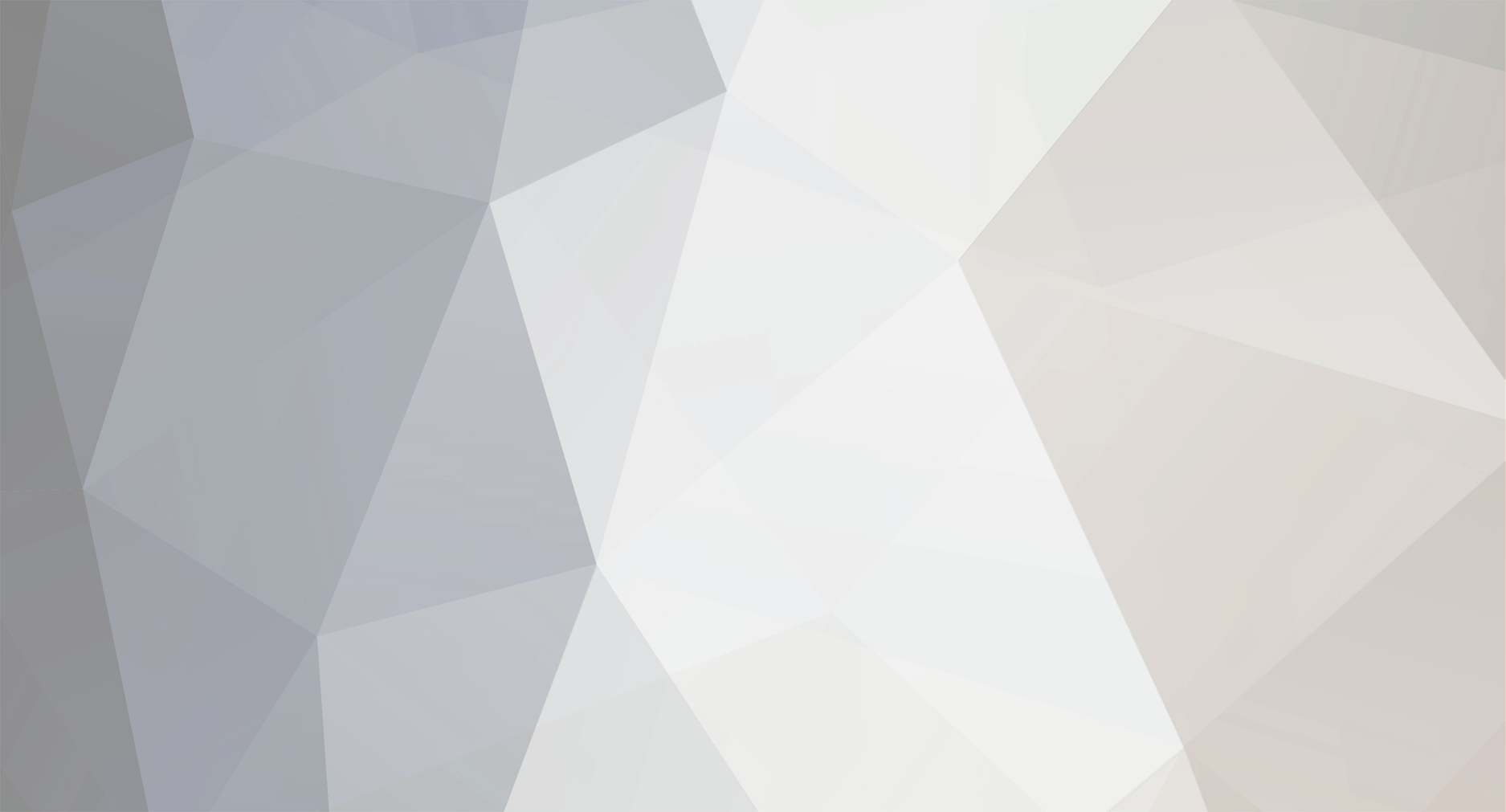
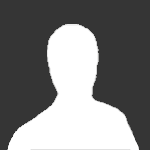
leizuofa
Staff group-
Content Count
198 -
Joined
-
Last visited
Content Type
Profiles
Forums
PLC programming technology and HMI interface design Simplified Chinese database
- PLC AND HMI SIMPLIFIED CHINESE ARTICLES
- PLC AND HMI SIMPLIFIED CHINESE ARTICLE Comments
- PLC AND HMI SIMPLIFIED CHINESE ARTICLE Reviews
PLC and HMI Brand Database
- PLC AND HMI BRANDS INTRODUCTIONS
- PLC AND HMI BRAND INTRODUCTION Comments
- PLC AND HMI BRAND INTRODUCTION Reviews
PLC programming technology and HMI interface design English database
- PLC AND HMI ENGLISH ARTICLES
- PLC AND HMI ENGLISH ARTICLE Comments
- PLC AND HMI ENGLISH ARTICLE Reviews
PLC programming technology and HMI interface design Russian database
- PLC AND HMI RUSSIAN ARTICLES
- PLC AND HMI RUSSIAN ARTICLE Comments
- PLC AND HMI RUSSIAN ARTICLE Reviews
Spanish database on PLC programming techniques and HMI interface design
- PLC AND HMI SPANISH ARTICLES
- PLC AND HMI SPANISH ARTICLE Comments
- PLC AND HMI SPANISH ARTICLE Reviews
German database on PLC programming technology and HMI interface design
- PLC AND HMI ARTICLES IN GERMAN
- PLC AND HMI ARTICLE IN GERMAN Comments
- PLC AND HMI ARTICLE IN GERMAN Reviews
Downloads
Store
Gallery
Blogs
Calendar
Videos
Everything posted by leizuofa
-
Documentación del sistema PLC
leizuofa posted A plc and hmi article in Spanish in PLC programming learning
La documentación del PLC es un registro de ingeniería muy importante de los pasos de control del proceso y, como ocurre con todas las descripciones técnicas, es esencial contar con registros de ingeniería detallados y precisos. Sin planos precisos, los cambios y modificaciones necesarios para la actualización y el diagnóstico son extremadamente difíciles o imposibles. Documentación del sistema PLC Todos los cables que van desde el PLC hasta el equipo de control y monitoreo deben estar claramente marcados y numerados en ambos extremos, y registrados en el diagrama de cableado. El PLC debe tener diagramas de escalera completos y actualizados (u otro lenguaje aprobado), y cada peldaño debe estar etiquetado con una descripción completa de su función. Los documentos esenciales en un sistema PLC son: 1. Descripción general del sistema y descripción completa de la operación de control; 2. Diagrama de bloques de las unidades del sistema; 3. Lista completa de cada entrada y salida, destino y número; 4. Diagrama de cableado de los módulos de E/S, identificación de la dirección para cada punto de E/S y ubicaciones de los bastidores; 5. Diagrama de escalera con descripción, número y función de los escalones. También es necesario tener la capacidad de simular el programa de escalera sin conexión en una computadora personal o en modo de fondo en el PLC, de modo que se puedan realizar cambios, actualizaciones y simulaciones de fallas sin interrumpir el funcionamiento normal del PLC, y se puedan evaluar los efectos de los cambios y las actualizaciones antes de incorporarlos. -
Ejemplo de programación de PLC sobre control de múltiples motores para principiantes
leizuofa posted A plc and hmi article in Spanish in PLC programming learning
Ejemplo de programación de PLC sobre control de múltiples motores para principiantes con el software de PLC Schneider Electric EcoStruxure Machine Expert Basic. Tenga en cuenta que este ejemplo de PLC es para estudiantes de ingeniería que estén interesados en aprender y practicar los ejercicios de PLC. Los programas de PLC industriales en tiempo real se diseñarán con más funciones de seguridad y protección. Ejemplo de programación de PLC sobre múltiples motores Diseñe una lógica de escalera de PLC para la siguiente aplicación. Estamos usando tres interruptores de palanca para controlar tres motores. Si el interruptor 1 está encendido, entonces el motor I, el motor II y el motor III estarán encendidos. Si el interruptor 2 está encendido, entonces el motor I y el motor II estarán encendidos. Si el interruptor 3 está encendido, entonces el motor I, el motor II y el motor III estarán apagados. Entradas digitales Las siguientes entradas digitales (DI) son necesarias en este programa de ejemplo. También se mencionan las direcciones DI del PLC asignadas. Interruptor 1: I0.0 Interruptor 2: I0.1 Interruptor 3: I0.2 Salidas digitales En este programa de ejemplo se requieren las siguientes salidas digitales (DO). También se mencionan las direcciones DO del PLC asignadas. Motor 1: Q0.0 Motor 2: Q0.1 Motor 3: Q0.2 Diagrama de escalera para control de múltiples motores Descripción del programa Para esta aplicación, utilizamos el software Ecostruxure Machine Expert Basic v1.2 para la programación. En el programa anterior, hemos utilizado un contacto normalmente abierto para el interruptor 1 (I0.0), contactos normalmente cerrados para el interruptor 2 (I0.1) y el interruptor 3 (I0.2) El interruptor 1 y el interruptor 3 están conectados en serie para el motor 1 y el motor 2, implementando así la compuerta lógica AND. Para el motor 3, el interruptor 1, el interruptor 2 y el interruptor 3 están conectados en serie, implementando así la compuerta lógica AND. Para que el motor 1 y el motor 2 estén encendidos, el interruptor 1 debe estar encendido y el interruptor 3 debe estar apagado. Cuando el interruptor 1 está encendido, el interruptor 2 y el interruptor 3 están apagados, el motor 3 estará encendido. Al encender el interruptor 3, se apagarán todos los motores, es decir, el motor 1, el motor 2 y el motor 3 estarán apagados. El motor 3 se apagará cuando se encienda el interruptor 2. Cuando se enciende el interruptor 1, todos los motores se encenderán porque la corriente también pasará por el interruptor 2 y el interruptor 3, ya que estos son contactos normalmente cerrados. Sin apagar el interruptor 1, el motor 1 y el motor 2 seguirán encendidos, pero el motor 3 se apagará cuando se encienda el interruptor 2. Al encender el interruptor 2, no pasará corriente al motor 3. Todos los motores se apagarán cuando se encienda el interruptor 3, incluso si los demás interruptores están encendidos. Cuando el interruptor 1 está encendido La corriente fluye a través del interruptor 1 ya que está en estado verdadero. En estado falso, el interruptor 3 y el interruptor 4 también pasan corriente a las salidas. Cuando el interruptor 2 está encendido La corriente no fluye a través del interruptor 2 cuando está encendido. En estado verdadero, el contacto normalmente cerrado interrumpe el circuito. Cuando el interruptor 3 está encendido El interruptor 3 es un contacto normalmente cerrado. Cuando está encendido, no permitirá que pase corriente a través de él. Como resultado, ninguna de las salidas estará encendida. -
SIEMENS-DE Tia Portal – OB20 Time Delay Interrupt Organization Block
leizuofa posted A plc and hmi article in German in PLC programming learning
In früheren Artikeln haben wir besprochen, was ein Organisationsblock ist, und wir haben über den Haupt-Zyklischen Interrupt OB1 und den Tageszeit-Interrupt OB10 gesprochen. In diesem Artikel werden wir die verschiedenen OBs weiter besprechen, und dieses Mal sprechen wir über den Time Delay Interrupt Organization Block oder OB20. Inhalt: Was ist OB20? Wie ruft man OB20 auf? Parameter der SRT_DINT-Anweisung. Beispielprogramm. Fazit. Was ist Time Delay Interrupt (OB20)? OB20 ist ein Organisationsblock, der vom Betriebssystem aufgerufen und ausgeführt wird, aber wir müssen dem Betriebssystem mitteilen, wann dieser OB20 aufgerufen werden soll. Das Betriebssystem erhält die Informationen vom Benutzer-SPS-Programm, um diesen OB20 aufzurufen. Es wartet auf die konfigurierte Verzögerungszeit und ruft dann die Logik auf und führt sie aus, die sich im OB20 befindet. Wir erstellen einen OB20-Block, indem wir im Projektbaum einen neuen Block hinzufügen. Siehe Abbildung 1. Abbildung 1 – Einen neuen OB20-Block erstellen Nachdem ich nun einen Zeitverzögerungs-Interrupt erstellt habe, stellt sich die Frage, wann dieser ausgeführt wird. Und wie konfiguriere ich die Zeitverzögerung der Blockausführung? Auch hier ist OB20 ein Organisationsblock, was bedeutet, dass Sie den auszuführenden Block nicht aufrufen, sondern dem Betriebssystem mitteilen, wann es ihn aufrufen und die darin enthaltene Funktionalität ausführen kann. Wie teilt man dem Betriebssystem mit, dass es OB20 aufrufen soll? Um dem Betriebssystem mitzuteilen, dass wir OB20 aufrufen möchten, verwenden wir SRT_DINT oder den Startzeitverzögerungs-Interrupt, siehe Abbildung 2. Abbildung 2 – Startzeitverzögerungsanweisung Parameter der SRT_DINT-Anweisung Wie Sie im letzten Bild sehen, können Sie die SRT_DINT-Anweisung verwenden, um OB20 aufzurufen. Sie müssen jedoch einige Parameter konfigurieren, damit die Anweisung funktioniert. EN: Die Anweisung wird erst ausgeführt, wenn am EN-Eingang ein negatives Flankensignal anliegt. Das bedeutet, dass Sie eine Bedingung aus dem Satz von Bedingungen zuweisen müssen, um das Signal zu aktivieren, und die Anweisung funktioniert nur, wenn diese Bedingung wahr und dann wieder falsch ist. OB_NR: Sie weisen die Nummer des Verzögerungsinterrupts zu, den Sie aufrufen müssen, in unserem Fall 20, da wir OB20 erstellt haben, aber wir können mehr als einen Verzögerungsinterrupt erstellen und müssen dann jeden mit einer separaten SRT_DINT-Anweisung aufrufen. DTIME: Dies ist die Verzögerungszeit, die Sie abwarten möchten, bevor Sie OB20 ausführen. Wir werden diese Zeit der Simulation halber auf 5 Sekunden festlegen. SIGN: Kennung, die angezeigt wird, wenn der Zeitverzögerungsinterrupt-OB in den Startereignisinformationen des OB aufgerufen wird. Beispiel-SPS-Programm Um OB20 besser zu verstehen, erstellen wir eine einfache Logik, um zu sehen, wie ein OB20 aufgerufen und ausgeführt werden kann. Wir werden dieses SPS-Beispiel auf der Logik aufbauen, die wir in früheren Artikeln für OB1 und OB10 erstellt haben. In OB20 erstellen wir eine Logik, die zählt, wie viele OB1-Zyklen innerhalb der 5 Sekunden Verzögerungszeit aufgerufen und ausgeführt wurden, die wir für OB20 konfiguriert haben. Siehe Abbildung 3. Abbildung 3 – Logik in OB20 Im letzten Bild sehen Sie, dass wir den MOVE-Befehl verwendet haben, um Informationen zu Zykluszählungen zu Beginn des OB20-Aufrufs und nach dessen Ausführung zu übertragen. Den Rest der Logik finden Sie in Abbildung 4. Abbildung 4 – Berechnen Sie, wie viele Zyklen innerhalb von 5 Sekunden gezählt werden Danach subtrahieren wir die beiden Werte der Zykluszählungen, um zu ermitteln, wie viele Zyklen innerhalb der 5 Sekunden Verzögerung ausgeführt wurden. Nachdem wir nun die gewünschte Logik erstellt haben, wie können wir OB20 aufrufen? Wie bereits erläutert, müssen wir die Anweisung SRT_DINT verwenden. Wir werden diese Anweisung innerhalb des OB10 verwenden, den wir zuvor so konfiguriert haben, dass er jede Minute ausgeführt wird. Das bedeutet, dass der OB20 ebenfalls jede Minute aufgerufen und ausgeführt wird, jedoch mit einer Verzögerungszeit von 5 Sekunden. Im vorherigen Artikel haben wir eine Logik erstellt, die angibt, wie oft der OB1 aufgerufen und ausgeführt wird. Außerdem haben wir eine weitere Logik erstellt, die den OB10 jede Minute aufruft. In diesem Beispiel verwenden wir den Aufruf des OB10, um den OB20 aufzurufen. Siehe Abbildung 5. Abbildung 5 – Aufruf des OB20 über OB10 Wir haben bereits gesagt, dass der SRT_DINT ein negatives Flankensignal am EN benötigt, damit der Aufruf gestartet werden kann. Aus diesem Grund haben wir das Signal TimeOfDayInterruptEnabled verwendet, von dem wir wissen, dass es wahr sein wird, wenn OB10 ausgeführt wird, und dann wieder auf falsch zurückgeht, was uns das Flankensignal gibt, das wir brauchen. Nachdem die gesamte SPS-Logik nun abgeschlossen ist, kompilieren und führen wir eine neue Simulation aus. Sehen Sie sich die folgende Simulation unseres Projekts an. Sie sehen in der Animation, dass die Werte der Zykluszählungen zunächst Nullen sind, aber wenn OB10 aufgerufen wird und TimeOfDayInterruptEnabled wahr ist, wartet die Logik 5 Sekunden, dann werden die Zählwerte mit den Zykluszählungen aktualisiert. Fazit OB20 ist ein Organisationsblock, der vom Betriebssystem aufgerufen und ausgeführt wird. Wir können dem Betriebssystem sagen, dass es OB20 mit der Anweisung SRT_DINT aufrufen soll. -
SPS vs. PAC – Die wichtigsten Unterschiede und Gemeinsamkeiten verstehen
leizuofa posted A plc and hmi article in German in PLC programming learning
Speicherprogrammierbare Steuerungen (SPS) und programmierbare Automatisierungssteuerungen (PAC) sind zwei Arten von Industriesteuerungen, die zur Automatisierung von Prozessen und Maschinen in der Fertigung, Verarbeitung und anderen industriellen Anwendungen verwendet werden. Beide Steuerungstypen haben ähnliche Funktionen, es gibt jedoch auch erhebliche Unterschiede zwischen ihnen. In diesem Artikel werden wir uns mit den Unterschieden, Gemeinsamkeiten und Beispielen von SPS und PAC befassen. Inhalt: Was sind SPS? Was sind PACs? Gemeinsamkeiten zwischen SPS und PAC. Unterschiede zwischen SPS und PAC. Beispiele für SPS-Modelle verschiedener Anbieter. Beispiele für PAC-Modelle verschiedener Anbieter. Wann ist eine SPS am besten geeignet? Und wann eine PAC? Fazit Was ist eine SPS? SPS steht für Speicherprogrammierbare Steuerung, ein spezialisierter Industriecomputer, der für Automatisierungssteuerungssysteme verwendet wird. SPS sind für den Betrieb in rauen Umgebungen konzipiert und werden zur Steuerung von Maschinen in Fertigungsanlagen, Fließbändern und anderen industriellen Umgebungen verwendet. SPS können in 5 verschiedenen Sprachen programmiert werden, z. B. Kontaktplanlogik, Funktionsblockdiagramme, Strukturtext, Anweisungsliste und sequentielle Diagramme. Diese 5 Sprachen sind gemäß den Normen IEC 61131-3 zugelassen und werden angewendet. Was ist ein PAC? PAC steht für Programmable Automation Controller (programmierbarer Automatisierungscontroller), der einer SPS ähnelt, aber über erweiterte Funktionen verfügt. PAC kombiniert die Fähigkeiten einer herkömmlichen SPS mit der Fähigkeit, viel kompliziertere Aufgaben auszuführen und mit anderen Geräten und Systemen zu kommunizieren, wodurch sie flexibler und leistungsfähiger als SPS sind. PAC wird typischerweise für komplexere Automatisierungs- und Steuerungsanwendungen in Branchen wie der Automobilindustrie, der Luft- und Raumfahrt und der Energieerzeugung verwendet. PAC kann in denselben 5 Sprachen wie SPS programmiert werden, aber auch in C und C++, wodurch sie die Codierung komplexerer Algorithmen handhaben können. Ähnlichkeiten zwischen SPS und PAC Die Ähnlichkeiten zwischen SPS und PAC sind so groß, dass es manchmal schwierig ist zu sagen, ob sie sich überhaupt unterscheiden. Obwohl es immer noch einige Unterschiede zwischen ihnen gibt. Die Ähnlichkeiten, die sie teilen, können sogar noch größer sein. Hier sind einige der Gemeinsamkeiten zwischen SPS und PAC: Kernfunktionalität Sowohl SPS als auch PAC sind für die zuverlässige und genaue Steuerung industrieller Automatisierungssysteme konzipiert. Sie werden verwendet, um Eingaben von Sensoren und anderen Geräten zu überwachen, die Informationen zu verarbeiten und dann Steuersignale an Aktuatoren und andere Geräte auszugeben. Programmierung Sowohl SPS als auch PAC verwenden Programmiersprachen, um Steuerlogik zu erstellen, die das Verhalten des Automatisierungssystems bestimmt. Sie teilen sich die 5 Programmiersprachen, die in den IEC 61131-3-Standards definiert sind, aber PAC bietet mehr Programmiersprachenoptionen, darunter C und C++. Haltbarkeit Sowohl SPS als auch PAC sind für raue Industrieumgebungen wie extreme Temperaturen, Feuchtigkeit und Vibrationen ausgelegt. Sie sind robust und zuverlässig, mit langer Lebensdauer und geringerem Wartungsaufwand. Modulares Design Sowohl SPS als auch PAC haben ein modulares Design, das eine einfache Erweiterung und Anpassung ermöglicht. Module können hinzugefügt oder entfernt werden, um bestimmte Anforderungen zu erfüllen. Industriestandards Sowohl PLC als auch PAC sind so gebaut, dass sie Industriestandards für Automatisierungs- und Steuerungssysteme wie IEC 61131 erfüllen. Diese Standards gewährleisten die Interoperabilität zwischen Geräten und Systemen verschiedener Hersteller. Unterschiede zwischen PLC und PAC Die Unterscheidung zwischen PAC und PLC kann etwas verschwommen sein. Obwohl es keine Definition dessen gibt, was ein PAC ausmacht, gibt es einige gemeinsame Merkmale, die PAC von PLC unterscheiden: Funktionalität Obwohl sowohl PLC als auch PAC für Automatisierungs- und Steuerungsanwendungen verwendet werden, verfügen PAC über erweiterte Funktionen wie Bewegungssteuerung, Prozesssteuerung und Datenerfassung. PAC verfügen normalerweise auch über mehr Verarbeitungsleistung und Speicher als PLC. Konnektivität PAC verfügen über erweiterte Konnektivitätsoptionen als PLC, darunter Ethernet, USB und Wireless. Dies erleichtert die Integration in größere Automatisierungssysteme und die Kommunikation mit anderen Geräten und Systemen. Kosten Aufgrund ihrer erweiterten Funktionalität und Flexibilität sind PAC im Allgemeinen teurer als PLC. Erweiterte Funktionen PACs verfügen häufig über erweiterte Softwarefunktionen als SPS, wie z. B. integrierte Bewegungssteuerung, Datenprotokollierung und erweiterte Diagnosetools. Diese Funktionen erleichtern Ingenieuren und Technikern die Überwachung und Fehlerbehebung des Steuerungssystems. Beispiele für SPS-Modelle verschiedener Anbieter Siemens S7-1500 SPS: Dies ist eine Hochleistungs-SPS von Siemens, einem der führenden Automatisierungsanbieter. Sie ist für anspruchsvolle Anwendungen konzipiert und bietet erweiterte Funktionen wie Bewegungssteuerung, Sicherheit und Schutz. Siehe Bild 1. Bild 1 – SIEMENS S7-1500 SPS Allen-Bradley CompactLogix 5370 SPS: Dies ist eine vielseitige SPS von Rockwell Automation, die eine breite Palette an E/A-Optionen und Kommunikationsprotokollen bietet. Sie eignet sich für eine Vielzahl von Anwendungen, darunter Maschinensteuerung und Prozessautomatisierung. Siehe Bild 2. Bild 2 – Allen-Bradley CompactLogix 5370 SPS Mitsubishi Electric Q Series SPS: Dies ist eine zuverlässige SPS von Mitsubishi Electric, die Hochgeschwindigkeitsverarbeitung, flexible E/A-Optionen und erweiterte Programmierfunktionen bietet. Sie eignet sich für eine Vielzahl von Anwendungen, darunter Automobil, Lebensmittel und Getränke sowie Pharmazeutika. Siehe Bild 3. Bild 3 – Mitsubishi Electric Q Series SPS Omron NJ Series SPS: Dies ist eine Hochgeschwindigkeits- und Hochleistungs-SPS von Omron, die erweiterte Bewegungssteuerung und Netzwerkfunktionen bietet. Sie eignet sich für eine Vielzahl von Anwendungen, darunter Verpackung, Druck und Halbleiterherstellung. Siehe Bild 4. Bild 4 – SPS der Serie Omron NJ Beckhoff TwinCAT SPS: Dies ist eine softwarebasierte SPS von Beckhoff, die auf einer PC-basierten Plattform läuft. Sie bietet erweiterte Funktionen wie Bewegungssteuerung, CNC und Robotik und eignet sich für eine Vielzahl von Anwendungen, einschließlich Maschinensteuerung und Prozessautomatisierung. Siehe Bild 5. Bild 5 – PC-basierte SPS Beckhoff TwinCAT CX9240 Beispiele für PAC-Modelle verschiedener Anbieter Emerson DeltaV DCS PAC: Dies ist ein PAC für verteilte Steuerungssysteme (DCS) von Emerson. Es ist für komplexe kontinuierliche Steuerungsanwendungen konzipiert und bietet erweiterte Funktionen wie Prozessmodellierung, Batch-Management und erweiterte Steuerung. Siehe Bild 6. Bild 6 – Emerson DeltaV DCS PAC Schneider Electric Modicon M340 PAC: Dies ist ein Hochleistungs-PAC von Schneider Electric, der erweiterte Funktionen wie Bewegungssteuerung, Sicherheit und Cybersicherheit bietet. Er eignet sich für eine Vielzahl von Anwendungen, darunter Energie, Wasseraufbereitung und Bergbau. Siehe Bild 7. Bild 7 – Modicon M340 PAC Einige weitere Beispiele für PACs sind: ABB AC 800M PAC Yokogawa ProSafe-RS PAC Phoenix Contact PLCnext Technology PAC Bosch Rexroth IndraMotion MLC PAC Wann ist eine SPS am besten geeignet? Und wann ein PAC? SPS und PAC werden in verschiedenen Arten von Automatisierungsanwendungen verwendet, abhängig von den spezifischen Anforderungen der jeweiligen Anwendung. Hier sind einige allgemeine Richtlinien, in welchen Fällen eine SPS und in welchen Fällen ein PAC am besten geeignet ist: SPS eignen sich am besten für: Diskrete Steuerungsanwendungen: SPS eignen sich am besten für Anwendungen mit diskreter Steuerung, wie z. B. die Steuerung des Betriebs eines Förderbands, einer Sortieranlage oder einer Verpackungsmaschine. Einfache Steuerungssysteme: SPS eignen sich ideal für Anwendungen mit einem relativ einfachen Steuerungssystem, das mit Kontaktplanlogik oder anderen ähnlichen Programmiersprachen programmiert werden kann. Kostensensitive Anwendungen: SPS sind im Allgemeinen günstiger als PACs, was sie zu einer guten Wahl für Anwendungen macht, in denen die Kosten ein wesentlicher Faktor sind. Kleine bis mittelgroße Systeme: SPS eignen sich für kleine bis mittelgroße Steuerungssysteme, in denen die Anzahl der Ein- und Ausgänge relativ gering ist. Ein Förderbandsystem in einer Fertigungsanlage ist ein gutes Beispiel für ein Automatisierungssystem, in dem eine SPS am besten geeignet ist. In dieser Anwendung ist die SPS für die Steuerung der Geschwindigkeit und Richtung des Förderbands sowie für die Überwachung des Status von Sensoren und anderen Geräten entlang der Förderlinie verantwortlich. Die SPS kann auch so programmiert werden, dass sie bestimmte Produktionsaufgaben wie Sortieren, Zählen oder Verpacken übernimmt. Ein Fördersystem hat normalerweise eine feste Struktur und einen genau definierten Satz von Vorgängen, die sequenziell ausgeführt werden müssen. SPS sind für diese Art von Anwendung gut geeignet, da sie für die Ausführung diskreter Steuerungsaufgaben ausgelegt sind und sehr zuverlässig funktionieren. SPS können einfach programmiert und konfiguriert werden, um verschiedene Arten von Sensoren, Aktoren und Kommunikationsprotokollen zu verarbeiten. PACs eignen sich am besten für: Prozesssteuerungsanwendungen: PAC eignet sich am besten für Anwendungen, die Prozesssteuerung beinhalten, wie z. B. die Steuerung des Betriebs einer Chemieanlage, einer Wasseraufbereitungsanlage oder eines Kraftwerks. Komplexe Steuerungssysteme: PAC ist ideal für Anwendungen mit einem komplexen Steuerungssystem, das erweiterte Algorithmen und Optimierungsfunktionen erfordert. Großsysteme: PAC eignet sich für groß angelegte Steuerungssysteme, bei denen die Anzahl der Ein- und Ausgänge hoch ist und das System über einen großen Bereich verteilt ist. Hochleistungsanwendungen: PAC ist für die Handhabung von Hochleistungsanwendungen geeignet, die eine schnelle Datenverarbeitung, Echtzeitsteuerung und hohe Zuverlässigkeit erfordern. Ein Kraftwerkssteuerungssystem ist ein gutes Beispiel für ein Automatisierungssystem, für das ein PAC am besten geeignet ist. In dieser Anwendung ist der PAC für die Steuerung und Überwachung einer großen Anzahl komplexer Prozesse und Geräte wie Turbinen, Generatoren, Kessel und Pumpen verantwortlich. Der PAC ist auch für das Sammeln und Analysieren von Daten von verschiedenen Sensoren und anderen Quellen und das Treffen von Entscheidungen auf der Grundlage dieser Daten zur Optimierung der Leistung des Kraftwerks verantwortlich. Ein Kraftwerkssteuerungssystem ist eine sehr komplexe und dynamische Umgebung, in der viele verschiedene Prozesse und Geräte gleichzeitig betrieben werden. PACs eignen sich gut für diese Art von Anwendung, da sie erweiterte Funktionen wie verteilte Steuerung, Redundanz und Fehlertoleranz bieten, die für die Gewährleistung der Zuverlässigkeit und Sicherheit des Kraftwerks unerlässlich sind. PACs können große Datenmengen verarbeiten und können so programmiert werden, dass sie komplexe Algorithmen und Optimierungsaufgaben ausführen. Fazit SPS und PAC werden beide in industriellen Automatisierungsanwendungen verwendet. Sie haben unterschiedliche Fähigkeiten und sind für unterschiedliche Arten von Anwendungen am besten geeignet. Bei der Auswahl zwischen SPS und PAC müssen die spezifischen Anforderungen der Anwendung berücksichtigt werden. PLC wird typischerweise in diskreten Steuerungsanwendungen verwendet, die über ein relativ einfaches Steuerungssystem verfügen. PAC wird in Prozesssteuerungsanwendungen verwendet, die über ein komplexes Steuerungssystem verfügen und erweiterte Algorithmen und Optimierungsfunktionen erfordern. -
SIEMENS-DE S7-1200 Hardwarekonfiguration – Siemens SPS-Tutorials
leizuofa posted A plc and hmi article in German in PLC programming learning
Die S7-1200 SPS ist eine kompakte, modulare und kostengünstige Lösung, die eine breite Palette an Funktionen und Flexibilität für kleine bis mittelgroße Automatisierungsanwendungen bietet. Zu diesen Funktionen gehören Kommunikationsoptionen, Speicher, CPU-Leistung und IO-Konfiguration. Wenn Sie einen Prozess steuern müssen, sollten Sie die SPS auswählen und so konfigurieren, dass sie Ihren Prozessanforderungen am besten entspricht. In diesem Artikel besprechen wir die Hardwarekonfiguration der S7-1200 SPS und geben ein Beispiel für die Konfiguration im Siemens Tia-Portal. Inhalt: Was ist die Hardwarekonfiguration einer SPS? Bedeutung der Hardwarekonfiguration. Einfaches Projektbeispiel. Wie konfigurieren wir unsere SPS mit dem gegebenen Beispiel? Hardwarekonfiguration der CPU. IO-Hardwarekonfiguration. HMI-Konfiguration. Fazit. Was ist die Hardwarekonfiguration einer SPS? Die Hardwarekonfiguration bezieht sich auf die spezifischen Komponenten der SPS, wie CPU, Speicher, Eingabe-/Ausgabemodule (E/A), Kommunikationsanschlüsse, Stromversorgung und alle zusätzlichen Module oder Zubehörteile, die möglicherweise benötigt und dem System hinzugefügt werden. Die Hardwarekonfiguration einer SPS umfasst auch das Aktivieren oder Deaktivieren einiger CPU-Funktionen, je nach Gerät, seinen Fähigkeiten und den Anforderungen Ihres Prozesses. Die Hardwarekonfigurationsschritte für eine SPS umfassen normalerweise Folgendes: Wählen Sie das geeignete SPS-Modell basierend auf den Anwendungsanforderungen. Identifizieren Sie die Eingabe-/Ausgabeanforderungen für das System, darunter Typ und Anzahl der Sensoren, Aktoren und anderen Geräte, die an die SPS angeschlossen werden. Wählen Sie das Kommunikationsprotokoll und die Netzwerktopologie, die zum Verbinden der SPS mit anderen Geräten und Systemen verwendet werden. Bestimmen Sie die Stromversorgungsanforderungen für die SPS und ihre Peripheriegeräte. Montieren Sie die SPS an einem geeigneten Ort und schließen Sie alle erforderlichen Kabel und Leitungen an. Konfigurieren Sie die SPS-Software für die Kommunikation mit den Hardwarekomponenten und richten Sie die entsprechenden Logik- und Steuerfunktionen ein. Die spezifischen Schritte zur Hardwarekonfiguration können je nach SPS-Modell und Anwendungsanforderungen variieren, aber dies sind die grundlegenden Schritte, die normalerweise in den Prozess einbezogen werden. In diesem Artikel sprechen wir über die Hardwarekonfiguration, die auf der TIA Portal-Plattform durchgeführt wird. Das heißt, wir gehen davon aus, dass Sie Ihre Anwendung kennen und dass Sie bereits Ihr SPS-Modell und die Stromversorgung ausgewählt haben. Sie können auf frühere Artikel zurückgreifen, in denen wir besprechen, wie Sie die SPS und die Stromversorgung auswählen, die am besten zu Ihrer Anwendung passen. Bedeutung der Hardwarekonfiguration in der SPS Eine ordnungsgemäße Hardwarekonfiguration stellt sicher, dass das System zuverlässig und robust ist. Wenn die Hardwarekomponenten nicht richtig konfiguriert sind, funktionieren sie möglicherweise nicht wie vorgesehen, was zu Systemausfällen oder -fehlern führt. Die Hardwarekonfiguration wirkt sich auf die Leistung des Systems aus. Durch Auswahl der richtigen Hardwarekomponenten und entsprechende Konfiguration kann das System mit maximaler Effizienz und Geschwindigkeit arbeiten und ein hohes Volumen an Ein- und Ausgängen verarbeiten. Die Hardwarekonfiguration wirkt sich auf die Skalierbarkeit und Flexibilität des Systems aus. Bei der Auswahl der Hardwarekomponenten und ihrer Konfiguration sollten zukünftige Erweiterungen oder Änderungen am System berücksichtigt werden, um sicherzustellen, dass das System problemlos Änderungen oder Upgrades verarbeiten kann. Die Hardwarekonfiguration wirkt sich auf die Kosten des Systems aus. Durch Auswahl der geeigneten Hardwarekomponenten und Konfiguration können unnötige Kosten vermieden und die Gesamtkosten des Systems minimiert werden. S7-1200-Hardwarekonfiguration Wir gehen von einem einfachen SPS-Projekt aus und sehen uns an, wie wir die SPS in unser Projekt konfigurieren können, bevor wir mit dem Schreiben unseres Codes beginnen. Temperaturkontrollsystem für einen Reaktor mit SPS Das Projekt beinhaltet die Kontrolle der Temperatur eines Reaktors mit einer SPS. Das System sollte die Temperatur des Reaktors messen und die Temperatur durch Kontrolle des Durchflusses einer Kühlflüssigkeit anpassen. Das Projekt verwendet vier Thermoelemente zur Messung der Temperatur, zwei Magnetventile zur Kontrolle des Durchflusses der Kühlflüssigkeit und einen Motor zum Antrieb des Laufrads des Reaktors. E/A-Konfiguration Eingänge: Thermoelemente 1 – 4: Dies sind 4 analoge Eingänge, die die Temperatur an verschiedenen Stellen im Reaktor messen. Not-Aus-Taster: Dies ist ein digitaler Eingang, der im Notfall zum Stoppen des Systems verwendet wird. Potentiometer für Temperatursollwert: Dies ist ein analoger Eingang, mit dem der Bediener den gewünschten Temperatursollwert einstellen kann. Ausgänge: Magnetventil 1 und 2: Dies sind 2 digitale Ausgänge, die den Durchfluss der Kühlflüssigkeit durch die Reaktorrohre steuern. Motorsteuerung: Dies ist ein digitaler Ausgang, der die Geschwindigkeit und Richtung des Motors steuert, der das Laufrad antreibt. Heizungssteuerung: Dies ist ein digitaler Ausgang, der das Heizsystem des Reaktors steuert. Systembetrieb: Das System wartet darauf, dass der Bediener den Temperatursollwert mit dem Potentiometer einstellt. Die SPS liest den Temperatursollwert und vergleicht ihn mit der aktuellen Temperatur des Reaktors, die von den vier Thermoelementen gemessen wird. Wenn die Reaktortemperatur unter dem Sollwert liegt, aktiviert die SPS den Heizungssteuerungsausgang, um die Temperatur zu erhöhen. Wenn die Reaktortemperatur über dem Sollwert liegt, aktiviert die SPS einen der Magnetventilausgänge, um den Durchfluss der Kühlflüssigkeit zu erhöhen und die Temperatur zu senken. Die SPS überwacht kontinuierlich die Temperatur und passt die Heizungs- und Kühlsysteme an, um den gewünschten Sollwert beizubehalten. Die SPS steuert auch den Motor, der das Laufrad antreibt, um den Inhalt des Reaktors zu mischen. Wenn der Not-Aus-Druckknopf gedrückt wird, deaktiviert die SPS alle Ausgänge und stoppt das System. Das SPS-Projekt kann je nach den spezifischen Anforderungen des Projekts weiter erweitert und geändert werden, um zusätzliche Funktionen wie Alarme, Datenprotokollierung oder Fernüberwachung einzuschließen. Wir werden uns jedoch nicht mit der Codierung der SPS-Logik dieses Systems befassen, sondern anhand dieses Beispiels erklären, wie die SPS hardwaremäßig so konfiguriert wird, dass sie zu unserem Projekt passt. Dazu gehört: Auswahl der SPS-CPU. Auswahl der IO-Module. Zuweisung der Eingangs- und Ausgangs-Tags zu den Hardwaremodulen. Zuweisung einer IP zur Kommunikation an die SPS. Zuweisung eines Schutzkennworts. Konfiguration der lokalen Zeit der SPS. Konfiguration des HMI und Herstellen der Verbindung mit der SPS. Wie konfiguriert man die SPS mit dem angegebenen Beispiel? Im Folgenden besprechen wir die grundlegende Erstellung eines SPS-Projekts mit der erforderlichen Hardware. Die Hardwarekonfiguration der CPU: Auswahl der CPU: Wenn Sie ein neues Projekt im TIA Portal starten, sollten Sie ein neues Gerät konfigurieren und es Ihrem Projekt hinzufügen. Siehe Bild 1. Bild 1. Konfigurieren Sie ein Gerät für Ihr Projekt Wie Sie dem vorherigen Bild entnehmen können, zeigt Ihnen das TIA-Portal bereits, dass der erste Schritt die Konfiguration eines neuen Geräts sein sollte. Im vorherigen Artikel haben wir besprochen, wie Sie die SPS auswählen, die zu Ihrem Prozess passt. Daher werden wir das hier nicht noch einmal erwähnen. Da es sich um ein einfaches Projekt handelt, wählen wir für unser Projekt die CPU 1214C AC/DC/RLY. Siehe Bild 2. Bild 2. Fügen Sie dem Projekt einen neuen Controller hinzu CPU-Eigenschaften: Je nachdem, welche CPU Sie für Ihr Projekt ausgewählt haben, stehen Ihnen unterschiedliche CPU-Funktionen und -Eigenschaften zur Verfügung. Sie können diese Funktionen je nach Bedarf aktivieren oder deaktivieren. Für einige der Funktionen sind zusätzliche Konfigurationen erforderlich. Siehe Bild 3. Bild 3 – Eigenschaften der CPU Wie Sie im vorherigen Bild sehen können, gibt es viele Eigenschaften, die Sie für Ihre CPU im Projekt festlegen können. Wir werden einige dieser Eigenschaften erwähnen, die Sie in jedem Projekt konfigurieren müssen, das Sie erstellen, andere Eigenschaften werden nur in Sonderfällen verwendet. Kommunikation: Dies ist eine sehr wichtige Konfiguration für jedes SPS-Projekt; Ihr Projekt wird höchstwahrscheinlich verschiedene Module und Geräte haben, die miteinander kommunizieren müssen. Das Einrichten der Kommunikation zwischen Ihrer SPS und diesen Geräten ist für Ihr Projekt wichtig. Durch die Auswahl der CPU haben Sie bereits definiert, wie die Kommunikation erfolgen soll. Einige CPUs funktionieren nur mit Profinet, einige nur mit Profibus und einige können beides verwenden. Die für dieses Beispiel ausgewählte SPS funktioniert nur mit Profinet. Über die Profinet-Schnittstelle legen Sie die IP-Adresse für Ihre SPS fest. Diese IP sollte im Projekt eindeutig sein; Sie können nicht dieselbe IP für zwei verschiedene Module verwenden. Siehe Bild 4. Bild 4 – Profinet-Schnittstelle Zykluszeit: Wie Sie wissen, ist dies eine weitere wichtige Eigenschaft für Ihre SPS. Die Zykluszeit Ihres Programms hängt davon ab, wie viel Code Sie geschrieben haben und wie lange die SPS braucht, um diesen Code auszuführen. In den Zykluszeiteigenschaften können Sie die Zyklusüberwachungszeit festlegen. Wenn die SPS länger als diese festgelegte Zeit braucht, um das Programm auszuführen, gibt die SPS einen Fehler aus. Siehe Bild 5. Mit dieser Eigenschaft können Sie auch die Mindestzykluszeit für Ihre CPU bestimmen. Dies können Sie tun, wenn Sie „Mindestzykluszeit für zyklische OBs aktivieren“ aktiviert haben. Sie können dann die gewünschte Mindestzykluszeit schreiben und die SPS passt ihre Leistung entsprechend dieser Zeit an. Natürlich ist diese Zeit durch die Leistungsfähigkeit der CPU begrenzt, sodass Sie diese Zeit nicht unter einen bestimmten Grenzwert senken können. Bild 5 – Zykluszeiteigenschaft System- und Taktspeicherbits: Systemspeicherbits und Taktspeicherbits sind in der CPU integrierte Bits, die das Betriebssystem verwendet, um bestimmte Ereignisse in der SPS anzuzeigen. Beispielsweise gibt es ein Speicherbit, das nur beim ersten Scan auf TRUE wechselt, oder ein Speicherbit, das TRUE wird, wenn sich der Diagnosestatus ändert. Es gibt auch einige dedizierte Taktspeicherbits, wie ein Bit, das einen Takt von 10 Hz darstellt, oder ein Bit, das einen Takt von 2 Hz darstellt. Diese Bits können in einigen Anwendungen sehr nützlich sein und bei gleicher Funktionalität eine Menge Programmiercode einsparen. Siehe Abbildung 6. Abbildung 6 – System- und Taktspeicherbits aktivieren Sie können die Verwendung eines oder beider Speicherbytes aktivieren; Sie können auch die Adresse dieser Bytes bestimmen, wie Sie auf der Abbildung sehen können. Tageszeit: Eine weitere sehr wichtige Eigenschaft Ihrer SPS ist das Einstellen der Zeit in Ihrer SPS. In fast jedem Projekt, das Sie erstellen, müssen Sie die Echtzeit kennen, um bestimmten Aktionen unterschiedliche Daten zuweisen zu können. Im vorherigen Artikel haben wir über lokale und Systemzeiten in der SPS und deren Verwendung gesprochen. Diese Eigenschaft der CPU ermöglicht es Ihnen, die lokale Zeit auf die gewünschte Zeitzone einzustellen. Siehe Abbildung 7. Abbildung 7 – Eigenschaft „Lokale Zeit“ Schutz und Sicherheit: Mit dieser Eigenschaft können Sie die Zugriffsebene und den Kennwortschutz für Ihre SPS bestimmen. Siehe Bild 8. Bild 8 – Schutz- und Sicherheitseigenschaft Die zuvor erwähnten Eigenschaften sind die am häufigsten konfigurierten Eigenschaften bei fast jedem SPS-Projekt, das Sie durchführen würden. Es gibt einige andere Eigenschaften, die bei einfachen Programmen wie Webservern und OPC UA weniger wahrscheinlich verwendet werden. Der nächste Schritt bei der Hardwarekonfiguration Ihres Projekts ist die Konfiguration der IOs. IO-Hardwarekonfiguration: Ein weiterer wichtiger Schritt Ihres Projekts ist die Konfiguration Ihrer IOs, d. h. Sie müssen entscheiden, wie viele IO-Module Sie benötigen und welche Art von IO-Modulen Sie benötigen. Bei der Entscheidung über Ihre IOs sollten Sie einige wichtige Punkte berücksichtigen, z. B. einige freie IO-Punkte zu haben und die IO-Module auszuwählen, die zu den Eingangssensoren und Ausgangsaktoren in Ihrem Projekt passen. Siehe Bild 9. Bild 9 – Analoges Eingangsmodul hinzufügen Wie wir in unserem Beispielprojekt erwähnt haben, verwenden wir 4 Thermoelemente als analoge Eingänge für meine SPS, also muss ich ein analoges Eingangsmodul mit mindestens 4 Eingangskanälen hinzufügen, da die ausgewählte SPS nur 2 analoge Eingangskanäle hat. Außerdem ist das Thermoelement ein spezieller Typ von analogem Eingang, der ein dediziertes Eingangsmodul erfordert. Deshalb haben wir uns für das Modul AI 8xTC entschieden, das 8 Eingangskanäle hat, die für die Verwendung mit Thermoelementen vorgesehen sind. Wir haben uns für das 8-Kanal-Modul und das 4-Kanal-Modul entschieden, um Reservekanäle für die zukünftige Verwendung zu haben, falls wir unser Projekt erweitern müssen. Wenn Sie zu den Eigenschaften des Moduls AI 8xTC gehen, werden Sie sehen, dass Sie jeden Eingangskanal einzeln konfigurieren können. Sie können den Typ des Thermoelements, die Messskala und andere Eigenschaften auswählen. Siehe Abbildung 10. Abbildung 10 – Eingangsmodul konfigurieren Als Nächstes müssen Sie Ihre IO-Tags definieren und jedem Eingang oder Ausgang einen entsprechenden IO-Punkt in Ihrer SPS oder in den IO-Modulen zuweisen. Siehe Abbildung 11. Abbildung 11 – Eingangs-Tags zuweisen Anschließend weisen Sie die restlichen Eingangs- und Ausgangs-Tags zu, siehe Abbildungen 12 und 13. Abbildung 12 – Eingangs-Tags für die SPS zuweisen Abbildung 13 – Ausgangs-Tags Ihrem Projekt zuweisen HMI-Konfiguration Ihr SPS-Projekt benötigt wahrscheinlich eine HMI. Nachdem Sie Ihre HMI ausgewählt haben, können Sie verschiedene Konfigurationen vornehmen. In diesem Artikel zeigen wir nur, wie die Kommunikation zwischen HMI und SPS konfiguriert wird. Wie Sie im vorherigen Bild sehen, wählen Sie ein HMI aus, indem Sie ein neues Gerät hinzufügen und dann ein HMI auswählen. Siehe Bild 14. Bild 14 – Auswählen eines HMI Es gibt verschiedene Möglichkeiten, die Kommunikation zwischen HMI und SPS einzurichten, aber der einfachste Weg ist über die Netzwerkansichtsseite. Siehe Bild 15. Bild 15 – Einrichten der HMI-Verbindung Auf der Netzwerkansichtsseite können Sie die Verbindung zwischen HMI und SPS einrichten, indem Sie einfach auf das kleine grüne Quadrat klicken, das Profinet vom HMI darstellt, und es auf die SPS ziehen. TIA Portal zeichnet dann eine grüne Linie zwischen den beiden Modulen und weist dem HMI automatisch eine IP-Adresse zu, um die Kommunikation zwischen ihnen einzurichten. Fazit Die Hardwarekonfiguration ist ein sehr wichtiger Schritt in jedem SPS-Projekt. Die richtige Hardwarekonfiguration Ihrer SPS stellt sicher, dass die erforderlichen Funktionen des Projekts erfüllt werden. Zur Hardwarekonfiguration gehören die Auswahl von E/A-Modulen, das Aktivieren oder Deaktivieren bestimmter CPU-Eigenschaften und das Konfigurieren verschiedener Geräte wie HMI mit Ihrer SPS. -
SIEMENS-DE Übersicht über SIEMENS PLC – S7-1500, S7-1200, S7-400, S7-300
leizuofa posted A plc and hmi article in German in PLC programming learning
Siemens ist ein bekanntes multinationales Unternehmen, das in einer Vielzahl von Branchen tätig ist, darunter Energie, Gesundheitswesen, Transport und Industrieautomatisierung. Siemens wurde 1847 gegründet und hat sich seitdem zu einem globalen Konzern mit Niederlassungen in vielen Ländern entwickelt. Siemens ist für seine innovativen Produkte und Dienstleistungen bekannt und gilt als eines der nachhaltigsten Unternehmen der Welt. In diesem Artikel geben wir einen Überblick über Siemens PLC, die einen sehr kleinen Teil der verschiedenen Produkte von Siemens im Bereich der Industrieautomatisierung ausmachen. Inhalt: Siemens in der Industrieautomatisierung. Verschiedene SPS-Familien von Siemens. Übersicht über Siemens S7 PLCs. Simatic S7-1200. Simatic S7-1500. Simatic S7-300. Simatic S7-400. Simatic S7-ET 200 CPU Warum gibt es so viele verschiedene Modelle? Wie entscheide ich, welcher Typ von S7-SPS am besten zu meiner Anwendung passt? Fazit. Siemens in der industriellen Automatisierung Siemens ist ein führendes Unternehmen im Bereich der industriellen Automatisierung und bekannt für seine hochwertigen Produkte und Lösungen. Das Unternehmen bietet eine breite Palette an Produkten für die industrielle Automatisierung, darunter speicherprogrammierbare Steuerungen (SPS), Mensch-Maschine-Schnittstellen (HMIs), Frequenzumrichter (VFDs) und industrielle Kommunikationsnetzwerke. Siemens bietet auch Softwarelösungen für die industrielle Automatisierung an, wie beispielsweise das Totally Integrated Automation TIA Portal, ein Engineering-Framework, das alle Automatisierungssoftwaretools auf einer Plattform integriert. Außerdem hat Siemens seine eigene Industrial Internet of Things (IIoT)-Plattform namens MindSphere entwickelt, die die Erfassung und Analyse von Daten von angeschlossenen Geräten in industriellen Umgebungen ermöglicht. Unterschiedliche SPS-Familien von Siemens Siemens hat zwei Hauptfamilien von SPS entwickelt, und zwar: Simatic S5-Familie von SPS Simatic S7-Familie von SPS Die Simatic S5-Serie war die vorherige SPS-Generation von Siemens und wird noch immer in einigen älteren Industriesystemen verwendet. Wird aber nicht mehr hergestellt. Die Simatic S7-Serie ist die aktuelle SPS von Siemens. Sie bietet eine breite Palette von CPUs mit unterschiedlichen Leistungs- und Funktionsstufen, um unterschiedliche Automatisierungsanforderungen zu erfüllen. Die S7-Serie ist für ihre Zuverlässigkeit, Robustheit und Flexibilität bekannt und wird häufig in Branchen wie der Automobil-, Lebensmittel- und Getränke- sowie Pharmaindustrie eingesetzt. Übersicht über die Siemens S7-SPS Die SPS-Generation Siemens S7 bietet eine breite Palette von CPUs mit unterschiedlichen Leistungs- und Funktionsstufen, um die Anforderungen verschiedener industrieller Automatisierungsprozesse zu erfüllen. Diese CPUs gehören zu einer der folgenden Unterfamilien: Simatic S7-1200 Die Simatic S7-1200 ist eine kompakte SPS für kleine bis mittelgroße Anwendungen. Mit ihrem kompakten Design, der integrierten Kommunikation und den Programmieroptionen bietet sie eine flexible und kostengünstige Automatisierungslösung. Simatic S7-1500 Die Simatic S7-1500 ist eine Hochleistungs-SPS für mittelgroße bis große Anwendungen. Sie bietet erweiterte Funktionen wie Bewegungssteuerung, Sicherheit und Schutz und eignet sich daher für komplexe Automatisierungsaufgaben. Simatic S7-300 Die Simatic S7-300 ist eine modulare SPS, die sich leicht an eine Vielzahl von Anwendungen anpassen lässt. Sie bietet eine hohe Verarbeitungsleistung, umfangreiche Kommunikationsoptionen und eine große Auswahl an E/A-Modulen und ist daher in vielen Branchen eine beliebte Wahl. Simatic S7-400 Die Simatic S7-400 ist eine Hochleistungs-SPS, die für anspruchsvolle Anwendungen entwickelt wurde, die eine hohe Verarbeitungsleistung und umfangreiche Kommunikationsfunktionen erfordern. Sie bietet eine große Anzahl an E/A-Modulen, Redundanzoptionen und erweiterte Diagnosefunktionen und eignet sich daher für komplexe Automatisierungsaufgaben. Simatic S7-ET 200SP Die Simatic S7-ET 200SP ist ein kompaktes Remote-E/A-System, das sich leicht in andere Simatic S7-SPS integrieren lässt. Sie bietet ein hohes Maß an Flexibilität, Skalierbarkeit und Modularität und eignet sich daher für verschiedene Automatisierungsanwendungen. Wenn Sie im TIA Portal ein neues Projekt erstellen und versuchen, ein neues Gerät hinzuzufügen, können Sie alle verfügbaren und unterstützten CPUs aus verschiedenen S7-Familien finden. Siehe Abbildung 1. Abbildung 1 – In der Simatic S7-Generation sind verschiedene SPSen verfügbar S7-1200 SPS Die Simatic S7-1200 ist eine vielseitige und kostengünstige SPS, die eine Reihe von Modellen bietet, um unterschiedliche Automatisierungsanforderungen zu erfüllen, was sie zu einer beliebten Wahl für kleine bis mittelgroße Anwendungen macht. Hier ist eine Übersicht über die verschiedenen Modelle der S7-1200-Serie: Simatic S7-1200 CPUs: Dies sind die Standard-CPUs der S7-1200-Serie und sie sind in verschiedenen Versionen erhältlich, darunter CPU 1211C, CPU 1212C, CPU 1214C, CPU 1215C und CPU 1217C. Sie bieten erweiterte Funktionen als die Basic Controller, einschließlich integrierter Kommunikationsschnittstellen und zusätzlicher E/A-Optionen. Sie sind auch in verschiedenen Versionen erhältlich, darunter DC/DC/DC, DC/DC/RLY, AC/DC/RLY und AC/DC/TC. Sie haben eingeschränkte Funktionen, sind aber ideal für einfache Steuerungsaufgaben. Simatic S7-1200 Safety Integrated: Dies ist eine sicherheitszertifizierte Version der S7-1200, die sicherheitsrelevante Funktionen wie Sicherheitseingänge, Sicherheitsausgänge und Sicherheitskommunikation enthält, um die Sicherheit des Automatisierungssystems zu verbessern. Simatic S7-1200 SIPLUS: Dies ist eine robuste Version der S7-1200, die für den Betrieb in rauen Umgebungen mit extremen Temperaturen, Feuchtigkeit und Vibrationen ausgelegt ist. Siehe Bild 2 für verschiedene Modelle der S7-1200. Bild 2 – Verschiedene Modelle der S7-1200-CPU S7-1500-SPS Die Simatic S7-1500 ist eine leistungsstarke SPS, die eine Reihe von Modellen bietet, um unterschiedliche Automatisierungsanforderungen zu erfüllen, was sie zu einer beliebten Wahl für anspruchsvolle Anwendungen macht. Hier ist eine Übersicht über die verschiedenen Modelle der S7-1500-Serie: Simatic S7-1500 Standard-CPUs: Dies sind die Standard-CPUs der S7-1500-Serie und sie sind in verschiedenen Versionen erhältlich, darunter CPU 1511-1 PN, CPU 1513-1 PN, CPU 1515-2 PN und CPU 1518-4 PN. Sie bieten Hochgeschwindigkeitsverarbeitung und erweiterte Kommunikationsoptionen wie Profinet, Profibus und Industrial Ethernet. Simatic S7-1500 Safety Integrated: Dies ist eine sicherheitszertifizierte Version der S7-1500, die sicherheitsrelevante Funktionen wie Sicherheitseingänge, Sicherheitsausgänge und Sicherheitskommunikation enthält, um die Sicherheit des Automatisierungssystems zu verbessern. Simatic S7-1500 Advanced Controller: Dies sind erweiterte Versionen der S7-1500, die zusätzliche Funktionen wie Bewegungssteuerung, Hochgeschwindigkeitszählung und erweiterte Kommunikationsoptionen bieten. Simatic S7-1500 T-CPU: Dies ist eine erweiterte Version der S7-1500-CPUs mit erweiterten Bewegungssteuerungsfunktionen wie Kinematikfunktionen sowie Getriebe- und Nockenfunktionen. Simatic S7-1500 TM NPU: Dies ist eine neuronale Verarbeitungseinheit (NPU), die für Anwendungen des maschinellen Lernens und der künstlichen Intelligenz (KI) wie vorausschauende Wartung, Qualitätskontrolle und Prozessoptimierung entwickelt wurde. Siehe Abbildung 3 für verschiedene Modelle der S7-1500. Bild 3 – Verschiedene Modelle der S7-1500 S7-300 SPS Simatic S7-300 CPUs: Dies sind die Standard-CPUs der S7-300-Reihe und sie sind in verschiedenen Versionen erhältlich, darunter CPU 312C, CPU 313C, CPU 314C, CPU 315-2DP, CPU 317-2DP und CPU 319-3PN/DP. Sie bieten hohe Verarbeitungsleistung, erweiterte Kommunikationsoptionen und eine breite Palette an E/A-Optionen. Simatic S7-300 fehlersichere CPUs: Dies sind sicherheitszertifizierte Versionen der S7-300 CPUs, die sicherheitsrelevante Funktionen wie Sicherheitseingänge, Sicherheitsausgänge und Sicherheitskommunikation umfassen, um die Sicherheit des Automatisierungssystems zu verbessern. Simatic S7-300 Compact CPUs: Dies sind kompakte Versionen der S7-300 CPUs, die eine geringere Größe und einen geringeren Stromverbrauch bieten und sich daher ideal für Anwendungen mit begrenztem Platz und begrenzter Stromversorgung eignen. Simatic S7-300 Technology CPUs: Dies sind spezialisierte CPUs, die für bestimmte Automatisierungsanwendungen wie Bewegungssteuerung, Temperaturregelung und Prozesssteuerung entwickelt wurden. Simatic S7-300 Distributed Controller: Dies sind modulare Controller, die verteilte E/A- und Kommunikationsoptionen bieten und sich daher ideal für Anwendungen eignen, die eine verteilte Automatisierung erfordern. Siehe Abbildung 4 für verschiedene Modelle von S7-300. Bild 4 – Verschiedene Modelle der S7-300 S7-400 SPS Simatic S7-400 CPUs: Dies sind die Standard-CPUs der S7-400-Reihe und sie sind in verschiedenen Versionen erhältlich, darunter CPU 412-1, CPU 414-1, CPU 414-2, CPU 416-2 und CPU 417-4. Sie bieten hohe Verarbeitungsleistung, erweiterte Kommunikationsoptionen und eine breite Palette an E/A-Optionen. Simatic S7-400H CPUs: Dies sind hochverfügbare CPUs, die Redundanzoptionen bieten, um die Verfügbarkeit und Zuverlässigkeit des Automatisierungssystems zu verbessern. Simatic S7-400F/FH CPUs: Dies sind sicherheitszertifizierte CPUs, die sicherheitsrelevante Funktionen wie Sicherheitseingänge, Sicherheitsausgänge und Sicherheitskommunikation umfassen, um die Sicherheit des Automatisierungssystems zu verbessern. Verteilte Steuerungen Simatic S7-400: Dies sind modulare Steuerungen, die verteilte E/A- und Kommunikationsoptionen bieten und sich daher ideal für Anwendungen eignen, die eine verteilte Automatisierung erfordern. Siehe Abbildung 5 für verschiedene Modelle von S7-400. Abbildung 5 – Verschiedene Modelle von S7-400 Simatic S7-ET 200 SPS Simatic S7-ET 200 CPUs: Dies sind die Standard-CPUs der S7-ET 200-Reihe und sie sind in verschiedenen Versionen erhältlich, darunter CPU 1511C-1 PN, CPU 1513-1 PN und CPU 1515-2 PN. Sie bieten hohe Verarbeitungsleistung, erweiterte Kommunikationsoptionen und eine breite Palette an E/A-Optionen. Simatic S7-ET 200F CPUs: Dies sind sicherheitszertifizierte CPUs, die sicherheitsrelevante Funktionen wie Sicherheitseingänge, Sicherheitsausgänge und Sicherheitskommunikation umfassen, um die Sicherheit des Automatisierungssystems zu verbessern. Simatic S7-ET 200SP CPUs: Dies sind kompakte CPUs mit reduzierter Größe und Stromverbrauch, was sie ideal für Anwendungen mit begrenztem Platz und begrenzter Stromversorgung macht. Siehe Abbildung 6 für verschiedene Modelle von S7-ET200. Bild 6 – Verschiedene Modelle von S7-ET200 Warum gibt es so viele verschiedene Modelle? Es gibt viele verschiedene Modelle von Siemens S7-SPS, die den Kunden eine große Auswahl an Optionen und Funktionen bieten, sodass sie die SPS auswählen können, die ihren spezifischen Automatisierungsanforderungen am besten entspricht. Die verschiedenen Modelle bieten unterschiedliche Funktionen, Verarbeitungsleistung, Speicher, Kommunikationsoptionen und E/A-Funktionen. Einige Modelle sind für bestimmte Anwendungen wie Bewegungssteuerung, Temperaturregelung und Prozesssteuerung konzipiert, andere für allgemeine Automatisierungssysteme. Da sich die Technologie weiterentwickelt und neue Automatisierungsanforderungen entstehen, entwickelt und veröffentlicht Siemens auch weiterhin neue Modelle und Versionen von S7-SPS mit erweiterten Funktionen und Fähigkeiten und bietet den Kunden die neueste Automatisierungstechnologie, mit der sie ihre Produktivität steigern, ihre Kosten senken und die Leistung ihres Systems verbessern können. Wie entscheide ich, welcher Typ von S7-SPS am besten zu meiner Anwendung passt? Die Auswahl des richtigen Typs von S7-SPS für Ihre Anwendung erfordert die sorgfältige Abwägung mehrerer Faktoren. Hier sind einige allgemeine Schritte, die Ihnen bei der Entscheidung helfen, welcher Typ von S7-SPS am besten zu Ihrer Anwendung passt: Bestimmen Sie die Größe und Komplexität Ihres Automatisierungssystems: Wenn Sie ein großes und komplexes Automatisierungssystem haben, benötigen Sie möglicherweise eine Hochleistungs-SPS wie die S7-400 oder S7-1500, die eine große Anzahl von E/A-Punkten und erweiterte Kommunikationsoptionen verarbeiten kann. Wenn Ihr System kleiner und weniger komplex ist, reicht möglicherweise eine kleinere SPS wie die S7-1200 oder S7-300 aus. Identifizieren Sie die erforderlichen E/A-Typen und zählen Sie sie: Jede S7-SPS verfügt über einen anderen Bereich an E/A-Optionen und Kapazitäten. Sie müssen den Typ und die Anzahl der E/A-Punkte bestimmen, die Sie für Ihre Anwendung benötigen, und die SPS auswählen, die diese unterstützen kann. Berücksichtigen Sie die erforderliche Verarbeitungsgeschwindigkeit und Leistung: Unterschiedliche S7-SPS haben unterschiedliche Verarbeitungsgeschwindigkeiten und Leistungsfähigkeiten. Sie müssen die erforderliche Verarbeitungsgeschwindigkeit bestimmen und die SPS auswählen, die Ihren Leistungsanforderungen gerecht wird. Bewerten Sie die erforderlichen Kommunikationsoptionen: Verschiedene S7-SPS bieten unterschiedliche Kommunikationsoptionen, wie Ethernet, Profibus, Profinet und AS-i. Sie müssen die erforderlichen Kommunikationsprotokolle für Ihre Anwendung bestimmen und die SPS auswählen, die diese unterstützt. Berücksichtigen Sie die erforderlichen Sicherheitsfunktionen: Wenn Ihre Anwendung Sicherheitsfunktionen wie Sicherheitseingänge, Sicherheitsausgänge und Sicherheitskommunikation erfordert, benötigen Sie möglicherweise eine sicherheitszertifizierte SPS wie die S7-1500F oder S7-400F. Fazit Siemens bietet eine breite Palette an Produkten für die industrielle Automatisierung, darunter verschiedene SPS-Modelle mit unterschiedlichen Funktionen und Leistungsmerkmalen, darunter die CPUs S7-1200, S7-1500, S7-300 und S7-400. Die vielen verschiedenen Modelle der Siemens S7-SPS bieten Kunden eine große Auswahl an Optionen und Funktionen. Bei der Auswahl des SPS-Modells, das am besten zu Ihrem Prozess passt, müssen vor der Auswahl der SPS einige Punkte berücksichtigt werden. Einige dieser Punkte sind die Anzahl der E/A, Sicherheitsanforderungen und Kommunikationsoptionen. -
SIEMENS-DE Verwendung von Taktspeicherbits im Siemens PLC TIA Portal
leizuofa posted A plc and hmi article in German in PLC programming learning
In diesem Artikel beschäftigen wir uns mit Taktmerkerbits im TIA-Portal und in der Siemens-SPS. Und wir zeigen, wie Sie die Verwendung der Merkerbits aktivieren und wie Sie dadurch das Codieren vieler Logikzeilen vermeiden können, um eine einfache Funktion zu erhalten, die Ihre SPS bereits intern ausführt. Inhalt: Was sind Taktmerkerbits? Die Notwendigkeit von Taktmerkerbits. Taktmerker in meinem Projekt aktivieren. Ein einfaches Programmbeispiel. Programmsimulation. Fazit. Was sind Taktmerkerbits? Ein Taktmerker ist ein Bitspeicher, der seinen binären Status periodisch im Verhältnis 1:1 ändert. Das bedeutet einfach, dass er seinen Status periodisch zwischen wahr und falsch mit einer vordefinierten Frequenz ändert. In der CPU sind 8 Taktmerkerbits vordefiniert, weshalb sie auch Taktmerkerbyte genannt werden. Sie entscheiden, welches Merkerbyte der CPU zum Taktmerkerbyte wird, wenn Sie die Verwendung des Merkerbytes aktivieren und die Taktmerkerparameter zuweisen. Die Notwendigkeit von Taktspeicherbits Sie brauchen den Taktspeicher nicht unbedingt, da Sie Ihre eigene Logik erstellen und dieselbe Funktionalität erreichen können. Es ist jedoch gut, ihn in der Tasche zu haben, wenn Sie eine solche Funktionalität benötigen. Denn das Erstellen von 8 separaten Logiken für 8 Taktspeicherbits wird einiges an Zeit und Mühe kosten und Ihr Programm möglicherweise unnötig groß machen. Sie können den Taktspeicher beispielsweise verwenden, um blinkende Anzeigelampen zu aktivieren oder periodisch wiederkehrende Vorgänge wie das Aufzeichnen von Istwerten zu initiieren. Jedem Bit des Taktspeicherbytes wird eine Frequenz zugewiesen. Siehe die folgende Tabelle. Bit des Taktspeicherbytes 7 6 5 4 3 2 1 0 Periode (s) 2.0 1.6 1.0 0.8 0.5 0.4 0.2 0.1 Frequenz (Hz) 0.5 0.625 1 1.25 2 2.5 5 10 Tabelle 1. Frequenzen der Taktspeicherbits gemäß dem TIA Portal-Hilfehandbuch. Taktspeicher in Siemens PLC aktivieren Um die Taktspeicherbits in Ihrer Logik zu verwenden, müssen Sie die Verwendung des Taktspeicherbytes in den Eigenschaften der CPU aktivieren. Siehe Abbildung 1. Abbildung 1 – Verwendung des Taktspeicherbytes aktivieren Sie können die Adresse des Bytes auswählen, das Sie dem Taktspeicher zuweisen möchten. Stellen Sie nur sicher, dass es nicht mit anderen Speicherbytes in Ihrer PLC-Logik in Konflikt gerät. Wie Sie auf dem Bild sehen, haben wir die Adresse 0 gewählt. Wenn Sie also das 2-Hz-Taktbit verwenden müssen, verwenden Sie das Bit %M0.3 Beispielprogramm für ein Tia Portal-Förderband In einem früheren Artikel haben wir ein einfaches Beispiel für ein Förderband verwendet, das ein Produkt zwischen Anfang und Ende des Bandes bewegt. Es gab eine Anzeige-LED, die EINSCHALTET, wenn das Band läuft. Siehe Bild 2. Bild 2 – Einfaches Förderbandsystem Wir verwenden dasselbe Beispiel, aber dieses Mal machen wir die LED mithilfe der Taktspeicherbits intuitiver. Dieses Mal verwenden wir die Taktspeicherbits mit der LED, um verschiedene Fälle des Prozesses anzuzeigen. Prozessbeschreibung In einem Förderbandsystem, das von einer SPS gesteuert wird, gibt es an den beiden Enden des Bandes zwei Anwesenheitssensoren, um die Anwesenheit eines Produkts zu erkennen. Wenn das Produkt am Anfang des Bandes erkannt wird, kann das Förderband über einen Start-Druckknopf gestartet werden. Wenn das Produkt das Ende erreicht, stoppt das Band automatisch und läuft erst wieder, wenn am Anfang erneut ein neues Produkt erkannt und der START-Druckknopf gedrückt wird. Die Anzeige-LED sollte je nach aktuellem Systemfall mehr als ein Verhalten aufweisen. Diese Fälle sind wie folgt: Wenn sich am Anfang des Bandes ein Produkt befindet, aber START noch nicht gedrückt wurde, sollte die LED mit einer Frequenz von 0,5 Hz blinken. Wenn das Förderband das Produkt bewegt, sollte die LED mit einer Frequenz von 2 Hz blinken. Wenn das Produkt das Ende des Bandes erreicht, sollte die LED EIN sein. Wenn das Produkt vom Ende entfernt wird, erlischt die LED. Projekt-IOs Wir haben 4 digitale Eingänge wie folgt: START: Start-Druckknopf zum Betreiben des Förderbands. STOP: Stopp-Druckknopf, um das Förderband jederzeit anzuhalten. P1: Anwesenheitssensor am Anfang des Bandes. P2: Anwesenheitssensor am Ende des Bandes. Wir haben auch 2 digitale Ausgänge wie folgt: MOTOR: Wenn aktiviert, beginnt das Förderband zu laufen. LED: wird gemäß der zuvor erwähnten Reihenfolge aktiviert. Programmcode Zuerst wählen wir unsere SPS aus und weisen die IO-Tags zu. Siehe Bild 3 Bild 3 – Zuweisen von Ein- und Ausgangs-Tags Vergessen Sie nicht, die Verwendung des Taktspeicherbytes zu aktivieren, wie in Bild 1 gezeigt. Wir werden zwei Codenetzwerke haben, eines für die Steuerung des Förderbands und ein anderes für die LED-Logik. Die Logik finden Sie in den Bildern 4 und 5. Bild 4 – Die Steuerlogik des Förderbands Bild 5 – Die Steuerlogik der LED Wie Sie sehen, wurde die Logik durch die Verwendung der Taktspeicherbits einfach und leicht lesbar. Stellen Sie sich vor, Sie würden dieselbe Logik ohne die Verwendung dieser Bits erstellen. Sie hätten viele Timer verwendet und Ihre Logik wäre ziemlich kompliziert gewesen. Programmsimulation Wir haben zuvor erklärt, wie wir PLCSim verwenden, um unseren Code zu simulieren. In diesem Beispiel verwenden wir die Simulationssequenz, um dieselbe Sequenz wie beim tatsächlichen Prozess zu erstellen und zu sehen, ob das LED-Verhalten der beabsichtigten Funktionalität entspricht oder nicht. Beginnen Sie mit der Kompilierung unseres Codes und starten Sie eine neue Simulation. Siehe Bild 6. Bild 6 – Programmsimulation Wie Sie sehen, ist die LED jetzt AUS; es sind keine Produkte am Anfang oder Ende des Förderbands vorhanden. Wir haben eine Simulationssequenz erstellt und sehen, wie die LED auf unterschiedliche Prozessbedingungen reagiert. Sehen Sie sich die folgende Animation an. Sehen Sie, ob Sie bemerken, wie sich das LED-Verhalten bei unterschiedlichen Prozessbedingungen ändert. Fazit Taktspeicherbits werden mit einer vordefinierten Frequenz ein- und ausgeschaltet. Sie sind sehr nützlich, wenn Sie blinkende Anzeigelampen aktivieren oder periodisch wiederkehrende Vorgänge einleiten müssen. Die Verwendung von Taktspeicherbits spart Ihnen die Zeit und den Aufwand, die Sie aufwenden würden, um dieselbe Funktionalität durch Ihre eigene Logik zu erreichen. -
SPS-Unterschied zwischen Timer und Zähler
leizuofa posted A plc and hmi article in German in PLC programming learning
Wenn Sie eine SPS-Logik entwickeln, benötigen Sie immer Timer und Zähler. Jeder Zyklus in einem Automatisierungsprozess ist im Allgemeinen ohne die Verwendung von Timern und Zählern unvollständig. Sie benötigen sie, um eine Aufgabe nach einer bestimmten Zeit auszuführen oder die Aufgabe für eine bestimmte Zeit ein-/auszuschalten. Ihre Verwendung hängt von der zu entwickelnden Anwendung ab. Und bevor ein Programmierer sich eingehend mit fortgeschrittenen Anweisungen der SPS befasst, muss er zunächst diese grundlegenden Blöcke verstehen, um sie richtig zu implementieren und Hilfe beim Erlernen der fortgeschrittenen Blöcke zu erhalten. In diesem Artikel lernen wir den Unterschied zwischen Timern und Zählern bei der SPS-Programmierung kennen. Was ist ein Timer? Ein Timer ist eine Anweisung, die verwendet wird, um einen Ausgang nach einer bestimmten Verzögerung ein- oder auszuschalten. Wenn Sie beispielsweise eine Lampe nach 5 Sekunden einschalten möchten, verwenden Sie einen Timer, um diese Aufgabe auszuführen. Ein Timer nimmt einen Eingang entgegen und wenn der Eingang eingeschaltet wird, wird seine Zeitmessung gestartet. Nach Ablauf der Zeit von 5 Sekunden wird der Timer-Ausgang eingeschaltet, wodurch die Lampe indirekt eingeschaltet wird. Wir sprechen hier von einem normalen Timer dieser Art. Es gibt zwei weitere Arten von Timern: Timer-Aus und Impulstimer. Kurz gesagt ist die Grundfunktion dieselbe: eine Aufgabe nach einer bestimmten Verzögerung ausführen. Zum besseren Verständnis siehe das obige Bild. Ein Timer hat vier Ein- und Ausgänge: Eingang, Sollwert, aktueller Wert und Ausgang. Ein Eingang nimmt die Bedingung zum Starten eines Timers an, ein Sollwert wird verwendet, um den eingestellten Timerwert anzunehmen, der aktuelle Wert zeigt den aktuellen laufenden Timerwert an und der Ausgang wird verwendet, um die damit verbundene Variable ein- oder auszuschalten. Wenn der PLC-Timer den Eingang erhält und der Sollwert 5 Sekunden beträgt, startet der Timer als 1, 2 und 3 und so weiter bis 5. Wenn 5 Sekunden abgelaufen sind, wird der Ausgang eingeschaltet. Wenn der Eingang ausgeschaltet wird, geht der aktuelle Wert des Timers sofort auf Null zurück. Ob der Timer lief oder nicht; Wenn der Eingang ausgeschaltet ist, startet der Timer nicht und sein Ausgang und sein aktueller Wert sind Null. Dies ist die Funktionsweise eines TON-Timers (Timer On Delay). Was ist ein Zähler? Ein Zähler ist eine Anweisung, die verwendet wird, um einen Ausgang einzuschalten, nachdem eine festgelegte Anzahl erreicht wurde. Die Anzahl kann entweder inkrementiert oder dekrementiert werden. Wenn Sie beispielsweise eine Lampe einschalten möchten, nachdem ein Druckknopf fünfmal gedrückt wurde, verwenden Sie einen Zähler, um diese Aufgabe auszuführen. Ein Zähler nimmt einen Eingang entgegen und wenn der Eingang eingeschaltet wird, wird sein Zähler auf 1 erhöht. Wenn der Eingang ausgeschaltet wird, passiert nichts. Wenn er den Eingang erneut empfängt, wird der Zähler auf 2 erhöht. Nachdem die Anzahl von 5 abgelaufen ist, wird der Zählerausgang eingeschaltet, wodurch die Lampe indirekt eingeschaltet wird. Wir sprechen hier vom Aufwärtszählertyp. Ein Zähler hat noch einen weiteren Typ – den Abwärtszähler. Kurz gesagt, die Grundfunktion ist dieselbe – eine Aufgabe nach einer bestimmten Anzahl ausführen. Zum besseren Verständnis siehe das obige Bild. Ein Zähler hat fünf Eingänge und Ausgänge – Zähleingang, Rücksetzeingang, Sollwert, aktueller Wert und Ausgang. Ein Zähleingang übernimmt die Bedingung zum Zählen, ein Rücksetzeingang übernimmt die Bedingung zum Zurücksetzen des Zählers, der Sollwert wird verwendet, um den Sollwert des Zählers zu übernehmen, der aktuelle Wert zeigt den aktuellen laufenden Zählerwert an und der Ausgang wird verwendet, um die damit verbundene Variable ein- oder auszuschalten. Wenn der Zähler den Zähleingang erhält und der Sollwert 5 ist, wird der Zähler auf 1 hochgezählt und so weiter bis 5; beim Empfang jedes Impulses im Zähleingang (d. h. der Zähleingang muss 5 Mal ein- und ausgeschaltet werden). Wenn 5 Zählungen abgeschlossen sind, wird der Ausgang eingeschaltet. Selbst wenn nun der Zähleingangsimpuls gegeben wird, wird der Zähler nach 5 weiter hochzählen und auch der Ausgang bleibt eingeschaltet. Um den Zählerstand wieder auf Null zurückzusetzen, müssen Sie einen Rücksetzeingang geben. Wenn dieser Eingang gegeben wird, wird der aktuelle Zählerwert Null und der Ausgang wird ebenfalls ausgeschaltet. Es ist also ähnlich wie bei der Funktion mit Verriegelung. Um den Zähler zu entriegeln, müssen Sie ihn zurücksetzen. Dies ist die Funktion eines CTU-Zählers (Count-Up-Zähler). Unterschied zwischen Timer und Zähler Die Hauptunterschiede zwischen Timern und Zählern in einer SPS sind wie folgt. Ein Timer muss seinen Eingang kontinuierlich haben, um eine Variable einzuschalten, aber ein Zähler muss seinen Eingang nicht kontinuierlich haben. Ein Timer arbeitet also unter kontinuierlichen Bedingungen, während ein Zähler unter Impulsbedingungen arbeitet. Wenn der Timer-Eingang entfernt wird, geht sein Ausgang zurück in den Nullzustand; aber wenn der Zähler-Eingang entfernt wird, behält der Zähler seinen letzten Wert bei. Ein Timer hat keinen Reset-Eingang, während ein Zähler einen Reset-Eingang benötigt, um den Zähler in seinen ursprünglichen Zustand zurückzusetzen. Die Arten von Timern sind – Timer ein, Timer aus und Timer-Impuls. Die Arten von Zählern sind – Zähler aufwärts und Zähler abwärts. Ein eingestellter Timerwert kann in Sekunden, Minuten oder Millisekunden angegeben werden; Der eingestellte Zählerwert ist jedoch eine feste Ganzzahl. -
MITSUBISHI-DE SPS-basiertes Produktsortiermaschinensystem – Liftsteuerung
leizuofa posted A plc and hmi article in German in PLC programming learning
In diesem fortschrittlichen SPS-Programm wird ein SPS-basiertes Produktsortiermaschinensystem verwendet, um verschiedene Produkte mithilfe des Lifts zu transportieren und die Teile nach Größe zu trennen. Hier sind drei Positionen verfügbar, je nach Größe, klein, mittel und groß. Die Förderbänder werden verwendet, um die Produkte zu transportieren und auf die Tabletts zu legen. SPS-basiertes Produktsortiermaschinensystem Die folgende Simulation zeigt das SPS-Sortiersystem mit Liftbetrieb. Ein- und Ausgänge Typ Gerätenr. Gerätename Betrieb Eingang X0 Oberer, höher EIN, wenn Teil erkannt wird. Eingang X1 Mitte EIN, wenn der Lift in einer unteren Position ist. Eingang X2 Unten EIN, wenn das Teil erkannt wird. Eingang X3 Teil auf Lift EIN, wenn das Teil erkannt wird. Eingang X4 Untere Liftposition EIN, wenn der Lift in der mittleren Position ist. Eingang X5 Mittlere Liftposition EIN, wenn der Lift in der mittleren Position ist. Eingang X6 Obere Liftposition EIN, wenn das Teil auf dem Lift ist. Eingang X10 Sensor EIN, wenn das Teil am linken Ende erkannt wird. Eingang X11 Sensor EIN, wenn das Teil am linken Ende erkannt wird. Eingang X12 Sensor EIN, wenn das Teil am rechten Ende erkannt wird. Eingang X13 Sensor EIN, wenn das Teil am linken Ende erkannt wird. Eingang X14 Sensor EIN, wenn das Teil am rechten Ende erkannt wird. Eingang X15 Sensor EIN, wenn der Lift in der oberen Position ist. Ausgang YO Versorgungskommando Ein Teil wird geliefert, wenn YO aktiviert ist: Metallzylinder wiederholt sich in der Reihenfolge S, L, M, L, M, S. Ausgang Y1 Förderband vorwärts EIN, wenn das Teil am rechten Ende erkannt wird. Ausgang Y2 Befehl zum Hochheben Der Aufzug fährt nach oben, wenn Y2 eingeschaltet ist. Der Aufzug stoppt, wenn Y2 ausgeschaltet ist. Ausgang Y3 Befehl zum Herunterheben Der Lift fährt nach unten, wenn Y3 eingeschaltet ist. Der Lift stoppt, wenn Y3 ausgeschaltet ist. Ausgang Y4 Befehl zum Anheben der Drehung Wenn Y1 eingeschaltet ist, bewegt sich das Förderband vorwärts. Ausgang Y5 Förderband senken vorwärts Der Lift dreht sich, um das Teil auf das Förderband zu übertragen, wenn Y4 EIN ist. Die Aufzüge drehen sich in die ursprüngliche Position zurück, wenn Y4 AUS ist. Ausgang Y6 Mittleres Förderband vorn Wenn Y5 eingeschaltet ist, bewegt sich das Förderband vorwärts. Ausgang Y7 Oberes Förderband nach vorn Wenn Y6 eingeschaltet ist, bewegt sich das Förderband vorwärts. Programmbeschreibung Das gesamte System besteht aus zwei Komponenten: Allgemeine Steuerung und Liftermanagement. Allgemeine Steuerung: Durch Aktivieren der Taste PB1 (X20) auf dem Bedienfeld wird der Zufuhrbefehl (Y0) für den Trichter initiiert. Durch Deaktivieren der Taste PB1 (X20) wird der Zufuhrbefehl (Y0) deaktiviert. Nach Aktivierung des Zufuhrbefehls (Y0) liefert der Trichter ein Teil. Die Förderer beginnen mit der Bewegung, wenn SW1 (X24) auf dem Bedienfeld aktiviert wird. Umgekehrt halten die Förderer die Bewegung an, wenn SW1 (X24) deaktiviert wird. Wenn der Sensor X10, X12 oder X14 links vom Förderer ein Teil erkennt, wird der entsprechende Förderer gestartet und transportiert das Teil zum Tablett am rechten Ende. Drei Sekunden nachdem ein Teil den Sensor X11, X13 oder X15 rechts vom Förderband passiert hat, wird das Förderband angehalten. Teile unterschiedlicher Größe (groß, mittel, klein) auf dem Förderband werden anhand der Eingänge der oberen (X0), mittleren (X1) und unteren (X2) Sensoren sortiert. Hebevorrichtungsverwaltung: Sobald das Teil auf dem Hebevorrichtungssensor (X3) in der Hebevorrichtung aktiviert wird, wird das Teil je nach Größe zu einem der folgenden Förderbänder transportiert: Großes Teil: Wird zum oberen Förderband geleitet Mittleres Teil: Wird zum mittleren Förderband geleitet Kleines Teil: Wird zum unteren Förderband geleitet Die Befehle zum Hochheben (Y2) und Herunterheben (Y3) werden basierend auf der Position der Hebevorrichtung verwaltet, die von den folgenden Sensoren erkannt wird: Oberes: X6 Mittleres: X5 Unteres: X4 Beim Transfer des Teils von der Hebevorrichtung zum Förderband wird der Befehl zur Hebevorrichtungsrotation (Y4) eingeleitet. Nach der Übergabe eines Teils kehrt der Lift in seine Ausgangsposition zurück und bleibt im Standby-Modus. PLC-Logik -
MITSUBISHI-DE SPS-Programm zur Bühnensteuerung – Vorhänge und Bühnenhöhenverstellung
leizuofa posted A plc and hmi article in German in PLC programming learning
Das SPS-Programm zur Bühnensteuerung ermöglicht das Öffnen und Schließen der Vorhänge sowie das Heben und Senken der Bühne. Es bietet zwei Betriebsarten: automatisch und manuell. SPS-Programm zur Bühnensteuerung Die folgende Simulation zeigt die Verwendung von SPS für Bühnensteuerungsanwendungen. Dies ist ein Hilfsprojekt, bei dem wir die Bühnenvorhänge automatisch und auch manuell mithilfe von Druckknöpfen öffnen und schließen müssen. Die Sensoren werden verwendet, um die Positionen der rechten und linken Vorhänge an verschiedenen Punkten zu erkennen. Nach dem Öffnen der Vorhänge wird die Bühne nach oben bewegt und in die oberste Position gehoben. Ebenso wird die mittlere Bühne nach unten bewegt, wenn die Vorhänge geschlossen sind. Die Bühnenposition wird auch mithilfe von unteren und oberen Grenzwertsensoren verfolgt. Liste der SPS-Geräte Die folgende Tabelle listet alle Ein- und Ausgänge in diesem SPS-Programm auf. Typ Gerätenr. Gerätename Betrieb Eingang X0 Innen (linker Vorhang) EIN, wenn der Vorhang halb aufgerissen ist. Eingang X1 EIN, wenn der Vorhang ganz schließt. EIN, wenn der Vorhang ganz öffnet. Eingang X2 Außen (linker Vorhang) EIN, wenn der Vorhang ganz schließt. Eingang X3 Innen (rechter Vorhang) EIN, wenn der Vorhang auf halbem Weg ist. Eingang X4 Mitte (rechter Vorhang) EIN, wenn der Vorhang ganz öffnet. Eingang X5 Außen (rechter Vorhang) EIN, wenn die Bühne eine untere Grenze erreicht. Eingang X6 Obere Bühnengrenze Die Bühne bewegt sich nach oben, wenn Y2 EIN ist. Die Bühne stoppt, wenn Y2 AUS ist. Eingang X7 Untere Bühnengrenze EIN, wenn die Bühne die obere Grenze erreicht. Ausgang Y0 Befehl Vorhang öffnen Vorhänge öffnen sich, wenn Y0 EIN ist. Vorhänge stoppen, wenn Y0 AUS ist. Ausgang Y1 Befehl Vorhang schließen Vorhänge schließen sich, wenn Y1 EIN ist. Vorhänge stoppen, wenn Y1 AUS ist. Ausgang Y2 Bühne auf Die Bühne bewegt sich nach oben, wenn Y2 EIN ist. Die Bühne stoppt, wenn Y2 AUS ist. Ausgang Y3 Bühne ab Die Bühne bewegt sich nach unten, wenn Y3 EIN ist. Die Bühne stoppt, wenn Y3 AUS ist. Ausgang Y5 Summer ertönt, wenn Y5 eingeschaltet ist (Lampe auf dem Bildschirm leuchtet). Programmbeschreibung SPS-Programm zur Steuerung von Bühneneinstellungen, einschließlich Öffnen/Schließen von Vorhängen und Heben/Senken der Bühne. Der Zweck dieses SPS-Programms besteht darin, die Steuerung einer Reihe von Bühneneinstellungen zu erleichtern, darunter Aufgaben wie Öffnen und Schließen von Vorhängen sowie Heben und Senken der Bühne selbst. Um unterschiedlichen Vorlieben und Anforderungen gerecht zu werden, bietet das Programm zwei verschiedene Betriebsmodi: automatisch und manuell. Automatischer Betrieb Wenn die „Begin“-Drucktaste (X16) auf dem Bedienfeld gedrückt wird, gibt ein Summer (Y5) einen 5 Sekunden langen Ton aus. Hinweis: Die „Begin“-Drucktaste (X16) kann nur aktiviert werden, wenn die Vorhänge geschlossen sind und die Bühne an ihrer unteren Grenze positioniert ist. Nachdem der Summer verstummt ist, wird der Befehl zum Öffnen der Vorhänge (Y0) aktiviert. Die Vorhänge öffnen sich weiter, bis sie ihre äußeren Grenzen erreichen, wie durch die Eingangssignale X2 und X5 definiert. Sobald die Vorhänge vollständig geöffnet sind, beginnt die Bühne mit dem Anheben, wenn der Befehl „Bühne auf“ (Y2) aktiviert wird. Die Bühne bewegt sich weiter nach oben, bis sie ihre obere Grenze erreicht, wie durch Eingangssignal X6 angezeigt. Durch Drücken der Taste „Ende“ (X17) auf dem Bedienfeld wird das Schließen der Vorhänge eingeleitet. Der Befehl zum Schließen der Vorhänge (Y1) wird aktiviert und die Vorhänge schließen sich, bis sie ihre inneren Grenzen erreichen, die durch Eingangssignale X0 und X3 definiert sind. Manueller Betrieb Die folgenden Vorgänge sind nur verfügbar, wenn der oben beschriebene automatische Betrieb nicht aktiv ist. Die Vorhänge können durch Drücken der Taste „Vorhang öffnen“ (X10) auf dem Bedienfeld geöffnet werden. Die Vorhänge halten an, sobald sie ihre äußeren Grenzen (X2 und X5) erreichen. Die Vorhänge können durch Drücken der Taste „Vorhang schließen“ (X11) auf dem Bedienfeld geschlossen werden. Die Vorhänge schließen sich weiter, bis sie ihre inneren Grenzen (X0 und X3) erreichen. Die Bühne kann durch Drücken der Taste „⬆ Bühne hoch“ (X12) auf dem Bedienfeld angehoben werden. Die Bühne stoppt, sobald sie ihre obere Grenze (X6) erreicht. Die Bühne kann durch Drücken der Taste „⬇ Bühne runter“ (X13) auf dem Bedienfeld abgesenkt werden. Die Bühne stoppt, sobald sie ihre untere Grenze (X7) erreicht. Die Anzeigelampen auf dem Bedienfeld leuchten bzw. erlöschen entsprechend und geben so eine visuelle Rückmeldung über den Status der Vorhänge und Bühnenvorgänge. SPS-Programmierung -
SIEMENS-DE Wie aktualisiere ich die Firmware-Version meiner SPS? – TIA Portal
leizuofa posted A plc and hmi article in German in PLC programming learning
In einem früheren Artikel haben wir über die Firmware-Version Ihrer SPS gesprochen und wie Sie Fehler behandeln, die aufgrund einer Firmware-Nichtübereinstimmung zwischen Ihrem Projekt im TIA Portal und Ihrer tatsächlichen SPS auftreten können. In diesem Artikel zeigen wir Ihnen, wie Sie die Firmware-Version Ihrer SPS aktualisieren. Inhalt: Was ist eine Firmware-Version? Warum kann die Firmware-Version mir Probleme bereiten? Wie erkenne ich die Firmware-Version meiner Hardware-SPS? Wie gehe ich mit Firmware-Versionsfehlern um? Wie aktualisiere ich die Firmware-Version meiner SPS? Fazit. Was ist eine Firmware-Version? Wie wir in einem früheren Artikel erklärt haben, ist die Firmware einer SPS oder eines SPS-Moduls (IOs, Kommunikationsmodule usw.) einfach die interne Software, die in der SPS installiert ist und dafür verantwortlich ist, was die Hardware tatsächlich tun kann. Eine SPS mit einer älteren Firmware-Version hat weniger Funktionen und interne Fähigkeiten als eine SPS mit einer neueren Firmware-Version. Bilder 1 und 2 zeigen Ihnen, wie dieselbe Hardware-SPS mit unterschiedlichen installierten Firmware-Versionen unterschiedliche Funktionen und Leistungsfähigkeit hat. Bild 1. Firmware-Version V4.0 Bild 2. Firmware-Version V4.4 Sie können sehen, dass der CPU jetzt durch das Update auf eine höhere Firmware-Version mehr Funktionen hinzugefügt wurden. Mit der höheren Firmware V4.4 verfügt die CPU jetzt neben anderen Funktionen, die ihre Leistungsfähigkeit verbessern, über OPC UA. Warum kann die Firmware-Version Probleme verursachen? Sie wählen Ihre SPS im TIA Portal nach einem der folgenden zwei Punkte aus: Sie haben die Hardware-SPS bereits gekauft, also wählen Sie dieselbe SPS aus, die Sie tatsächlich im TIA Portal-Projekt haben. Sie haben noch keine SPS gekauft, also wählen Sie im TIA Portal eine SPS aus, die Ihren Anforderungen entspricht, und kaufen diese dann später. In beiden Fällen tritt ein Problem auf, wenn die Firmware-Version der im TIA Portal-Projekt ausgewählten SPS von der Firmware-Version der tatsächlichen Hardware abweicht. Und bei manchen SPS wird Ihr Programm nicht einmal auf die Hardware-SPS heruntergeladen. Sie sollten also immer sicherstellen, dass die Firmware-Version der tatsächlichen SPS mit der im TIA-Portal ausgewählten SPS übereinstimmt. Es ist erwähnenswert, dass Sie keine Probleme mit Ihrem Programm haben werden, wenn die im TIA-Portal ausgewählte Firmware-Version älter ist als die der tatsächlichen SPS. Sie verlieren zwar einige der SPS-Funktionen und -Fähigkeiten, aber Ihr Programm wird einwandfrei funktionieren. Im Gegenteil treten Probleme auf, wenn die im TIA-Portal ausgewählte Firmware-Version neuer ist als die der tatsächlichen SPS. Dann haben Sie ein Problem. Wenn Sie die Firmware-Version Ihrer Hardware nicht kennen, sollten Sie daher im TIA-Portal-Projekt die ältere Version auswählen. Wie kann ich die Firmware-Version der Hardware-SPS herausfinden? Wir können die Firmware-Version der Hardware-SPS, die wir haben, auf eine von zwei Arten herausfinden: Von der SPS selbst: Die Firmware-Version jeder SPS oder jedes SPS-Moduls ist immer irgendwo auf dem Hardwaregerät vermerkt. Über die TIA Portal-Software: Mit der TIA Portal-Software können Sie Ihre SPS mit Ihrem TIA Portal verbinden und nach dem Gerät suchen. Anschließend können Sie die Firmware-Version des Hardwaregeräts finden. Wir haben im vorherigen Artikel gezeigt, wie das geht. Wie gehe ich mit Firmware-Versionsfehlern um? Wenn die Firmware-Version der tatsächlichen Hardware-SPS älter ist als die Version der im TIA Portal-Projekt ausgewählten SPS, führt dies zu Firmware-Fehlern. Um diese Fehler zu beheben, können wir einen der folgenden Ansätze ausprobieren: Wir können die SPS im TIA Portal-Projekt so auswählen, dass sie dieselbe oder eine ältere Firmware-Version wie die tatsächliche SPS hat. Das haben wir im vorherigen Artikel gezeigt. Wir können die Firmware-Version der tatsächlichen Hardware-SPS auf eine höhere Firmware-Version als die in Ihrem Projekt ausgewählte oder zumindest auf dieselbe Firmware-Version aktualisieren. Und das ist der Inhalt dieses Artikels. Wie aktualisiere ich die Firmware-Version meiner SPS? Sie können die Firmware-Version Ihrer SPS auf zwei Arten aktualisieren: Online über das TIA Portal. Offline über die Siemens Memory Card SMC. Aktualisieren Sie die Firmware online mit TIA Portal: Sie müssen kein vorhandenes Projekt im TIA Portal geöffnet haben, Sie benötigen lediglich die TIA Portal-Software und müssen die SPS mit Ihrem PC verbinden. Siehe Abbildung 3. Abbildung 3. Öffnen Sie Tia Portal, ohne ein neues Projekt zu erstellen. Wenn Sie TIA Portal öffnen, gehen Sie zum Online-Zugriff, wählen Sie den geeigneten Kommunikationsadapter zwischen Ihrer SPS und Ihrem PC und drücken Sie dann auf „Erreichbare Geräte aktualisieren“, um nach Ihrer SPS zu suchen. Siehe Abbildung 4. Abbildung 4. Suchen Sie Ihre SPS. Nachdem die SPS gefunden wurde, wie Sie im vorherigen Bild sehen können, öffnen Sie den SPS-Ordner und drücken Sie auf „Online und Diagnose“, um die SPS-Firmwareversion anzuzeigen. Siehe Abbildung 5. Abbildung 5. Die aktuelle Firmwareversion der SPS. Um JETZT die Firmwareversion zu aktualisieren, drücken Sie auf das Attribut „Firmware-Update“. Siehe Bild 6. Bild 6. Firmware-Update-Seite. Wie Sie sehen, wird beim Drücken des Attributs „Firmware-Update“ das aktuelle Firmware-Update V4.1.3 angezeigt. Außerdem wird der Firmware-Loader angezeigt, in dem Sie nach der Firmware-Version suchen können, die Sie installieren möchten. Natürlich muss die Firmware-Version zuerst auf Ihrem PC installiert sein, was bedeutet, dass wir die Firmware-Version herunterladen müssen. Um die Firmware-Version herunterzuladen, sollten Sie sich bei Ihrem Siemens-Konto anmelden. Wenn Sie noch keins haben, können Sie ganz einfach ein neues Konto erstellen. Die Aktivierung dauert jedoch 1 bis 2 Tage. Danach können Sie nach der Firmware-Version für Ihre SPS suchen. In unserem Fall haben wir eine S7-1200 CPU 1214C AC/DC/RLY und wir suchen anhand der Artikelnummer nach der Firmware-Version. Siehe Abbildung 7. Abbildung 7. Suchen Sie nach der Firmware-Version Ihrer SPS. Laden Sie anschließend die Firmware-Version herunter, die Sie installieren möchten. In unserem Fall möchten wir unsere SPS auf V4.4.0 aktualisieren, also laden wir diese Version auf unseren PC herunter. Siehe Bild 8. Bild 8. V4.4.0 herunterladen Die heruntergeladene Datei ist eine ZIP-Datei. Sie sollten die Datei entpacken, um die Datendatei mit der Firmware-Version zu erhalten, und dann zum Attribut „Firmware Loader“ zurückkehren und auf „Durchsuchen“ klicken, um nach der Firmware-Version zu suchen. Siehe Bild 9. Bild 9. Suchen Sie nach der Datei mit der Firmware-Version. Machen Sie sich keine Sorgen, dass Sie bei diesem Schritt einen Fehler machen, denn wenn die Firmware-Version nicht mit der SPS kompatibel ist, können Sie das Update nicht ausführen. Siehe Bild 10. Bild 10. Das Update wird nicht fortgesetzt, wenn die Firmware nicht übereinstimmt. Wie Sie sehen, trat beim Versuch, eine Firmware-Version für eine 1215C-CPU in unsere SPS mit einer 11214C-CPU hochzuladen, eine Fehlermeldung auf, dass die Datei nicht für die SPS geeignet sei. Klicken Sie JETZT erneut auf „Durchsuchen“, aber suchen Sie dieses Mal nach der richtigen Firmware-Version. Siehe Bild 11. Bild 11. Keine Fehlermeldung, wenn die Firmware-Version richtig ist. Wie Sie sehen, gab es keine Fehlermeldung, als wir eine geeignete Firmware-Version auswählten, und wir können jetzt auf „Update ausführen“ klicken, um mit der Aktualisierung unserer SPS zu beginnen. Sobald Sie den Aktualisierungsvorgang starten, wird ein Fenster zur Firmware-Aktualisierung angezeigt und am Ende wird eine Erfolgsmeldung angezeigt, wenn die Aktualisierung problemlos verlief. Siehe Bilder 12 und 13. Bild 12. Eine Firmware-Aktualisierung wird ausgeführt. Bild 13. Firmware-Aktualisierung erfolgreich abgeschlossen. Nachdem die Firmware-Version aktualisiert wurde, aktualisieren Sie Ihre Kommunikation, indem Sie erneut auf „Erreichbare Geräte aktualisieren“ klicken und die Firmware-Version der SPS überprüfen. Sie werden feststellen, dass die SPS jetzt die Firmware-Version V.4.4.0 statt V4.1.3 hat. Das bedeutet, dass wir die Firmware-Version unserer SPS aktualisieren konnten. Siehe Bild 14. Bild 14. Die Firmware wurde auf V4.44.0 aktualisiert Und so aktualisieren wir die Firmware-Version unserer SPS mithilfe des TIA-Portals. Offline mithilfe der Siemens-Speicherkarte SMC: Die andere Methode zum Aktualisieren der Firmware unserer SPS ist die Verwendung der SIEMENS-Speicherkarte SMC. Dazu müssen wir nur die Firmware-Version herunterladen, die wir verwenden möchten. Dann kopieren wir die Firmware-Version von unserer SPS auf die SMC und stecken die SMC in den dafür vorgesehenen Steckplatz in der SPS. Beim nächsten Einschalten der SPS wird die Firmware aktualisiert. Fazit Sie können die Firmware-Version mithilfe der TIA-Portal-Software oder der SIEMENS SMC-Speicherkarte aktualisieren. Achten Sie darauf, dass Sie die Firmware-Version genau richtig auswählen. Wenn eine Nichtübereinstimmung zwischen SPS und TIA-Portal besteht, wird das Update nicht gestartet. -
Schritte zur Inbetriebnahme vor Ort für SPS-Programmierer
leizuofa posted A plc and hmi article in German in PLC programming learning
Wenn ein neuer SPS-Programmierer vor Ort geht, um ein Projekt in Betrieb zu nehmen, stellt sich als allererstes die Frage, wie das geht. Das liegt daran, dass das SPS-System umfangreich und schwer zu verstehen ist. Daher muss jeder SPS-Programmierer wissen, was zu tun ist, wenn er vor Ort geht und die richtige Planung vornimmt. Bei einer so großen Anzahl von elektrischen Feldkabeln und -geräten ist es notwendig, zu verstehen, was er tut, und die SPS-Programmlogik zu verstehen. In diesem Beitrag lernen wir die Inbetriebnahmeschritte kennen, die ein SPS-Programmierer befolgen muss. Schritte zur Inbetriebnahme vor Ort für SPS-Programmierer Der allererste Schritt für einen SPS-Programmierer besteht darin, zu prüfen, ob er die gesamte erforderliche SPS-Software auf seinem Laptop installiert hat. Angenommen, der Standort verfügt über eine Automatisierung von Schneider im System. Dann muss er zuerst die gesamte entsprechende SPS-Software auf seinem Laptop installieren. Die Software muss jedes Mal korrekt geöffnet werden und alle zugehörigen Treiber müssen ebenfalls ordnungsgemäß reagieren. Danach muss er seinen Laptop an die Automatisierungshardware in seinem Büro anschließen. Dadurch wird sichergestellt, dass er ordnungsgemäß in das System hoch- und herunterladen kann. Eine unsachgemäße Softwareinstallation oder Konnektivität kann zu Fehlern bei der Inbetriebnahme vor Ort führen. Anschließend muss er die endgültige Sicherungskopie auf seinem Laptop erstellen und die SPS-Logik mit der Simulation überprüfen. Dadurch wird sichergestellt, dass er den gesamten Prozess versteht, wenn er vor Ort ist. Nehmen Sie anschließend alle Kommunikationskabel mit und machen Sie sich bereit, vor Ort zu gehen. Wenn sich herausstellt, dass das System aus Zeitgründen nicht vollständig überprüft wird, notieren Sie die ausstehenden Punkte und Logikfehler, die während des Tests festgestellt wurden. Stellen Sie sicher, dass dies bei der Inbetriebnahme überprüft wird. Sobald er vor Ort ist, werfen Sie zunächst einen Blick auf den Gesamtzustand der Anlage. Wie viele mechanische Arbeiten stehen noch aus, wie viele elektrische Arbeiten stehen noch aus; das ist am wichtigsten. Überprüfen Sie auch den Zustand der Versorgungseinrichtungen wie Wasser, Luft und Dampf. Notieren Sie alle Status und erstellen Sie eine tägliche Aktivitätenliste auf Ihrem Laptop. Geben Sie diese Datei an Ihren unmittelbaren Vorgesetzten weiter, damit dieser weiß, wo die Aktivität feststeckt, und die entsprechende Person entsprechend antreiben kann, um die Arbeit zu erledigen. Sobald das Panel zum Testen übergeben wurde, beginnen Sie mit der Überprüfung der Feld-IOs. Gemäß der IO-Liste und dem Schaltplan muss das entsprechende Feldgerät entsprechend funktionieren. Notieren Sie alle gefundenen Probleme und wenden Sie sich an den Elektriker, um sie zu beheben. Wenn das SPS-System Kommunikationsgeräte enthält, müssen Sie diese ebenfalls überprüfen. Alle Kommunikationsgeräte müssen in der Lage sein, im Netzwerkbus ordnungsgemäß mit dem SPS-Automatisierungssystem zu kommunizieren. Nachdem die Feldverdrahtung überprüft wurde, muss überprüft werden, ob alle mechanischen Geräte gemäß der Verdrahtung funktionieren oder nicht. Schließlich ist der Prozessablauf wichtig, und wenn das Gerät nicht reagiert, läuft der Prozess nicht ordnungsgemäß. Nachdem der gesamte Teil der Geräteüberprüfung abgeschlossen ist, besteht der nächste Schritt darin, die Logik mit dem Prozessingenieur zu überprüfen. Es muss überprüft werden, ob die Anlage gemäß der geschriebenen Logik läuft oder nicht. Wenn Probleme gefunden werden, prüfen Sie, ob sie durch Logik behoben werden können oder ob sie vom Prozessingenieur behoben werden müssen. Ziehen Sie eine Schlussfolgerung und lösen Sie diese. Damit ist Ihre SPS-Inbetriebnahmeaktivität abgeschlossen. Speichern Sie alle endgültigen Backups und übergeben Sie sie zur Sicherheit Ihrem Vorgesetzten. Notieren Sie sich außerdem alle endgültigen Prozessparameter und zeichnen Sie zum besseren Verständnis ein Video der laufenden Anlage auf. Erstellen Sie den Abschlussbericht und lassen Sie ihn vom Kunden unterschreiben, um nachzuweisen, dass die Inbetriebnahme erfolgt ist. Notieren Sie alle seine Anmerkungen und sorgen Sie dafür, dass sie so schnell wie möglich behoben werden. Schritte zur Inbetriebnahme der SPS Die wichtigsten Schritte zur Inbetriebnahme der SPS sind unten kurz aufgeführt. Dokumentation überprüfen: Überprüfen Sie die Systemanforderungen und Schaltpläne. Sicherheitsprüfungen: Überprüfen Sie Lockout/Tagout und andere Sicherheitsprotokolle. Hardwareprüfung: Überprüfen Sie die SPS und die E/A-Module auf Schäden. Einschalten: Schalten Sie die SPS ein und bestätigen Sie die Grundfunktionen. Kommunikation herstellen: Richten Sie Verbindungen zwischen der SPS und dem Programmierterminal ein. Firmware aktualisieren: Installieren Sie bei Bedarf die neueste SPS-Softwareversion. E/A konfigurieren: Richten Sie Eingangs- und Ausgangsmodule ein. Programm laden: Laden Sie den ursprünglichen SPS-Code in das System herunter. Testmodi: Überprüfen Sie einzelne Eingänge, Ausgänge und die Kommunikation. Schleifenprüfungen: Stellen Sie die Signalintegrität zwischen Feldgeräten und der SPS sicher. Logikprüfung: Überprüfen Sie die SPS-Funktionen und -Sequenzen. Simulation: Testen Sie komplexe Logik mit simulierten Eingaben. Prozessstart: Beginnen Sie mit dem ersten Testlauf des Prozesses. Feinabstimmung: Passen Sie die PID-Reglerabstimmung, Timer, Zähler und Sollwerte basierend auf den Testläufen an. Dokumentation aktualisieren: Protokollieren Sie während der Inbetriebnahme vorgenommene Änderungen. Funktionstests: Überprüfen Sie, ob das gesamte System wie erwartet funktioniert. Bedienerschulung: Bringen Sie den Bedienern bei, wie sie das neue Setup verwenden. Backup erstellen: Speichern Sie das endgültige SPS-Programm und die Konfigurationsparameter. Genehmigung durch den Kunden: Lassen Sie sich vom Kunden oder Projektmanager freigeben. Übergabe: Stellen Sie die Dokumentation für die Systemübergabe fertig. Auf diese Weise haben wir die Inbetriebnahmeschritte gesehen, die der SPS-Programmierer befolgen muss. -
ALLEN BRADLEY-DE AENT-Modul in Rockwell SPS – Remote-IO-Adapter
leizuofa posted A plc and hmi article in German in PLC programming learning
In der industriellen Automatisierung gibt es drei Arten von IOs – lokal, remote und verteilt. Dies definiert, ob sich die IOs in einem lokalen Schaltschrank oder einem Remote-Netzwerk-Panel befinden. Dies wird anhand der Position der Feldinstrumente vom Panel aus entschieden. Verschiedene Arten von Automatisierungsherstellern haben entsprechende Module in ihren Produkten, um mit Remote-IOs zu arbeiten. Eine dieser berühmten Marken ist Rockwell. In Rockwell SPS ist das AENT-Modul der am häufigsten verwendete Netzwerkadapter für die IO-Kommunikation. Dieses Modul kann an einem anderen Ort als der lokalen SPS angeschlossen werden und ist über Ethernet-Kommunikation mit dieser verbunden. Die entsprechenden IOs sind mit dem AENT-Modul verbunden. In diesem Beitrag werden wir uns das Konzept des AENT-Moduls in Rockwell SPS ansehen. AENT-Modul in Rockwell SPS Wie bereits erwähnt, ist ein AENT-Modul eine Art Remote-IO-Adapter. Das Modul enthält keine CPU; es handelt sich lediglich um eine Netzwerkschnittstelle, die zur Kommunikation von Feld-IOs mit der Haupt-SPS über das Ethernet-IP-Protokoll verwendet wird. Das bedeutet, dass keine Logik in das Modul geschrieben werden kann, da es nur Daten von damit konfigurierten IO-Modulen liest und an die Haupt-SPS-CPU schreibt. Sie können maximal 64 IO-Module mit einem AENT-Modul verbinden, um eine Schnittstelle herzustellen. Es wird im Allgemeinen durch die Serie 1734-AENT identifiziert. Über dieses Modul erhalten Sie nicht nur IO-Daten, sondern auch jede einzelne Diagnose der IOs. Dies erleichtert die Fehlerbehebung erheblich. Die Modulkommunikation erfolgt über das Ethernet-IP-Protokoll und verfügt hierfür über RJ45-Anschlüsse. Es kann entweder im Halbduplex- oder im Vollduplex-Modus kommunizieren. Die Standardstromversorgung für dieses Modul beträgt 24 V DC. IP-Adresskonfiguration Es gibt drei allgemeine Methoden, mit denen die IP-Adresse im Modul eingestellt wird – Durch Einstellen der Schalter darauf (es hat drei Zahlen, die die letzten drei Ziffern der IP-Adresse bezeichnen) Mithilfe der von Rockwell erhältlichen BootP/DHCP-Software Mithilfe der von Rockwell erhältlichen IP-Konfigurationssoftware. Sobald Sie die IP-Adresse eingestellt haben, können Sie das Modul für Ihre Kommunikation mit der Haupt-SPS verwenden. In der SPS-Software (Studio 5000) müssen die IO-Module in diesem AENT-Modul konfiguriert werden. Diese Module kommunizieren dann ihren IO-Status über das AENT-Modul an die Haupt-CPU. Dieses Modul kann in Sterntopologie oder Baumtopologie verwendet werden. LED-Diagnose Das Modul verfügt über die folgenden LEDs zur Diagnose – Modulstatus, Netzwerkstatus, Netzwerkaktivität, POINT-Bus-Status, Systemstrom und Feldstrom. Sie können eine detaillierte Beschreibung der einzelnen LEDs erhalten, indem Sie den Katalog lesen. Dies hilft bei der detaillierten Fehlerbehebung des Moduls. Zu beachten ist, dass das an das Modul angeschlossene Netzteil maximal 10 IO-Module ansteuern kann. Daher ist nach jeweils 10 an das AENT angeschlossenen Modulen ein Netzteilmodul erforderlich. Gehäusegröße Einer der wichtigsten Begriffe im Zusammenhang mit diesem Modul ist die Gehäusegröße. Gehäusegröße bezeichnet die Anzahl der mit AENT verbundenen Module. Wenn beispielsweise 19 IO-Module verwendet werden, müssen Sie die Gehäusegröße in der AENT-Konfiguration auf 20 einstellen. Der Adapter speichert diese Gehäusegrößeneinstellung im nichtflüchtigen Speicher. Wenn die nichtflüchtige Gehäusegröße des Adapters nicht mit der tatsächlichen Anzahl der auf seiner Rückwand vorhandenen Module übereinstimmt, stellt der Adapter keine I/O-Verbindungen her. Sobald Sie online sind, müssen Sie diese Größe außerdem online und nicht offline einstellen. Erst nach diesem Schritt können Sie das Modul zur Kommunikation von IO-Werten mit der Haupt-CPU verwenden. Das AENT-Modul ist ein Adapter höherer Reichweite und wird daher nur mit drei SPS-Typen verwendet – Control Logix, Compact Logix und Flex Logix. Auf diese Weise haben wir das Konzept des in Rockwell PLC verwendeten AENT-Moduls gesehen. -
So implementieren Sie SR Flip Flop mithilfe der SPS-Kontaktplanlogik
leizuofa posted A plc and hmi article in German in PLC programming learning
Dies ist das SPS-Programm zum Implementieren von SR Flip Flop in SPS. Lernen Sie die SPS-Programmierung mit dieser Beispiellogik. SR Flip Flop mithilfe der SPS-Kontaktplanlogik Problembeschreibung Implementieren Sie ein Programm für SR Flip Flop-Logik in SPS mithilfe der Kontaktplansprache. Problemdiagramm SPS-Lösung Wie wir wissen, können komplexere Systeme nicht allein mit kombinatorischer Logik gesteuert werden. Der Hauptgrund ist, dass wir keine Sensoren hinzufügen können oder wollen, um alle Bedingungen zu erkennen. In diesen Fällen können wir Ereignisse verwenden, um den Zustand des Systems abzuschätzen. SR Flip Flop wird zum Ein- oder Ausschalten verwendet – um etwas ein- oder auszuschalten. Die meisten PLCs haben spezielle Anweisungen für die SR Flip Flop-Funktion. Daher ist für diese Art von PLCs keine benutzerdefinierte Logik erforderlich. SR Flip Flop führt zuerst die SET-Funktion und dann die RESET-Funktion aus. Hinweis: Hier betrachten wir die einfache Funktion des SR-Flipflop-Befehls ohne Verwendung eines speziellen Befehls oder einer Latch-Funktion. Hier verwenden wir eine einfache Latch-Schaltung für die SR-Flipflop-Funktion. Hier werden wie in der Abbildung gezeigt zwei Drucktasten oder zwei Eingänge für die Programmimplementierung verwendet. Wenn der Benutzer die SET-Taste drückt oder 1 am S-Eingang empfangen wird, ist der Q-Ausgang EIN und wenn die RESET-Taste gedrückt wird oder 1 am R-Eingang empfangen wird, ist Q^ EIN. Liste der Ein-/Ausgänge Digitale Eingänge Set-Eingang: - I0.0 Reset-Eingang: - I0.1 Digitale Ausgänge Q-Ausgang: - Q0.0 Q^-Ausgang: - Q0.1 M-Speicher Relaisspule 1: - M0.0 Relaisspule 2: - M0.1 SPS-Kontaktplan zur Implementierung des SR-Flipflops Programm erklärt Für dieses SPS-Programm verwenden wir S7-300 SPS und TIA-Portalsoftware zur Programmierung. Wir können diese Logik auch mit anderen SPS implementieren. Netzwerk 1: Hier haben wir den NC-Kontakt der Relaisspule 1 (M0.0) verwendet, sodass der Q-Ausgang (Q0.0) ausgeschaltet ist, wenn die Reset-Taste gedrückt wird. Netzwerk 2: Hier haben wir den NC-Kontakt der Relaisspule 2 (M0.1) verwendet, sodass der Q^-Ausgang (Q0.1) AUS ist, wenn die Set-Taste gedrückt wird. Netzwerk 3: Hier wird die Relaisspule 1 (M0.0) verriegelt, wenn wir die RESET-Taste (I0.0) drücken. Netzwerk 4: Hier wird die Relaisspule 2 (M0.1) verriegelt, wenn wir die SET-Taste (I0.1) drücken. Wenn beide Eingänge beim Einschalten niedrig sind, wird der Q^-Ausgang (Q0.1) aufgrund seiner Reihenfolge hoch. Wenn beide Eingänge Hinweis: Die obige Anwendung kann von der tatsächlichen Anwendung abweichen. Dieses Beispiel dient nur zu Erklärungszwecken. Wir können diese Logik auch in anderen SPS implementieren. Dies ist das einfache Konzept der Implementierung der SR-Flip-Funktion ohne Anweisung. Wir können dieses Konzept auch in anderen Beispielen verwenden. Alle im Beispiel berücksichtigten Parameter dienen nur zu Erklärungszwecken. Die Parameter können in tatsächlichen Anwendungen unterschiedlich sein. Ergebnis -
SPS-Programm zum Lesen der Temperatur in der SPS
leizuofa posted A plc and hmi article in German in PLC programming learning
Dies ist ein SPS-Programm zum Lesen der Temperatur in der SPS. Lernen Sie die SPS-Programmierung anhand von Beispielproblemen und -lösungen. Temperatur in der SPS lesen Problembeschreibung Schreiben Sie ein SPS-Programm, in dem wir die tatsächliche Temperatur überwachen können. Hier verwenden wir einen externen Temperaturregler und sein Ausgang ist auch mit der SPS verbunden, um die Temperatur des Materials im Tank zu überwachen. Problemdiagramm Problemlösung RTD-Geräte mit einem Widerstand, der sich bei Temperaturänderungen linear ändert. Dieser Widerstandswert ändert sich bei Temperaturänderungen und durch Zufuhr eines konstanten Stroms kann der gemessene Spannungsabfall über dem Widerstand verwendet werden, um den neuen Widerstand und damit die Temperatur zu bestimmen. RTDs gibt es in verschiedenen Typen, der häufigste Typ ist ein PT100. Es besteht aus Platin, das auf 100 Ohm bei 0 Grad C kalibriert wurde. In der obigen Anwendung möchten wir die Materialtemperatur des Tanks messen. Dazu verwenden wir einen RTD-Sensor, der die Temperatur des Tanks misst und ein Signal an den Temperaturregler sendet. Der Temperaturregler sendet ein Signal in Form einer Spannung (0-10 V DC). Wenn der RTD eine Temperatur von 0 Grad erkennt, sendet er 0 V DC und wenn die Höchsttemperatur erkannt wird, sendet er 10 V DC an die SPS. Der Temperaturregler ist direkt mit der SPS verbunden, sodass die SPS die Spannung liest. Hinweis: – Hier betrachten wir zur Erklärung eine einfache Anwendung. Wir müssen die Materialtemperatur des Tanks mithilfe eines RTD-Sensors messen. Und berücksichtigen Sie auch andere Komponenten zu Steuerungszwecken. Angenommen, der Skalierungsbereich des Temperaturreglers beträgt 0-100 °C = 0 bis 10 V DC, und entsprechend diesem Signal berücksichtigt die SPS 0 bis 27648. E/A-Liste M-Speicher Analogwert vom Temperaturregler: MW100 Tatsächlicher Wert vom Temperaturregler: MD104 Multiplikation: MD108 Tatsächliche Temperatur in °C: MD112 SPS-Kontaktplandiagramm zum Ablesen der Temperatur Erklärung der SPS-Logik Für diese Anwendung haben wir S7-300 SPS und TIA-Portalsoftware zur Programmierung verwendet. Wir können diese Logik auch mit anderen SPSen implementieren. Netzwerk 1: In diesem Netzwerk implementieren wir eine Logik zur Wertkonvertierung. Es ist notwendig, den Wert für Multiplikationszwecke oder Berechnungen von INT in DINT umzuwandeln. Mithilfe der Konvertierungsanweisung wird der Analogwert des RTD (MW100) in einen tatsächlichen Analogwert (MD104) umgewandelt. Hinweis: Der Temperaturregler liefert ein 0-10-V-Gleichstromsignal an die SPS. Ein ADC-Konverter oder ein analoges Eingangsmodul wandelt dieses Analogsignal in eine digitale Form um, und der Bereich dieses Digitalsignals liegt zwischen 0 und 27648. Dieser Digitalbereich kann sich von einer SPS zur anderen ändern. Netzwerk 2: Wir haben einen RTD-Temperaturbereich von 0 bis 100 °C und einen Ausgangsspannungsbereich von 0 bis 10 V Gleichstrom. Wir müssen also diese Spannungsausgabe in Bezug auf die Temperaturanzeige skalieren. Hier multiplizieren wir den Wert gemäß der Gleichung und der Endwert wird in MD108 gespeichert. Hinweis: Hier liegt der Temperaturregler und der Temperaturmessbereich bei 0-100 °C. Netzwerk 3: Jetzt wird für das Endergebnis der multiplizierte Wert durch 27648 geteilt, das Ergebnis wird in MD112 (tatsächliche Temperatur in °C) gespeichert. Hinweis: Die obige Anwendung kann von der tatsächlichen Anwendung abweichen. Dieses Beispiel dient nur zu Erklärungszwecken. Wir können diese Logik auch in anderen SPS implementieren. Dies ist das einfache Konzept der Temperaturmessung in der S7-300-SPS. Wir können dieses Konzept auch in anderen Beispielen verwenden. Alle im Beispiel berücksichtigten Parameter dienen nur zu Erklärungszwecken. Die Parameter können in tatsächlichen Anwendungen unterschiedlich sein. -
SPS-Programm zur Skalierung von Regelventilen
leizuofa posted A plc and hmi article in German in PLC programming learning
Dies ist ein SPS-Programm zur Implementierung einer analogen Skalierung in einer SPS S7-300. Skalierung von Regelventilen Problembeschreibung Implementieren Sie ein SPS-Programm in S7-300 zur analogen Skalierung. Problemdiagramm Problemlösung Analoge Eingänge kommen von verschiedenen Sensoren oder Transmittern. Transmitter wandeln physikalische Größen in elektrische Signale um. Wir können viele physikalische Größen mithilfe von analogen Sensoren messen, wie z. B. Temperatur, Druck, Füllstand, Entfernung, Durchfluss usw. Natürlich können wir alle physikalischen Größen mithilfe von analogen Sensoren messen, aber als Beispiel und zur Erklärung nehmen wir hier ein Beispiel für ein Regelventil. Wie in der Abbildung gezeigt, betrachten wir hier ein Regelventil und es hat einen 4-20 mA-Ausgang (Ventilrückmeldung) und einen 4-20 mA-Eingang (Ventilbefehl) für den Betrieb. Wenn die SPS also 20 mA an das Durchflussregelventil abgibt, ist das Ventil zu 100 % geöffnet und bei 4 mA zu 0 % (geschlossen). Andererseits liefert das Durchflussregelventil auch ein Ausgangssignal, das für ein geschlossenes Kreislaufsystem/zur Anzeige des Ventilprozentsatzes verwendet werden kann. Wenn das Ventil zu 100 % geöffnet ist, erhält die SPS ein 20-mA-Signal und bei 0 % ein 4-mA-Signal. Hinweis: Wir betrachten hier zur Vereinfachung ein geschlossenes Kreislaufsystem, sodass der Bediener den Befehlsparameter zum Öffnen des Regelventils im Bereich zwischen 0 % und 100 % einstellt. Jetzt liefert das Regelventil gemäß dem geschlossenen Kreislaufsystem ein Ausgangssignal (Ventilrückmeldung) und mithilfe der SCALE-Anweisung kann der Bediener den tatsächlichen Ventilöffnungsparameter auf Grafiken sehen. Liste der Ein-/Ausgänge M-Speicher Aktivierungsbefehl – Skalierung: M0.0 Bipolare Auswahl – Skalierung: M0.1 Tatsächlicher Wert vom Sensor oder Transmitter: MW10 Fehlerwort – Skalierung: MW12 Skalierter Ausgang: MD20 Aktivierungsbefehl – Entskalierung: M1.0 Bipolare Auswahl – Entskalierung: M0.2 Angegebener Wert vom Display: MD24 Fehlerwort – Entskalierung: MW16 Unskalierter Ausgang: MW26 SPS-Kontaktplandiagramm für Ventilskalierung Kontaktplanlogik erklärt Für diese Anwendung verwenden wir S7-300 PLC und TIA-Portalsoftware zur Programmierung. Wir können diese Logik auch mit anderen SPS implementieren. Netzwerk 1: In diesem Netzwerk wird die Skalierungslogik ausgeführt, wenn der Befehl „Enable“ (M0.0) eingeschaltet ist. Der Befehl „Scale“ soll die Ganzzahl (hier 4-20 mA-Signal vom Steuerventil oder MW10) am Parameter IN konvertieren, die in physikalischen Einheiten zwischen einer Untergrenze (0 % Ausgabe) und einer Obergrenze (100 % Ausgabe) skaliert werden kann. Das Ergebnis oder die skalierte Ausgabe (MD20) des Befehls wird am Parameter OUT ausgegeben. Wenn die bipolare Auswahl (M0.1) eingeschaltet ist, wird angenommen, dass der Wert am Parameter IN bipolar ist (Bereich zwischen -27648 und +27648). Wenn die bipolare Auswahl (M0.1) ausgeschaltet ist, wird angenommen, dass der Wert am Parameter IN unipolar ist (Bereich zwischen 0 und 27648). Netzwerk 2: Der Befehl „Unscale“ wird verwendet, um die Gleitkommazahl (angegebener Wert aus der Anzeige oder MD24) im Parameter IN in physikalische Einheiten zwischen einer Untergrenze und einer Obergrenze zu skalieren. Das Ergebnis des Befehls wird am Parameter OUT ausgegeben (unskalierte Ausgabe MW26). Wenn die bipolare Auswahl (M0.2) eingeschaltet ist, wird angenommen, dass der Wert am Parameter IN bipolar ist (Bereich zwischen -27648 und +27648). Wenn die bipolare Auswahl (M0.2) ausgeschaltet ist, wird angenommen, dass der Wert am Parameter IN unipolar ist (Bereich zwischen 0 und 27648). Fehlercodetabelle: Hinweis: Die obige Anwendung kann von der tatsächlichen Anwendung abweichen. Dieses Beispiel dient nur zu Erklärungszwecken. Wir können diese Logik auch in anderen SPS implementieren. Dies ist das einfache Konzept der Befehle SCALE und UNSCALE. Wir können dieses Konzept auch in anderen Beispielen verwenden. Alle im Beispiel berücksichtigten Parameter dienen nur zu Erklärungszwecken. In tatsächlichen Anwendungen können die Parameter anders sein. Ergebnis -
Beispiele für die Programmierung von SPS-Timern – TON, TOF, TP und TONR
leizuofa posted A plc and hmi article in German in PLC programming learning
Diskussion über Beispiele für die Programmierung von SPS-Timern: Verschiedene SPS-Timer sind TON, TOF, TP und TONR. SPS-Timer-Anweisungen und Beispiele für die SPS-Timer-Logik. SPS-Timer-Programmierung Implementierung von IEC-Timern (TON, TOF, TP &TONR) in S7-1200 SPS mithilfe des TIA Portals. In vielen Anwendungen besteht die Anforderung, Zeit oder Signalfluss zu steuern. Beispielsweise muss ein Ventil oder ein Motor so gesteuert werden, dass er für eine bestimmte Zeitspanne läuft, nach einer bestimmten Zeitspanne oder nach einer gewissen Verzögerung eingeschaltet wird. Problemdiagramm Problemlösung Für dieses Problem verwenden wir IEC-Timer (TON, TOF, TP &TONR) in S7-1200 PLC mit Beispielen. In PLCs sind eine Reihe verschiedener Formen von Timern zu finden. Wie im obigen Diagramm gezeigt, wird der Einschaltverzögerungstimer nach einer bestimmten Zeitverzögerung eingeschaltet. Der Ausschaltverzögerungstimer ist nach dem Ausschalten des Eingangs für eine festgelegte Zeitspanne eingeschaltet. Der Impulstimer schaltet für eine festgelegte Zeitspanne ein oder aus. Der Akkumulatortimer zeichnet Zeitintervalle auf. Betrachten wir hier das Beispiel von vier Motoren und vier SCHALTERN zur Erklärung von Timern. Wir müssen drei Motoren auf unterschiedliche Weise starten. Der erste Motor startet nach einer Verzögerung von 10 Sekunden, der zweite Motor startet sofort und schaltet nach einer Verzögerung von 10 Sekunden aus, der dritte Motor startet mit einem Impuls und schaltet mit einer Verzögerung von 10 Sekunden aus. Der vierte Motor läuft insgesamt 10 Sekunden. Liste der Eingänge/Ausgänge Liste der Eingänge SCHALTER 1: I0.0 SCHALTER 2: I0.1 SCHALTER 3: I0.2 SCHALTER 4: I0.3 Reset: I0.4 Liste der Ausgänge MOTOR 1: Q0.0 MOTOR 2: Q0.1 MOTOR 3: Q0.2 MOTOR 4: Q0.3 SPS-Kontaktplan für Timer Wir können die Anweisung „Einschaltverzögerung generieren“ oder „Einschaltverzögerung“ verwenden, um das Setzen des Ausgangs Q um die programmierte Dauer PT zu verzögern. Die Anweisung wird gestartet, wenn das Ergebnis des Eingangs IN von 0 auf 1 wechselt (positive Flanke). Sie können den aktuellen Zeitwert am ET-Ausgang des Timerblocks überwachen. Der Timerwert beginnt bei T#0s und endet, wenn der Wert der Dauer PT erreicht ist. Der ET-Ausgang wird zurückgesetzt, sobald der Signalzustand am Eingang IN auf 0 wechselt. Mit der Anweisung Ausschaltverzögerung generieren oder Ausschaltverzögerungstimer können wir das Zurücksetzen des Ausgangs Q um die programmierte Dauer PT verzögern. Der Ausgang Q wird gesetzt, wenn das Ergebnis der logischen Verknüpfung (RLO) am Eingang IN von 0 auf 1 wechselt (positive Signalflanke). Wir können den aktuellen Zeitwert am ET-Ausgang überwachen. Mit der Anweisung Impuls generieren können wir den Ausgang Q für eine programmierte Dauer setzen. Die Anweisung wird gestartet, wenn das Ergebnis des Eingangs IN von 0 auf 1 wechselt (positive Flanke). Die programmierte Zeit (PT) beginnt, wenn die Anweisung gestartet wird. Bei diesem Timer wird der Signalzustand am Ausgang Q selbst dann nicht beeinflusst, wenn eine neue positive Flanke erkannt wird, solange die PT-Zeitdauer läuft. Der Zeitakkumulatorbefehl oder Akkumulatortimer wird verwendet, um Zeitwerte innerhalb eines durch den Parameter „Programmierte Zeit“ (PT) festgelegten Zeitraums zu akkumulieren. Wenn der Signalzustand am Eingang IN von 0 auf 1 wechselt (positive Flanke), wird der Befehl ausgeführt und die Dauer PT startet. In diesem Fall bleibt der Parameter Q auf 1 eingestellt, auch wenn der Signalzustand am Parameter IN von 1 auf 0 wechselt (negative Flanke). Der Eingang R setzt den Ausgang Q zurück. Programmbeschreibung In diesem Problem berücksichtigen wir die S7-1200-SPS und die TIA-Portalsoftware zur Programmierung. Netzwerk 1: In diesem Netzwerk haben wir einen Einschaltverzögerungstimer (Einschaltverzögerung generieren) für MOTOR 1 (Q0.0) verwendet. Wenn sich der Status von SCHALTER 1 (I0.0) von 0 auf 1 ändert, wird die Timeranweisung ausgeführt und aktiviert MOTOR 1 (Q0.0) nach einer Verzögerung von 10 Sekunden. Netzwerk 2: In diesem Netzwerk haben wir einen Ausschaltverzögerungstimer (Ausschaltverzögerung generieren) für MOTOR 2 (Q0.1) verwendet. Wenn sich der Status von SCHALTER 2 (I0.1) von 0 auf 1 ändert, wird die Timeranweisung ausgeführt und aktiviert MOTOR 2 (Q0.1) sofort. Auch wenn sich der Status von SCHALTER 2 (I0.1) wieder auf 0 ändert, wird die programmierte Zeit (PT) gestartet und nach Ablauf der Zeit ist MOTOR 2 (Q0.1) AUS. Netzwerk 3: In diesem Netzwerk haben wir einen Impulstimer (Impuls generieren) für MOTOR 3 (Q0.2) verwendet. Wenn der Status von SCHALTER 3 (I0.2) von 0 auf 1 wechselt, wird die Timeranweisung ausgeführt und aktiviert MOTOR 3 (Q0.2) sofort. In diesem Fall wird der Status von MOTOR 3 (Q0.2) selbst dann nicht beeinflusst, wenn eine neue positive Flanke erkannt wird, solange die programmierte Zeit (PT) läuft. Netzwerk 4: In diesem Netzwerk haben wir einen Akkumulatortimer (Akkumulatorzeit) für MOTOR 4 (Q0.3) verwendet. Wenn der Status von SCHALTER 4 (I0.3) von 0 auf 1 wechselt, wird die Timeranweisung ausgeführt und MOTOR 4 (Q0.3) startet nach 10 s. MOTOR 4 (Q0.2) bleibt eingeschaltet, auch wenn der Eingangsstatus wieder auf 0 wechselt. Der Reset (I0.4) ist erforderlich, um den Timer oder die akkumulierte Zeit zurückzusetzen. Laufzeittestfälle -
SPS-Programm für positive Flankenimpulsausgabe für einen Scanzyklus
leizuofa posted A plc and hmi article in German in PLC programming learning
Dies ist ein SPS-Programm für positive Flankenimpulsausgabe für einen Scanzyklus. Lernen Sie die Leiterlogik mit der Lösung. Positive Flankenimpulsausgabe Problembeschreibung In einigen Anwendungen müssen wir eine Operation/Funktion basierend auf einem externen Eingangssignal ausführen. Wir können einen digitalen Eingang als Auslösebefehl verwenden, um die erforderliche Funktion zu aktivieren. Manchmal verwenden wir einen positiven Übergang des digitalen Eingangssignals, um den Befehl auszulösen, anstatt eines kontinuierlichen/Vollimpuls-Digitaleingangssignals. Hier betrachten wir ein Beispiel für eine einfache Logik, in der zwei Registerwerte nach Erhalt des Auslösebefehls inkrementiert werden. Jedes Register hat einen voreingestellten Wert, sagen wir „1“. Daher werden bei jedem Auslösebefehl die Werte des Addiererregisters um den Wert „1“ inkrementiert. Für das Addiererregister 1 verwenden wir einen durch positive Flanke (0 bis 1) ausgelösten Eingang und für das Addiererregister 2 verwenden wir ein einfaches digitales Eingangssignal (0 bis 1 und 1 bis 0). Wir sehen die Vor- und Nachteile der Verwendung eines Auslösebefehls mit und ohne positive Flanke. Wir können dieselbe Logik in anderen Anwendungen verwenden, z. B. zum Nullsetzen der Registerwerte, zum Erzwingen der Registerwerte mit einem definierten Wert mit geringen logischen Änderungen usw. Problem Lösung Wir können diese Art von Problemen durch eine positive oder steigende Flanke des digitalen Eingangs lösen. Hier betrachten wir die S7-300-SPS zur Programmierung, damit wir den Wert überwachen und simulieren können. Wir können PLC SIM zu Simulationszwecken verwenden. Hier haben wir ein einfaches Beispiel betrachtet. In diesem Beispiel betrachten wir das Register „Addierer 1“, das den Wert „1“ addiert, wenn der Übergang von 0 auf 1 des Triggerbefehls erfolgt. Der Registerwert wird nach jeder Auslösung um den Wert 1 erhöht. Für das Register „Addierer 2“ wird der Wert nach dem Empfang des digitalen Eingangs erhöht. Hier verwenden wir keine positive Flankentriggerung. Liste der Ein-/Ausgänge Liste der Eingänge Triggerbefehl: I0.0 Speicherspule Positive Flanke des Triggerbefehls: M0.0 Gesamtwert: MW2 Gesamtwert 2: MW4 SPS-Kontaktplanlogik Netzwerk 1: Der Anfangswert des Registers „Addierer 1“ ist Null. Nach 18-maligem Auslösen des Triggerbefehls mit positiver Flanke ist die Ausgabe der Wert 18, da sie um den Wert „1“ erhöht wird. Simulation (PLCSIM-300) für Triggerbefehl mit positiver Flanke. Netzwerk 2: Der Anfangswert des Registers „Addierer 2“ ist Null. Nach 18-maligem Auslösen des Triggerbefehls (ohne positive/negative Flanke) ist die Ausgabe eine Zufallszahl (z. B. 7506) anstelle des Werts 18, wie es beim direkt empfangenen Triggerbefehl der Fall ist. Simulation (PLCSIM-300) für Triggerbefehl ohne positive Flanke. SPS-Logikbeschreibung In dieser Anwendung haben wir Siemens S7-300 PLC und TIA Portal Software zur Programmierung verwendet. Hier haben wir zwei Beispiele zur Erklärung positiver Flanken betrachtet. Jeder kann das Konzept leicht verstehen. In Netzwerk 1 erfolgt, wenn der Triggerbefehl (I0.0) ausgelöst wird, ein Übergang von 0 auf 1 und der positive Impulsbefehl wird ausgeführt. Angenommen, das Register „Addierer 1“ wird mit dem Wert „1“ in MW0 gespeichert. Wenn der Triggerbefehl (I0.0) ausgelöst wird, wird der Wert um „1“ erhöht. Hier haben wir beispielsweise 18 Mal ausgelöst, wenn Addierer 1 Null ist, also hat der Addierer 18 zum Gesamtwert (MW0) addiert. Ein weiteres Beispiel haben wir in Netzwerk 2 ohne Verwendung eines positiven Impulses genommen. Hier können Sie also das Ergebnis sehen. Angenommen, wir haben 18 Mal gedrückt oder ausgelöst, aber es wurden 7506 (das ist ein zufälliger Wert, der während der Simulation anders sein kann) zum Gesamtwert 2 (MW4) addiert, also ist es keine richtige Addition. Denn ein Impuls hat steigende oder fallende Flanken/positive oder negative Impulse (0 zu 1 und 1 zu 0). Auch hier haben wir PLC SIM zur Simulation verwendet, also können wir die Gesamtaddition simulieren. Im ersten Netzwerk haben wir eine positive Flanke hinzugefügt, also zeigt der Simulator 18. Im zweiten Netzwerk haben wir einen Triggerbefehl ohne positive Flanke hinzugefügt, also zeigt er einen zufälligen Wert. Das ist das Konzept der positiven Flanke, wir können diese positive Flanke während jeder Programmieranwendung verwenden. Das obige Programm und die Simulation dienen nur zu Erklärungszwecken und der Simulationswert kann während der Simulationszeit anders sein. Ergebnis Hinweis: Die obige PLC-Logik liefert eine grundlegende Idee zur Anwendung des Triggerbefehls mit positiver Flanke in der PLC-Logik. Die Logik ist begrenzt und keine vollständige Anwendung. -
SPS-Programm für tägliche Produktionsaufzeichnungen
leizuofa posted A plc and hmi article in German in PLC programming learning
SPS-Programm für tägliche Produktionsaufzeichnungen. Lernen Sie die Problembeschreibung mit einer detaillierten Erklärung der Kontaktplanlogik. Tägliche Produktionsaufzeichnungen Problembeschreibung In vielen Branchen muss die Anzahl der an einem Tag hergestellten Produkte gezählt werden, und dies ist sehr wichtig, um die Produkte zu verkaufen oder die Produktionsmenge täglich zu verfolgen. Früher wurden menschliche Bediener mit der Zählung der Endprodukte beauftragt, aber aufgrund einiger menschlicher Fehler ist eine genaue Zählung nicht möglich. Daher können wir nicht alle Produkte richtig zählen und die Produktionsmenge nicht effektiv verfolgen. Meistens treten diese Arten von Problemen in der Lebensmittel- und Getränkeindustrie, der Kartonverpackungsindustrie, bei Flaschenabfüllanwendungen usw. auf. Daher können wir eine einfache SPS-basierte Logik verwenden, um die tägliche Produktion zu verfolgen und elektronisch aufzuzeichnen. Problemdiagramm SPS-Lösung Hier werden wir das Problem der Zählung der Endprodukte mithilfe von Sensoren und SPS-Programmierung lösen. Der erste Sensor erfasst das Produkt und zählt die Menge. Der Wert wird auf der Digitalanzeige angezeigt (siehe Abbildung oben). Zur Vereinfachung betrachten wir ein einfaches Beispiel für ein System zum Zählen leerer Kartons. In diesem System werden leere Kartons vom ersten Prozess zum zweiten Prozess transportiert (also von einem Ort zum anderen). Der Sensor wird zum Zählen der leeren Kartons verwendet. Wenn der Sensor also einen leeren Karton erkennt, beginnt die Anzeige, also das Zählen von 1, und dies geschieht mit einer einfachen Logik. Alle 24 Stunden bzw. nach einem Tag können wir den Zählerwert mit der RESET-Taste zurücksetzen. Zur Vereinfachung betrachten wir hier zwei Produktionschargen. Außerdem haben wir für jede Charge zwei Chargenabschlussanzeigen für den Bediener berücksichtigt, die auf dem lokalen Bedienfeld angezeigt werden. Mit der SPS-Logik implementieren wir die gewünschte Logik. Wenn also eine Charge abgeschlossen ist, leuchtet die Anzeigelampe gemäß dem SPS-Programm. Sobald das Produktionsziel erreicht ist, kann der Anzeigezähler mit der RESET-Taste zurückgesetzt werden. Liste der Ein-/Ausgänge Eingabeliste Boxdetektorsensor: I0.0 Reset: I0.1 Hauptschalter: I0.2 Ausgabeliste Ziel erreicht: Q0.0 Charge 1 erreicht: Q0.1 Charge 2 erreicht: Q0.2 Kontaktplan für tägliche Produktionsaufzeichnung SPS-Programmbeschreibung In dieser Anwendung haben wir Siemens S7-1200 PLC und TIA Portal Software zur Programmierung verwendet. Netzwerk 1: In Netzwerk 1 haben wir den Hauptschalter (I0.2) verwendet, um das System/die Charge zu starten, und wir haben den Schließerkontakt des Boxdetektorsensors (I0.0) in Reihe verwendet. Hier haben wir einen Aufwärtszähler betrachtet, sodass der Zähler zu zählen beginnt, wenn der Boxdetektorsensor (I0.0) die Box erkennt. Hier haben wir auch den Zielerreichungsausgang (Q0.0) zur Zielerreichungsanzeige für die Bedieneranzeige auf dem Bedienfeld verwendet. Durch Drücken der RESET-Taste (I0.1) kann der Bediener den alten Produktionsdatensatz ZURÜCKSETZEN. Der Zählerbetrieb wird zum Zählen der Produkte verwendet, wobei RESET (I0.1) zum Zurücksetzen des Produktionsdatensatzes verwendet wird. Der voreingestellte Wert (PV) beträgt 20 Produkte. Der Zählerwert (CV) ist MW2 und gibt die tatsächliche Anzahl der vom Sensor erkannten Produkte an. Dieser Wert wird in den folgenden Sprossen verwendet, um den Chargenstatus zu verfolgen. Netzwerk 2: In Netzwerk 2 haben wir die Charge1-Logik vom Zählerblockausgang CV verwendet. Hier haben wir einen Komparator zum Zählen von 10 Kartons für Charge 1 verwendet. Wenn dieser abgeschlossen ist, leuchtet die Lampe „Charge 1 abgeschlossen“ (Q0.1). In diesem Fall wird ein gleicher Komparator hinzugefügt, dessen Eingang (MW2) ist und der für 10 Produkte gilt. Netzwerk 3: In Netzwerk 3 haben wir die Charge1-Logik vom Zählerblockausgang CV verwendet. Hier haben wir einen Komparator verwendet, um 20 Kartons für Charge 2 zu zählen. Wenn dieser abgeschlossen ist, wird die Lampe für Charge 2 (Q0.2) eingeschaltet. Auf diese Weise können wir entscheiden, wie viele Produkte und Chargen produziert werden. Laufzeittestfälle Hinweis: Die obige SPS-Logik liefert eine grundlegende Vorstellung von der Anwendung von SPS in der industriellen Produktionsaufzeichnung. Die Logik ist begrenzt und keine vollständige Anwendung. -
SPS-Programm für den Wasserfüll- und -entleerungsprozess
leizuofa posted A plc and hmi article in German in PLC programming learning
Dies ist ein SPS-Programm für den Wasserfüll- und -entleerungsprozess mit S7-1200 SPS. Wasserfüll- und -entleerungsprozess Problembeschreibung In vielen Branchen oder Werken werden viele manuelle Wasserfüllsysteme zur Wasserspeicherung verwendet. Das manuelle System hat viele Nachteile, wie z. B. Genauigkeit, Zeitverzögerungsprobleme, Flüssigkeitsverlust und Zeitaufwand. Und aufgrund des manuellen Systems müssen wir einen Bediener für die Bedienung der Maschine einsetzen. Durch das manuelle System kommt es zu Wasserverschwendung. Hier diskutieren wir ein halbautomatisches System. Diagramm SPS-Lösung Um dieses Problem zu lösen, verwenden wir zur Programmierung eine S7-1200 SPS. Hier verwenden wir zwei Sensoren zur Füllstandsmessung, einen für hohen Füllstand und einen für niedrigen Füllstand. Wir verwenden ein Zufuhrventil (MV1) für den Füllzyklus des Tanks und ein Ablassventil (MV2) für den Entleerungszyklus des Tanks. Beide werden gemäß der Sensorlogik gesteuert. Wenn der Wasserstand unter den niedrigen Pegel fällt, wird das Zufuhrventil automatisch eingeschaltet, und wenn der Wasserstand einen hohen Pegel erreicht und dies vom Hochpegelsensor erkannt wird, wird der Entladevorgang automatisch eingeschaltet. Wenn ein hoher Pegel erkannt wird, wird ein Summer als Alarmsignal eingeschaltet. Der Zyklus wird gestoppt, wenn der Benutzer die Stopptaste auf dem Bedienfeld drückt. SPS-Ein- und Ausgänge Digitale Eingänge Start PB: I0.0 Stop PB: I0.1 TLB 1: I0.3 TLB 2: I0.2 Digitale Ausgänge Zyklus EIN: Q0.0 Ventil MV1 (Zufuhr): Q0.1 Ventil MV2 (Abfuhr): Q0.2 Rührwerk/Mischer M: Q0.3 Summer: Q0.4 SPS-Wasserfüll- und -ablassvorgang SPS-Programmerklärung Für diese Anwendung haben wir S7-1200 PLC und TIA-Portalsoftware zur Programmierung verwendet. In Netzwerk 1 haben wir einen Verriegelungskreis für den Zyklus-EIN-Ausgang (Q0.0) verwendet. Er kann durch Drücken von START PB (I0.0) gestartet und durch Drücken von STOP PB (I0.1) gestoppt werden. Wenn der Zyklus gestartet wird, überprüft das System den Füllstand des Tanks. Wenn der Tankpegel niedrig ist, wird der Fütterungsprozess gestartet, und wenn der Tankpegel hoch ist, wird der Entladezyklus gestartet. Der Einfachheit halber haben wir hier für beide Sensoren im Programm einen Schließerkontakt gewählt. Dies kann vor Ort durch Relaislogik erfolgen oder Sie können solche Sensoren verwenden. Wenn der Tank einen niedrigen Pegel erkennt, wird TLB 2 (I0.2) aktiviert und der Fütterungszyklus wird eingeschaltet. Hier haben wir den Öffnerkontakt von TLB1 (I0.3) gewählt, sodass der Fütterungszyklus gestoppt wird, wenn die SPS einen hohen Pegel erkennt. Wenn der Tank einen hohen Pegel erkennt, wird TLB 1 (I0.3) aktiviert und der Entladezyklus wird eingeschaltet. Hier haben wir den Öffnerkontakt von TLB2 (I0.2) gewählt, sodass der Entladezyklus gestoppt wird, wenn die SPS einen niedrigen Pegel erkennt. Mischer M (Q0.3) sollte während des Entladezyklus zum Mischen eingeschaltet sein. Hier haben wir auch einen Alarm für einen hohen Pegel berücksichtigt, um den Bediener zu informieren. Wenn TLB 1 (I0.3) erkannt wird, wird der Summer (Q0.4) aktiviert. Während aller Funktionen sollte der Zyklus eingeschaltet sein. Laufzeittestfälle Hinweis: Die obige SPS-Logik liefert eine grundlegende Vorstellung der Anwendung von SPS im Wasserfüll- und -entladeprozess. Die Logik ist begrenzt und stellt keine vollständige Anwendung dar. -
SPS-Programm für automatische Flüssigkeitsmischanwendungen
leizuofa posted A plc and hmi article in German in PLC programming learning
Erstellen Sie ein SPS-Programm für automatische Flüssigkeitsmischanwendungen mithilfe der Kontaktplanlogik-Programmierung. Lernen Sie den Mischprozess mithilfe eines SPS-Kontaktplandiagramms kennen. Flüssigkeitsmischanwendung Problembeschreibung In vielen Branchen werden viele Mischsysteme zum Mischen von Lösungen verwendet. Einige Anlagen verwenden Vollautomatik oder Halbautomatik. Ein manuelles System hat viele Nachteile, wie z. B. mangelnde Genauigkeit, Zeitverzögerungsprobleme, Flüssigkeitsverlust, Zeitaufwand usw. Hier diskutieren wir die halbautomatische Anwendung eines Mischsystems. Diagramm Problemlösung Für dieses Beispiel verwenden wir SPS-Programmierung und dafür eine Siemens S7-1200 SPS. Zur einfachen Erklärung können wir ein einfaches Beispiel eines Mischsystems wie oben gezeigt betrachten. In dieser Anwendung kann der Bediener mithilfe der Schalter S1 und S2 eine reine, unvermischte Lösung herstellen. Und der Bediener kann mithilfe des Schalters S3 eine gemischte Lösung oder ein gemischtes Material herstellen. Der Bediener beobachtet den Füllstand des Tanks und kann die Flüssigkeit im Tank durch Betätigen des Ventils V5 ablassen. Außerdem läuft der Rührmotor M, während der Tank gefüllt wird. Wir werden ein Verriegelungssystem bereitstellen, damit der Bediener nicht beide Schalter gleichzeitig betätigen kann. V1, V3 und V5 sind manuelle Ventile, die nicht mit der SPS verbunden sind. V2 und V4 sind elektronisch betriebene Ventile, die von der SPS gesteuert werden können. Liste der SPS-Ein- und Ausgänge Digitale Eingänge Es gibt drei Schalter S1, S2 und S3 S1: I0.0 S2: I0.1 S3: I0.3 Digitale Ausgänge Wir haben zwei Ventile, V2 und V4. ein Rührmotor M1 V2: Q0.0 V4: Q0.1 M1: Q0.2 SPS-Kontaktplan für automatische Flüssigkeitsmischanwendung SPS-Programm erklärt Für diese Anwendung haben wir S7-1200 PLC und TIA-Portalsoftware zur Programmierung verwendet. In Netzwerk 1 haben wir den Schließerkontakt von S1 (I0.0) und den Öffnerkontakt von S2 (I0.1) und S3 (I0.2) in Reihe geschaltet. Durch Aktivieren des Schalters S1 kann der Bediener das Ventil V2 für Lösung 1 (Flüssigkeit 1) STARTEN. In Netzwerk 2 haben wir den Schließerkontakt von S2 (I0.1) und den Öffnerkontakt von S1 (I0.0) und S3 (I0.2) in Reihe geschaltet. Durch Aktivieren des Schalters S2 (I0.1) kann der Bediener das Ventil V4 (Q0.1) für Lösung 2 (Flüssigkeit 2) STARTEN. Für beide Netzwerke 1 und 2 haben wir eine Parallelschaltung gewählt, den Schließerkontakt von S3 (I0.2) und in Reihe mit dem Öffnerkontakt von S1 (I0.0) und S2 (I0.1). Aufgrund der obigen Parallelschaltung kann der Bediener beide Ventile durch Aktivieren des Schalters S3 (I0.2) für die Mischlösung (Flüssigkeit 1 und Flüssigkeit 2) betätigen. Unter unseren Bedingungen sollte der Rührer M1 (Q0.2) automatisch aktiviert werden, während der Tank gefüllt wird. Daher haben wir den Schließerkontakt von V2 (Q0.1) und parallel den Schließerkontakt von V4 (Q0.1) gewählt, sodass der Rührer automatisch durch Betätigen eines beliebigen Schalters aktiviert wird. Laufzeittestfälle Hinweis: Die obige SPS-Logik bietet eine grundlegende Vorstellung von der Anwendung von SPS in Flüssigkeitsmischanwendungen. Die Logik ist begrenzt und stellt keine vollständige Anwendung dar. -
SPS-Programm zur automatischen Lampensteuerung in Lagereinrichtungen
leizuofa posted A plc and hmi article in German in PLC programming learning
Dies ist das SPS-Programm zur automatischen Lampensteuerung in Lagereinrichtungen. Automatische Lampensteuerung Problembeschreibung Beim alten Verfahren drückte die Person, wenn sie das Lager betrat, den Schalter und alle Lampen im Lager gingen an. Wenn wir alle Lampen gleichzeitig einschalten, entsteht ein höherer Energieverbrauch. Dieses Problem tritt im alten Verfahren auf, daher sind Lösungen für dieses Verfahren erforderlich. Wir können dieses Problem durch einfache Automatisierung oder ein Verriegelungssystem lösen. Problemdiagramm SPS-Problemlösung Wir können dieses Problem durch einfache Verriegelung mithilfe einer SPS lösen. Wie in der Abbildung gezeigt, betrachten wir ein Lager für die Industrie und es gibt mehrere Segmente in der Einrichtung. Beispielsweise haben wir nur drei Segmente für das Lager berücksichtigt. Nehmen wir an, wir haben hier 3 Lampen für 3 Segmente und 3 Schalter für den Betrieb. Wenn eine Person das Lagerhaus (die Lagereinrichtung) für Arbeiten betritt, betätigt sie Lampe 1 durch Drücken des Schalters 1. Wenn die Arbeit abgeschlossen ist, schaltet der Bediener das Licht AUS. Hier stellen wir ein Verriegelungssystem bereit, sodass eine Person die Lampe eines anderen Segments nicht betätigen kann, bis sie die Lampe des ersten Segments stoppt. Derselbe Fall tritt in anderen Segmenten auf. Durch die Verwendung dieser Automatisierungs-/Verriegelungsschaltung können wir also Energie sparen. Hinweis: Diese Art der Verriegelung gilt nur für einige Arten von Lagereinrichtungen, da diese bedient werden, indem man jeweils nur in einem Segment arbeitet, bevor man zum nächsten Segment in der Lagereinrichtung geht. Liste der Ein-/Ausgänge Digitale Eingänge SW1: I0.0 SW2: I0.2 SW3: I0.3 Digitale Ausgänge Lampe 1: Q0.0 Lampe 2: Q0.1 Lampe 3: Q0.2 SPS-Kontaktplan für automatisches Ein-/Ausschalten der Lampe SPS-Programmbeschreibung Für diese Anwendung haben wir S7-1200 PLC und TIA-Portalsoftware zur Programmierung verwendet. Netzwerk 1: Im obigen Programm haben wir den NO-Kontakt von SW 1 (I0.0) zum Betreiben der Lampe 1 (Q0.0) verwendet und NC-Kontakte in Reihe geschaltet. Wenn der Benutzer also andere Schalter drückt, wird Lampe 1 (Q0.0) AUS sein. Netzwerk 2: In Netzwerk 2 haben wir die Logik für Lampe 2 (Q0.1) geschrieben. Durch Betätigen von SW2 (I0.2) kann der Bediener Lampe 2 (Q0.1) betätigen. Und wenn die NC-Kontakte in Reihe geschaltet sind, wird Lampe 2 (Q0.1) ausgeschaltet, wenn der Benutzer andere Schalter drückt. Netzwerk 3: In Netzwerk 3 haben wir die Logik für Lampe 3 (Q0.2) geschrieben. Durch Betätigen von SW3 (I0.2) kann der Bediener Lampe 3 (Q0.2) betätigen. Und wenn die NC-Kontakte in Reihe geschaltet sind, wird Lampe 3 (Q0.2) ausgeschaltet, wenn der Benutzer andere Schalter drückt. Laufzeittestfälle Hinweis: Die obige SPS-Logik bietet eine grundlegende Vorstellung von der Anwendung eines SPS-Programms zur automatischen Lampensteuerung. Die Logik ist begrenzt und keine vollständige Anwendung. -
Schreiben Sie ein SPS-Logik-GATE-Programm für das folgende SPS-Beispiel. Logik-GATE-Programm Schreiben Sie ein Programm, das B3:0 mit B3:1 UND-verknüpft, wenn I:0.0/0 aktiviert ist, B3:0 mit B3:1 ODER-verknüpft, wenn I:0.0/1 aktiviert ist, B3:0 mit B3:1 XOR-verknüpft, wenn I:0.0/2 aktiviert ist, und B3:0 KOMPLEMENTIERT, wenn I:0.0/3 aktiviert ist. B3:1 soll in jedem Fall das Ergebnis enthalten. Wenn mehr als ein Eingang I:0.0/0-I:0.0/3 aktiviert ist, wird nur eine der Operationen ausgeführt. Die Prioritätsreihenfolge für Operationen sollte von UND (höchste Priorität) bis KOMPLEMENT (niedrigste Priorität) sein. SPS-Kontaktplanlogik
-
SPS-Programm für Stern-Dreieck-Motorstarter
leizuofa posted A plc and hmi article in German in PLC programming learning
Wenn ein Elektromotor gestartet wird, zieht er einen hohen Strom, der typischerweise 5-6 Mal höher ist als der normale Strom. Bei Gleichstrommotoren gibt es beim Start keine Gegen-EMK, daher ist der Anfangsstrom im Vergleich zum normalen Strom sehr hoch. Um den Motor vor diesen hohen Anlaufströmen zu schützen, verwenden wir einen Stern- und Dreieckstarter. Bei der Sternschaltung ist die Versorgungsspannung des Motors einfach geringer. Daher verwenden wir beim Starten des Motors eine Sternschaltung. Nach dem Motorlauf ändern wir die Verbindung von Stern zu Dreieck, um die volle Geschwindigkeit des Motors zu erreichen. Stern-Dreieck-Motorstarter Die folgende Abbildung zeigt die Wicklungsverbindungen in Stern- und Dreieckkonfiguration nacheinander. Es ist ersichtlich, dass bei der Sternschaltung ein Ende aller drei Wicklungen kurzgeschlossen ist, um einen Sternpunkt zu bilden, während das andere Ende jeder Wicklung an die Stromversorgung angeschlossen ist. Bei der Dreieckkonfiguration sind die Wicklungen so verbunden, dass eine geschlossene Schleife entsteht. Die Verbindung jeder Wicklung ist in der obigen Abbildung dargestellt. Im tatsächlichen Motor werden die dreiphasigen Verbindungen in der folgenden Reihenfolge bereitgestellt: Um also in einem praktischen Motor eine Wicklungsverbindung im Stern- und Dreieckstil herzustellen, ist die Verbindung oben dargestellt. Der Hauptverteiler wird verwendet, um die Wicklungen mit Strom zu versorgen. Er muss ständig eingeschaltet sein. Zunächst ist der Sternschütz geschlossen, während der Dreieckschütz geöffnet ist. Dadurch werden die Motorwicklungen in Sternkonfiguration gebracht. Wenn der Motor an Geschwindigkeit gewinnt, wird der Sternschütz geöffnet, während der Dreieckschütz geschlossen ist, wodurch die Motorwicklungen in Dreieckkonfiguration gebracht werden. Die Schütze werden mithilfe einer SPS gesteuert. Der folgende Abschnitt des SPS-Tutorials erklärt die Kontaktplanprogrammierung für den Stern-Dreieck-Motorstarter. SPS-Programm für Stern-Dreieck-Motorstarter: SPS-Kontaktplanlogik Sprosse 1 Hauptschütz: Der Hauptschütz hängt vom normalerweise offenen Startdruckknopf (I1), dem normalerweise geschlossenen Stoppknopf (I2) und dem normalerweise geschlossenen Überlastrelais ab. Das bedeutet, dass der Hauptschütz nur aktiviert wird, wenn der Startknopf gedrückt ist, während der Stoppknopf nicht gedrückt und das Überlastrelais nicht aktiviert ist. Parallel zum Startknopf I1 wird ein normalerweise offener Eingang mit der Bezeichnung (Q1) hinzugefügt. Dadurch wird ein Druckknopf erstellt, der bedeutet, dass der Motor, sobald er gestartet ist, auch dann gestartet bleibt, wenn der Startknopf losgelassen wird. Sprosse 2 Sternschütz: Der Sternschütz hängt vom Hauptschütz, den normalerweise geschlossenen Kontakten des Timers (T1) und den normalerweise geschlossenen Kontakten des Ausgangs-Dreieckschützes (Q3) ab. Der Sternschütz wird also nur aktiviert, wenn der Hauptschütz eingeschaltet, der Zeitausgang nicht aktiviert und der Dreieckschütz nicht aktiviert ist. Timer T1: Timer T1 misst die Zeit, nach der die Wicklungsverbindung des Stern-Dreieck-Starters geändert werden muss. Er beginnt mit der Zeitzählung, nachdem der Hauptschütz aktiviert wurde. Sprosse 3 Dreieckschütz: Der Dreieckschütz wird aktiviert, wenn der Hauptschütz (Q1) aktiviert wird, Timer T1 aktiviert ist und der Sternschütz (Q3) deaktiviert ist. Siehe auch die Programmierung des Druckknopfs und andere Anforderungen für einen einfachen Motorstarter, die im PLC-Tutorial erklärt werden: Motorstarter Hinweis: Dieser Beitrag dient nur zu Bildungs- oder Referenzzwecken. Für einen stromführenden Stromkreis werden einige Ergänzungen zum obigen Stromkreis vorgenommen, wie z. B. sicherheitsrelevante, je nach Anwendung einige Verriegelungen usw. -
SPS-Motorsteuerung, Kontaktplanlogik-Programmierung
leizuofa posted A plc and hmi article in German in PLC programming learning
Jetzt besprechen wir, wie eine SPS-Motorsteuerung funktioniert. Bevor wir uns mit dem Artikel befassen, nehmen wir einige Bedingungen an. Eine SPS muss einen Motor starten, wenn die Starttaste gedrückt wird. Sie verfügt über drei Sperren: Hohe Motorvibration, Überlastung und hohe Motortemperatur. Wenn eine der Sperren aktiviert wird, muss die SPS den Motor sofort stoppen. Die SPS muss den Motor stoppen, wenn die Stopptaste gedrückt wird. Die SPS-Auslöselogik oder Sperre darf nur aktiviert werden, wenn sich der Motor im Fernmodus befindet. SPS-Motorsteuerung In der obigen Abbildung: Rote LED-Anzeigen auf den Eingangs- und Ausgangskarten der SPS zeigen an, ob die jeweiligen E/A-Kanäle aktiviert sind. Hinweis: In der obigen Abbildung werden die Signale des lokalen Bedienfelds nicht angezeigt. Das lokale Bedienfeld ist direkt mit dem Motorzuführer verbunden. 24-V-Gleichstrom direkt angeschlossen (im Allgemeinen werden Sicherungen oder Barrieren verwendet, Strom wird über Sammelschiene verteilt) SPS-Eingänge Start-Druckknopf Stopp-Druckknopf Hohe Vibration Hohe Temperatur Überlastungsauslösung Laufrückmeldung Lokaler/Remote-Status SPS-Ausgänge Startbefehl (Remote-Start) Stoppbefehl (Remote-Stopp) Startfreigabe (optional) Der Motor ist ein dreiphasiges, mit 415 V Wechselstrom betriebenes Gerät. Standardmäßig werden Hochspannungsgeräte also von Umspannwerken oder Motorsteuerungszentren (MCC) mit Strom versorgt, die elektrisch betrieben werden. Daher gehen wir davon aus, dass dieser Motor an einen einfachen Motorzuführer im Umspannwerk angeschlossen ist. Im Allgemeinen hat der Motorzuführer auch Eingänge vom Feld (lokales Bedienfeld) und von der SPS. Diese sind in der folgenden Abbildung dargestellt. Hinweis: Der Motorzuführer kann Start-, Stopp- und andere Auslöseanzeigen wie Überlastung usw. im Motorzuführerfeld haben, die in der Abbildung nicht dargestellt sind. Diese sind (zusätzlich zum LCP) auf dem Motorzuführungspanel montiert. Wenn der Motorzuführung Start- und Stoppbefehle von der SPS empfängt, bezeichnen wir diese als Fernstart- und Fernstoppsignale. Wenn der Motorzuführung Start- und Stoppbefehle von einem lokalen Bedienfeld (LCP) empfängt, das im Feld (in der Nähe des Motors) installiert ist, bezeichnen wir diese als lokale Start- und lokale Stoppsignale. In der Regel verfügt dieses LCP auch über einen Not-Aus- und einen lokalen/ferngesteuerten Auswahlschalter. Der Motorzuführungsschalter sendet auch einen lokalen/ferngesteuerten Status an die SPS. Wenn sich der lokale/ferngesteuerte Auswahlschalter im lokalen Modus befindet, berücksichtigt der Motorzuführungsschalter nur Signale vom LCP und ignoriert die Befehle der SPS. Wenn sich der lokale/ferngesteuerte Auswahlschalter im Fernmodus befindet, berücksichtigt der Motorzuführungsschalter Signale von der Fernsteuerung, d. h. der SPS, und ignoriert die Signale vom LCP. Beispiel: Wenn sich der lokale/ferngesteuerte Auswahlschalter im Fernmodus befindet. Wenn der Feldbediener den Startdruckknopf vom Feld-LCP aus gedrückt hat, wird der Motor nicht gestartet, da die Auswahl im Fernmodus erfolgt. Abhängig vom Status des lokalen/ferngesteuerten Auswahlschalters entscheidet der Motorzuführer, welche Signale berücksichtigt werden, d. h. entweder PLC- oder LCP-Signale. Hinweis: Die lokale/ferngesteuerte Auswahl wird nicht für Nothalt- oder Stoppbefehle von PLC oder LCP angewendet. Unabhängig vom Modus werden die Stoppbefehle vom Motorzuführer akzeptiert und der Motor wird sofort gestoppt. Dies ist ein Sicherheitsrisiko. Sehen wir uns an, wie eine PLC einen Motor steuert. Jetzt ist der lokale/ferngesteuerte Auswahlschalter im Remote-Modus. Hier senden wir ein Freigabesignal (Startfreigabe) an den Motorzuführer. Zum Starten des Motors muss die Freigabe in Ordnung sein, andernfalls wird der Motorzuführer stromlos gemacht oder startet den Motor nicht. In PLC wird die Startfreigabe als zusätzliche Sicherheit und zur Überprüfung des Verriegelungsstatus verwendet. Wenn alle Verriegelungen in Ordnung sind, wird nur das Freigabesignal an den Motorzuführer gesendet. Im Allgemeinen nennen wir dies „Start Permissive“, da es, wie der Name schon sagt, nur zum Starten des Motors erforderlich ist. Nach dem Starten des Motors wird der Status dieses Permissive-Signals vom Motorzuführer nicht berücksichtigt (nur zum Starten des Motors erforderlich). Dies ist ein optionales Signal. Für Motoren mit hoher Kapazität werden Start-Permissive-Signale verwendet. Für Motoren mit normaler oder geringer Kapazität werden diese sehr selten verwendet, was wiederum von unseren Anwendungen, der Branche, den Anforderungen usw. abhängt. Nehmen wir an, alle Verriegelungen sind in Ordnung, also sendet die SPS das Permissive-Signal an den Motorzuführer. Jetzt wird der Start-Druckknopf gedrückt. Zuerst prüft die SPS den lokalen/Remote-Status. Wenn er sich im Remote-Status befindet, fährt sie fort. Wieder prüft sie, ob aktive Auslösungen/Verriegelungen vorhanden sind. Wenn keine Verriegelung vorhanden ist oder alles normal funktioniert, sendet die SPS einen Startbefehl an die Unterstation, in der der Motorzuführer installiert ist. In diesem Beispiel haben wir drei Verriegelungen: Motorvibration hoch, Motortemperatur hoch und Überlastauslösung. Im Allgemeinen sind Motoren mit hoher Kapazität mit Vibrations- und Temperatursensoren ausgestattet. In unserem Beispiel betrachten wir Vibrationssignale als ausfallsicher, daher ist der Standardstatus normalerweise geschlossen. Wenn eine starke Vibration auftritt, wird der Kontakt normalerweise offen und die SPS löst den Motor aus bzw. stoppt ihn. Wir haben eine weitere Verriegelung, nämlich die Überlastauslösung. Dieser Eingang wird vom Motorzuführer übernommen. Das Signal des Temperatursensors ist normalerweise offen und wird bei hoher Temperatur normalerweise geschlossen und die SPS schaltet den Motor aus/stoppt ihn. Hinweis: Der ausfallsichere oder standardmäßige Kontaktstatus (NC oder NO) hängt von unserer Anwendung oder den Logikanforderungen ab. Hier diskutieren wir nur ein Beispiel zum Verständnis des Konzepts. Nach Erhalt des Startbefehls von der SPS wird der Motorzuführer aktiviert und schaltet den Motor ein. Nach dem Motorstart sendet der Motorzuführer die Laufrückmeldung an die SPS. Die Laufrückmeldung wird in der Grafik angezeigt. Bei einigen SPS oder Sicherheits-SPS sendet die SPS automatisch ein Stoppsignal an den Motorzuführer, wenn die Laufrückmeldung nicht innerhalb eines bestimmten Zeitrahmens (z. B. innerhalb von 5 Sekunden) empfangen wird. Dies ist eine optionale Funktion in normalen SPS-Anwendungen (ein Muss bei Sicherheits-SPS). Wenn beispielsweise jetzt eine hohe Vibration auftritt, sendet die SPS einen Stoppbefehl an den Motorzuführer und dieser stoppt den Motor sofort. Der Laufrückmeldungsstatus wird ebenfalls entsprechend aktualisiert. Der Motor wird gestartet, wenn der Füllstandstransmitter hoch ist, und wird wieder gestoppt, wenn der Füllstandstransmitter niedrig ist. Abkürzungen: MCC: Motor Control Center oder Unterstation, wo der Motor mit Strom versorgt wird. PLC/DCS: Steuerungssystem, wo der Motor logisch (automatisch) oder durch Bedienhandlung (manuell) gesteuert werden kann. LCP: Lokales Bedienfeld, das vor Ort in der Nähe des Motors installiert wird und Start- und Stopp-Druckknöpfe enthält.