normalmente cerrado, en estado falso, permitirá que la señal pase a través de él. Cuando el interruptor 1 y el interruptor 3 están encendidos y el interruptor 2 está apagado, el LED 2 se encenderá. El interruptor 2 permitirá la señal cuando esté en estado falso. La señal fluye a través del interruptor 2 y el interruptor 3, ya que estos están en estado verdadero. En estado falso, el interruptor 1 también pasa la señal a las salidas. Por lo tanto, el LED 2 estará encendido. Cuando se encienden más de dos entradas, el contacto normalmente cerrado utilizado para el tercer interruptor no cerrará el circuito en estado verdadero. Por lo tanto, el LED 2 se apagará. Cuando los 3 interruptores están encendidos Cuando los tres interruptores SWITCH 1 (I0.0), SWITCH 2 (I0.1), SWITCH 3 (I0.2) están encendidos, el LED 3 estará encendido y apagará las otras dos salidas. -
Ejemplo de lógica de PLC en varios interruptores y motores
leizuofa posted A plc and hmi article in Spanish in PLC programming learning
Aprenda el ejemplo de lógica de PLC en varios interruptores y motores con el diagrama de escalera. Este ejemplo de lógica de PLC está preparado para que los estudiantes de ingeniería aprendan y practiquen la lógica de escalera. El diseño del mismo programa de PLC para uso industrial será diferente. Ejemplo de lógica de PLC Enunciado del problema: Diseñe una lógica de escalera de PLC para la siguiente aplicación. Se utilizan cuatro interruptores de palanca para controlar cuatro motores. Si el interruptor 1 está encendido, entonces el motor I estará encendido. Si el interruptor 2 está encendido, entonces el motor I y el motor II estarán encendidos. Si el interruptor 3 está encendido, entonces el motor I, el motor II y el motor III estarán encendidos. Si el interruptor 4 está encendido, entonces el motor I, el motor II, el motor III y el motor IV estarán encendidos. Entradas del PLC A continuación se menciona la lista de entradas digitales para esta lógica de PLC. Interruptor 1: I0.0 Interruptor 2: I0.1 Interruptor 3: I0.2 Interruptor 4: I0.3 Salidas del PLC Las salidas digitales requeridas se enumeran a continuación. Motor 1: Q0.0 Motor 2: Q0.1 Motor 3: Q0.2 Motor 4: Q0.3 Lógica de escalera de varios interruptores y motores A continuación se muestra la lógica del PLC para el enunciado del problema dado. Explicación del programa Para este ejemplo, utilizamos el software PLC de Schneider para la programación. En el programa PLC anterior, hemos utilizado un contacto normalmente abierto para el interruptor 1 (I0.0), el interruptor 2 (I0.1), el interruptor 3 (I0.2) y el interruptor 4 (I0.3). El interruptor 1, el interruptor 2, el interruptor 3 y el interruptor 4 están conectados en paralelo para el motor 1, implementando así la compuerta lógica OR. Para el motor 2, las entradas del interruptor 2, el interruptor 3 y el interruptor 4 están conectadas en paralelo, implementando así la compuerta lógica OR. El interruptor 3 y el interruptor 4 están implementando la compuerta lógica OR, es decir, están conectados en paralelo para el motor 3. Solo el interruptor 4 está conectado al motor 4. Para que el motor 1 esté encendido, el interruptor 1, el interruptor 2, el interruptor 3 o el interruptor 4 deben estar encendidos. Para encender el motor 2, el interruptor 2, el interruptor 3 o el interruptor 4 deben estar encendidos. Cuando el interruptor 3 o el interruptor 4 están encendidos, el motor 3 se encenderá. El motor 4 se encenderá cuando se encienda el interruptor 4. Resultados de la simulación del PLC A continuación, veremos los resultados de la simulación del PLC con diferentes combinaciones de interruptores de entrada ON y OFF. Cuando el interruptor 1 está ON Cuando se enciende el interruptor de palanca 1, la corriente fluye a través de él (aquí usamos el término "Corriente" en el caso de un circuito eléctrico, por lo que aquí puede asumirlo como "Corriente" o simplemente llamarlo "Señal"). Como resultado, el motor 1 se enciende. Los demás motores permanecerán apagados porque el interruptor 1 no está conectado a ellos. Cuando el interruptor 2 está ON La corriente fluirá a través del interruptor 2 cuando se encienda, lo que encenderá el motor 1 y el motor 2. Esto es así porque el interruptor 2 está conectado solo al motor 1 y al motor 2. Cuando el interruptor 3 está encendido Cuando el interruptor 3 está encendido, fluye a través de él la corriente que encenderá tres motores, es decir, Motor 1, Motor 2 y Motor 3. El interruptor de entrada 3 está conectado solo a estas salidas. El motor 4 permanecerá apagado ya que el interruptor 3 no está conectado a él. Cuando el interruptor 4 está encendido El interruptor 4 encenderá todos los motores cuando esté encendido. El interruptor 4 está conectado a todos los motores; cuando esté encendido, se encenderán el motor 2, el motor 2, el motor 3 y el motor 4. -
Programa PLC para drenar los mismos productos de dos tanques
leizuofa posted A plc and hmi article in Spanish in PLC programming learning
Este es un programa PLC para drenar los mismos productos de dos tanques. Aprenda la programación de PLC con este sencillo ejemplo. Drenar los mismos productos de dos tanques Descripción del problema Dos tanques están llenos con los mismos productos. El drenaje de materiales de estos dos tanques depende del requisito del tanque de almacenamiento. Implemente la lógica para este sistema en el PLC utilizando un diagrama de escalera. Diagrama del problema Solución de ejemplo de PLC Aquí se utilizan dos tanques para el sistema. Para la medición de nivel, se utilizan dos sensores (sensores de nivel bajo). Como se muestra en la figura, aquí utilizamos dos bombas para transferir los materiales de los tanques (Tanque 1 y Tanque 2) a los tanques de almacenamiento. Aquí utilizaremos un transmisor de nivel para la medición de nivel del tanque de almacenamiento. La BOMBA 1 y la BOMBA 2 se controlarán mediante la retroalimentación del transmisor de nivel. Aquí utilizamos dos bombas para un funcionamiento suave. Ambas bombas se pondrán en funcionamiento cuando se detecte que el nivel de los tanques de almacenamiento está por debajo de su límite. Nota: Aquí estamos considerando una automatización simple para este sistema. En este sistema se utiliza un transmisor de nivel que medirá el nivel del depósito. El tanque de almacenamiento tiene una altura de 500 cm para simplificar y la retroalimentación del transmisor de nivel es de 4 a 20 mA. Usaremos un PLC S7-300 para esta aplicación. Usaremos escala para fines de programación. Lista de E/S Lista de entradas INICIO de ciclo:- I0.0 PARADA de ciclo:- I0.1 Nivel bajo del tanque 1:- I0.2 Nivel del tanque 2:- I0.3 Lista de salidas Bomba 1:- Q0.0 Bomba 2:- Q0.1 Memoria M Bit de ENCENDIDO de ciclo:- M0.0 Valor analógico del transmisor:- MW10 (INT) Valor analógico del transmisor:- MD100 (DINT) Valor de multiplicación:- MD104 Nivel de agua real (cm):- MD108 Diagrama de escalera de PLC para drenar los mismos productos de dos tanques Explicación del programa Para esta aplicación, utilizamos el PLC S7-300 y el software del portal TIA para la programación. Red 1: Utilizamos un circuito de enclavamiento para la salida de ciclo ON (M0.0). Puede iniciarse presionando START PB (I0.0) y detenerse presionando STOP PB (I0.1). Red 2: Aquí, el conteo o valor real que proviene del transmisor es actual (4 a 20 mA), por lo que al usar el canal de entrada analógica en el PLC podemos convertirlo en un conteo digital. Este dígito está en formato INT (MW10), por lo que debemos convertirlo en DINT (MD100) para el cálculo o la multiplicación. Red 3: El valor DINT (MD100) se multiplica por la altura máxima (500 cm) del tanque para fines de cálculo. Red 4: El valor multiplicado (MD104) se divide por el recuento máximo del módulo analógico (27648). Y la altura real final se almacena en MD108. Red 5: Aquí usamos un comparador para la BOMBA 1 (Q0.0). Durante la demanda de material, el operador operará la BOMBA 3 y la altura del nivel del agua disminuirá. Entonces, según nuestra automatización o sistema, necesitamos llenar el tanque de almacenamiento; la bomba 1 se encenderá si el nivel del agua es menor que su límite (aquí hemos tomado 480 cm). Nota: la BOMBA 1 debe detenerse si se detecta un nivel bajo (I0.2) del tanque 1. Red 6: Aquí usamos un comparador para la BOMBA 2 (Q0.1). Durante la demanda de material, el operador operará la BOMBA 3 y la altura del nivel del agua disminuirá. Por lo tanto, según nuestra automatización o sistema, necesitamos llenar el tanque de almacenamiento; la bomba 2 se pondrá en marcha si el nivel del agua es inferior a su límite (aquí hemos tomado 480 cm). Nota: la BOMBA 2 debe detenerse si se detecta un nivel bajo (I0.3) del tanque 2. Durante todo el ciclo de funciones debe estar ENCENDIDA. Nota: la aplicación anterior puede ser diferente de la aplicación real. Este ejemplo es solo para fines explicativos. También podemos implementar esta lógica en otros PLC. Este es el concepto simple del sistema de drenaje; también podemos usar este concepto en otros ejemplos. Todos los parámetros considerados en el ejemplo son solo para fines explicativos; los parámetros pueden ser diferentes en las aplicaciones reales. Además, no se consideran todos los enclavamientos en la aplicación. Resultado